Packing pressure is a critical yet often misunderstood parameter in the injection molding process. As a professional plastic injection molding manufacturer, I’m here to demystify packing pressure, why it matters, and how to optimize it for high-quality parts. Stick with me!
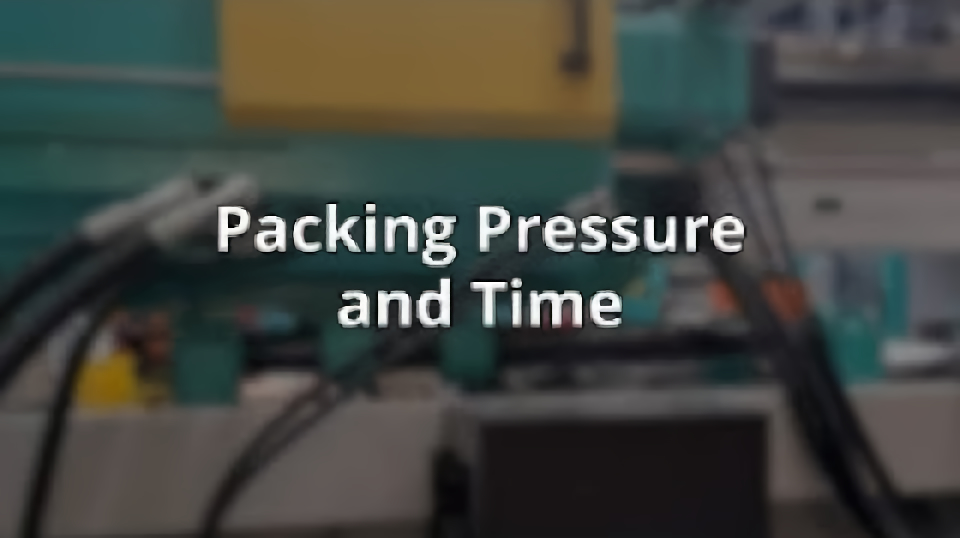
What is Packing Pressure in Injection Molding?
In short, packing pressure is the pressure applied to the molten plastic after the mold cavity has been filled to its target volume, usually 95-98%. Its purpose is to “pack” more material into the mold to account for shrinkage as the part cools.
The packing pressure phase typically lasts 5-15 seconds depending on the size and geometry of the part and the material being used. This allows time for the material to cool and solidify before the part is ejected.
Proper packing is crucial for producing uniform, dimensionally stable injection molded parts with a nice cosmetic finish free of sinks, voids, and other defects. It aligns the polymer molecules to maximize density too.
Now let’s break down the phases:
Injection Phase
This is when the reciprocating screw shoots forward, injecting molten resin into the mold cavity at high velocity. The goal is to quickly fill around 95% of the mold.
Too high injection pressure can cause jetting, excessive shear heating, and flashing. We want enough pressure to fill the majority of the cavity before the material starts to solidify at the flow front.
Packing Phase
Once the cavity is 95-98% full, the machine switches from velocity control to pressure control.
The packing pressure is substantially lower than the injection pressure. We want to limit shear heating while gently flowing additional material into the mold to account for shrinkage.
Holding Phase
After the packing phase, the pressure is held constant allowing any trapped gases to vent while the gate solidifies. This bridges the gap between the packing and cooling phases.
Proper packing pressure minimizes sinks, warpage, and molecular orientation while creating a dense, cosmetically appealing part.
Now let’s move onto why optimizing packing is so vital in the first place!
Why is Packing Pressure So Important?
In one word: Quality.
As polymers solidify in the mold, they experience volumetric shrinkage up to 15% for semi-crystalline resins like polypropylene.
We need to pack additional material into the mold to compensate for this shrinkage. Without sufficient packing, we end up with defects like sinks, voids, and excessive warpage.
The material also needs time to vent gases that could cause visual defects. Ever see those pesky bubbles on the surface of your part? Entrapped gases are usually the culprit.
Lastly, packing aligns the polymer molecules to minimize residual stresses and molecular orientation. This maximizes density, rigidity, and cosmetics.
Ideally, parts pop out of the press looking like they came right off the showroom floor!
How Much Packing Pressure Do You Need?
As the resident SEO nerd and not a plastics engineer, I can’t give an exact number here. Too many variables are at play between material selection, part geometry, and processing conditions.
However, a general guideline is to apply a packing pressure approximately 20-50% of your injection pressure. semicrystalline resins usually require more packing pressure than amorphous resins.
You should start on the lower end around 20% then increase gradually as needed to eliminate visual defects.
It’s also crucial your injection pressure is stable first. Tweaking the pack won’t fix an unstable process!
Consult your material supplier for specific recommendations based on the resin you are running. Their technical documents have a wealth of information.
Oh, one more quick tip!
To determine if your packing pressure is in the ballpark, listen for when the screw motor kicks into high gear at the end of velocity control. If you hear it instantly on transfer to pressure control, packing pressure is likely too high. We want a subtle transition to avoid overpacking.
Let your friendly ears be your guide!
Optimizing the Packing Profile
Simply setting the packing pressure isn’t always enough for a robust process. We need to optimize the pressure ramp up and transitions for a stable curve.
This specialized waveform is called the “packing profile”.
It consists of:
Packing Pressure
As I mentioned earlier, a typical starting point is 20-50% of injection pressure depending on material.
For example, if my injection pressure is 10,000 PSI, I’ll start with 2,000-5,000 PSI packing pressure.
Packing Time
Longer flow lengths need more time to properly pack material at the end of flow. Aim for 5-15 seconds of packing time depending on part size.
Pressure Intensification
Some molds pack best when we intensify pressure during packing. This can help force material into difficult areas prone to sinks.
Try increasing packing pressure 10-20% midway through packing. Listen for screw recovery sounds.
Decompression
The pressure release at the end of pack needs to be gradual, especially for materials like polycarbonate. Try lowering pressure over 3-5 seconds.
This ensures material doesn’t recoil from the mold surfaces as pressure releases.
Wrapping Up Packing Pressure
I hope this shed some light on the often confusing yet critical injection molding process parameter known as “packing pressure”.
The goal is to properly pack the mold applying enough pressure (around 20-50% of injection) for long enough (5-15 secs) to deliver fully packed, void free, dimensionally sound parts.
It compensates for shrinkage as the hot plastic cools while aligning molecules to prevent defects like sinks. Master packing, master molding!
Now get out there, tweak some pressures, and make some awesome parts my friends!