La risoluzione dei problemi nel processo di stampaggio a iniezione è un'abilità fondamentale per chiunque lavori nella produzione di plastica. Essendo un metodo di produzione intricato e caratterizzato da molte variabili, inevitabilmente si verificano problemi che richiedono una rapida identificazione e la risoluzione di problemi per evitare costosi tempi di inattività. In questa guida completa, come professionista produttore di stampaggio a iniezioneIn questa sede verranno illustrate metodologie collaudate di risoluzione dei problemi per risolvere in modo efficiente i difetti e stabilizzare i processi.
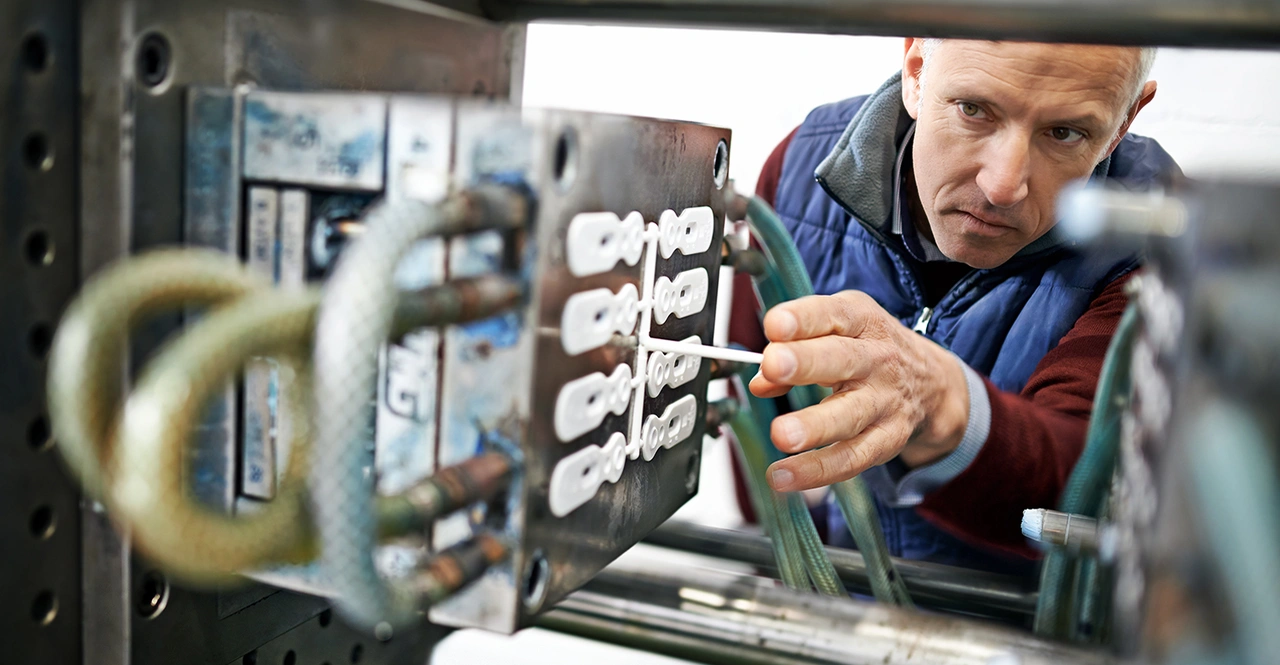
Introduzione
Il Risoluzione dei problemi per il processo di stampaggio a iniezione comporta misure sia reattive che proattive. Gli sforzi reattivi consistono nell'affrontare i difetti nel momento in cui si verificano, attraverso l'analisi sistematica delle cause e la correzione. Gli sforzi proattivi ottimizzano i processi per la stabilità attraverso una solida configurazione delle macchine, il controllo dei processi e gli studi di capacità.
La padronanza dei principi di risoluzione dei problemi è essenziale per gli stampatori a iniezione che cercano l'eccellenza operativa. Individuando tempestivamente i problemi e identificando rapidamente le soluzioni, le aziende di trasformazione possono ottenere una maggiore produttività, una riduzione degli scarti/lavorazioni, un miglioramento della qualità e una riduzione dei costi.
