Plastic injection molding is one of the most versatile and cost-effective manufacturing processes available today. With plastic injection molding, you can produce complex, highly accurate plastic parts on a large scale. However, one of the key steps with this process is selecting the right plastic material for your application.
There are thousands of different plastics on the market, each with its own unique set of properties. Depending on factors like strength, flexibility, heat resistance, chemical resistance, and cost, certain plastics are better suited for certain applications than others.
So what materials can be used in plastic injection molding? In this comprehensive guide, as a professional plastic injection molding manufacturer, I’ll highlight the top 10 most commonly used injection molding plastics, overviewing their key characteristics and ideal applications.
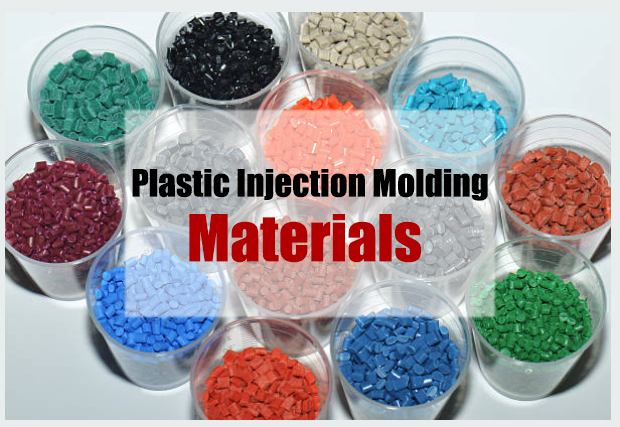
What Is Plastic Injection Molding?
Before jumping into the materials, let’s start with a quick overview of what exactly plastic injection molding is and why material selection is so crucial.
Plastic injection molding is a manufacturing process whereby a plastic polymer is heated until it becomes molten, then injected at high pressure into a mold cavity. The mold is held shut until the plastic cools and hardens into the desired shape.
There are several reasons why injection molding is such a ubiquitous manufacturing method:
- Cost-effectiveness – Producing plastic parts via injection molding is extremely cost-effective, especially for large production runs. The high initial costs of designing and CNC machining the mold tooling are offset by the low per-part cost.
- Material versatility – There are thousands of different thermoplastic and thermoset polymers to choose from, each with unique mechanical, thermal, chemical, and electrical properties. This allows for very application-specific material selection.
- Complex geometries – Multi-part injection molds featuring slides, cores, unscrewing mechanisms, and more enable the production of complex plastic geometries that would be impossible or extremely costly to produce otherwise.
- Efficiency – Once the injection molds are tooled up and the molding processes is optimized, plastic parts can be mass produced extremely rapidly. Single injection molding machines can crank out thousands of plastic parts per day.
- Consistency – Every shot produces an identical plastic part, ensuring complete consistency across entire production runs. No variance part-to-part.
With all that said, arguably the most critical step in any injection molding project is selecting the proper plastic resin. But with thousands of materials available, all with varying properties and characteristics, this can be easier said than done!
Let’s take a look at ten of the most widely used injection molding plastics.
What Materials Can Be Used in Plastic Injection Molding?
Acrylonitrile Butadiene Styrene (ABS)
ABS, or acrylonitrile butadiene styrene, is an amorphous thermoplastic widely used across consumer goods, electronics, automotive applications, and toys (like LEGO bricks!).
Some key characteristics of ABS plastic include:
- High impact strength and toughness
- Rigidity – ranges from soft to hard grades
- Resistance to corrosive chemicals and high temps
- Excellent dimensional stability
- Easy to thermoform and fabricate
- Available in various aesthetic finishes
Despite its stellar mechanical properties and versatility, ABS does have some downsides to consider:
- Susceptible to stress cracking
- Vulnerable to UV radiation
- Flammable
- Poor weathering characteristics
All things considered, ABS injection molding is ideal for:
- Consumer electronics
- Automotive parts
- Appliance housing
- Protective equipment
- Toys
Polypropylene (PP)
Polypropylene (PP), also referred to as “polypropene”, is a thermoplastic polymer used across a wide range of injection molding applications, especially food packaging.
molding polypropylene properties include:
- High melting point
- Chemical and moisture resistance
- Extremely versatile
- Low density
- Excellent fatigue resistance
- Recyclable
Despite being somewhat difficult to paint or bond, polypropylene has superior mechanical properties, is resistant to warping, and is both food contact-safe and recyclable, making it a common choice for injection molding household products and various containers.
Common applications of polypropylene injection molding include:
- Food containers
- Appliances
- Automotive parts
- Hinges, packaging
- Piping, plumbing
- Polypropylene rope
Nylon (Polyamide)
Nylon encompasses a family of synthetic polymers that are commonly injection molded into products that call for high strength, wear resistance, and temperature resistance.
Some noteworthy properties of nylon injection molding resins include:
- High tensile strength
- Chemically resistant
- Low coefficient of friction
- Heat resistant – good high temp properties
- Highly versatile – alloys well
- Good abrasion and wear resistance
- Available in various grades (nylon 6, nylon 66, etc)
Despite its stellar mechanical properties, nylons do absorb moisture and oils, making them less suitable for certain applications. Types of products made from injection molded nylon include:
- Bearings/gears
- Fasteners
- Automotive parts
- Industrial parts
- Food packaging
- Appliances
Acetal (POM)
Also referred to as polyoxymethylene (POM), acetal plastic is known for its high rigidity, strength, and thermal stability in comparison to other injection molding thermoplastics.
