Polipropylen, powszechnie znany jako PP, to wszechstronny polimer termoplastyczny wykorzystywany w szerokim zakresie zastosowań formowania wtryskowego. Ale czy polipropylen może być formowany wtryskowo? Jako profesjonalista formowanie wtryskowe tworzyw sztucznych Producent, pomogę ci się tego dowiedzieć.
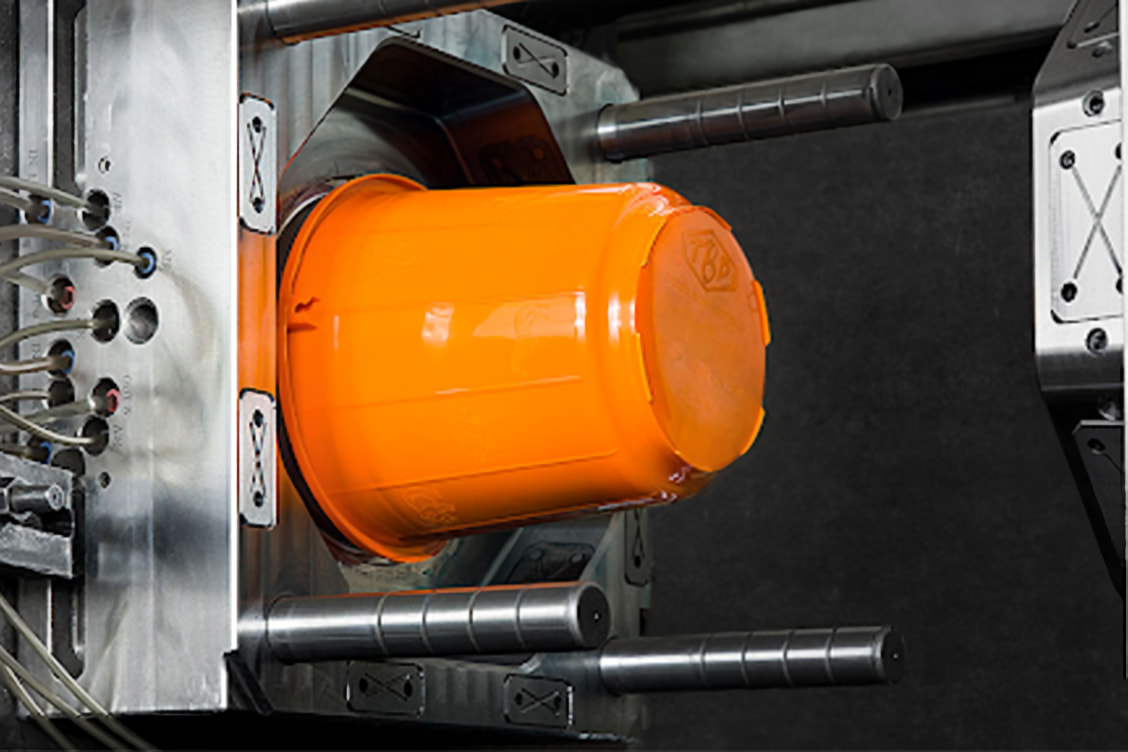
Czy polipropylen może być formowany wtryskowo?
W skrócie: Tak, polipropylen może być formowany wtryskowo. W rzeczywistości formowanie wtryskowe jest jednym z najpopularniejszych procesów produkcji części i produktów z polipropylenu.
Polipropylen ma wiele właściwości, które czynią go idealnym materiałem do formowania wtryskowego, w tym niski koszt, odporność chemiczną, odporność na zmęczenie i niski współczynnik tarcia. Główne branże wykorzystujące polipropylen formowany wtryskowo obejmują motoryzację, medycynę, opakowania żywności, towary konsumpcyjne i inne.
Dlaczego polipropylen jest powszechnie formowany wtryskowo?
