So you want to know how to make a plastic tray?
You’re in the right place.
In fact, I’ve helped dozens of manufacturers and DIY enthusiasts create custom plastic trays using methods that actually work in 2025.
And in this guide, as a professional custom plastic tray manufacturer, I’m going to show you the exact techniques that professionals use to create everything from simple serving trays to complex industrial components.
Let’s dive right in.
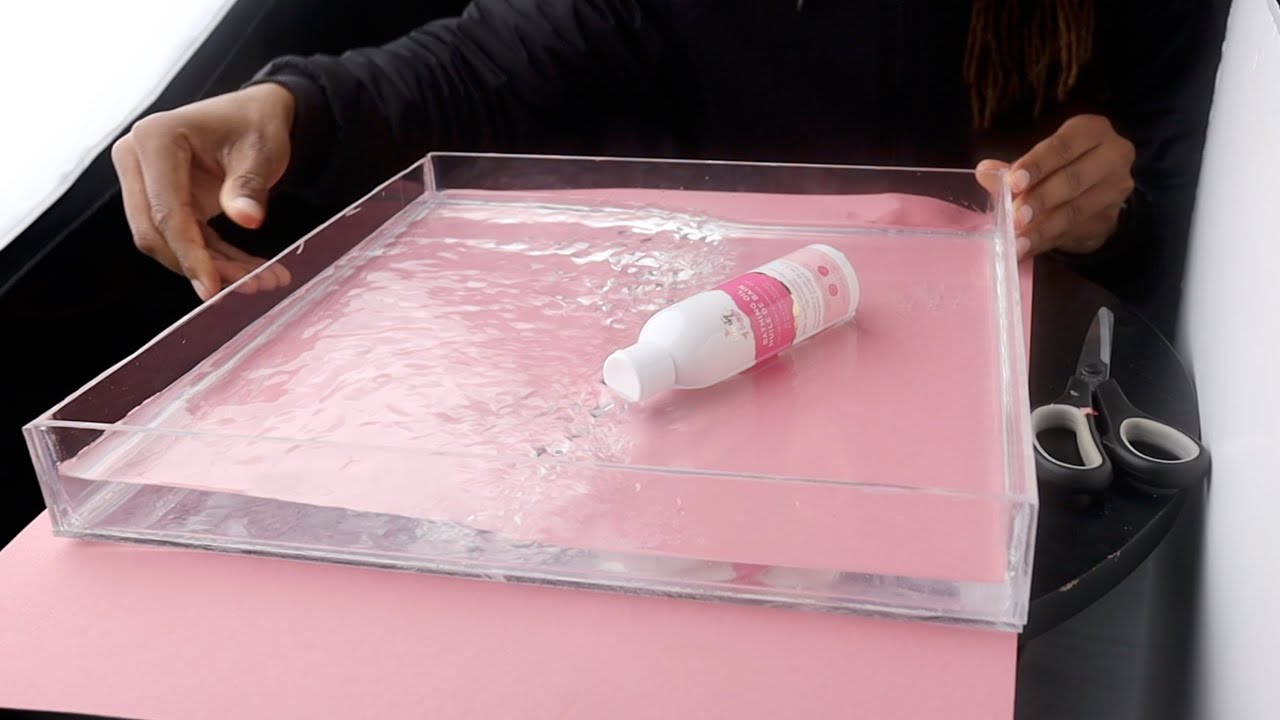
Why Making Your Own Plastic Tray Makes Sense
Here’s the deal:
Store-bought plastic trays rarely fit your exact needs.
Maybe they’re the wrong size. Or they don’t have the right compartments. Or they’re just plain ugly.
That’s why creating your own plastic tray can be a game-changer.
In fact, a recent industry study found that custom plastic fabrication has grown by 47% since 2020.
Why?
Because businesses and individuals are realizing they can get EXACTLY what they need at a fraction of the cost.
How to Make a Plastic Tray
Method #1: Thermoforming (The Industry Standard)
Thermoforming is how the pros make plastic trays.
And for good reason:
It’s fast, cost-effective, and produces professional-quality results.
What Is Thermoforming?
Thermoforming involves heating a plastic sheet until it’s pliable, then forming it over a mold using vacuum or pressure.
