Lo stampaggio a iniezione di materie plastiche è un processo produttivo complesso con molte variabili. Per produrre pezzi di alta qualità, è necessario uno stampo preciso in grado di sfornare sempre pezzi omogenei. È qui che entra in gioco l'analisi del flusso.
L'analisi del flusso dello stampo simula il flusso della plastica fusa nello stampo durante il processo di iniezione. Questa analisi predittiva rivela potenziali difetti e opportunità di ottimizzazione.prima tagliare qualsiasi acciaio.
Di conseguenza, è possibile perfezionare la progettazione dello stampo, scegliere la resina ideale, ottimizzare il sistema di canali e bilanciare i tassi di riempimento tra le cavità. In questo modo si ottengono tempi di ciclo più rapidi, tassi di scarto più bassi e un passaggio graduale alla produzione su larga scala. Come professionista produttore di stampaggio a iniezione di plasticaIn questo post tratterò tutto ciò che riguarda l'analisi del flusso per lo stampaggio a iniezione di materie plastiche.
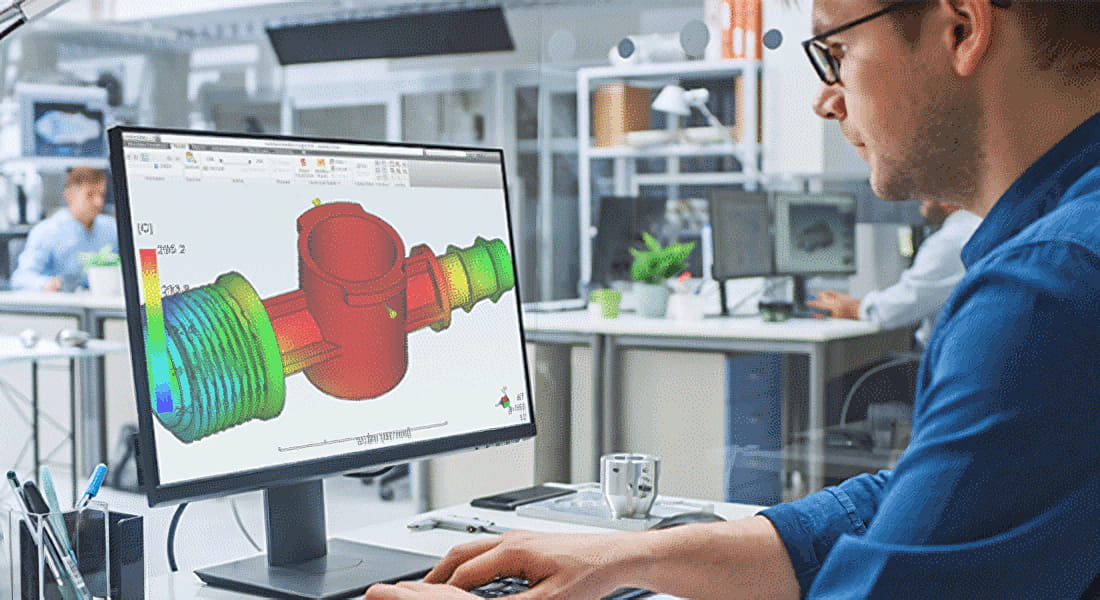
Come funziona l'analisi del flusso di stampo?
Il software di analisi del flusso di stampi importa i vostri CAD e replica digitalmente il processo di stampaggio a iniezione. Solutori FEA specializzati simulano il flusso di resina nello stampo di raffreddamento, mappando variabili come pressione, temperatura, velocità di taglio, orientamento delle fibre e altro ancora nello spazio e nel tempo.
Il software produce visualizzazioni codificate a colori che evidenziano potenziali problemi come linee di saldatura, trappole d'aria, esitazioni e colpi corti. Identificando i problemi in anticipo, gli ingegneri possono modificare il progetto, la selezione dei materiali, i parametri di processo e gli utensili prima di lavorare la piastra.
Ecco una panoramica generale dei vantaggi della simulazione:
Ottimizzare la progettazione dei pezzi
Le simulazioni FEED prevedono con precisione i difetti più comuni, come deformazioni, segni di affondamento e difetti superficiali. Modificando tempestivamente le geometrie problematiche, è possibile ottimizzare il progetto per ottenere prestazioni di stampaggio.
L'analisi controlla anche le variazioni di spessore delle pareti, rileva angoli di sformo troppo aggressivi e convalida i dettagli dell'inserto, come fori filettati, testi e rilievi. Ciò riduce l'usura degli utensili e le operazioni di post-stampaggio.
Selezionare il materiale migliore
Grazie a un database di oltre 6000 materiali, l'analisi aiuta a selezionare la resina e il grado ottimali in base ai requisiti di prestazione e stampabilità. I compromessi tra facilità di scorrimento, ritiro e proprietà meccaniche diventano chiari.
È inoltre possibile ottenere visibilità sull'orientamento delle fibre di vetro per i polimeri rinforzati. L'orientamento influisce direttamente sulla resistenza e può essere regolato con flow leader e modifiche della geometria.
Bilanciamento del riempimento tra le cavità
La simulazione del riempimento mostra l'esatta posizione del fronte di flusso a intervalli di tempo prestabiliti, identificando il momento in cui ogni cavità si riempie. I risultati rivelano esitazioni, linee di saldatura e trappole d'aria da eliminare.
