Injection molding is one of the most popular manufacturing processes. But like any manufacturing process, scrap is inevitable. Excess scrap leads to higher costs and lower profits. So how can you reduce scrap in injection molding?
In this complete guide, as a professional plastic injection molding manufacturer, we’ll cover several proven methods to decrease scrap rates in your injection molding operations. By the end, you’ll have actionable tips to enhance quality, streamline processes, and minimize wasted material.
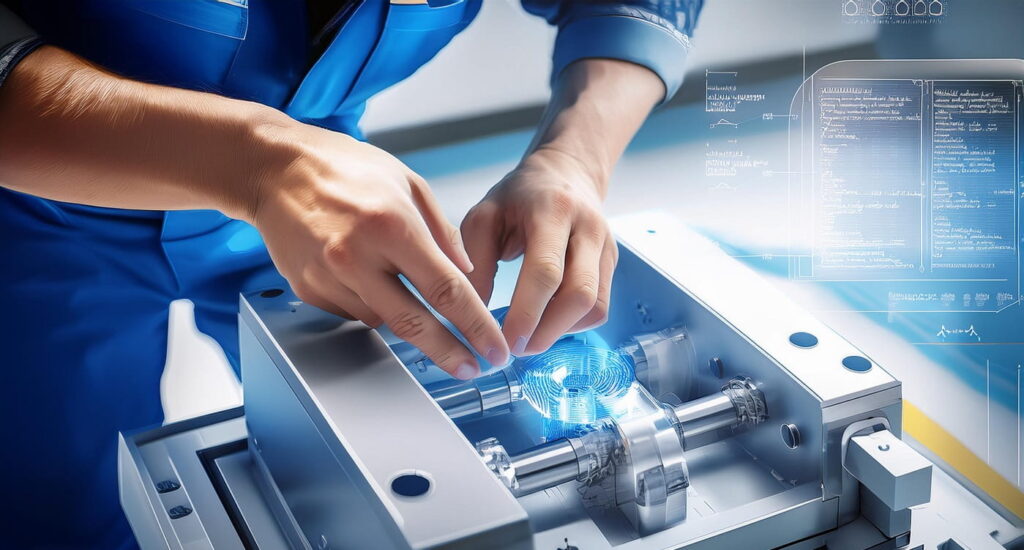
Why Is Scrap a Problem in Injection Molding?
Let’s start with why scrap is such a big issue in the first place.
There are two main reasons:
1. Material Costs Are High
Plastic pellets and resin aren’t cheap. Prices fluctuate, but you can expect to pay anywhere from $1-5 per pound depending on the material.
And it’s not just the cost of the raw plastic itself. You also have expenses related to shipping, storage, handling, and more.
With profit margins already slim, consistently high scrap rates can seriously eat into your bottom line.
2. It’s Bad for The Environment
Assuming your excess plastic makes its way to a landfill (as most scrap eventually does), that’s plain bad.
Landfill plastic can take over 400 years to decompose. And even then, it doesn’t fully break down but rather turns into microplastics – which leads to environmental issues down the road.
So by reducing injection molding scrap, you also reduce your business’ environmental impact.
4 Tips to Slash Injection Molding Scrap Rates
Now that you know why minimizing scrap is important, let’s get into some actionable ways to actually reduce it.
1. Analyze and Address Root Causes
The first step is figuring out why scrap is being produced in the first place.
Start by tracking your current scrap rates. This gives you a benchmark to measure progress.
Then, dig into the reasons behind the waste. Common sources include:
- Machine wear and tear
- Viscosity changes
- Process variation
- Poor mold design
- Contamination
Once you identity root causes, you can start addressing them.
For example, if machine Issues are leading to defects, prioritize maintenance. If it’s contamination, improve material changeover procedures.
Pinpointing and fixing these scrap triggers is key to decreasing waste.
2. Implement Process Monitoring and Control
Modern injection molding relies heavily on sensors, data collection, and process control software.
These technologies help you:
- Maintain optimal melt temp and viscosity
- Minimize process variations
- Continuously tune parameters like pressure and temperature
The result? Far fewer defects and scrapped parts.
So I recommend integrating process monitoring systems if you haven’t already. The upfront cost is easily justified by the material savings you’ll see.
3. Optimize Production Planning
Another approach is focusing on your production planning and scheduling.
Efficient planning minimizes changeovers. Which decreases contamination issues that result in scrap parts.
It also means your machines run closer to capacity. This maximizes productivity and minimizes wasted cycles.
Overall, good scheduling = less waste.
4. Improve Part and Mold Design
Finally, don’t overlook part and mold design.
Seemingly minor design tweaks can sometimes have an outsized impact on scrap rates.
For example, changing ejector pin placement can improve part release – leading to far fewer damaged components.
Work closely with your mold maker to analyze current molds. Identify any opportunties to reduce scrap through improved tooling.
FAQ: Reducing Scrap in Injection Molding
Here are answers to some common questions about minimizing scrap material:
How much scrap is normal for injection molding?
It depends a lot on the complexity of your parts. But for relatively high volume production, a scrap rate between 1-5% is typical.
Rates above 5% suggest your processes need improvement. Anything above 10% is quite high and should be addressed immediately.
Does purging reduce scrape rates in color changes?
Yes. Dedicated purging compounds push out residue far better than simply using the next resin. This leads to fewer transition parts with contamination – minimizing scrap.
Can you eliminate injection molding waste completely?
It’s unlikely you’ll reduce scrap to absolute zero. However, rates under 1% are achievable if you implement robust process control practices.
Getting scrap rates as close to zero as possible should be the end goal.
What are other ways to decrease injection molding waste?
On top of the tips outlined above, you can also:
- Recycle scrap plastic back into raw material
- Design parts and runners to use less plastic
- Schedule production from light colors to dark colors
- Improve training to reduce operator error
Key Takeaways: Reducing Your Injection Molding Scrap
And there you have it – a complete guide to lowering scrap rates.
To recap, focus on these areas:
- Analyzing root causes like machine wear and resin contamination
- Implementing process monitoring and control
- Optimizing production planning to minimize changeovers
- Tweaking part and mold designs to enable demolding
Getting scrap rates as close to zero as possible should be every injection molder’s goal. It saves money, improves efficiency, and is better for the environment.
So measure your current scrap rates, pinpoint exactly why it’s occurring, and take steps to address those root causes. By following the tips covered here, you’ll be well on your way to slashing scrap in your facility.