Injection molding and 3D printing are two of the most popular manufacturing methods for producing plastic parts. Both have their advantages and disadvantages when it comes to factors like cost, speed, strength, design freedom and more.
So how do you know which process is better for your specific application? In this comprehensive guide, as a professional injection molding manufacturer, we’ll compare injection molding vs 3D printing across ten factors to help you make the right choice.
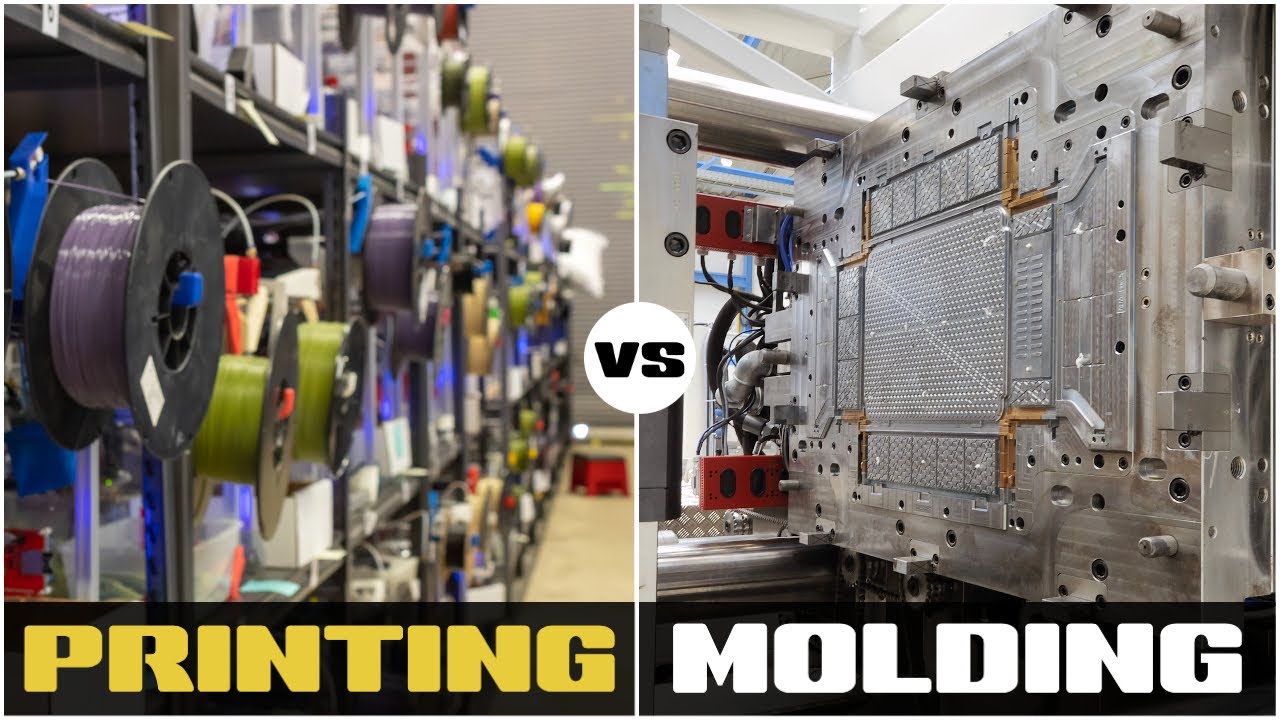
How Injection Molding Works
Injection molding creates plastic parts by injecting molten plastic material at high pressure into a mold. The mold has a cavity that gives the part its shape.
Here’s a quick overview of the injection molding process:
- Plastic pellets are fed into a heated barrel where they melt.
- A screw injects the molten plastic into the mold cavity with pressure.
- The plastic cools and solidifies into the final part shape.
- The mold opens and the part gets ejected out.
This process allows for rapid production of intricate, high-tolerance plastic parts. However, injection molding does require upfront investment in steel or aluminum tooling.
How 3D Printing Works
3D printing builds up plastic parts layer-by-layer using materials like plastic filament, resin or powder. Parts are produced from 3D model files rather than traditional tooling.
