Formowanie wtryskowe i formowanie tłoczne to dwa najpopularniejsze procesy produkcyjne do pracy z tworzywami sztucznymi i gumą. Ale co dokładnie je wyróżnia? Jako profesjonalista Producent form wtryskowych z tworzyw sztucznychZamierzam omówić kluczowe różnice między formowaniem wtryskowym a tłocznym, abyś mógł określić, który proces może lepiej odpowiadać Twoim potrzebom produkcyjnym.
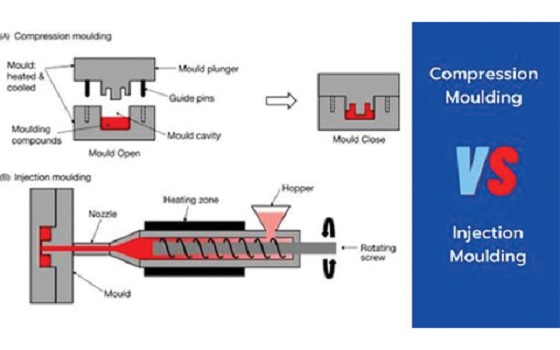
Jak działa formowanie wtryskowe
Formowanie wtryskowe to technika polegająca na podgrzewaniu plastiku aż do jego upłynnienia, a następnie wtłaczaniu go do gniazda formy pod ekstremalnym ciśnieniem. Gdy tworzywo sztuczne ostygnie i zestali się, efektem końcowym jest uformowana część, która przybrała kształt formy.
Rzeczywisty proces formowania wtryskowego działa w następujący sposób:
Najpierw plastikowe granulki są podawane ze zbiornika do podgrzewanego cylindra wtryskarki. Granulki są podgrzewane do punktu, w którym topią się w ciecz, która może być następnie wtryskiwana.
Następnie upłynniony plastik jest wtryskiwany przez dyszę do gniazda formy pod wysokim ciśnieniem - mówimy tu o około 15 000 do 30 000 PSI. Forma pozostaje zaciśnięta przed tym wysokim ciśnieniem, aby zapobiec wyciekom, podczas gdy tworzywo sztuczne przepływa przez wnękę, wypełniając każdą szczelinę.
Gdy tworzywo sztuczne wypełni formę, część ma wystarczająco dużo czasu na schłodzenie i utwardzenie, zanim zostanie ostatecznie wyrzucona z otwartej formy. Efekt końcowy? Idealnie uformowana plastikowa część, która dokładnie pasuje do kształtu formy.
Analiza korzyści płynących z formowania wtryskowego
Istnieje wiele powodów, dla których formowanie wtryskowe stało się tak popularną techniką produkcji. Oto niektóre z największych korzyści, których należy być świadomym:
Niezwykle wysoka prędkość produkcji
W porównaniu z większością innych metod formowania tworzyw sztucznych, formowanie wtryskowe oferuje niesamowicie krótkie czasy cyklu. W wielu przypadkach są to zaledwie sekundy! Ułatwia to produkcję tysięcy, a nawet milionów plastikowych części na bieżąco.
Niższe koszty jednostkowe
Dzięki szybkości formowania wtryskowego w połączeniu z możliwością ponownego użycia form, proces ten umożliwia bardzo niskie koszty jednostkowe przy dużych wolumenach produkcji. Im więcej części produkujesz, tym mniej średnio kosztuje każda pojedyncza część.
Doskonała spójność i precyzja
Formowanie wtryskowe jest cenione za swoją spójność. Cykl po cyklu, proces ten może odtwarzać części z tworzyw sztucznych w niezwykle wąskim zakresie tolerancji dzięki precyzyjnemu charakterowi form stalowych w połączeniu ze zautomatyzowaną produkcją. Ta spójność umożliwia wytwarzanie produktów z wymiennymi zespołami części.
Szeroki zakres opcji tworzyw sztucznych
Formowanie wtryskowe działa zarówno z polimerami termoplastycznymi, jak i termoutwardzalnymi, co zapewnia producentom szeroką gamę opcji materiałowych, takich jak ABS, nylon, polietylen, polistyren, żywica epoksydowa, silikon i inne. Niektóre wypełniacze, takie jak szkło, węgiel i metal, mogą być nawet dodawane w celu zwiększenia wytrzymałości i funkcjonalności.
