Injection molding can produce high volumes of plastic parts efficiently and precisely. However, the high initial costs make small batch production expensive. Is injection molding ultimately a cost-efficient process? As with most manufacturing processes, the cost dynamics depend greatly on the production volume. As a professional plastic injection molding manufacturer, I will help you find it out!
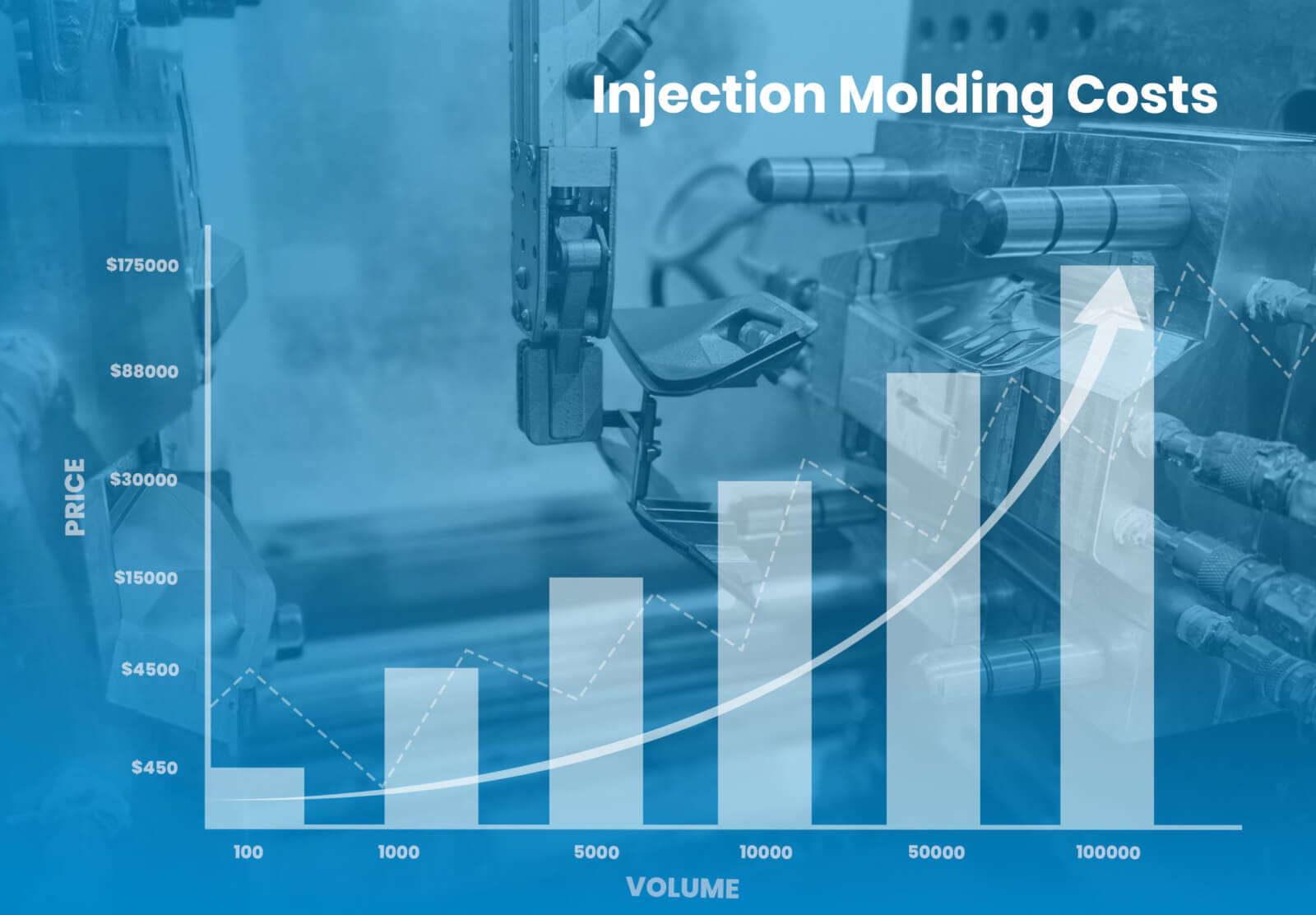
Is Injection Molding Cost Efficient?
The short answer is “it depends”. For mass production, injection molding offers exceptional value. But for small batches, the numbers rarely make sense. By understanding these cost dynamics, plastics manufacturers can determine if adopting injection molding aligns with their budget and business goals.
Upfront Costs Can Be Substantial
Let’s start by looking at some of the major upfront costs involved with injection molding:
Injection Molding Machines
Industrial injection molding machines range from $50,000 for medium-sized machines to over $200,000 for large machines designed for high-volume production. These substantial equipment costs place injection molding out of reach for small companies looking to produce small batches.
Creating Steel Molds
Tooling represents one of the biggest upfront costs. Steel molds for injection molding can run from $5,000 for simple molds up to $100,000 or more for large, complex molds. Developing molds requires extensive machining time and expertise. All this racks up costs before even a single part comes off the production line.
Engineering and Design Costs
There are also significant engineering and design costs involved. Creating 3D CAD models and drawings, analyzing mold flow, and refining the mold tool design all require an investment of skilled labor. These expenses can also tally up quickly.
So clearly, getting an injection molding operation off the ground requires some deep pockets. But once the infrastructure is in place, the incremental costs of production can be extremely low.
Economies of Scale Make It Ideal for Mass Production
As mentioned earlier, the initial tooling represents a major fixed cost. But once the steel mold is fabricated, it can churn out hundreds of thousands of plastic parts before requiring maintenance or replacement. And the raw plastic material is cheap, costing between $0.90 to $2.30 per pound on average.
So while setup costs are steep, incremental production costs are minimal, allowing the price per unit to drop exponentially with volume.
To demonstrate, let’s look at a hypothetical example. Say a company invests $20,000 to have a steel mold fabricated and purchases an injection molding machine for $75,000. If they only require 100 units, then the cost per piece is $950…extremely expensive plastic parts!
But if they require 100,000 units, then the cost per unit plummets to just $0.95 per piece. Now that represents some serious value for money!
This dynamic of high fixed costs and low variable costs makes injection molding ideal for mass production volumes. The more units produced, the more the initial investment gets amortized, leading to very attractive per-piece costs.
Steps To Improve Cost Efficiency
For companies hoping to adopt injection molding, particularly those intending to produce small batches, here are three tips to maximize cost efficiency:
1. Use Rapid 3D Printed Tooling
With resin-based 3D printing, molds can be printed for $100 to $5,000 rather than having steel molds CNC machined for up to $100k. Although less durable than metal tools, 3D printed molds allow producing small batches far more affordably.
2. Consider Outsourcing
Rather than purchasing expensive equipment, outsourcing to a specialty injection molding company reduces startup costs. Specialists have the machines, materials, and expertise to cost-effectively handle small batch orders.
3. Order Larger Volumes When Possible
It almost always makes sense to produce extra units, even if it means holding stock. Because the incremental cost per additional piece is negligible, spending a bit more upfront to order a larger volume significantly drives down the cost per unit.
The Verdict? Yes, With Large Volumes
So in summary, injection molding can be extremely cost efficient if high production volumes are required. The high upfront expenses and lack of flexibility make small batches cost prohibitive. Companies hoping to adopt injection molding should focus on high volumes, rapid tooling, or outsourcing to maximize cost efficiency.
For producing 1,000+ units, injection molding represents one of the most affordable plastic part manufacturing methods. But for prototyping and volumes below 100-500 units, alternative technologies like CNC machining and 3D printing tend to make more financial sense.