Formowanie wtryskowe akrylu to proces kształtowania tworzywa akrylowego poprzez wtryskiwanie go do formy. Pozwala to na formowanie akrylu w produkty takie jak soczewki, ekrany i panele. Jako profesjonalista formowanie wtryskowe akrylu Producent przeprowadzi Cię krok po kroku przez cały proces wtrysku akrylu.
The Proces formowania wtryskowego akrylu Rozpoczyna się od zaprojektowania formy do stworzenia pożądanej części. Granulat akrylowy jest następnie suszony, ładowany do wtryskarki i wtryskiwany do formy. Po schłodzeniu i utwardzeniu część akrylowa jest wyrzucana i może przejść przez dodatkowe etapy wykańczania.
Czytaj dalej, a ja omówię każdy etap formowanie wtryskowe akrylu aby pomóc Ci dokładnie zrozumieć, jak to działa.
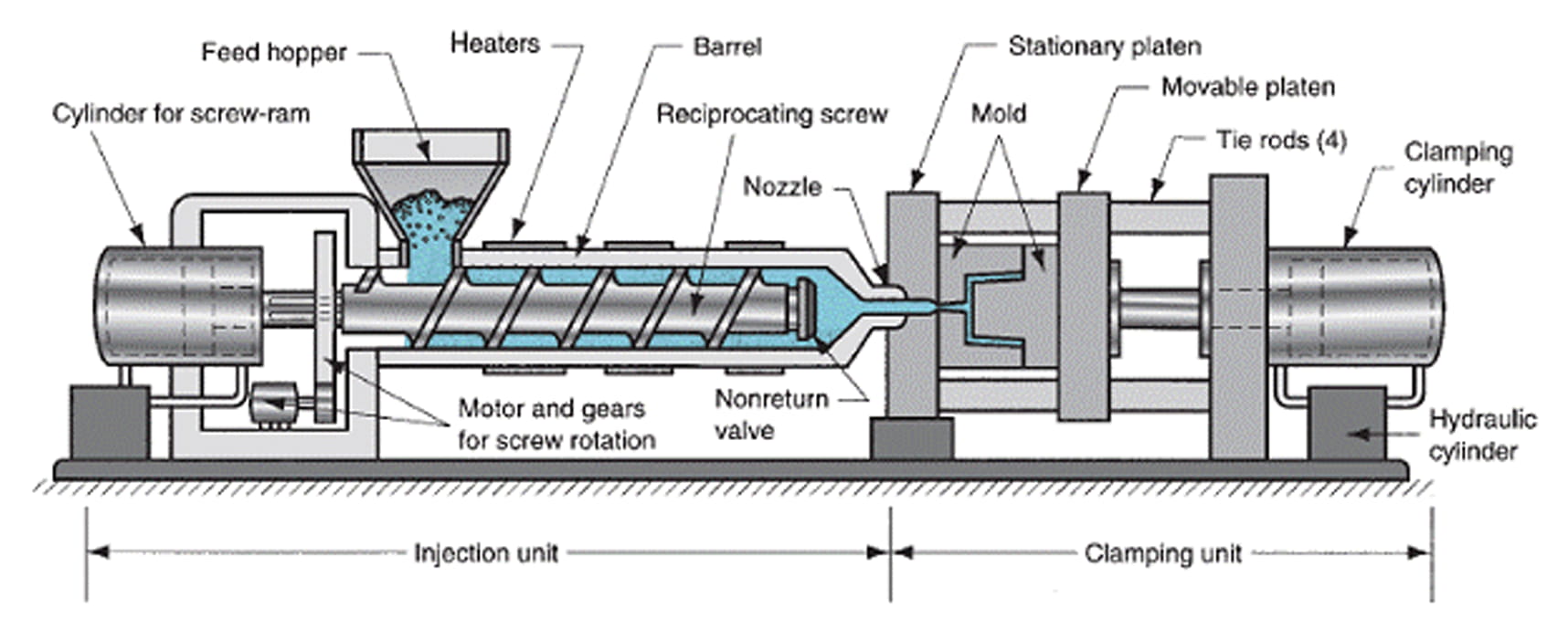
Proces formowania wtryskowego akrylu
Krok 1: Projekt formy
Pierwszym krokiem jest stworzenie formy wtryskowej do formowania części akrylowych. Forma składa się z dwóch połówek - połowy wnęki i połowy rdzenia, które łączą się, tworząc wewnętrzną przestrzeń formy. Akryl przyjmuje ten kształt po wstrzyknięciu.
Projektanci form wykorzystują 3D CAD do precyzyjnego modelowania form wtryskowych. Złożone geometrie i cechy można zaprojektować szczegółowo i przekształcić w kod obróbki dla warsztatu form. Otwory, wkładki, teksturowanie i inne specyfikacje są również uwzględniane na tym wczesnym etapie.
