Shrinkage. The bane of every injection molder’s existence.
You design a part with perfect dimensions. Program the mold machine accordingly. Run some samples. Then bam! The parts come out undersized.
Not the end of the world. But nobody likes surprises… especially when high-precision parts are on the line.
The good news? Shrinkage doesn’t have to ruin your day. With a bit of planning and finesse, it can be tamed.
As a professional plastic injection molding manufacturer, I will share how to get shrinkage under control so you can mold parts to exacting specifications.
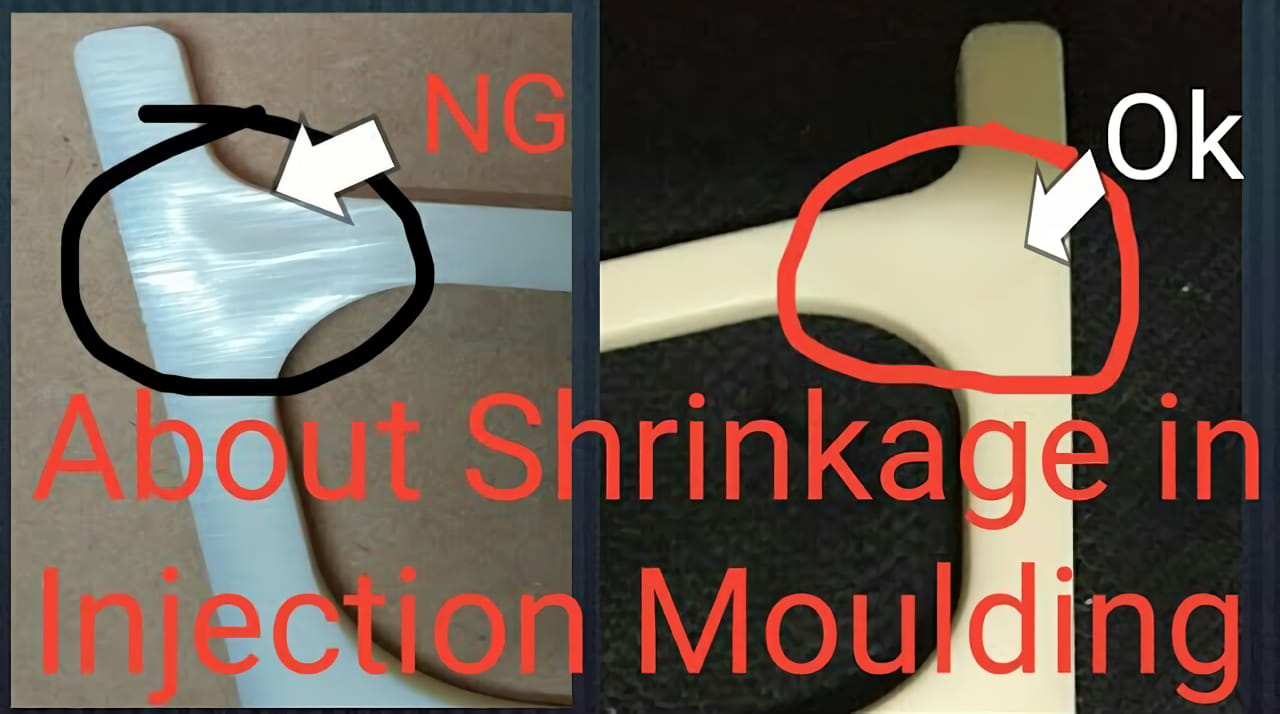
What Causes Shrinkage in Injection Molding?
Before we tackle solutions, we need to understand what causes the problem in the first place.
See, all plastics shrink as they cool from molten goo to solid parts. The hotter the plastic, the more expanded the polymer chains. As things cool down, thermal contraction kicks in. (You know, that whole “hot air rises” business from elementary school science class.)
The amount of shrinkage depends on a few factors:
- Material: Amorphous resins like ABS tend to shrink more than crystalline resins like nylon. Why? The polymer chains in amorphous materials aren’t as closely packed, so there’s more room for them to contract during cooling.
- Mold design: Thicker parts or parts with uneven wall thicknesses are prone to uneven shrinkage. The thicker areas cool — and thus shrink — slower than thinner sections.
