Formowanie wtryskowe jest jednym z najbardziej wszechstronnych i opłacalnych procesów produkcji części z tworzyw sztucznych na dużą skalę. Od klocków Lego po etui na iPhone'a, niezliczone produkty, których używamy na co dzień, zaczęły się jako stopiony plastik wtryskiwany do precyzyjnie obrobionych stalowych form.
Jednak formowanie wtryskowe wykorzystuje swój potencjał tylko wtedy, gdy projektujesz części specjalnie dla tego procesu. W przeciwieństwie do druku 3D lub Obróbka CNCKomponenty formowane wtryskowo mają bardzo surowe wymagania projektowe, aby prawidłowo wypełniać formy, unikać wad i czysto wysuwać się z oprzyrządowania po schłodzeniu.
Ignorowanie zasad projektowania form wtryskowych może prowadzić do znacznych opóźnień i niepotrzebnych kosztów na praktycznie każdym etapie, od prototypowania po produkcję. A ponieważ proces ten obejmuje kosztowne oprzyrządowanie stalowe, zmiany projektu po wyprodukowaniu formy mogą być niezwykle czasochłonne i kosztowne.
W tym kompleksowym przewodniku, jako profesjonalista producent form wtryskowychPodzielę się moimi najlepszymi wskazówkami i strategiami dotyczącymi projektowania części z tworzyw sztucznych w celu osiągnięcia sukcesu w formowaniu wtryskowym. Dowiesz się o krytycznych kwestiach projektowych, takich jak jednolita grubość ścianki, kąty pochylenia, konstrukcja żeber i występów, skurcz materiału, wykończenie powierzchni i wiele innych.
Zacznijmy od podstaw samego procesu formowania wtryskowego. Dokładne zrozumienie, w jaki sposób stopiony plastik przepływa do wnęk, pomoże zrozumieć wiele wytycznych projektowych.
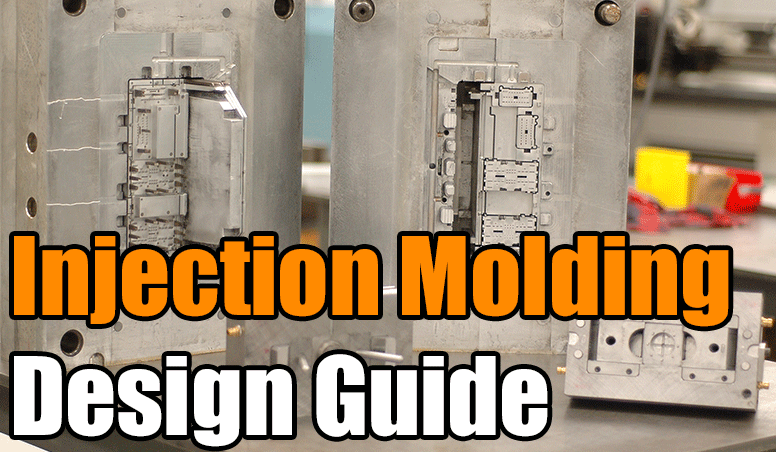
Co to jest formowanie wtryskowe i jak działa?
Maszyny do formowania wtryskowego podgrzewają granulki żywicy z tworzywa sztucznego, aby stopić je w ciecz, którą maszyny wtłaczają do stalowych form pod silnym ciśnieniem hydraulicznym. Po schłodzeniu i zestaleniu tworzywa sztucznego, forma otwiera się i automatycznie wyrzuca gotowe części.
Formy zawierają dwa podstawowe elementy stalowe:
- Wnęka: Przednia połowa oprzyrządowania tworzy zewnętrzne cechy wizualne części. Powszechnie określa się ją jako "stronę A" narzędzia.
- Rdzeń: Tylna połowa oprzyrządowania tworzy wewnętrzną i w dużej mierze ukrytą geometrię, taką jak żebra, występy, wkładki i inne elementy funkcjonalne. Producenci form wtryskowych często nazywają to "stroną B".
Miejsce styku dwóch połówek formy tworzy linię podziału, która jest niewielką linią widoczną na komponentach po zakończeniu produkcji.