Prawidłowe zaprojektowanie formy ma kluczowe znaczenie. Inteligentne bramy, otwory wentylacyjne, kąty ciągu zapewniają prawidłowy przepływ akrylu i wysokiej jakości efekt końcowy. Doświadczony producent form weźmie te niuanse pod uwagę podczas wytwarzania ostatecznego narzędzia do produkcji form.
Krok 2: Przygotowanie materiału akrylowego
W swojej surowej postaci akryl występuje w postaci półprzezroczystych kulek lub granulek przypominających granulowany cukier. Producenci utrzymują żywicę akrylową w stanie suchym w środowisku o kontrolowanym klimacie, aby utrzymać odpowiednią zawartość wilgoci. Zbyt duża ilość wilgoci powoduje powstawanie pęcherzyków i innych defektów po wstrzyknięciu do formy.
Niektóre żywice akrylowe są higroskopijne. W związku z tym producenci ładują materiał z leja suszącego, który zawiera złoża osuszające. Następnie podgrzewane suszarki ogrzewają akryl powyżej 200°F, aby usunąć resztkową wilgoć przed formowaniem.
Wysuszony akryl spływa do pojemników, gdzie czeka na wtrysk. Niektóre wtryskarki mają nawet wbudowane suszarki żywicy, aby uprościć system dostarczania materiału.
Proces suszenia akrylu
Bardzo ważne jest, aby żywica akrylowa pozostała sucha jak kość przed formowaniem wtryskowym. Jakakolwiek śladowa wilgoć zamienia się w parę, gdy gorący plastik wchodzi do formy.
Nawet najbardziej precyzyjnie wykonane części wykazują małe pęknięcia, pęcherzyki i defekty wizualne, gdy wewnątrz znajduje się wilgoć. No bueno!
Krok 3: Zaciskanie formy
Aby rozpocząć produkcję, operator maszyny zaciska formę wtryskową w prasie. Siłowniki hydrauliczne wywierają tony ciśnienia, aby bezpiecznie zamknąć rdzeń i połówki wnęki. Zapobiega to wyciekaniu stopionego tworzywa sztucznego pod ciśnieniem, gdy jest ono wtryskiwane z dużą prędkością.
Nacisk zacisku musi przezwyciężyć zbiorcze siły próbujące rozepchnąć połówki formy podczas wtrysku. Pręty łączące zwiększają wytrzymałość między płytami.
Krok 4: Wstrzykiwanie akrylu
Gdy forma jest bezpiecznie zaciśnięta, stopiony akryl wypływa z cylindra wtryskowego do wlewu. System prowadnic kieruje gorącą żywicę do każdej szczeliny wnęki narzędzia, aby całkowicie wypełnić pustą przestrzeń.
Prasy ślimakowe podają stałe granulki do cylindra i wykorzystują grzałki elektryczne i energię mechaniczną do upłynnienia tworzywa sztucznego. Wystrzeliwuje on do przodu, gdy ciśnienie wtrysku przekroczy ciśnienie w gnieździe formy.
Pack and Hold
Aby zapobiec przedwczesnemu krzepnięciu, po wypełnieniu wnęki wlewa się więcej żywicy. Powoduje to upakowanie dodatkowego stopionego akrylu i zastosowanie ciśnienia utrzymującego do momentu zamarznięcia bramki.
Części zachowują kształt i ulegają mniejszym odkształceniom dzięki temu dodatkowemu etapowi pakowania. Daje to dodatkowy czas gorącej żywicy na uzyskanie ostatecznego kształtu przed schłodzeniem.
Krok 5: Chłodzenie i utwardzanie
Po zapakowaniu, schłodzona woda krąży przez porty wewnątrz narzędzia, aby zestalić przegrzane tworzywo akrylowe. Złożony układ kanałów jest strategicznie ukierunkowany na gorące punkty w celu przyspieszenia chłodzenia.
Sworznie wypychacza lekko się wysuwają, aby obkurczyć plastik z powierzchni rdzenia. Zapobiega to przywieraniu części, gdy są gotowe do wypchnięcia z formy.
Czas chłodzenia zależy od grubości ścianki. Grubszy plastik zatrzymuje ciepło dłużej niż cieńsze przekroje. Nowsze formy wykorzystują kanały konformalne, aby przyspieszyć chłodzenie i skrócić czas cyklu.
Krok 6: Wyrzucanie części akrylowych
Do ręcznego wysuwania utwardzonego elementu akrylowego:
- Siła zacisku zwalnia się, umożliwiając rozdzielenie połówek formy wtryskowej
- Za pomocą prętów prowadzących płyta wypychacza przesuwa się do przodu, aby wypchnąć części z wnęki narzędzia
- Ramiona robotów lub pracownicy chwytają gotowe elementy poza prasą formierską
W przypadku prostszych kształtów z prostymi formami ciągnącymi najlepiej sprawdzają się automatyczne systemy wyrzucania. Umożliwiają one natychmiastowe usuwanie części z każdej powierzchni narzędzia bez konieczności wykonywania pracy ręcznej.
