Lo stampaggio a iniezione è uno dei processi produttivi più versatili ed economici per la produzione di parti in plastica su scala. Dai Lego alle custodie per iPhone, innumerevoli prodotti che utilizziamo ogni giorno sono nati come plastica fusa iniettata in stampi di acciaio lavorati con precisione.
Tuttavia, lo stampaggio a iniezione sfrutta il suo potenziale solo se si progettano pezzi specifici per il processo. A differenza della stampa 3D o Lavorazione CNCI componenti stampati a iniezione hanno requisiti di progettazione molto severi per riempire correttamente gli stampi, evitare difetti ed essere espulsi in modo pulito dall'attrezzatura dopo il raffreddamento.
Ignorare i principi di progettazione dello stampaggio a iniezione può comportare notevoli ritardi e costi inutili praticamente in ogni fase, dalla prototipazione alla produzione. Inoltre, dato che il processo prevede costose attrezzature in acciaio, le modifiche al progetto dopo la fabbricazione dello stampo possono essere estremamente dispendiose in termini di tempo e denaro.
In questa guida completa, come professionista produttore di stampaggio a iniezioneCondividerò i miei migliori consigli e strategie per la progettazione di parti in plastica per il successo dello stampaggio a iniezione. Imparerete a conoscere considerazioni critiche sulla progettazione, come lo spessore uniforme delle pareti, gli angoli di sformo, la progettazione di nervature e bocche, il ritiro del materiale, la finitura superficiale e molto altro ancora.
Iniziamo con le basi del processo di stampaggio a iniezione. Capire esattamente come la plastica fusa fluisce nelle cavità aiuterà molte linee guida di progettazione ad avere senso.
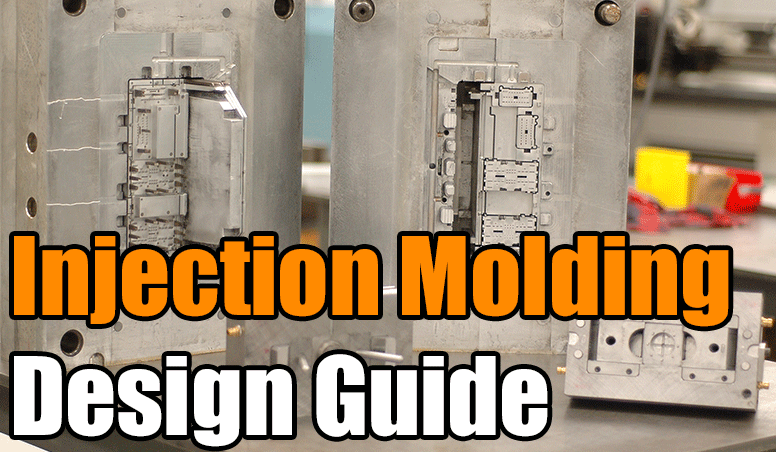
Che cos'è lo stampaggio a iniezione e come funziona?
Le macchine per lo stampaggio a iniezione riscaldano i pellet di resina plastica per fonderli in un liquido che le macchine forzano in stampi di acciaio sotto un'intensa pressione idraulica. Dopo che la plastica si è raffreddata e solidificata, lo stampo si apre ed espelle roboticamente i pezzi finiti.
Gli stampi contengono due componenti principali in acciaio:
- Cavità: La metà anteriore dell'utensile crea le caratteristiche visive esterne dei pezzi. È comunemente chiamata "lato A" dell'utensile.
- Nucleo: La metà posteriore dello stampo forma la geometria interna e in gran parte nascosta, come le nervature, le bugne, gli inserti e altre caratteristiche funzionali. Gli stampatori a iniezione spesso chiamano questo lato "B".
Il punto in cui le due metà dello stampo si incontrano forma la linea di separazione, che è una piccola linea di testimonianza visibile sui componenti dopo la produzione.
La comprensione dei fondamenti delle macchine e degli utensili per lo stampaggio a iniezione è fondamentale per progettare pezzi di successo con questo processo. Vediamo le principali considerazioni sulla progettazione che ogni ingegnere deve tenere a mente.