Możliwości formowania wkładek
Formowanie wtryskowe umożliwia formowanie wtryskowe, zaawansowaną technikę, która pozwala na osadzanie elementów metalowych, plastikowych lub elektronicznych w części z tworzywa sztucznego podczas formowania. Może to skonsolidować etapy po montażu.
Analiza wad formowania wtryskowego
Oczywiście żaden proces produkcyjny nie jest całkowicie doskonały. Formowanie wtryskowe wiąże się również z kilkoma ograniczeniami, takimi jak:
Wysokie koszty początkowe
Same formy wtryskowe są zwykle wykonane ze stali lub aluminium i muszą wytrzymać nacisk zaciskający przekraczający sześć ton. Ta precyzyjna konstrukcja nie jest tania, a formy regularnie kosztują co najmniej $5,000+.
Odpady materiałowe z biegaczy
Kanały, które dostarczają płynne tworzywo sztuczne do gniazda formy, nazywane są prowadnicami. Prowadnice te pozostawiają nadmiar utwardzonego tworzywa sztucznego po każdym cyklu, który jest odrzucany jako złom.
Ograniczenia dotyczące dużych części
Choć formowanie wtryskowe może być użyteczne, napotyka ono ograniczenia w przypadku bardzo dużych komponentów. Wszystko, co waży ponad 50 funtów lub ma metalowe wkładki, zazwyczaj wymaga przejścia na alternatywne procesy, takie jak prasowanie lub termoformowanie.
Czym jest formowanie tłoczne?
Teraz, gdy omówiliśmy już tajniki formowania wtryskowego, porównajmy je z formowaniem tłocznym. Podobnie jak formowanie wtryskowe, formowanie tłoczne wykorzystuje formy do formowania elementów z tworzyw sztucznych lub gumy. Przyjmuje jednak wyraźnie inne podejście:
Po pierwsze, formowanie tłoczne rozpoczyna się od podgrzania surowca z tworzywa sztucznego lub gumy do postaci grubszych, giętkich arkuszy. Operator ręcznie umieszcza te zmiękczone arkusze między dwiema otwartymi połówkami formy.
Następnie połówki formy są zamykane i stosowane jest ciśnienie mechaniczne lub hydrauliczne. To intensywne ciśnienie ściska plastikowe arkusze w zagłębieniach formy, rozprowadzając materiał, aż wypełni każdą szczelinę.
W tym samym czasie do samej formy doprowadzane jest ciepło. Powoduje to dalsze zmiękczenie i utwardzenie tworzywa sztucznego/gumy. Po całkowitym utwardzeniu połówki formy cofają się, a końcowe uformowane części są wyrzucane lub przycinane.
Zasadniczo, zamiast wstrzykiwać upłynniony materiał, jak ma to miejsce w przypadku formowania wtryskowego, formowanie tłoczne rozpoczyna się od prostych arkuszy plastiku/gumy i ściska je do kształtu.
Przegląd zalet formowania tłocznego
Podobnie jak formowanie wtryskowe, formowanie tłoczne ma swój własny zestaw wyraźnych zalet produkcyjnych:
Niższe koszty oprzyrządowania
Formy kompresyjne są zazwyczaj wykonane z tańszych metali, takich jak stopy aluminium lub stali. Zawierają również mniej ruchomych komponentów. To sprawia, że oprzyrządowanie do formowania tłocznego jest w większości przypadków tańsze niż formowanie wtryskowe.
Skalowalność dla większych komponentów
Ręczny charakter formowania tłocznego sprawia, że jest ono znacznie bardziej odpowiednie do formowania bardzo dużych części z tworzyw sztucznych lub gumy w porównaniu do zautomatyzowanych pras wtryskowych. Na przykład producenci z branży lotniczej wykorzystują formowanie tłoczne do produkcji skrzydeł samolotów i innych dużych komponentów.
Elastyczność materiału
Metoda ta działa wyjątkowo dobrze w przypadku elastycznych, giętkich materiałów, które nie płyną łatwo w postaci skroplonej, takich jak guma. Może również obsługiwać polimery termoutwardzalne dzięki niższemu ciśnieniu.
