Threaded parts are extremely common across countless industries, from plumbing fittings to fasteners to plastic bottles. Creating threaded components requires specialized techniques and considerations compared to conventional plastic parts. In this comprehensive guide, as a professional plastic injection molding manufacturer, I’ll walk you through everything you need to know about making threaded plastic parts using injection molding.
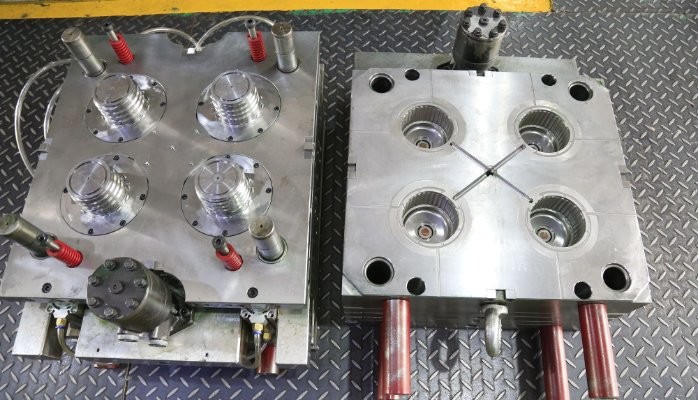
An Overview of Threaded Parts
Threaded parts contain spiral ridges, known as threads, that allow them to fasten together with mating threads. Screws, bolts, nuts, bottle caps, and hose fittings are some examples of threaded parts.
The main benefit of threads is that they form a strong, leak-proof, and reusable connection without requiring welding, brazing, or adhesives. By simply rotating the threaded component, it will assemble tightly into its matching part.
Common Thread Types
There are several standardized thread profiles, including:
- Unified Thread Standard (UNC/UNF): Commonly used for general purposes in the US. Defined by thread angle, pitch, and diameters.
- ISO Metric Thread: The international standard with a 60° thread angle. Specifies thread pitch and diameter.
- NPT/NPS: For tapered or straight threaded pipe connections.
- ACME: Trapezoidal thread for lead screws and other power transmission applications.
The thread type must be compatible with the mating component. So proper selection and specification of threads is critical.
Key Considerations for Injection Molded Threads
Because of their complex geometry, producing threaded features in injection molded plastic requires special mold components and process considerations compared to conventional molding.
Here are some key factors to account for:
1. Mold Components
- Threaded Cores: Hardened steel cores machined with the target thread profile. Inserted into the mold cavity.
- Unscrewing Mechanisms: Automatic or manual means to disengage threaded cores from the molded part.
- Side Cores: Can produce undercut features in threads to prevent splitting.
2. Material Selection
- Materials must have adequate strength, hardness, and ductility to resist thread damage.
- Fillers like glass fiber reduce material flexibility during demolding.
3. Part Design
- Draft angles to facilitate mold release.
- Wall thickness uniformity.
- Minimal core locks.
Getting these parameters right is crucial for producing functional threaded plastic parts via injection molding.
The Threaded Injection Molding Process Step-By-Step
Here are the key phases to make threaded plastic components by injection molding:
Step 1: Mold Design
The mold must be precision-machined to enable details like threads to be accurately reproduced in the molded parts.
Key sub-steps include:
- Designing the mold cavity around the part geometry.
- Fabricating threaded cavity inserts.
- Integrating features for automated or manual core removal.
Any undercuts in the threads may need side-action cams or slides to avoid obstructing ejection.
Step 2: Mold Assembly
Before production, the mold must be assembled and calibrated:
- The threaded core pins and blocks are inserted into the mold halves.
- Cavity alignment is confirmed to minimize flash around the threads.
- Any side-action components are oriented.
- Cooling channels are connected.
Step 3: Injection Molding
Now the complete mold is mounted into a plastic injection molding machine to begin part production.
The basic cycle includes:
- Clamping – The two halves of the mold are pressed together with immense pressure.
- Injection – Super heated molten plastic fills the mold cavity via runners and gates.
- Cooling – After filling the impression completely, cooling channels and mold walls chill the plastic.
- Ejection – Pins eject the solid plastic part from the mold. The threads are formed in the cavity.
- Reset – The mold closes as automated mechanisms retract side cores and eject the threaded cores.
The mold then opens, parts are removed, and the automated cycle repeats continuously.
Fine-tuning molding parameters like melt temperature, injection speed, and cooling time is needed to yield high quality threaded parts.
Step 4: Post-Processing
- Parts are trimmed, finished, and inspected after molding.
- Functional checks assess thread integrity by test fitting with matching threaded hardware.
- Passed parts are packed and shipped. Defective items are discarded or granulated.
With robust mold construction and dialing in process settings appropriately during initial sampling runs, injection molding can reliably produce plastic components with intricate thread details.
Frequently Asked Questions
Can any plastic be molded with threads?
- Technically yes, but each material has different requirements based on its viscosity, shrinkage, flexibility, etc. Amorphous and semi-crystalline plastics like nylon, acetal, polypropylene, ABS are best suited for threaded parts.
How many threads per inch (TPI) can be molded?
- As a rule of thumb plastic threads should use coarser pitches than metal threads. Around 10-20 TPI is typically preferred to avoid premature thread damage in plastics. Ultra fine pitches below 20 TPI require very high precision molding.
What tolerance can be held on injection molded threads?
- With precision tooling and process control, molded threads can achieve fairly tight 3-5% tolerances depending on the plastic used. But in general plastic threads intrinsically have looser tolerances than machined or forged metal threads.
Is ultrasonic welding suitable for assembling threaded plastic parts?
- Ultrasonic welding causes material flow and deformation so it is generally not suitable for securing threaded plastic parts, which rely on precise dimensions for effective function. Joining threaded parts via conventional fastening techniques is recommended instead.
Key Takeaways
- Specialized cores and mold components enable injection molding of plastic threads.
- Material flexibility, draft angles minimize demolding damage.
- Automated unscrewing mechanisms improve quality and lower costs.
- Coarser threads and allowances accommodate greater plastic process variation.
With attention to mold design, tolerance allocation, and material characteristics, intricate plastic threaded components can be manufactured via injection molding economically on an industrial scale.