Linee guida fondamentali per lo stampaggio a iniezione
Sebbene gli stampatori a iniezione siano in grado di produrre componenti in plastica incredibilmente precisi e complessi, gran parte del loro controllo di processo si concentra sul perfezionamento di parametri quali temperatura, pressione, forza di chiusura e tempi di ciclo.
In qualità di progettista di componenti, la vostra responsabilità è quella di progettare prodotti adatti alla realtà del flusso di materie plastiche fuse in utensili d'acciaio dal costo superiore a $100.000.
Ecco i miei migliori consigli per ottenere il massimo dal processo di stampaggio a iniezione:
Spessore della parete
La linea guida più importante per la progettazione dello stampaggio a iniezione è il mantenimento di uno spessore uniforme delle pareti in tutti i pezzi. Quando la plastica si raffredda, si restringe. Le parti non uniformi causano un raffreddamento non uniforme, con conseguente deformazione o incrinatura dei componenti.
Ecco alcune regole importanti quando si considera lo spessore delle pareti per il proprio programma:
- Spessore target tra 2-4 mm per la maggior parte delle applicazioni. È possibile realizzare parti a parete ultra-sottile inferiori a 1 mm, ma richiede una precisione estremamente elevata.
- Non variare mai lo spessore delle pareti di più di 15% in ogni singola parte per evitare un raffreddamento non uniforme.
- Quando si deve passare da una parete più spessa a una più sottile, utilizzare smussi o filetti graduali per garantire un flusso regolare.
Inoltre, le pareti spesse non solo si restringono di più, ma trattengono il calore. Pareti più sottili e uniformi producono meno scarti dovuti a problemi di raffreddamento. I cicli più rapidi riducono anche i costi di produzione.
Angoli di sformo
Il ritiro della plastica che si attacca alle pareti degli stampi in acciaio blocca le linee di produzione, danneggia gli utensili e fa aumentare gli scarti. Mentre le superfici strutturate aiutano i pezzi a staccarsi dall'attrezzatura, gli angoli di sformo consentono l'espulsione robotizzata dei pezzi senza problemi.
L'abbozzo consiste nel rastremare leggermente le pareti verticali, di solito tra 1 e 5 gradi, per evitare che i componenti stampati si incollino. Come linee guida:
- Aggiungere un tiraggio minimo di 2 gradi su tutte le pareti verticali.
- Aumentare gli angoli di sformo su elementi più alti del nucleo/cavità o su finiture superficiali profondamente strutturate.
Gli stampi in acciaio richiedono manutenzione e sostituzioni periodiche nel corso della produzione. Tuttavia, angoli di sformo efficaci prolungano la durata complessiva dell'utensile.
Design della nervatura e del bocchettone
Le nervature e le bugne rafforzano sezioni altrimenti a parete sottile e soggette a flessione o deformazione sotto carico. La corretta integrazione di queste caratteristiche consente di ridurre l'uso di materiale e i costi, prevenendo al contempo i guasti.
Seguite queste regole di progettazione per le nervature:
- Aggiungere dei filetti alla base di tutte le costole per garantire la resistenza.
- Impostare lo spessore della nervatura tra 50-60% dello spessore nominale della parete per evitare l'affondamento.
- Per le parti estetiche, mantenere l'altezza della nervatura al di sotto di 2,5 volte lo spessore per eliminare il restringimento visibile.
Le linee guida del capo includono:
- Dimensioni del diametro esterno dell'attacco 2,5X diametro della ferramenta (viti, ecc.).
- Limitare lo spessore del bocchettone a <60% delle pareti per evitare segni di lavandino sulle superfici esterne visibili.
- Aggiungere i tasselli dalle bocche alle pareti adiacenti per garantire la rigidità.
Le nervature di rinforzo e le boccole per la ferramenta ben progettate sono il segno distintivo di componenti stampati a iniezione funzionali e durevoli.
