Lo stampaggio a iniezione è oggi uno dei processi produttivi più comuni e versatili. Dall'elettronica alle apparecchiature mediche ai prodotti di consumo, le parti in plastica stampate a iniezione sono presenti in quasi tutto ciò che ci circonda. Il processo è abbastanza semplice: la resina plastica viene fusa sotto estremo calore e pressione in una plastica liquida, quindi iniettata in stampi metallici complessi e chiusi per creare parti dalla forma complessa.
Lo stampaggio a iniezione di pezzi grandi condivide lo stesso concetto di base, ma coinvolge processi, attrezzature e stampi più grandi. Proprio come i pezzi più piccoli, i componenti stampati a iniezione di grandi dimensioni richiedono un delicato equilibrio di decine di variabili diverse per produrre un buon pezzo, dalla formulazione della resina alla tempistica precisa del processo di iniezione. E quando si lavora con volumi maggiori di materiale plastico, diventa ancora più impegnativo controllare e ottimizzare il processo.
Un parametro chiave di successo per stampaggio a iniezione di grandi parti è il tempo di ciclo: il tempo che intercorre tra l'iniezione della plastica nelle cavità dello stampo e l'espulsione del pezzo finito, per poi ricominciare da capo. Poiché le aziende di stampaggio di materie plastiche spesso producono volumi elevati di pezzi, tempi di ciclo più lunghi significano una minore produzione di pezzi. E questo può avere un forte impatto sui costi dei pezzi per i clienti che pagano per componente. Per questo motivo, le grandi aziende di stampaggio a iniezione lavorano costantemente per ridurre il più possibile i tempi di ciclo.
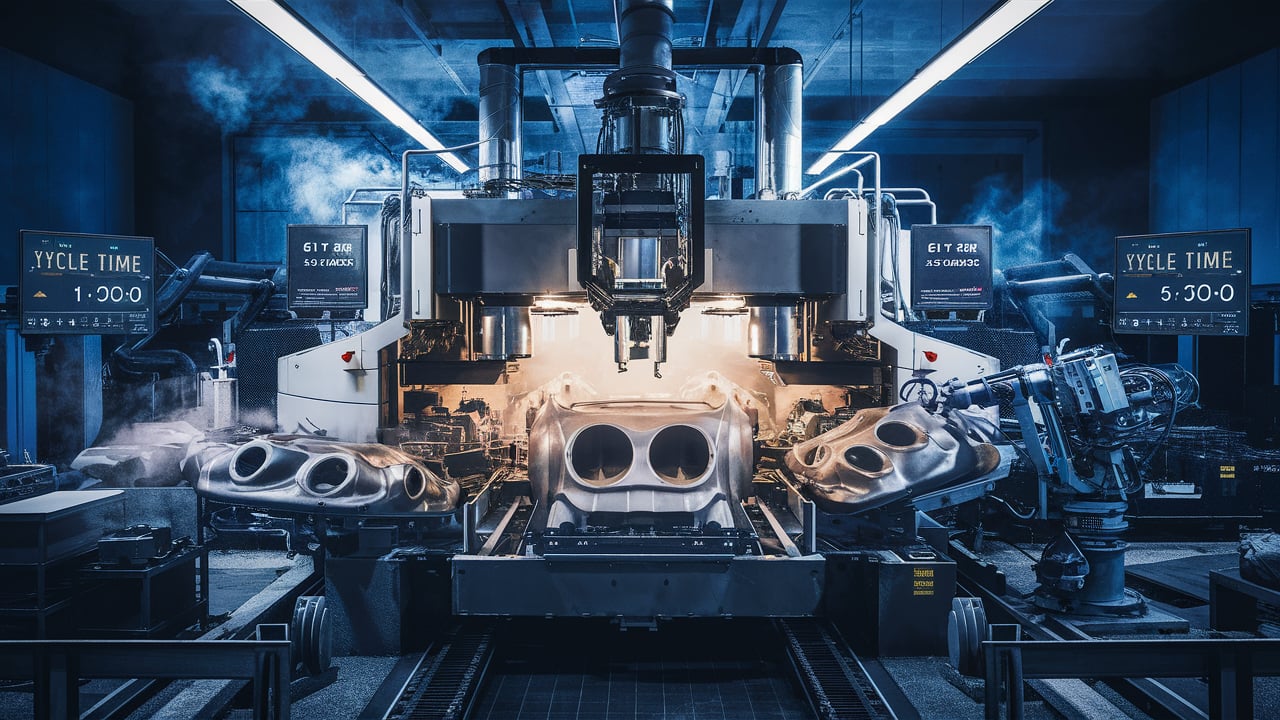
Come ridurre il tempo di ciclo dello stampaggio a iniezione di pezzi di grandi dimensioni
Quando si tratta di stampaggio a iniezione di pezzi di grandi dimensioni, esistono opportunità per ridurre i tempi di ciclo fin dalle prime fasi di pianificazione. Quasi ogni componente del processo ha un impatto sui tassi di produzione dei pezzi, dagli stampi stessi alle dimensioni delle macchine. E ogni fase può essere sfruttata attraverso l'ottimizzazione del processo o una tecnologia avanzata. Vediamo alcuni dei modi in cui le grandi aziende di stampaggio a iniezione stanno migliorando i tempi di ciclo per i componenti in plastica di grandi dimensioni.
