Reducing cooling time is crucial for injection molding operations. The cooling stage often takes up the majority of the overall cycle time. So optimizing cooling can lead to big productivity gains.
In this complete guide, I will teach you several techniques for slashing your cooling times as a professional plastic injection molding manufacturer. By the end, you’ll know exactly how to enhance cooling efficiency in your injection molding process.
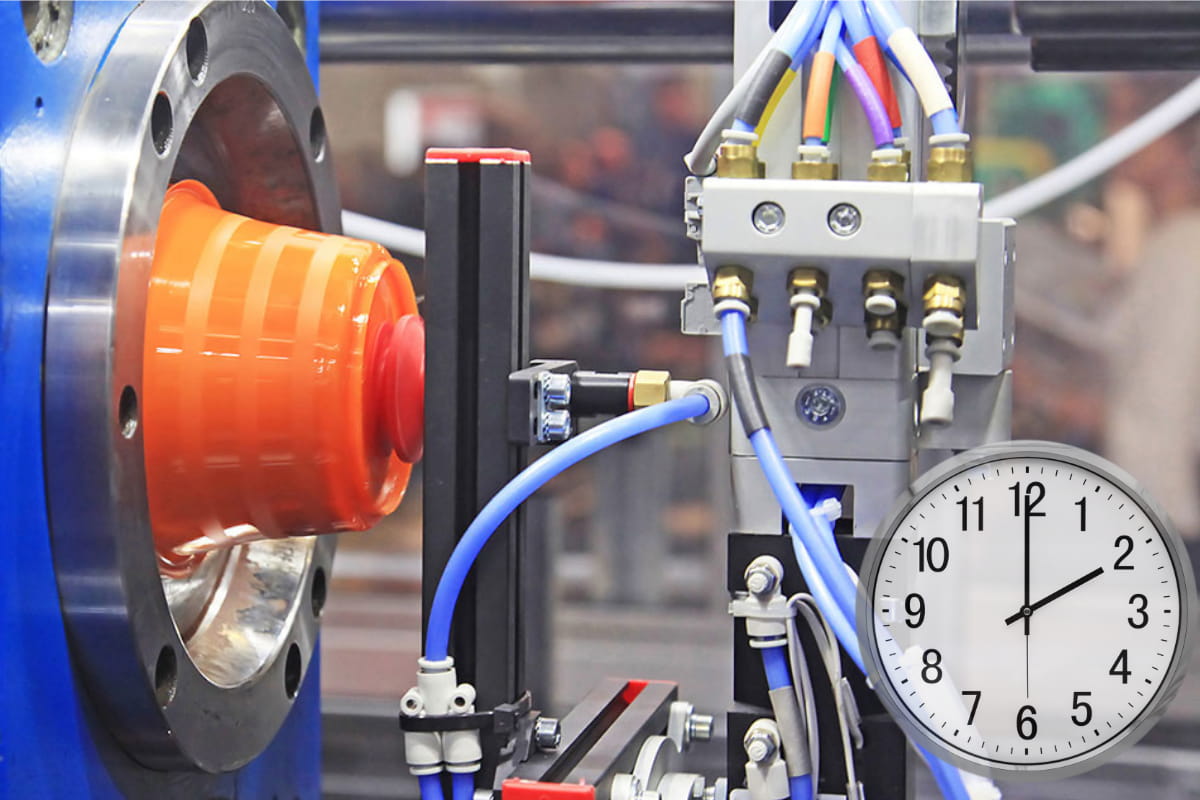
Why Cooling Time Matters in Injection Molding
The cooling process is when molten plastic solidifies into its final shape within the mold cavity. Sufficient cooling time allows the material to fully set before ejection.
So cooling time impacts:
Part Quality
Inadequate cooling can cause issues like warping, shrinkage, and sinks. Proper cooling minimizes internal stresses for dimensionally accurate parts.
Cycle Time
As cooling can account for over 80% of total cycle time, reducing cooling time directly speeds up production.
Production Costs
Shorter cycles mean higher hourly output. This lowers per part costs thanks to economies of scale.
Clearly, cooling time optimization is vital for profitable injection molding. Now let’s explore some techniques to slash cooling times.
How to Reduce Cooling Time in Injection Molding
Here are the top methods that leading molders use to enhance cooling efficiency:
1. Optimize Cooling Channels
Cooling channels circulate fluid to extract heat from the mold and solidifying plastic.
Strategic cooling channel design can dramatically improve cooling rates. Here’s how:
- Place channels close to the cavity to minimize the conductive heat transfer distance. This enables faster, more uniform cooling.
- Use conformal channels that follow the part geometry instead of straight channels. Conformal layouts provide better surface contact for heat removal.
- Incorporate more channels near thick sections and around critical features that require additional cooling.
With optimized cooling channels, you can reduce cooling times by 30% or more.
2. Select Faster Cooling Materials
Material choice significantly impacts cooling behavior. Some general guidelines when selecting materials for faster cooling:
- Favor plastics with higher thermal conductivity like PBT or POM to improve heat transfer.
- Consider glass or mineral filled materials to enhance thermal conductivity vs unfilled variants.
- For very thin sections, amorphous materials often cool faster than semi-crystallines that require additional crystallization time.
3. Employ Rapid Cooling Techniques
Rapid cooling involves aggressively extracting heat to cut cooling time. Possible approaches include:
- High pressure water blasts directed at the mold cavity surface.
- Air blasts or vortex tubes to create turbulent, high-transfer air flow across mold surfaces.
- Direct contact water lines with turbulence enhancers for maximum heat transfer.
Rapid cooling techniques can reduce cooling times by 50% or more compared to conventional methods.
4. Heat Mold Surface Before Injection
Preheating the mold cavity surface right before injection reduces the initial temperature difference between the plastic and mold.
This smaller delta-T helps plastic adjacent to mold walls solidify faster. Resulting cooling time savings will depend on factors like material, wall thickness, and molding conditions.
5. Lower Ejection Temperature
Conventional practice is to cool parts to below the material’s heat deflection temperature before ejection. However, cooling 5-10°C above this threshold may suffice to maintain dimensional stability in some cases.
Since cooling rates exponentially decay as temperature lowers, reducing the target ejection temperature slightly can shorten cooling time. Any reductions must be validated to prevent introducing part defects.
6. Analyze and Optimize Process Parameters
Fine-tuning process parameters provides additional cooling time savings:
- Lower melt temperatures result in a higher temperature differential for faster cooling. But ensure temperatures provide proper flow properties.
- Faster fill rates result in less heat loss during injection, reducing subsequent cooling time.
- Higher holding pressures compress plastic to counteract sink from shrinkage, enabling earlier mold opening.
Finding the optimal balance of parameters maximizes cooling efficiency.
Conclusion
I hope this guide gives you several ideas on how to slash cooling times. To summarize, focus on:
- Optimizing your cooling channels layouts. Conformal designs provide major time reductions.
- Selecting faster cooling materials whenever suitable. High thermal conductivity plastic grades help dissipate heat.
- Leveraging rapid cooling approaches like water blasts or air vortex tubes.
- Carefully analyzing process parameters to create faster cooling conditions.
With the right cooling optimizations, you can achieve substantial gains in productivity and part quality through shorter cycle times.
So analyze your current cooling process and implement some of the techniques shared here. Your injection molding operations will become faster and more efficient as a result.