Injection molding is a manufacturing process used to create plastic parts from thermoplastic and thermosetting polymers. When you produce injection molded components, a key design consideration is determining the optimal location of the parting line.
But what exactly is a parting line? And why does its placement matter when designing parts for injection molding? As a professional plastic injection molding manufacturer, I’ll explain everything in this comprehensive guide.
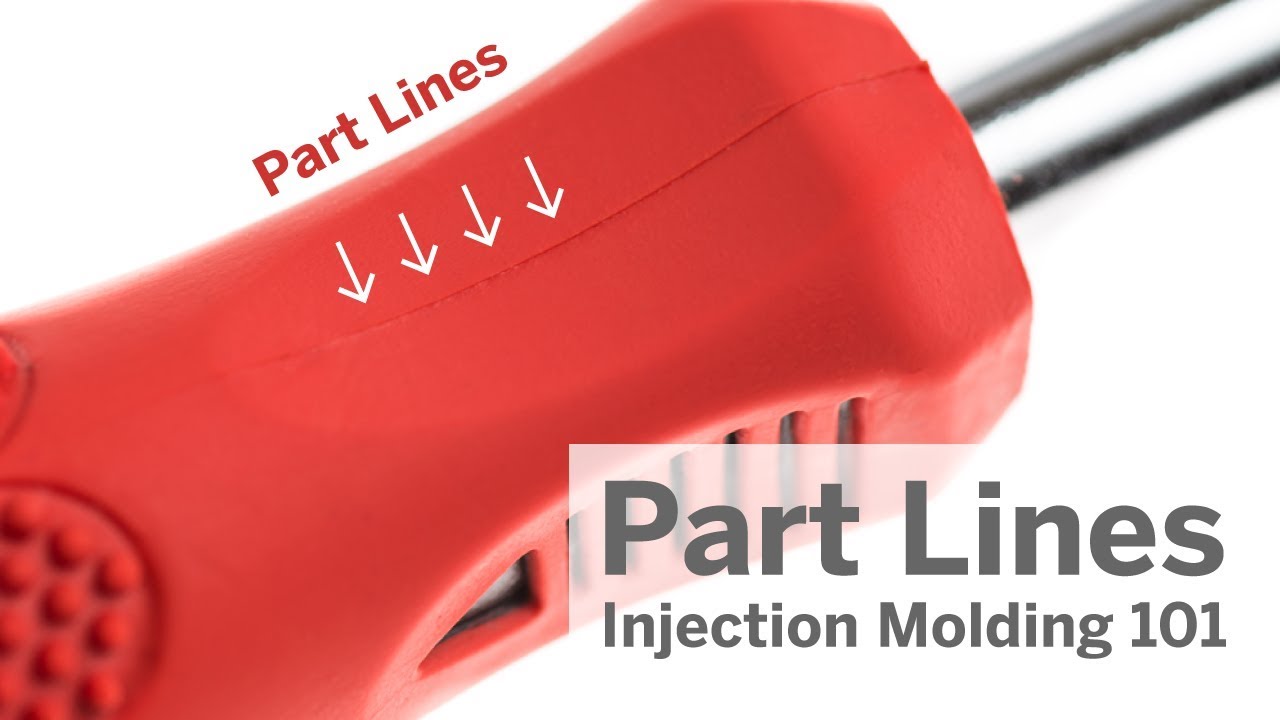
What is a Parting Line in Injection Molding?
A parting line refers to the linear mark left on an injection molded part from the seam where the two halves of the injection mold meet.
Here’s a quick overview of how parting lines form:
- Injection molds consist of two primary components: the cavity and the core.
- The cavity forms the exterior features of the molded part.
- The core forms interior and undercut features.
- Where the edges of the core and cavity meet is called the parting line.
When hot, high-pressure plastic fills the mold cavity, it takes the shape of the mold’s interior walls. Once the molten plastic solidifies, the two mold halves separate along the parting line so the plastic part can be ejected.
This separation inevitably leads to a witness mark or residual seam on the part’s surface. And that’s your parting line.