The basic process looks like this:
- A digital 3D design file is sliced into layers
- The printer lays down successive layers of material
- Layers are fused together creating the final part
With no tooling required, 3D printing allows for fast design iterations and on-demand production. However, cycle times for printing each part are slower compared to injection molding.
Now that we’ve covered the basics of each process, let’s see how they compare across ten important factors:
Injection Molding vs 3D Printing: Which Method is Better?
Lead Time
- Injection molding – Weeks or months; time is required to machine steel/aluminum molds
- 3D printing – Hours or days; no tooling minimizes lead time
Clearly, 3D printing has a significant advantage when it comes to lead time. The ability to go straight from design to printed part makes it ideal for prototypes and low volume production.
Setup Cost
- Injection molding – $10,000+ for a single steel mold
- 3D printing – $100 to $1,000+ for printer
Injection molds are expensive precision tools often costing tens of thousands of dollars. 3D printers have become very affordable in comparison.
Part Quantity
- Injection molding – Thousands to millions of parts
- 3D printing – 10 to 10,000+ parts
Injection molding economics favor high quantities to maximize mold utilization. 3D printing tends to make more sense for fewer parts.
Part Size
- Injection molding – No restrictions; only limited by mold/press size
- 3D printing – Constrained by printer build volume
Very large parts may only be possible with injection molding depending on the 3D print technology used. New large-scale 3D printers can produce big parts fast.
Design Freedom
- Injection molding – Restrictive; draft angles required
- 3D printing – High degree; complex geometries easily printed
3D printing offers far more freedom when it comes to part geometry. Self-supporting angles and complex internal structures are no problem.
Accuracy and Tolerances
- Injection molding – ±0.005 inch or tighter
- 3D printing – ±0.030 inch average; varies by process
Precision steel molds allow injection molding to achieve tighter tolerances. 3D printing accuracy is steadily improving but still trails injection molding.
Surface Finish
- Injection molding – Glossy, smooth finish from molded tool
- 3D printing – Layer lines cause rough “stair-step” finish
Most injection molded parts have a better cosmetic appearance straight from the mold with no post-processing required. 3D printed parts typically need sanding/polishing.
Part Strength
- Injection molding – Excellent; dense, uniform material
- 3D printing – Varies; depends on print orientation
The layer-based fabrication process of 3D printing leads to anisotropic material properties. Parts may be weaker along certain axes.
Material Options
- Injection molding – Broad range; hundreds of thermoplastics/thermosets
- 3D printing – Limited but growing set of plastics
Injection molding works with just about any plastic resin. Material choices for 3D printing are currently narrower but rapidly expanding.
Environmental Impact
- Injection molding – High scrap rates; non-recyclable runners
- 3D printing – Low waste; supports easily removed/recycled
Given its additive nature, 3D printing uses only the required amount of material leading to less waste. Machining molds also has a higher environmental cost.
When Should You Use Injection Molding vs 3D Printing?
Now that you know the core differences between the two manufacturing methods, here is a quick guide on when injection molding or 3D printing is the better choice:
Best Applications for Injection Molding
- High volume production runs exceeding 10,000+ parts
- Tight tolerance and precision requirements
- Parts with fine production-grade finishes
- Situations where material strength is critical
- Large overall part sizes
Best Applications for 3D Printing
- Prototyping and early testing with functional thermoplastics
- Bridge manufacturing before injection molding tools are ready
- Short design-to-part lead times
- Low to medium production volumes under 10,000 parts
- Complex and custom part geometries
- Jigs, fixtures, assembly aids and end-use production tools
Keep in mind you don’t necessarily have to choose one or the other. Many product development projects start with 3D printed prototypes, then use a small batch of injection molded parts for testing, before finally ramping up to full mass production.
Combining 3D printing and injection molding allows you to leverage the strengths of each process at the appropriate stage. This hybrid strategy results in getting high quality products to market faster.
The Bottom Line
When weighing injection molding vs 3D printing, there’s no universally “better” choice. The right manufacturing method depends on parameters like quantity, quality, design, lead time and more.
Injection molding makes sense for mass production while 3D printing suits low volumes with customization. Often, utilizing both technologies in tandem yields the best results.
Hopefully this overview gives you a balanced perspective on the injection molding vs 3D printing decision. Reach out if you need any guidance selecting the optimal process for your next project!