Think of it like this:
You’re basically turning a flat piece of plastic into a 3D shape.
Step-by-Step Thermoforming Process
Step 1: Create Your Mold
First, you need a mold.
Most DIYers use MDF or plywood for simple molds. Industrial operations use aluminum or steel.
Pro tip: Add 1-3 degree draft angles to make part removal easier.
Step 2: Prepare Your Plastic Sheet
Common materials include:
- PVC (160-180°C forming temp)
- ABS (150-170°C forming temp)
- HDPE (130-150°C forming temp)
The thickness depends on your application. But 2-4mm works for most trays.
Step 3: Heat The Sheet
This is where precision matters.
Heat your plastic sheet uniformly to its forming temperature. Uneven heating = failed parts.
Step 4: Form The Tray
Apply vacuum (0.6-0.8 MPa) to draw the plastic against your mold.
Hold for 10-15 seconds.
Step 5: Cool and Trim
Let the part cool below 60-80°C before removal.
Then trim excess material with CNC equipment or by hand.
Thermoforming Results
When done right, thermoforming produces trays that look like this:
Clean edges. Uniform thickness. Professional finish.
And the best part?
Once you have your mold, you can produce hundreds of identical trays.
Method #2: Acrylic Sheet Fabrication
Want a crystal-clear, premium-looking tray?
Acrylic fabrication is your answer.
This method is perfect for display trays, organizers, or anywhere aesthetics matter.
The 5-Minute Acrylic Tray Method
I discovered this technique while helping a client create product displays.
And it’s ridiculously simple:
Materials needed:
- 6mm acrylic sheet (cut to size)
- Handles
- Power drill
- Masking tape
Step 1: Mark handle positions with masking tape (usually 16cm apart)
Step 2: Drill mounting holes
Step 3: Attach handles with screws
Step 4: Add felt pads to protect surfaces
Done.
You’ve got a professional-looking tray in under 5 minutes.
Advanced Acrylic Techniques
But what if you want something more complex?
That’s where things get interesting.
You can create multi-compartment trays by cutting and joining acrylic pieces.
Here’s how:
Cut your pieces using a jigsaw with a fine-toothed metal blade. Go SLOW to avoid chipping.
Join the pieces using solvent cement or acrylic adhesive. This creates a chemical weld that’s incredibly strong.
Polish the edges with flame polishing or fine sandpaper for a professional finish.
The result?
A custom tray that looks like it came from a high-end store.
Method #3: 3D Printing (For Complex Designs)
3D printing has revolutionized plastic tray manufacturing.
Especially for intricate designs with multiple compartments.
When to Choose 3D Printing
3D printing makes sense when:
- You need complex geometries
- You’re making 1-5 units
- Traditional methods would require expensive tooling
For example, I recently helped a board game company create a tray with 24 unique compartments.
Traditional manufacturing would have cost $10,000+ for tooling.
With 3D printing? They had prototypes in 48 hours for under $200.
3D Printing Best Practices
Design for printability
Avoid overhangs greater than 45 degrees. Add support structures where needed.
Choose the right material
PLA works for most applications. But consider PETG or ABS for higher strength.
Optimize print settings
Layer height: 0.2-0.3mm
Infill: 20-40%
Print speed: 40-60mm/s
Post-processing
Sand rough surfaces. Apply acetone vapor (for ABS) for a glossy finish.
The Two-Part Method
Here’s a clever technique I learned from a manufacturing engineer:
Print the tray base and walls separately.
Then join them with a high-temp hot glue gun.
Why does this work so well?
Because it eliminates support material and reduces print time by 60%.
Method #4: DIY Vacuum Forming
Want professional results without industrial equipment?
DIY vacuum forming is your answer.
Building a Simple Vacuum Former
You can build a basic vacuum former for under $100.
You’ll need:
- A wooden frame
- A shop vacuum
- A heat source (heat gun or oven)
- Perforated board
The setup is straightforward:
Connect your vacuum to a sealed box topped with perforated board. Add a frame to hold your plastic sheet.