Dodatkowe etapy wykańczania
Po podstawowym wypychaniu, części akrylowe często poddawane są dodatkowym procesom formowania końcowego:
- Odetnij nadmiar plastiku
- Szlifowanie lub polerowanie śladów narzędzi współpracujących
- Powierzchnie polerowane płomieniem i parą
- Nakładanie twardych powłok dla lepszej ochrony
- Łączenie zespołów za pomocą kleju lub spawania
Te prace wykończeniowe poprawiają kosmetykę i przygotowują komponenty akrylowe do wysyłki lub następnego procesu produkcyjnego.
The Proces formowania wtryskowego akrylu Kontynuuje, gdy dodatkowe komponenty są obtryskiwane, etykiety przylegają, sprzęt jest montowany, a końcowe testy potwierdzają jakość części.
Zastosowania akrylowego formowania wtryskowego
Przezroczyste lub kolorowe tworzywo akrylowe oferuje elastyczność produkcji przy użyciu technik formowania wtryskowego. Przyjrzyjmy się kilku typowym zastosowaniom.
Automatyczne światła przednie i tylne
Producenci samochodów formują niestandardowe reflektory i tylne światła z akrylu. Materiał ten jest odporny na lata eksploatacji na drodze, nie ulegając degradacji pod wpływem promieniowania UV.
Reflektory posiadają złożone odbłyśniki, które wymagają precyzyjnego formowania wtryskowego. Tworzywo akrylowe tworzy również idealne soczewki optyczne do rozpraszania wiązek światła tam, gdzie jest to potrzebne.
Syntetyczny lód
Można formować wtryskowo specjalne gatunki akrylu, aby naśladować wygląd i właściwości tarcia lodu. Lodowiska syntetyczne są odpowiedzią na wysokie koszty utrzymania tradycyjnego lodu w stanie zamrożonym.
Obiekty do curlingu, łyżwiarstwa figurowego i hokeja działają przez cały rok dzięki wtryskiwanemu akrylowi. Materiał ten dobrze sprawdza się również w przypadku tymczasowych imprez na lodzie, które nie mają stałej infrastruktury chłodniczej.
Ekrany LCD
Płaskie ekrany opierają się na akrylowych oknach i optycznych rurkach świetlnych, które zapewniają żywą klarowność wyświetlacza. Producenci form precyzyjnie wytwarzają wolne od wad, ultra przezroczyste tworzywo sztuczne, które przepuszcza światło przez różne warstwy LCD.
Wykwalifikowani technicy polerują uformowane linie podziału po rozformowaniu. Pozwala to usunąć skazy przed umieszczeniem innych komponentów elektronicznych między uformowanymi szybami.
Najczęściej zadawane pytania dotyczące procesu formowania wtryskowego akrylu
Poniżej znajdują się odpowiedzi na najczęściej zadawane pytania dotyczące procesu formowania wtryskowego akrylu:
Jakie maszyny są używane?
Standardowe prasy do formowania wtryskowego przetwarzają termicznie związki akrylowe do zastosowań formierskich. Maszyny obejmują zarówno małe pionowe, jak i większe poziome konfiguracje z tonami siły zacisku.
Wtryskiwany akryl współpracuje również z prasami do formowania wtryskowego metali. Te wyspecjalizowane maszyny oprócz tradycyjnych żywic wykorzystują również sproszkowane mieszanki metali.
Czy można formować wtryskowo wszystkie rodzaje akrylu?
Tak, gatunki takie jak akryl wytłaczany, akryl odlewany z komórek i akryl odlewany w sposób ciągły są z powodzeniem formowane wtryskowo. Producenci dostosowują procedury chłodzenia, współczynniki wypełnienia, temperaturę formy i inne parametry do przetwarzania różnych formuł akrylowych.
Po co plastyfikować akryl?
W postaci surowego granulatu akryl nie płynie i nie wypełnia skomplikowanych detali. Plastyfikacja przekształca sztywną żywicę akrylową w swobodnie płynący płyn. Pozwala to na całkowitą penetrację formy przed schłodzeniem, które przywraca akrylowi stały kształt.
Podgrzewanie akrylu w temperaturze od 240°C do 320°C topi materiał, zapewniając odpowiednią lepkość wtrysku. Akryl rozkłada się chemicznie dopiero w temperaturze ponad 380°C, czyli znacznie powyżej standardowych temperatur formowania.
Wnioski
Zrozumienie całości Proces formowania wtryskowego akrylu pozwala zaplanować wprowadzenie na rynek produktu, który efektywnie wykorzystuje ten przezroczysty materiał z tworzywa sztucznego.
Wykorzystanie odpowiedniego partnera w zakresie formowania wtryskowego pomaga uniknąć opóźnień w produkcji i kosztownych błędów iteracyjnych. Ich doświadczenie zrobi różnicę podczas kwalifikacji form akrylowych.