- Processing conditions: Fast injection speeds paired with low holding pressure allows material to pack together loosely in the mold cavity. Which allows for more shrinkage when things cool off.
Now that we know why shrinkage happens, let’s talk about how to beat it.
How to Reduce Shrinkage in Injection Molding?
Getting shrinkage under control involves three main approaches:
- Optimize your mold design
- Select the right material
- Adjust your process parameters
Let’s break those down.
1. Optimize Your Mold Design
If the mold machine had it’s way, every part would cool at the exact same rate across all sections. No uneven cooling = no uneven shrinkage or warpage.
But we don’t live in a perfect world. And achieving completely uniform cooling across complex 3D geometries is easier said than done.
Even so, we can use a few design strategies to get as close as possible:
- Eliminate abrupt changes in wall thickness: Try to transition between thin and thick sections gradually (fillets are your friends here). This helps prevent “hot spots” and minimizes uneven shrinkage.
- Watch those corners: Sharp corners act as stress concentrators which accentuates material shrinkage. Radiused corners distribute stress more evenly.
- Strategic rib placement: Ribs and gussets reinforce parts without changing wall thickness significantly. Be careful not to create new hot spots though.
- Dial-in your gates: Gate placement determines how material flows into the mold. Make sure things fill nice and even. No weak points where material can’t fully pack.
Pro tip: Simulation software can preview temperature distributions and shrinkage before cutting any steel. This lets you optimize the mold design digitally vs. through costly trial-and-error on the production floor.
2. Select the Right Material
If extreme dimensional precision is needed, start with the right raw material.
Here are some things to consider regarding shrinkage:
- Amorphous vs crystalline resins: As mentioned earlier, amorphous materials like ABS or polycarbonate (PC) tend to shrink more than crystalline resins. Acetal and nylon are better options if shrinkage needs to be limited.
- Reinforced plastics: Tossing some fiberglass, carbon fiber or talc into the material mix bolsters dimensional stability. The tradeoff is these fillers or reinforcements can make the plastic more viscous — potentially causing molding issues.
- Know your PVT data: Every material supplier provides detailed information on their resin’s shrinkage characteristics across different temperature and pressure ranges (PVT data). Review this info to select the best option.
Bottom line: Work with your material vendor to pick the resin that meets both application needs AND offers minimal shrinkage.
3. Refine Those Process Parameters
Last but not least, leverage the flexibility of injection molding machines to refine the molding process itself.
The goal is to pack as much material into the mold as possible BEFORE things start to solidify. This leaves less room for the natural contraction that occurs during cooling.
Here are some process tweaks worth trying:
- Crank up the pressure: Applying more injection pressure forces polymer chains closer together. Turning up pack and hold pressure counteracts shrinkage after the initial injection by compacting the molecules even more.
- Slow the fills: Fast fill rates can leave weak spots in the material profile. Dropping injection speed allows material to pack together more tightly.
- Extend cooling time: I know, I know… longer cycle times eat into productivity. But allowing parts to cool fully before ejecting avoids removing them in a “solidified but still shrinking” state.
Pro tip: Don’t crank pressures sky high right off the bat. Start conservative and increase gradually while assessing part quality. Excessive pressure can also cause issues like sink marks, voids or flashes.
How Much to “Oversize” for Shrinkage?
Now comes the moment of truth.
Putting all this insight into practice ultimately requires one more step — compensating for shrinkage by intentionally oversizing the mold cavity.
But by how much?
As always, there are no hard and fast rules. Shrinkage depends on all the factors outlined above. The best answer comes from producing samples that mimic your production mold/process as closely as possible.
However, here are some ballpark oversizing targets based on the resin you’re working with:
- Polyethylene (PE): 2-5%
- Polypropylene (PP): 1.5-3%
- Acrylonitrile Butadiene Styrene (ABS): 2-4%
- Nylon: 2-4%
These percentages need to be validated through sampling runs, but they provide reasonable starting points for initial mold sizing.
The key is to tweak dimensions from there based on real measured data from molded parts. It takes some iterative tweaking, but zeroing in on the exact oversize needed to produce accurately sized, dimensionally stable parts is worth the effort.
No one said injection molding was easy! But a bit of knowledge combined with some strategic process tweaking goes a long way to minimizing shrinkage.
And when all is said and done, that nicely sized part popping out of the mold makes it all worthwhile!