Istnieje kilka kluczowych powodów, dla których polipropylen jest tak często wybierany do formowania wtryskowego:
1. Efektywność kosztowa
Po polietylenie, polipropylen jest drugim najczęściej stosowanym tworzywem sztucznym na świecie. Ta duża ilość pozwala utrzymać koszty na niższym poziomie w porównaniu z innymi tworzywami sztucznymi. Polipropylen formowany wtryskowo może produkować bardzo ekonomiczne części na dużą skalę.
2. Właściwości mechaniczne
Właściwości mechaniczne polipropylenu sprawiają, że nadaje się on do formowania wtryskowego pod wysokim ciśnieniem:
- Doskonała wytrzymałość zmęczeniowa i żywotność
- Dobra udarność (dla kopolimeru)
- Wysoka wytrzymałość na rozciąganie
Materiał z łatwością układa się w skomplikowane geometrie form i zachowuje wyraźne cechy po zestaleniu.
3. Szybkość produkcji
Polipropylen ma niską lepkość w porównaniu do innych popularnych tworzyw sztucznych. Pozwala to na szybkie wypełnienie skomplikowanych detali formy, skracając czas cyklu. Szybsze cykle oznaczają wyższą wydajność części i niższe koszty produkcji.
4. Stabilność wymiarowa
Chociaż jego współczynnik kurczliwości jest wyższy niż w przypadku niektórych innych tworzyw sztucznych, polipropylen kurczy się dość równomiernie w kierunku przepływu i przepływu krzyżowego. Ta stabilność wymiarowa zapewnia części o niezawodnej dokładności i tolerancji.
5. Właściwości powierzchni
Śliskie wykończenie powierzchni polipropylenu ułatwia uwalnianie z oprzyrządowania formy po wtrysku. Części łatwo wysuwają się z form bez przywierania lub deformacji.
6. Odporność chemiczna
Polipropylen wykazuje wysoką odporność chemiczną na różne kwasy, zasady i rozpuszczalniki. Pozwala to na szerokie zastosowanie w formowanych wtryskowo pojemnikach i sprzęcie laboratoryjnym narażonym na działanie różnych chemikaliów.
7. Zdolność do recyklingu
Polipropylen jest klasyfikowany jako nadające się do recyklingu tworzywo sztuczne #5. Jego części mogą być wielokrotnie poddawane recyklingowi i ponownemu przetworzeniu. Dzięki temu polipropylen spełnia różne wymogi prawne.
Kluczowe zastosowania polipropylenu formowanego wtryskowo
Formowanie wtryskowe polipropylenu produkuje miliardy plastikowych części każdego roku. Główne branże wykorzystujące ten proces obejmują:
Opakowania na żywność i napoje
Pojemniki na nabiał, butelki na przyprawy, opakowania delikatesowe i inne produkty mające kontakt z żywnością wykorzystują barierę dla wilgoci i odporność chemiczną polipropylenu. Wielowarstwowe technologie barierowe z polipropylenu pomagają wydłużyć okres przydatności do spożycia.
Opieka zdrowotna i medycyna
Sterylizowalny polipropylen nadaje się do formowania wtryskowego części medycznych, takich jak szalki Petriego, pipety, probówki wirówkowe i płytki do testów diagnostycznych. Ten autoklawowalny materiał wytrzymuje wielokrotną sterylizację bez znaczących zmian właściwości.
Towary konsumpcyjne
Niedrogie formowanie wtryskowe polipropylenu tworzy wszelkiego rodzaju tanie plastikowe towary konsumpcyjne, w tym butelki, pojemniki do przechowywania, pojemniki na baterie, obudowy urządzeń, zabawki, artykuły ogrodnicze i wiele innych.
Artykuły gospodarstwa domowego
Narzędzia kuchenne, małe urządzenia, pojemniki do przechowywania i inne artykuły gospodarstwa domowego często zawierają formowane wtryskowo elementy z polipropylenu. Materiał ten charakteryzuje się wysoką temperaturą użytkowania, odpornością na plamy i wytrzymałością na mycie w zmywarce.