Un approccio strutturato alla risoluzione dei problemi di stampaggio a iniezione
Una risoluzione efficace dei problemi richiede una struttura che consenta di esaminare metodicamente i potenziali problemi. Le fasi includono di solito:
Ispezione accurata
Controllare attentamente che il pezzo non presenti difetti e misurare le dimensioni critiche. Le foto aiutano l'analisi. Pulire lo stampo e assicurarsi che i componenti mobili funzionino correttamente.
Comprendere le condizioni di base
Confrontare i setpoint di processo con linea di base parametri di un processo convalidato. Esaminare le liste di controllo per la preparazione di macchine, materiali e stampi.
Analizzare le cause principali
Valutare i possibili fattori di processo, materiale, stampo e macchina in base al modello di difetto. Analizzare le tendenze utilizzando i dati di processo.
Implementare le soluzioni
Le azioni correttive devono affrontare direttamente le cause principali, a partire dalla regolazione delle condizioni di processo. Le modifiche all'hardware vengono effettuate solo se necessarie.
Confermare i risultati
Eseguire test per confermare la completa risoluzione del problema. Aggiornare la documentazione del processo e condividere i risultati tra i team per evitare che si ripetano.
Esaminiamo ora alcuni dei difetti più comuni nello stampaggio a iniezione e i consigli pratici per affrontarli in modo efficiente.
Difetti comuni dello stampaggio a iniezione e soluzioni
Curvatura
Per deformazione si intende la distorsione o la torsione del pezzo stampato dopo l'espulsione. Si verifica a causa di un ritiro non uniforme, in genere dovuto a spessori di parete non uniformi o a variazioni di raffreddamento. La deformazione è comune nei pezzi piatti e di grandi dimensioni con nervature minime per la rigidità strutturale.
Cause
- Raffreddamento non uniforme da sezioni spesse e sottili
- Orientamento da alte velocità di iniezione
- Tensioni residue di stampaggio
- Espulsione prima della corretta solidificazione
Soluzioni
- Ottimizzare i circuiti di raffreddamento per un raffreddamento uniforme
- Ridurre la velocità di iniezione e confezionare a pressioni inferiori
- Aumentare la temperatura dello stampo per ridurre le variazioni di viscosità
- Ritardare l'espulsione fino a quando la temperatura della plastica non si abbassa sufficientemente.
Segni di lavandino
I segni di affondamento sono piccole depressioni lucide nello stampo dovute a un'insufficiente pressione di imballaggio. Compaiono spesso quando lo spessore delle pareti cambia bruscamente. Di natura estetica, gli avvallamenti possono essere ammaccature poco profonde o crateri profondi, a seconda dello spessore del pezzo.
Cause
- Basse pressioni di iniezione o di impaccamento
- Blocco anticipato del cancello
- Alta temperatura dello stampo
- Tempo di raffreddamento insufficiente
Soluzioni
- Aumentare la pressione dell'impacco, il tempo e la velocità di iniezione della massa fusa.
- Aumentare la dimensione dei colpi e ridurre l'ammortizzazione
- Spostare il cancello in aree più spesse
- Temperature di fusione e di stampo più basse
Scatti brevi
I colpi corti si riferiscono a un riempimento incompleto dello stampo con conseguenti sezioni mancanti, di solito le più lontane dalla porta. I pezzi presentano linee frontali di flusso visibili dove la plastica ha smesso di muoversi. Le riprese brevi sono dovute a un volume di materiale, a una temperatura o a una pressione insufficienti per riempire completamente lo stampo.