Biorąc pod uwagę słabe strony formowania tłocznego
Podobnie jak w przypadku każdej innej techniki produkcyjnej, formowanie tłoczne wiąże się z kilkoma wadami i ograniczeniami, na które również warto zwrócić uwagę:
Nadmierne odpady materiałowe
Całe zgniatanie podczas formowania tłocznego zmusza materiał do rozlania się poza linię podziału, pozostawiając nadmiar "błysku" plastiku lub gumy, który jest odrzucany, przyczyniając się do wyższych kosztów materiału na część.
Wolniejsze czasy cyklu
W przeciwieństwie do błyskawicznych prędkości formowania wtryskowego, formowanie tłoczne zajmuje minuty, a nie sekundy, aby zakończyć każdy cykl ze względu na dłuższe wymagania dotyczące utwardzania. Ogranicza to możliwości produkcyjne.
Proces pracochłonny
Potencjał automatyzacji w przypadku formowania tłocznego jest znacznie mniejszy niż w przypadku formowania wtryskowego. Etap ręcznego ładowania arkuszy z natury opiera się bardziej na pracy człowieka niż zautomatyzowanych systemów.
Kluczowe różnice między formowaniem wtryskowym a formowaniem tłocznym
Teraz, gdy omówiliśmy podstawy obu technik produkcyjnych, porównajmy bezpośrednio niektóre z najważniejszych kontrastów między formowaniem wtryskowym a formowaniem tłocznym:
Metoda formowania
Metody formowania rdzenia znacznie się różnią - formowanie wtryskowe wtryskuje upłynniony plastik do formy, podczas gdy formowanie tłoczne ściska arkusze plastiku/gumy.
Potencjał automatyzacji
Formowanie wtryskowe może być niemal w pełni zautomatyzowane, zapewniając spójność bez użycia rąk. Kompresja wymaga ręcznego załadunku dla każdego cyklu.
Czas cyklu Prędkość
Formowanie wtryskowe mierzy czas cyklu w sekundach, podczas gdy czas cyklu formowania tłocznego trwa kilka minut.
Spójność i precyzja części
Komponenty formowane wtryskowo oferują większą precyzję wymiarową i spójność w porównaniu z technikami prasowania.
Przydatność materiału
Wtrysk dobrze sprawdza się w przypadku termozmiękczających tworzyw sztucznych; kompresja lepiej radzi sobie z termoutwardzalnymi tworzywami sztucznymi i gumą.
Początkowe koszty formowania
Cena oprzyrządowania jest niższa w przypadku form tłocznych niż wtryskowych.
Zastosowania końcowe
Formowanie wtryskowe nadaje się do małych, skomplikowanych części z tworzyw sztucznych wszystkich typów. Formowanie tłoczne doskonale sprawdza się w przypadku prostszych lub większych elementów gumowych i plastikowych.
Wybór między formowaniem wtryskowym a formowaniem tłocznym
Decyzja o tym, czy formowanie wtryskowe lub tłoczne ma sens dla danego zastosowania, zależy od kilku czynników:
Wielkość produkcji - Formowanie wtryskowe ma sens finansowy tylko w przypadku masowo produkowanych elementów z tworzyw sztucznych ze względu na wyższe koszty formy. Kompresja może być idealnym rozwiązaniem dla mniejszych serii produkcyjnych.
Rozmiar części - Formowanie tłoczne umożliwia tworzenie znacznie większych komponentów w porównaniu do pras wtryskowych o ograniczonych rozmiarach.
Złożoność części - Jeśli wymagane są skomplikowane detale, wąskie tolerancje i elementy dekoracyjne, formowanie wtryskowe może wytwarzać bardzo precyzyjne elementy z tworzyw sztucznych.
Wymagania dotyczące wydajności - Lekkie i wyjątkowo wytrzymałe części z tworzyw sztucznych to specjalność formowania wtryskowego.
Rodzaj materiału - Termoutwardzalne polimery i guma często lepiej nadają się do formowania tłocznego niż techniki wtrysku roztopionej cieczy.
Żadne pojedyncze rozwiązanie nie jest lepsze we wszystkich przypadkach - ostatecznie sprowadza się to do dostosowania mocnych i słabych stron produkcji do idealnego procesu formowania dla Twoich potrzeb. Identyfikacja tych potrzeb wymaga dogłębnego spojrzenia na proponowaną geometrię części, specyfikacje wydajności, ograniczenia budżetowe i oczekiwania produkcyjne.