Wnętrza samochodowe
Elementy wykończenia wnętrza samochodu prawie zawsze zawierają pewien poziom polipropylenu wypełnionego włóknem szklanym. Materiał o wysokiej sztywności nadaje się do formowania kratek głośników, otworów wentylacyjnych, osłon słupków, oparć siedzeń, części konsoli i klamek drzwi wewnętrznych.
Przykłady te pokazują wszechstronność formowania wtryskowego polipropylenu w wielu głównych branżach.
Przegląd procesu formowania wtryskowego polipropylenu
Podczas gdy zaprojektowany materiał i geometria części wpływają na sukces, przetwarzanie odgrywa równie kluczową rolę. Konsekwentna kontrola procesu formowania pomaga zapewnić solidną, powtarzalną produkcję elementów z polipropylenu.
Oto krótki przegląd podstawowych faz formowania wtryskowego podczas pracy z polipropylenem:
Faza plastyfikacji
- Plastikowe granulki wchodzą do cylindra wtryskowego i są transportowane do przodu
- Temperatura bębna 220-280°C topi granulki w jednorodny płyn
- Mieszanie śrubowe zapewnia odpowiednią temperaturę i konsystencję
Faza wtrysku
- Nagromadzenie stopionego materiału przed ślimakiem osiąga wymaganą objętość
- Ciśnienie wtrysku hydraulicznego wtryskuje PP o niskiej lepkości do formy
- Szybkie tempo napełniania ułatwia pakowanie skomplikowanych części
Faza pakowania
- Dodatkowy materiał przylega do chłodzonych części, aby zapobiec ich kurczeniu się.
- Ciśnienie pakowania wynosi zazwyczaj około połowy ciśnienia wtrysku
Faza chłodzenia
- Kanały chłodzące regulują temperaturę formy w zakresie 40-60°C
- Polipropylen zestala się do ostatecznego uformowanego kształtu
- Wystarczające chłodzenie minimalizuje naprężenia szczątkowe
Faza wyrzutu
- Forma otwiera się i trzpienie wypychacza usuwają część stałą
- Niskie tarcie powierzchniowe umożliwia łatwe uwalnianie
- Szybkie cykle uzupełniane kolejnym strzałem wkrótce potem
Równowaga tych faz umożliwia produkcję dużych ilości formowanych elementów z polipropylenu. Inżynierowie wykorzystują wieloletnią wiedzę na temat przetwarzania, aby podnieść jakość, wydajność i wydajność części.
Zasady projektowania form wtryskowych z polipropylenu
Podczas gdy polipropylen łatwo poddaje się formowaniu wtryskowemu, przestrzeganie najlepszych praktyk projektowych ułatwi przetwarzanie i zmaksymalizuje sukces:
Grubość ścianki
- Docelowa ścianka nominalna między 1,5-3 mm
- Jednolita grubość sprzyja równomiernemu napełnianiu i chłodzeniu
- Obszary o większej grubości mogą wymagać zastosowania liderów przepływu lub indywidualnych bramek.
Promienie i zanurzenie
- Dodaj duże promienie wewnętrzne, aby zminimalizować punkty naprężeń
- Kąty zanurzenia ≥ 1° ułatwiają wysuwanie części
Żebra i kliny
- Żebra pomagają wzmocnić ściany, jednocześnie minimalizując masę
- Wysokość nie powinna przekraczać 50% grubości ścianki
- Kratownice wzmacniają powierzchnie nośne
Żywe zawiasy
- Docelowa grubość około 0,25-0,5 mm
- Wydłużenie ścieżki przepływu, aby zapobiec przedwczesnemu zamarzaniu
Tekstury i funkcje
- Ograniczenie głębokości tekstur dla możliwości formowania
- Umożliwiają prawidłowy ciąg na podniesionych symbolach
Przestrzeganie znormalizowanych praktyk zwiększa wskaźniki sukcesu w zakresie możliwości produkcyjnych za pierwszym razem. Wczesne nawiązanie współpracy z doświadczonymi wtryskarkami w celu sfinalizowania szczegółów technicznych.