Cause
- Basse velocità o pressioni di iniezione
- Congelamento precoce del cancello
- Eccessiva viscosità
- L'umidità inibisce il flusso
- Bocchette tappate che intrappolano i gas
Soluzioni
- Aumento della dimensione dei pallini, della velocità di iniezione e della temperatura di fusione
- Aumentare la pressione del pacco/tenere la pressione, tempo
- Garantire una profondità di sfiato adeguata
- Asciugare il materiale secondo le specifiche
Flash
Il flashing consiste in sottili strati di plastica con sporgenze simili a pinne lungo le linee di divisione dello stampo, i perni di espulsione, le guide o gli inserti. L'infiammabilità si verifica quando la forza di serraggio non è sufficiente a resistere alle pressioni di iniezione, consentendo alle facce dello stampo di separarsi leggermente.
Cause
- Pressione o velocità di iniezione elevate
- Forza di serraggio dello stampo insufficiente
- Profondità di sfiato non corretta
- Cattivo allineamento delle piastre dello stampo
Soluzioni
- Riduzione della pressione di iniezione e aumento del tempo
- Aumentare il tonnellaggio della pinza o la pressione di alimentazione
- Regolare la profondità della terra del flash
- Migliorare l'allineamento e la lavorazione degli stampi
Segni di bruciatura
Le bruciature si riferiscono a macchie e striature scurite o scolorite su un pezzo stampato, di solito in prossimità di porte, prese d'aria o guide. Le bruciature sono dovute al surriscaldamento di queste aree a flusso limitato, a causa del taglio eccessivo o della mancanza di raffreddamento.
Cause
- Elevata velocità di iniezione che aumenta il calore di taglio
- Cattiva progettazione di cancelli, guide e terreni
- Mancanza di raffreddamento vicino ai cancelli
- Problemi di compatibilità dei materiali
Soluzioni
- Ridurre le velocità e le pressioni di iniezione
- Aggiornamento di cancelli, guide e ugelli
- Aggiungere canali di raffreddamento vicino al gate
- Garantire un'adeguata essiccazione del materiale
Jetting
Il jetting si riferisce alle linee di flusso o alle striature ad alta lucentezza causate dall'effetto fontana della massa fusa. Si verifica quando la massa fusa non impatta sulle pareti della cavità e crea un flusso turbolento e impetuoso. Il jetting è dovuto a velocità di iniezione elevate senza una sufficiente contropressione.
Cause
- Alta velocità di iniezione
- Bassa contropressione
- Diametro ridotto della porta
- Assenza di impingement
Soluzioni
- Ridurre la velocità di iniezione
- Aumentare la contropressione per ottenere un flusso laminare
- Dimensioni del cancello aperto per un ingresso agevole
- Impattare la fusione su costole spesse/bossoli
Vuoti
I vuoti sono piccole sacche d'aria che compaiono all'interno dei pezzi, di solito nelle aree più spesse. Si formano a causa dei gas disciolti nella fusione sottoposta a calore/pressione, che escono dalla soluzione quando la pressione si abbassa improvvisamente. I gas vengono quindi intrappolati all'interno del corpo del pezzo.
Cause
- Degassamento di umidità
- Congelamento precoce del cancello
- Bassa pressione di riempimento
- Scarsa progettazione dello sfiato
Soluzioni
- Asciugare il materiale secondo le linee guida
- Aumentare la pressione del pacco, cancelli
- Spostamento dei cancelli nelle sezioni più pesanti
- Aggiungere bocchette di ventilazione di dimensioni adeguate
Linee di flusso
Le linee di flusso si riferiscono alle linee di saldatura visibili lungo i confini del fronte di flusso derivanti dal flusso della fontana. Si presentano come increspature o rugosità superficiali in linea con il flusso di fusione, accentuate dagli additivi orientanti. Le linee di flusso indicano l'impaccamento prima del congelamento delle porte.
Cause
- Basse temperature di fusione
- Velocità di riempimento lenta che consente la formazione di pelli
- Raffreddamento non uniforme
- Forme geometriche che causano la divisione del flusso
Soluzioni
- Aumentare le temperature di fusione e stampo
- Aumentare i tassi di riempimento dell'iniezione
- Equalizzare gli spessori delle pareti delle sezioni
- Angoli interni arrotondati
Difetti di superficie
I difetti di superficie riguardano le texture stampate che causano un'estetica scadente invece di un'elevata lucentezza progettata. Sono dovuti a riempimenti, umidità o altri contaminanti che alterano la finitura della superficie. I tipi di difetti variano da buche, striature e fossette a texture di pelle ruvida.