Progettare tenendo conto dei tempi di ciclo
La riduzione dei tempi di ciclo dello stampaggio a iniezione di grandi pezzi inizia con la progettazione del pezzo stesso. In generale, quanto più larghe e spesse sono le pareti e le dimensioni complessive di un pezzo in plastica, tanto più lungo sarà il tempo di solidificazione. Pertanto, il modo migliore per migliorare i tempi di ciclo è ridurre lo spessore delle pareti e le dimensioni complessive dei componenti in plastica, ove possibile.
Oggi progettazione assistita da computer (CAD) offre un controllo molto più avanzato dei parametri per ottimizzare il progetto fin dalle prime fasi.
Ad esempio, un software di simulazione come Moldflow consente ai produttori di vedere come la plastica scorrerà all'interno di una cavità virtuale dello stampo e di evidenziare i potenziali problemi. Ciò significa che è possibile sperimentare diversi spessori delle pareti, posizionamenti delle porte e geometrie dei pezzi, e valutare l'impatto sui tempi di riempimento e sulle velocità di raffreddamento, il tutto all'interno del software. Ciò consente di apportare rapide modifiche al progetto per ridurre al minimo i tempi di ciclo, molto prima di tagliare costosi stampi in acciaio.
Progettazione per un raffreddamento efficiente
Il raffreddamento è di gran lunga la parte più lunga del processo di stampaggio a iniezione, quindi la progettazione dello stampo per un trasferimento ottimale del calore è fondamentale. La maggior parte degli stampi per pezzi grandi incorpora canali di raffreddamento interni per far circolare acqua o olio refrigerato e allontanare rapidamente il calore dalla superficie del pezzo.
La progettazione dei moderni sistemi di raffreddamento è estremamente precisa e consente di posizionare i canali di raffreddamento molto vicino alle caratteristiche del pezzo. I progressi di tecnologie come il raffreddamento conformale (che utilizza la stampa 3D per creare canali curvi che si adattano con precisione a contorni complessi) offrono la possibilità di ottenere velocità di raffreddamento ancora più elevate.
In qualità di produttore di pezzi in plastica, lavorare a stretto contatto con il progettista dello stampo a iniezione per ottimizzare il posizionamento del canale di raffreddamento può produrre notevoli miglioramenti nella riduzione dei tempi di ciclo.
Scegliere il materiale plastico giusto
La scelta della giusta formulazione del materiale è un altro fattore che migliora i tempi di ciclo dello stampaggio a iniezione di grandi pezzi. Proprietà come la temperatura di fusione (quanto deve essere calda la resina prima di fluire) e la conducibilità termica (la velocità con cui il calore si trasferisce attraverso la plastica) possono avere un impatto enorme.
Ad esempio, una resina acrilica può richiedere circa 480 gradi Fahrenheit per fondere e fluire nelle cavità dello stampo. Il nylon, invece, fonde a meno di 420 gradi e si solidifica più rapidamente. Queste differenze possono tradursi in tempi di ciclo più brevi di diversi secondi o addirittura minuti per pezzo, se si considera l'immensa quantità di materiale presente nei componenti stampati a iniezione di grandi dimensioni.
Una consulenza tempestiva con il fornitore del materiale per selezionare la formulazione ideale per cicli più rapidi è preziosa. Anche la personalizzazione delle proprietà della resina in base all'applicazione può essere utile.
Sfruttare il software di simulazione
Come accennato in precedenza, un software di simulazione sofisticato offre un valore immenso nella progettazione di pezzi e processi per cicli di stampaggio a iniezione più rapidi. La simulazione dello stampaggio a iniezione di plastica Moldflow prende in considerazione numerose variabili e simula il modo in cui la resina fluisce, si raffredda e si solidifica nella cavità dello stampo chiuso.
Ad esempio, Moldflow consente di sperimentare diversi punti di iniezione, variabili del ciclo (come la temperatura della colata) e configurazioni dei canali di raffreddamento per raggiungere un equilibrio ottimale. È possibile valutare l'impatto su variabili del ciclo come i tempi di riempimento, le velocità di raffreddamento, la durata totale del ciclo, i requisiti di forza di chiusura e la qualità del pezzo, il tutto all'interno della simulazione.
Il software per lo stampaggio virtuale riduce enormemente i tempi e le congetture una volta realizzati gli stampi di produzione. La maggior parte delle aziende leader nello stampaggio a iniezione di materie plastiche utilizza strumenti di simulazione in quasi tutti i progetti.
