The debate between 3d printing versus injection molding has been going on for years in manufacturing circles. With advancements in additive manufacturing, the question arises – is 3d printing cheaper than injection molding?
This comparison seeks to provide an up-to-date, data-driven analysis on the cost differences between these two popular manufacturing processes. As a professional plastic injection molding manufacturer, I aim to settle this debate once and for all through an objective assessment.
Let’s start from the basics before diving into the pricing breakdown.
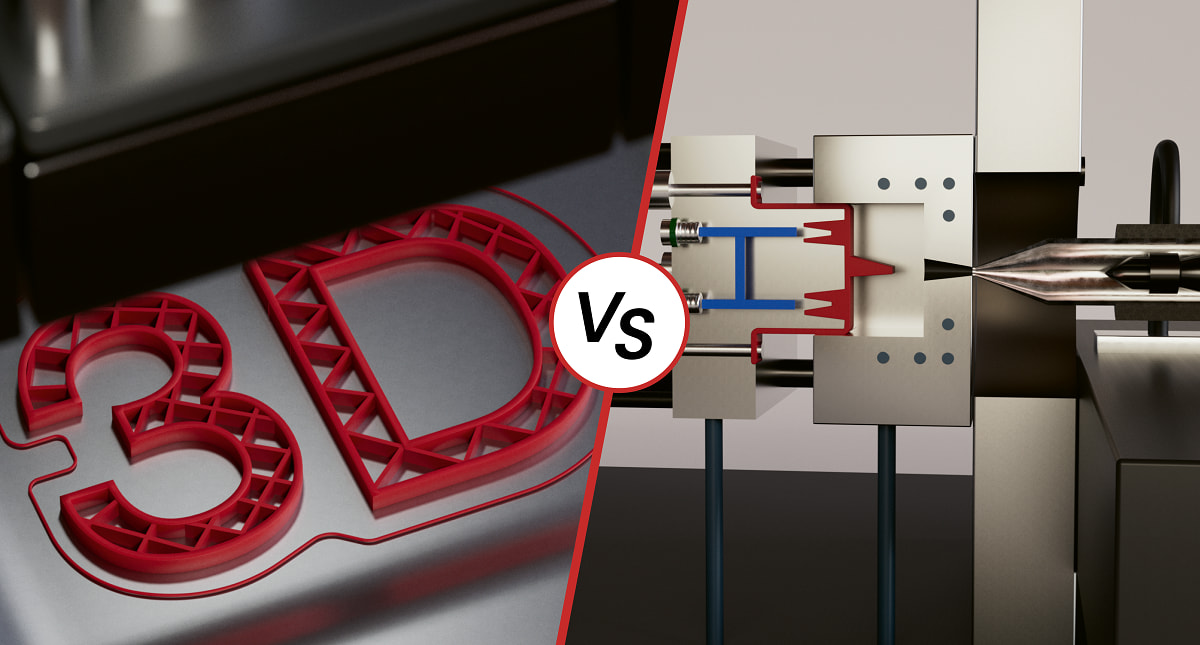
What Are 3d Printing and Injection Molding? A Quick Primer
First of all, 3d printing refers to a process called additive manufacturing. It involves creating three-dimensional objects by depositing material layer upon layer from the bottom up.
Common 3d printing technologies you may have heard of include FDM (Fused Deposition Modeling), SLA (Stereolithography), and SLS (Selective Laser Sintering). Each method utilizes different materials and techniques, but the underlying principle stays the same.
On the other hand, injection molding is a manufacturing process that has been around for decades. It works by injecting molten plastic into a mold cavity and allowing it to cool and solidify into the final shape.
The upfront cost mainly comes from CNC machining the steel mold required. But once the mold is ready, the per part cost becomes very affordable through large scale production.
Now that we’re familiar with both processes, let’s analyze the exact pricing differences through real-world data.
Factors That Make Production Cost Vary Between 3d Printing vs Injection Molding
Like all manufacturing, pricing depends on a variety of factors including:
- Build volume
- Part size
- Material
- Labor
- Print time
- Required tooling
Accounting for all variables allow us to make an apples-to-apples comparison.
Right off the bat, we know injection molding has high upfront costs from steel machining. 3d printing pays as you go with no expensive tooling.
However, 3d printing takes longer to produce each part which significantly impacts pricing at scale. Let’s explore this idea further through an example.