Cause
- CarryoverContaminazione incrociata
- Scarsa lucidatura dello stampoImmunità nei materialiBlush della portaRegolamenti con contaminanti
Soluzioni
- Sequenza di produzione
- Pulizia dalla muffa
- Le asciugatrici funzionano correttamente
- Sfiato
- Cicli più brevi
- Macinazione pulita
Striature di colore
Le striature di colore consistono in una distribuzione non uniforme del colore nella parte stampata, che appare come strisce chiare/scure. Il risultato è una scarsa dispersione dei coloranti nella resina o una fusione non omogenea. Il taglio o le temperature elevate degradano gli additivi.
Cause
- Miscelazione inadeguata
- Intasamento parziale dei canali caldi
- Tempo di residenza della resina eccessivo
- Elevato numero di giri della vite, velocità di iniezione
Soluzioni
- Aumentare la contropressione e il numero di giri della vite
- Pulire completamente i canali caldi
- Riduzione dei cicli e dei tempi di permanenza
- Velocità di iniezione più basse
Segni di strombatura
I segni di strombatura si riferiscono a striature argentate che si irradiano in modo irregolare dai fronti di flusso causati da una piccola separazione degli strati di fusione. All'esame ingrandito assomigliano a crepe. Le striature sono dovute a contaminazione, umidità o decomposizione nelle zone di taglio.
Cause
- Surriscaldamento e degrado dei materiali
- L'umidità intrappolata si spegne in un lampo
- Contaminazione da regrind
- Riscaldamento eccessivo del taglio
Soluzioni
- Temperature della canna più basse
- Asciugare correttamente i materiali
- Eliminare le fonti di contaminazione
- Aumentare la profondità di sfiato
Linee di saldatura
Le linee di saldatura sono linee di giunzione visibili dove si incontrano fronti di fusione separati. Hanno una resistenza inferiore a quella del materiale sfuso. La pressione di mantenimento deve imballare lo stampo prima che le pelli si congelino completamente in una linea di maglia debole.
Cause
- Formazione prematura della pelle
- Basse temperature di fusione
- Raffreddamento non uniforme
- Sfogo improprio
Soluzioni
- Aumentare le temperature di fusione/stampo
- Aumentare i tassi di riempimento dell'iniezione
- Equalizzare gli spessori delle sezioni
- Allargare gli sfiati per i gas intrappolati
Fragilità
La fragilità si riferisce alla perdita di forza d'urto o di duttilità delle parti, causando cricche o fratture sotto sforzo. Riempitivi, rinforzi e pigmenti possono infragilire i materiali. Anche la degradazione termica o meccanica riduce la tenacità.
Cause
- Contaminazione da materiali degradati o da miscele incrociate di resine
- Eccessivi riempimenti che riducono la resistenza agli urti
- Surriscaldamento dovuto a forti sollecitazioni o temperature elevate
- Vuoti interni che innescano la propagazione delle cricche
Soluzioni
- Prevenire la contaminazione incrociata
- Ottimizzare i carichi di riempimento per la resistenza all'impatto
- Temperature di processo più basse
- Aumentare la pressione di riempimento per ridurre al minimo i vuoti
Risoluzione efficace dei problemi di stampaggio a iniezione
Imparare a riconoscere rapidamente i difetti, a valutarne le cause profonde e a individuare le azioni correttive separa gli stampatori a iniezione di livello medio da quelli d'élite. Lo sviluppo del controllo del processo attraverso i principi dello stampaggio scientifico riduce al minimo la risoluzione dei problemi.
Sfruttando un approccio strutturato e questa panoramica dei problemi di stampaggio più comuni, le aziende di trasformazione possono ottenere tempi di attività, rendimenti e capacità elevati. Padroneggiare Risoluzione dei problemi per il processo di stampaggio a iniezione stabilisce la stabilità necessaria per le operazioni snelle.