Sfruttare la tecnologia di monitoraggio dei processi
I sistemi di monitoraggio del processo che analizzano i dati dei sensori dagli stampi in tempo reale sono estremamente utili per ottimizzare i parametri di iniezione che influiscono sui tempi di ciclo dei pezzi di grandi dimensioni. Questi sistemi (come RJG Technologies eDART) monitorano le variabili chiave durante il processo di stampaggio a iniezione, raccolgono dati e forniscono analisi dettagliate sullo stampaggio, come le curve di pressione di riempimento, le velocità di iniezione e le velocità di raffreddamento.
Questo tipo di dati di feedback consente agli ingegneri di processo di "microottimizzare" tutti i parametri di processo che incidono sui tempi di ciclo, come le temperature di fusione, le velocità di iniezione, le pressioni e le velocità di raffreddamento. E per le applicazioni più impegnative, come i componenti in plastica sovrastampati, il monitoraggio del processo aiuta a garantire la qualità dei pezzi, riducendo al contempo i secondi vitali.
Anche piccoli aggiustamenti di variabili come la velocità di iniezione, la pressione di chiusura dello stampo e il tempo di raffreddamento possono portare a significativi miglioramenti della produttività su lunghe serie di pezzi in plastica. La trasparenza dei dati fornita dal monitoraggio dei processi è indispensabile per il miglioramento continuo.
Investite in macchine più veloci
Con le immense forze di serraggio e le pressioni di iniezione richieste per produrre pezzi commerciali di grandi dimensioni, le macchine per lo stampaggio a iniezione di materie plastiche convenzionali possono talvolta diventare dei colli di bottiglia nel processo.
Piuttosto che cercare di strappare fino all'ultimo briciolo di prestazioni da un'apparecchiatura obsoleta, molti grandi produttori di pezzi scelgono di investire in macchine all'avanguardia. Tecnologie come gli azionamenti elettrici delle pinze stampo (anziché idraulici), i bracci robotizzati multiasse e le presse di grande tonnellaggio consentono di aumentare la velocità di ciclo necessaria per rimanere competitivi a livello globale.
Lo stampaggio di pezzi di grandi dimensioni comporta importanti investimenti di capitale, quindi l'acquisto di macchine aggiuntive per la produzione di volumi più elevati può essere un investimento intelligente a lungo termine per migliorare i profitti. Quando si valutano i costi delle nuove macchine, bisogna sempre considerare i potenziali miglioramenti della produttività nelle proprie proiezioni.
Implementare l'ottimizzazione basata sui dati
In definitiva, qualsiasi processo di stampaggio a iniezione di materie plastiche ha decine di variabili in gioco. Pertanto, i miglioramenti della qualità dei pezzi e della produttività complessiva si riducono all'ottimizzazione continua del processo basata sui dati. Gli stabilimenti più avanzati utilizzano il monitoraggio del processo, la raccolta automatica dei dati, gli strumenti di simulazione e la scienza dei dati per mettere costantemente a punto i parametri di processo.
Quando si tratta di ridurre i tempi di ciclo dello stampaggio a iniezione per pezzi di grandi dimensioni, la creazione di una fabbrica più intelligente e connessa risulta alla fine vincente. Migliorando sistematicamente variabili chiave come i tassi di riempimento/confezionamento dei materiali, i tempi di raffreddamento e i parametri di processo, i produttori di parti in plastica ottengono nel tempo una produzione più elevata, una migliore conformità e una riduzione dei costi dei pezzi. I progressi nel campo dell'apprendimento automatico e dell'intelligenza artificiale rendono i dati del processo di stampaggio a iniezione sempre più utili.
Conclusione
Ci sono sempre opportunità per migliorare la produttività nello stampaggio a iniezione di grandi pezzi, a partire dalla progettazione dei pezzi e dalla selezione delle resine plastiche fino alla robotica di fabbrica e all'analisi. Le aziende con esperienza nello stampaggio scientifico, nella scienza dei materiali, nella simulazione e nell'ottimizzazione delle macchine saranno quelle che eccelleranno.
La fabbrica del futuro sfrutterà ogni sensore di processo, set di dati sui materiali e strumento di modellazione per ottenere sistematicamente miglioramenti incrementali nella qualità dei pezzi, nei tempi di ciclo, nei tassi di rendimento e nella produttività. I grandi produttori di parti in plastica che abbracciano la trasformazione digitale e le fabbriche connesse otterranno miglioramenti continui che aumenteranno i risultati finanziari.
Un'efficace riduzione del tempo di ciclo per lo stampaggio di pezzi di grandi dimensioni richiede un approccio a livello di sistema lungo tutta la catena del valore, dalla progettazione del pezzo fino alle operazioni di stampaggio a iniezione. Ma i guadagni sostanziali in termini di costi dei pezzi, produttività e ricavi valgono l'investimento.