Polipropylen a inne tworzywa termoplastyczne
Polipropylen należy do szerszej rodziny termoplastycznych materiałów do formowania wtryskowego. Jak wypada na tle innych popularnych tworzyw sztucznych?
Polipropylen a akrylonitryl-butadien-styren (ABS)
ABS oferuje doskonałą udarność i odporność na ciepło, ale wymaga wyższego ciśnienia formowania. Niewypełniony ABS kosztuje również więcej niż polipropylen. Warto rozważyć ABS w przypadku wysokich wymagań wytrzymałościowych, pomimo wyższych kosztów narzędzi i części.
Polipropylen a polietylen (PE)
Gatunki polietylenu zapewniają doskonałą odporność chemiczną i niskie tarcie, ale brakuje im sztywności w porównaniu z polipropylenem. PE również mniej się kurczy podczas formowania. Polietylen nadaje się do zastosowań wymagających elastyczności i obojętności chemicznej.
Polipropylen a poliwęglan (PC)
Poliwęglan zapewnia wyjątkowo wysoką odporność na uderzenia, nieporównywalną z polipropylenem. Jego przezroczyste odmiany charakteryzują się również wysoką przepuszczalnością światła. Jednak formowany wtryskowo PC kosztuje znacznie więcej niż PP. Poliwęglanu należy używać tylko wtedy, gdy takie właściwości uzasadniają dodatkowe koszty.
Polipropylen a polistyren (PS)
PS ogólnego przeznaczenia wypełnia podobną niszę niskich kosztów jak polipropylen, ale ma znacznie niższą udarność. Wymaga również suszenia przed przetwarzaniem, aby uniknąć rozchodzenia się i defektów powierzchni. Wybierz polipropylen zamiast PS, aby uzyskać lepsze właściwości mechaniczne.
Polipropylen a akryl (PMMA)
Akryl wykazuje doskonałą przejrzystość optyczną i odporność na promieniowanie UV, w przeciwieństwie do standardowego polipropylenu. Jednak formowanie wtryskowe akrylu wymaga wysoce kontrolowanych warunków, aby zapobiec zniekształceniom i przywieraniu. Gdy wydajność optyczna jest najważniejsza, należy użyć PMMA.
Podsumowując, alternatywne tworzywa termoplastyczne przewyższają polipropylen w niektórych aspektach właściwości, ale zazwyczaj wiąże się to ze znacznym wzrostem kosztów. Należy dokładnie określić, gdzie polipropylen nie nadaje się do danego zastosowania, a następnie rozważyć, czy inny materiał uzasadnia skok cenowy. Polipropylen stanowi optymalną równowagę między kosztami, wydajnością i możliwościami dla tysięcy zastosowań formowania wtryskowego.
Wnioski
W tym artykule sprawdziliśmy, dlaczego polipropylen jest tak szeroko stosowanym materiałem do formowania wtryskowego w dziesiątkach branż. Omówiliśmy korzystne właściwości ekonomiczne, materiałowe i przetwórcze, które umożliwiają szerokie zastosowanie formowania wtryskowego polipropylenu. Podsumowano główne zastosowania w opakowaniach żywności, medycynie, towarach konsumpcyjnych, motoryzacji i innych kluczowych rynkach. Przedstawiono również wytyczne dotyczące formowania wtryskowego części z polipropylenu, podkreślając ważne kwestie projektowe.
Porównanie polipropylenu z innymi tworzywami termoplastycznymi ujawniło niszowe sytuacje, w których alternatywne materiały mogą uzasadniać wyższe koszty niż polipropylen, w zależności od wymagań aplikacji. Dzięki szerokiemu zastosowaniu i globalnej infrastrukturze dostaw, należy oczekiwać, że formowane wtryskowo komponenty polipropylenowe będą nadal wiodły prym w branży produkcyjnej w przyszłości.