So in summary:
A parting line refers to the visible seam on an injection molded component’s surface caused by tiny gaps between the two mold halves.
Why Does Parting Line Placement Matter?
The parting line impacts your injection molded component’s appearance, functionality, manufacturability, and cost.
Here’s a closer look at why parting line placement is so crucial in plastic part design.
Aesthetic Concerns
For consumer products, cosmetics are often essential. This means minimizing or camouflaging visible parting lines.
Strategic parting line placement can help make these mold seam marks less conspicuous. For example, you can align parting lines with:
- Sharp corners or edges
- Existing feature lines in the part geometry
- Areas that will get painted or receive pad printing
You can also specify special surface finishes like textures or gloss patterns to help visually disguise parting line locations.
Functional Impact
Beyond just looks, parting lines can potentially interfere with part performance. Poorly placed seam lines might:
- Weaken strength in high stress areas
- Disrupt critical dimensions and tolerances
- Cause flash issues affecting assembly or performance
So when designing your plastic component, carefully consider how the parting line location coincides with functional aspects like fastening points, precision features, sealing surfaces, etc.
Manufacturability Factors
Parting line placement also impacts the complexity and cost of manufacturing your injection molded parts.
The parting line determines the:
- Line of draw – Direction along which mold halves separate
- Draft angles – Degree of slope for vertical surfaces to allow ejection
- Mold Actions – Secondary slides/lifters needed for complex geometries
More intricate parting lines require more complex mold designs and precision machining. This drives up tooling costs.
So to streamline manufacturability, opt for simple, straight parting lines whenever feasible.
Types of Parting Lines
While a centrally located, straight parting line is most common, several variations exist:
Vertical
As the name suggests, vertical parting lines run perpendicular to the direction of mold opening. This is generally the simplest type.
Stepped
Stepped parting lines contain one or more right-angled jogs in the plane of mold separation. Useful for unbalanced injection pressure.
Inclined
Inclined parting lines follow an angled path relative to mold opening. Helpful for complex geometries.
Curved
With curved parting lines, the seam closely traces a contoured or rounded portion of the part surface.
Comprehensive
For intricate components, a comprehensive parting line combines multiple lines along different planes and angles.
The type of parting line impacts factors like injection pressure balance, aesthetics, slides/lifters needed, and effort to polish and maintain sharp mold details over runs.
Parting Line Design Tips and Strategies
Now that you understand the fundamentals, here are some best practices to consider when designing parting lines:
Focus on simplicity – Opt for basic straight or slightly stepped parting lines when possible. Complex lines increase mold costs.
Place intelligently – Position parting lines along areas like sharp corners or edges to make them less visible. Keep off cosmetic faces or sealing surfaces.
Align with ejector layout – Coordinate parting line placement with ejector pin locations needed for clean demolding.
Mind weld lines – Consider fiber orientation and how polymer flow converges along parting lines to minimize weak weld line areas.
Watch wall stock – Wall stock variation from one mold half to another can impact parting line quality and performance.
Consider texturing – Specify special surface finishes to help visually hide parting line locations on cosmetic faces.
Validate with DFM – Get upfront Design for Manufacturability analysis to confirm optimal parting line placement.
Taking the time upfront to carefully plan parting line placement will pay dividends in terms of easier manufacturing, lower molded part costs, and better performing end products.
Conclusion
To quickly recap, the key things product designers should know about parting lines in injection molding are:
- Parting lines form where mold halves meet, causing visible witness marks
- Placement impacts aesthetics, function, manufacturability and costs
- Multiple parting line types exist, with various complexity tradeoffs
- Following best practices for positioning and design is crucial
Armed with this understanding, you’ll be equipped to make informed decisions about parting lines when developing plastic components suitable for injection molding.
Carefully considering this small but vital aspect of your part design can go a long way toward creating a product that both delights customers and streamlines manufacturing.
Now over to you – do you have any other tips or insight into working with parting lines for injection molded parts? I’d love to hear your thoughts and experiences in the comments below!