Case Study: 3d Printed Drone Frame vs Steel Mold and Plastic Parts
To clearly demonstrate the pricing dynamics, we will analyze a real world project – manufacturing drone frames.
A designer requires small batches between 1 to 250 units. Two options are viable here:
Option A: 3d Print with FDM
FDM printers lay down plastic filament layer by layer to build parts.
For our 10 inch x 4 inch x 2 inch drone frame, a desktop FDM printer can manufacture each unit for $45 when accounting for:
- Machine time
- Labor
- Filament material
At 250 units total, the final price is $45 x 250 = $11,250
Option B: Injection Mold
First, we CNC machining the steel mold at around $5,800. But now we can produce plastic drone frames for only $6 each.
Assuming 250 drone frames like our 3d printing example, the production costs are:
- Mold tooling = $5,800
- 250 units x $6 per unit = $1,500
The total comes out to $7,300. Even when factoring in the mold tooling costs, at this quantity injection molding is significantly cheaper.
You can see how the production volume and method impact final pricing. Another aspect we must account for is part size and complexity…
Analysis: Production Volume Thresholds and Dimensions
Our case study clearly illustrates how production volume changes the equation between 3d printing vs injection molding pricing. But what volumes exactly make injection molding start to make sense?
Small Parts Under 4 Cubic Inches
For tiny, highly complex parts, 3d printing remains cheaper up until 1,000 units.
The compact build volume means less plastic filament used. And the $6,000 mold tooling costs don’t offset such a low quantity.
An example would be a small but high precision plastic gear.
Medium Parts Between 4 inch^3 to 12 inch^3
When it comes to medium sized parts like our drone frame, the minimum viable quantity is around 500 units.
Here the mold tooling balances out against the rising filament costs. Although 3d printing stays competitive up to ~500 units.
Large Parts Over 12 Cubic Inches
For bigger parts with lower relative complexity, the tipping point can be as low as 100 units.
Bulky 3d prints become exponentially expensive from increased material demands. Yet, the $10,000+ mold makes up for this starting at ~100 large parts.
An example would be printing giant LEGO blocks versus injection molding.
By accounting for both volumes and geometries between 3d printing versus injection molding cost per part, we arrive at a more holistic understanding.
Is 3d Printing More Affordable for Prototypes? Analysis of NRE Costs
The data so far has focused specifically on manufacturing costs. But for new product development, you cannot underestimate the NRE (Non-Reoccurring Engineering) costs.
NRE refers to design and testing costs prior to full production. This includes creating CAD models and prototypes for validation.
Is 3d printing cheaper than injection molding when it comes to prototyping?
The short answer is – absolutely.
Let’s say you print 20 different design iterations with a desktop FDM 3d printer before settling on a final drone frame.
At $50 each, your total prototype cost is $1,000.
But employing CNC machining for injection mold prototypes will run you around $2,500 per version. After optimizing just 5 designs at $12,500, 3d printing is over 10X cheaper already for prototyping purposes.
The ease of uploading tweaked CAD models combined with no expensive tooling makes additive manufacturing vastly more affordable during the design phase. And given that injection molds last for hundreds of thousands of cycles, it makes zero sense to spend this capital before finalizing the perfect design.
Key Takeaways – Is 3d Printing More Cost Effective Overall?
By taking a data oriented approach to analyzing pricing, we can determine guidelines on when 3d printing versus injection molding makes sense:
- 3d printing almost always cheaper for design prototyping because it has no NRE costs
- Final production volumes and part sizes are key factors for manufacturing pricing
- 3d printing only makes sense up to ~1000 units for tiny parts and ~100 units for large bulky parts
- Injection molding becomes exponentially more affordable at production scales above these thresholds
In Conclusion
Is 3d printing cheaper than injection molding?It depends.For businesses preparing to scale production, injection molding does provide the most bang for buck in the long run. But without question, additive manufacturing accelerates product development what can in many cases determine the success or failure of a new product release.
The true optimal path forward likely incorporates both complementary processes at different development stages. As 3d printing and molding technologies continue advancing, we unlock incredible potential for innovating world-changing products.
With the right application, additive manufacturing provides unmatched affordability during prototyping and early testing that is critical for today’s agile hardware startups. But once designs finalize and volumes rise, injection molding simply cannot be beaten from quality to price at mass production levels.