Acetal plastic, also known as polyoxymethylene (POM), is one of the most versatile engineering thermoplastics used in injection molding applications. In this comprehensive guide, as a professional plastic injection molding manufacturer, I’ll share if and why acetal plastic is commonly used for injection molding.
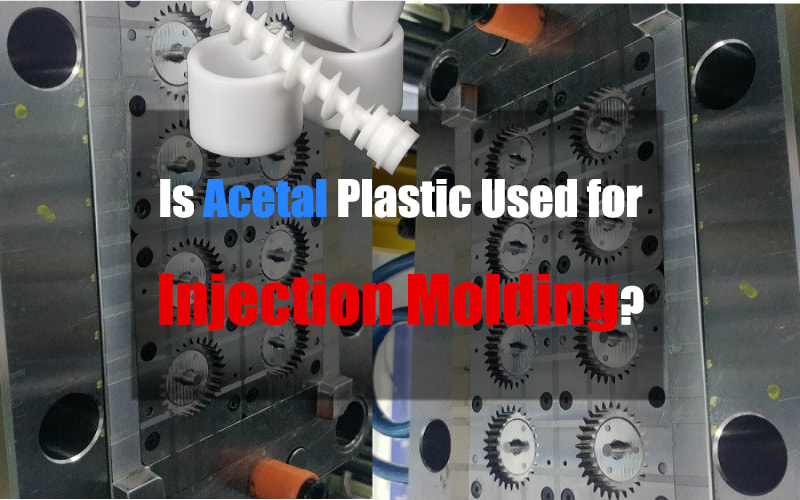
Acetal Plastic Overview
Let’s start with an overview of acetal plastic. Acetal, the shortened term for polyoxymethylene (POM), is a highly crystalline thermoplastic polymer made from formaldehyde. It has excellent mechanical properties, low coefficient of friction, high chemical resistance and dimensional stability.
Acetal polymers consist of long molecular chains of repeating CH2O units connected by acetal linkages. Based on their chemical structure, they can be classified into two types:
Homopolymer acetal – Made up of only oxymethylene units
Copolymer acetal – Contains alternating sequences of oxymethylene and oxyethylene units
The most well-known brand of homopolymer acetal is DuPontTM Delrin®. Some key properties that make acetal suitable for injection molding include:
High strength and stiffness – Acetal has a tensile strength of 65-70 MPa and tensile modulus of 3,000-4,600 MPa. This imparts great load-bearing capacity.
Low friction – Dynamic coefficient of friction of acetal against steel is 0.25-0.35, enabling smooth sliding motion.
Excellent dimensional stability – Moisture absorption is only 0.2%, leading to highly stable dimensions.
Good chemical resistance – Resistant to alcohols, esters, ketones and other organic solvents.
Easy machinability – Can be precision machined easily similar to metals.
FDA compliance – Meets FDA regulations for food contact.
These exceptional properties of acetal make it well-suited for injection molding high-performance plastic components.
Is Acetal Plastic Used for Injection Molding?
Yes, acetal plastic is one of the most versatile thermoplastics used for molding high-precision, low friction and chemically resistant plastic components across industries.
Why Acetal Plastic is Used for Injection Molding
Here are the key reasons why acetal is one of the most widely injection molded plastics globally across industries:
1. Dimensional Stability
The outstanding dimensional stability of acetal is a major advantage for maintaining tight tolerances in injection molded parts. This stems from its highly ordered crystalline structure and low moisture absorption tendency.
Complex plastic parts often shrink and warp during manufacturing. But acetal’s dimensional consistency enables molding precision plastic components with accurate dimensions.
2. High Load-bearing Strength
With a tensile strength upwards of 65 MPa and modulus of 3,000 MPa, acetal imparts greater mechanical strength than most thermoplastics. This makes acetal suitable for injection molding high-strength parts for load-bearing and high-stress applications.
3. Low Friction and Wear Resistance
Acetal has an inherently low coefficient of friction against metals and other plastics. This self-lubricating property minimizes friction and associated energy losses in moving mechanical assemblies.
The excellent sliding capacity coupled with outstanding wear resistance provides durable low-maintenance operation of injection molded acetal components. Common examples include gears, bushings, bearings, etc.
4. Broad Chemical Resistance
Acetal offers good resistance to a wide variety of chemicals including oils, greases, aliphatic hydrocarbons and alcohols. It can withstand exposure to gasoline, diesel fuel, aqueous salt solutions, dilute acids and bases.
This allows molded acetal parts to retain structural and functional integrity when exposed to different chemicals.
Applications of Acetal Injection Molding
Here are some common applications of injection molded acetal components across major industries:
Automotive Industry
Gears, pulleys, wipers, handles, connectors, insulators
Medical Devices
Valves, precision gears, orthopedic parts, surgical instruments
Food Processing Equipment
Conveyors, chutes, gears, bearings
Appliances
Washing machine agitators, blender blades, clock gears
Electrical Equipment
Switch parts, insulation parts, connectors, breakers, sensors
Acetal grades – Unmodified acetal, Glass fiber reinforced (10-30% GF), Impact modified, Lubricated, Conductive acetal containing carbon fibers
In all these applications, manufacturers leverage acetal’s exceptional dimensional accuracy, strength, smooth sliding motion and long-term chemical resistance by injection molding parts using different acetal grades.
Key Considerations for Injection Molding Acetal
While acetal offers outstanding moldability, here are some design and processing guidelines to follow:
- Maintain uniform wall thickness as much as possible
- Minimum draft angles of 0.5-1°
- Generous internal radii to minimize stress concentration
- Fine polishing of cavity surface
- Low injection speeds
- Medium melt & mold temperatures
Adhering to these acetal injection molding best practices results in dimensionally accurate and aesthetically appealing molded plastic parts in an efficient and cost-effective manner.
In Summary
The acetal’s unique balance of mechanical properties and chemical resistance coupled with excellent processability make it one of the top choices for injection molding high-performance plastic components across sectors. Leveraging the right acetal grade and following ideal molding guidelines helps reap maximum benefits out of this exceptional material.