Tassi di ritiro del materiale
Ogni materiale plastico si ritira in modo diverso quando si raffredda all'interno degli stampi a iniezione. Tuttavia, la maggior parte di essi si restringe tra 2-4%, il che deve essere preso in considerazione nei progetti.
Se si trascura il ritiro, i pezzi sottodimensionati non sono in grado di assemblarsi correttamente con i componenti di accoppiamento nel prodotto finito. Il trucco consiste nel compensare progettando deliberatamente pezzi leggermente sovradimensionati.
Le tecniche più comuni utilizzate dagli stampisti esperti comprendono:
- Aumento dello spessore complessivo della parete.
- Aggiunta di interferenze come le nervature di schiacciamento sugli inserti.
- Progettazione di grandi montanti a pressione al posto dei fori.
Esaminare i dati di ritiro degli stampi del produttore durante la selezione dei materiali. Inoltre, prototipare nuovi stampi per confermare le corrette strategie di compensazione del ritiro.
Una corretta progettazione del ritiro evita i problemi legati alle operazioni secondarie di post-stampaggio.
Linee di separazione
In precedenza, abbiamo esaminato le basi degli stampi a iniezione multi-pezzo e come si formano i componenti in cui le metà si incontrano lungo la linea di divisione.
Come linea guida di progettazione, la localizzazione delle linee di divisione richiede un equilibrio estetico/funzionale e il riconoscimento del loro impatto sulla producibilità.
Per quanto riguarda l'aspetto estetico, spesso nascondiamo le linee di separazione lungo spigoli vivi non cosmetici o le posizioniamo sul retro dei componenti. Le azioni laterali e altri meccanismi complessi fanno lievitare i costi di attrezzaggio per la sigillatura su superfici curve.
Un ottimo posizionamento della linea di divisione migliora anche la resistenza dello stampo e il ciclo di vita. È sufficiente prestare attenzione ai punti di riempimento, ai sottosquadri e all'espulsione per evitare l'erosione.
Posizione/tipo di cancello
La progettazione dei gate è direttamente legata al successo dello stampaggio, in quanto introducono la plastica fusa nelle cavità. La posizione dei cancelli influenza notevolmente i tempi di ciclo, le pressioni di iniezione richieste e l'estetica dei componenti.
I tipi di cancelli più comuni sono:
- Cancelli perimetrali: L'approccio più diffuso prevede un profilo rettangolare lungo la linea di demarcazione.
- Cancelli a punta calda: Il cancello rotondo iniettato attraverso il tetto della cavità è il migliore per la concentricità.
- Cancelli diretti: Cancelli grandi per un rapido riempimento dello stampo, ma richiede la rimozione del cancello secondario.
Al di là del tipo, attenetevi ai seguenti principi fondamentali per la collocazione dei cancelli:
- Posizionare i cancelli per riempire prima le sezioni dello stampo più profonde.
- Tenere lontano da superfici cosmetiche o da punti ad alta sollecitazione.
- Utilizzare più porte per facilitare il riempimento di geometrie complesse.
I gate agiscono essenzialmente come "materozze" che guidano il flusso di plastica nelle cavità dello stampo, proprio come nella colata. L'attenzione alla quantità, alla forma, al posizionamento e alle dimensioni dei gate rimane fondamentale per uno stampaggio a iniezione senza difetti e ad alta resa.
Il bilancio
Si spera che questa guida abbia fornito alcune utili linee guida di alto livello per la progettazione dello stampaggio a iniezione come introduzione. Ora che avete compreso le linee guida principali e avete accesso a risorse supplementari, siete pronti a progettare incredibili pezzi in plastica ottimizzati per la produzione con stampaggio a iniezione di precisione.
La messa in pratica di questi concetti snellirà la pre-produzione, preverrà i difetti e porterà alla creazione di linee di produzione robuste che sfornano prodotti impeccabili.
Quali domande di progettazione vi vengono in mente quando vi avventurate nel vostro prossimo progetto di componenti stampati a iniezione? Non esitate a contattarmi se volete approfondire l'argomento. Sono sempre felice di aiutare i colleghi a rafforzare le capacità tecniche e a condividere le migliori pratiche.