Key characteristics of acetal resin include:
- Extremely strong and rigid
- Low coefficient of friction – slick surface
- Excellent thermal stability and chemical resistance
- Withstands repeated impacts
On the downside, acetal plastic is relatively expensive compared to commodity resins. Applications well-suited to acetal injection molding:
- Precision gears
- Pulleys
- Automotive interior parts
- Plumbing fixtures
- Door latches
- Ball bearings
- Appliance components
Polycarbonate (PC)
Polycarbonate (PC) injection molding resin is an optically clear amorphous thermoplastic that exhibits exceptional impact strength and dimensional stability across a wide temp range.
advantages polycarbonate injection molding:
- Highly impact resistant
- Optical clarity – glasslike transparency
- Heat resistance
- Dimensional stability
- Flame retardant grades available
Despite being prone to stress cracking and somewhat notch sensitive, polycarbonate is the go-to option for injection molding transparent or minimally colored parts across safety equipment, electronics, and other applications requiring high impact strength.
Typical applications include:
- Eyeglasses
- Safety face shields
- Police riot shields
- Automotive lenses
- Electronic displays/screens
Polyethylene (PE)
The polyethylenes make up one of the most widely injection molded plastic families on the planet. From bottles and jugs to toys and bags, polyethylene has become ubiquitous, and for good reason.
Polyethylenes can be broken down into several classifications, but some overarching characteristics include:
- Chemical and moisture resistance
- Food contact safe
- Excellent impact strength
- Low coefficient of friction
- Recyclable
With outstanding chemical resistance, low cost, high availability, and recyclability, it comes as no surprise that polyethylene ranks at the very top in terms of global plastic resin demand. Some examples of injection molded polyethylene products:
- Milk jugs
- Shampoo/soap bottles
- Wire and cable insulation
- Toys
- Disposable cups
- Folding chairs
- Buckets
If you’re unsure which specific grade of polyethylene best fits your application, it helps to consult with your injection molder early on in the design process.
Acrylic (PMMA)
Acrylic plastic injection molding compounds, also referred to as polymethyl methacrylate (PMMA), acrylic glass, or plexiglass, provide excellent optical clarity and weatherability.
acrylic injection molding pros:
- Optical clarity – glasslike transparency
- UV and weathering resistant
- Rigid – brittle depending on grade
- Lightweight
- LowScatter loss
On the downside, acrylics demonstrate poor resistance to abrasion and chemicals. Despite its shortcomings in certain chemical or mechanical applications, acrylic injection molding is ubiquitous across:
- Signs
- Display cases
- Aquariums
- Vehicle lighting lenses
- Medical equipment
- Bathroom ware
Polystyrene (PS)
Polystyrene falls into a class of plastics known as vinyl polymers – the sixth most abundant plastic resin globally. It possesses many desirable characteristics:
- Optically clear grades available
- Excellent dimensional stability
- Electric insulation properties
- Low moisture absorption
- Economical
- Recyclable
Unfortunately polystyrene is inherently brittle with low impact and puncture resistance. This rules it out for more demanding applications. But polystyrene injection molding offers an affordable solution across numerous consumer products:
- Disposable utensils
- Protective packaging
- Egg cartons
- CD cases
- Rulers
- Petri dishes
If high impact strength is required, manufacturers typically opt for high impact polystyrene (HIPS) compounds which contain polybutadiene rubber to increase ductility.
Thermoplastic Elastomers (TPE)
Thermoplastic elastomers (TPE) make up a unique class of copolymers that consist of materials exhibiting both thermoplastic and elastomeric properties.
characteristics thermoplastic elastomer injection molding:
- Elasticity and resilience of rubber
- Processability of thermoplastics
- Customizable hardness – shore A 10 to shore D 60
- Abrasion/chemical/corrosion resistance
- Ability to stretch repetitively
Because TPEs cost considerably more than other commodity resins, they’re typically only used when their specific performance characteristics are required.
Some examples include:
- Automotive HVAC seals
- Sports safety goggles
- Electrical wire insulation
- Medical tubing/equipment
- Footwear
- Consumer goods
- Weather stripping
Liquid Crystal Polymer (LCP)
Liquid crystal polymers (LCPs), while not nearly as ubiquitous as other major injection molding resins covered here, offer an unmatched combination of heat resistance, strength, and stiffness coupled with excellent chemical resistance.
Why consider LCP injection molding?
- Extreme heat resistance – functional to 260°C
- Chemically inert – excellent chemical resistance
- Incredibly stiff and strong
- Low flammability/smoke
- Dimensionally stable
- Naturally lubricious
The downsides? LCPs are one of the most expensive injection molding plastics per pound globally. Plus, being an exceptionally rigid material, designs call for very gradual transitions in wall thickness to prevent cracking.
But for components requiring the ultimate performance under extreme conditions, LCPs frequently fit the bill for:
- Aerospace electronics
- Semiconductor manufacturing equipment
- Precision automotive components
- Medical devices
What Material Is Best For Your Application?
With so many plastic injection molding materials available, it can be daunting to settle on one resin for your application.
To wrap things up, here’s a quick 3-step process to aid your material selection for injection molding:
1. Define mechanical/thermal/chemical requirements – What strength, temperature resistance, rigidity, ductility, etc does your plastic component require during function? What chemical exposures will it endure?
2. Research suitable resins – Once your performance requirements are fully defined, you can narrow the playing field substantially in terms of applicable injection molding materials.
3. Select 2-3 candidate plastics – With your list of candidate resins whittled down, you can now directly compare pros/cons side-by-side. Reach out to your injection molder for final input/approval before committing to one!
Of course, this simplified approach just skims the surface in terms of injection molding material selection best practices. But I hope it at least provides some guidance on the where to start!
Each application calls for a very unique set of material properties. Collaborating closely with your injection molder throughout the early design process helps ensure you settle on plastic resin that’s perfectly tailored to your product and end-use environment!