Il bilanciamento dei sistemi di guide e dei layout di controllo garantisce un riempimento simultaneo. In questo modo si evita il sovraimballaggio e si riducono al minimo i requisiti di forza di chiusura.
Ottimizzazione dei canali di raffreddamento
L'analisi fornisce grafici della temperatura durante il ciclo di stampaggio, quantificando l'accumulo di calore superficiale e interno. Gli ingegneri ottimizzano quindi il posizionamento della linea di raffreddamento e il materiale per evitare i punti caldi e limitare i tempi di ciclo.
Convalida delle impostazioni di processo
Infine, l'analisi consente di individuare il tempo di riempimento, la pressione di iniezione, la temperatura di fusione e i profili di imballaggio ottimali. Le funzioni di progettazione automatica degli esperimenti (DOE) semplificano l'ottimizzazione.
I 6 principali vantaggi della simulazione del flusso dello stampo
Al di là di una panoramica generale, ecco sei vantaggi tangibili che derivano dal rendere l'analisi del flusso dello stampo una parte standard del vostro processo di stampaggio a iniezione:
1. Tagliare le iterazioni di produzione
I prototipi fisici comportano costi e tempi significativi. Simulando il processo di stampaggio in digitale, si evitano i cicli di prove ed errori di messa a punto degli stampi.
Questo riduce il tempo totale di sviluppo di settimane o mesi. L'analisi del flusso riduce al minimo i cicli di produzione per ottenere strumenti robusti e ad alto rendimento al primo tentativo.
2. Ridurre i tempi di commercializzazione
La rapidità con cui i prodotti arrivano sul mercato rappresenta un chiaro vantaggio competitivo. L'accelerazione dei tempi di rilascio dipende da un processo di sviluppo efficiente dei componenti in plastica.
L'analisi del flusso dello stampo riduce il ciclo di progettazione → costruzione → collaudo per fornire più rapidamente strumenti affidabili. Eliminando le congetture si evita un ciclo prolungato di costruzione, stampo, test dei pezzi, identificazione dei problemi, ripetizione. Questo effetto a cascata consente di ridurre drasticamente i tempi di commercializzazione.
3. Costi di produzione inferiori
Scarti e rilavorazioni uccidono i margini di profitto. La messa a punto di strumenti e processi per ridurre i difetti consente di ottenere importanti risparmi sui costi per pezzo, che si moltiplicano con la produzione in serie.
L'analisi del flusso previene molti difetti comuni e costosi dello stampaggio a iniezione, come i colpi corti, il flash, i segni di affondamento e la deformazione. Questo porta a una maggiore capacità di processo e a una riduzione dei costi di produzione.
4. Garantire rendimenti elevati
Uno stampo a iniezione che non riesce a riempirsi in modo costante causa gravi problemi. Se solo una parte delle cavità si riempie a ogni ciclo, si sprecano materiale, energia e tempo per spurgare i pezzi difettosi.
L'analisi preventiva uniforma i tassi di riempimento in tutto l'utensile, garantendo cavità piene e massimizzando la resa produttiva.
5. Ottenere informazioni sulla progettazione
La simulazione digitale offre una visibilità unica del processo di stampaggio, impossibile da ottenere con la sola sperimentazione. Osservare i fronti di flusso che riempiono le cavità, seguire le variazioni di temperatura del materiale e visualizzare l'orientamento delle fibre offre preziose indicazioni di progettazione.
Gli ingegneri utilizzano queste informazioni avanzate per ottimizzare la stesura, il gating, i layout e le prestazioni dei materiali.
6. Valutare i compromessi della progettazione
Ogni decisione progettuale comporta dei compromessi. Cambiare la resina, modificare lo spessore delle pareti o la geometria comporta molteplici ripercussioni sulle prestazioni.
La simulazione fornisce i dati per valutare i compromessi associati quando si modifica il progetto dello stampo, le condizioni di lavorazione o la selezione del materiale.
Quando è necessario eseguire l'analisi del flusso di muffa?
Sebbene sia possibile stampare a iniezione i pezzi senza un'analisi preliminare, si consiglia di integrare la simulazione nelle prime fasi del processo di sviluppo:
- Stampi a più cavità
- Geometrie complesse
- Specifiche di tolleranza strette
- Utilizzo di nuove resine
In pratica, si vuole simulare qualsiasi progetto con costi elevati o incertezza. Identificare in anticipo i potenziali difetti utilizzando l'analisi del flusso dello stampo riduce il rischio e fa risparmiare tempo e denaro.
Da asporto
L'analisi del flusso dello stampo offre una visibilità unica sul processo di stampaggio a iniezione. La simulazione avanzata prevede con precisione il modo in cui la resina fluisce negli stampi complessi, scoprendo precocemente i difetti e presentando opportunità di ottimizzazione.
Questo porta a una riduzione degli scarti, a una diminuzione dei requisiti di serraggio, a un riempimento bilanciato, a una progettazione robusta degli utensili e, in ultima analisi, a un time-to-market più rapido. Invece di tagliare l'acciaio e sperare nel meglio, la simulazione fornisce i dati per progettare la qualità.
Integrando l'analisi in anticipo e convalidando la producibilità dei pezzi in modo digitale, si snellisce lo sviluppo, si riducono i costi e si accelera il rilascio di prodotti robusti stampati a iniezione.