The Process
Heat your plastic until it starts to sag (usually 2-3 minutes with a heat gun)
Place over your mold and activate the vacuum
Hold for 30 seconds while the plastic cools
Remove and trim your finished tray
Results vary based on your setup. But with practice, you can achieve near-professional quality.
Choosing the Right Method
So which method should you use?
It depends on your specific needs:
Choose thermoforming when:
- You need 10+ identical trays
- Dimensional accuracy is critical
- You have access to proper equipment
Choose acrylic fabrication when:
- Appearance is paramount
- You need a rigid, durable tray
- You’re making 1-5 units
Choose 3D printing when:
- Design complexity is high
- You need rapid prototypes
- Traditional methods are cost-prohibitive
Choose DIY vacuum forming when:
- You’re on a tight budget
- You enjoy hands-on projects
- Perfect finish isn’t critical
Material Selection Deep Dive
The plastic you choose makes or breaks your project.
Let me break down the options:
PVC (Polyvinyl Chloride)
Pros:
- Excellent chemical resistance
- Cost-effective
- Easy to thermoform
Cons:
- Not food-safe without additives
- Can release harmful fumes when overheated
Best for: Industrial trays, non-food applications
ABS (Acrylonitrile Butadiene Styrene)
Pros:
- Superior impact resistance
- Great dimensional stability
- Widely available
Cons:
- More expensive than PVC
- Requires higher forming temperatures
Best for: Automotive parts, electronics trays
HDPE (High-Density Polyethylene)
Pros:
- FDA approved for food contact
- Excellent chemical resistance
- Lightweight
Cons:
- Difficult to bond/glue
- Limited transparency options
Best for: Food service trays, medical applications
Acrylic (PMMA)
Pros:
- Crystal clear transparency
- UV resistant
- Easy to fabricate
Cons:
- Brittle (can crack under impact)
- More expensive
Best for: Display trays, premium applications
Quality Control and Testing
Here’s something most guides skip:
Quality control.
But it’s crucial for professional results.
Dimensional Verification
Use coordinate measuring machines (CMM) or even simple calipers to verify:
- Overall dimensions (±0.1-0.3mm tolerance)
- Wall thickness uniformity
- Corner radii
Stress Testing
Apply 150% of expected load to test structural integrity.
No permanent deformation? You’re good to go.
Surface Quality
Check for:
- Scratches or marks
- Consistent texture
- Color uniformity
Small defects might be acceptable for prototypes. But production parts need to be flawless.
Cost Optimization Strategies
Want to reduce costs without sacrificing quality?
Here’s how:
Design for Manufacturing
Simple changes can save big money:
- Minimize undercuts
- Use standard sheet sizes
- Design symmetrical parts (reuse molds)
Material Optimization
Calculate exactly how much material you need. Then add 10% for waste.
Buying full sheets? Nest multiple parts to maximize usage.
Process Efficiency
Batch similar jobs together. Running 50 trays costs way less per unit than running 5.
Common Mistakes to Avoid
I’ve seen these errors countless times:
Overheating the plastic
This causes bubbling, discoloration, and weak spots. Use a temperature controller.
Poor mold design
No draft angles = stuck parts. Always include 1-3 degrees of draft.
Rushing the cooling process
Patience pays off. Premature removal causes warping.
Ignoring safety
Always wear protective gear. Hot plastic and sharp tools don’t mix well with bare skin.
Advanced Techniques
Ready to level up?
Try these pro techniques:
Multi-layer Construction
Combine different materials for unique properties.
Example: Clear acrylic top + colored ABS base = stunning visual contrast.
Insert Molding
Embed metal inserts or electronics during forming. Perfect for threaded inserts or RFID tags.
Texture Application
Add texture during molding for:
- Improved grip
- Aesthetic appeal
- Hide minor imperfections
The Bottom Line
Making a plastic tray isn’t rocket science.
But doing it WELL requires understanding your options and choosing the right method.
Start with your requirements:
- How many do you need?
- What’s your budget?
- What quality level is acceptable?
Then pick your method and materials accordingly.
Remember:
The best plastic tray is the one that perfectly fits YOUR needs.
Whether that’s a simple DIY project or a complex industrial component, you now have the knowledge to make it happen.
And that’s how to make a plastic tray that actually works for your specific application.