Zrozumienie podstaw wtryskarek i oprzyrządowania ma kluczowe znaczenie dla skutecznego projektowania części przy użyciu tego procesu. Przyjrzyjmy się najważniejszym kwestiom projektowym, o których musi pamiętać każdy inżynier.
Kluczowe wytyczne projektowe dla formowania wtryskowego
Podczas gdy wykwalifikowani formierze wtryskowi mogą wytwarzać niezwykle precyzyjne i złożone komponenty z tworzyw sztucznych, większość ich kontroli procesu koncentruje się na doskonaleniu parametrów, takich jak temperatura, ciśnienie, siła zacisku i czas cyklu.
Jako projektant komponentów jesteś odpowiedzialny za projektowanie produktów dostosowanych do realiów przepływu stopionych tworzyw sztucznych do stalowych narzędzi kosztujących ponad $100,000.
Oto moje najlepsze wskazówki, jak najlepiej wykorzystać proces formowania wtryskowego:
Grubość ścianki
Najważniejszą wytyczną projektową dotyczącą formowania wtryskowego jest utrzymanie jednolitej grubości ścianek wszystkich części. Gdy tworzywo sztuczne stygnie, kurczy się. Niejednolite części powodują nierównomierne chłodzenie, co prowadzi do wypaczenia lub pęknięcia komponentów.
Oto ważne zasady przy rozważaniu grubości ścianki dla programu:
- Docelowa grubość w zakresie 2-4 mm dla większości zastosowań. Ultracienkościenne części poniżej 1 mm są możliwe, ale wymagają bardzo wysokiej precyzji.
- Nigdy nie zmieniaj grubości ścianki o więcej niż 15% w pojedynczej części, aby zapobiec nierównomiernemu chłodzeniu.
- Gdy konieczne jest przejście między grubszymi i cieńszymi ściankami, należy zastosować stopniowe fazowania lub zaokrąglenia zapewniające płynny przepływ.
Ponadto grube ścianki nie tylko bardziej się kurczą, ale także zatrzymują ciepło. Cieńsze, jednolite ścianki produkują mniej odpadów z powodu problemów z chłodzeniem. Szybsze cykle również obniżają koszty produkcji.
Kąty zanurzenia
Kurczący się plastik przyklejający się do stalowych ścian formy zatrzymuje linie produkcyjne, uszkadza oprzyrządowanie i zwiększa ilość odpadów. Teksturowane powierzchnie ułatwiają uwalnianie części z oprzyrządowania, a kąty pochylenia umożliwiają łatwe, zrobotyzowane wyrzucanie części.
Draft polega na lekkim zwężeniu pionowych ścian - zwykle od 1 do 5 stopni - aby zapobiec przywieraniu formowanych elementów. Jako wytyczne:
- Dodaj co najmniej 2 stopnie ciągu na wszystkich pionowych ścianach.
- Zwiększ kąty ciągu w przypadku wyższych elementów rdzenia/wnęki lub głęboko teksturowanych wykończeń powierzchni.
Formy stalowe wymagają konserwacji i okresowej wymiany w trakcie produkcji. Jednak efektywne kąty pochylenia wydłużają ogólną żywotność narzędzia.
Konstrukcja żebra i szefa
Żebra i występy wzmacniają cienkościenne sekcje podatne na zginanie lub wypaczanie pod obciążeniem. Prawidłowe zastosowanie tych cech pozwala zmniejszyć zużycie materiału i koszty, jednocześnie zapobiegając awariom.
Przestrzegaj tych zasad projektowania żeber:
- Dodaj filety u podstawy wszystkich żeber dla wzmocnienia.
- Ustaw grubość żeber w zakresie 50-60% nominalnej grubości ścianki, aby zapobiec zapadaniu się.
- W przypadku części o estetycznym wyglądzie należy utrzymywać wysokość żeber poniżej 2,5-krotności grubości, aby wyeliminować widoczne kurczenie się.
Wytyczne szefa obejmują:
- Zewnętrzna średnica piasty 2,5 x średnica sprzętu (śruby itp.).
- Ogranicz grubość ścianek do <60%, aby uniknąć śladów zacieków na widocznych powierzchniach zewnętrznych.
- W celu zwiększenia sztywności należy dodać kliny łączące występy z sąsiednimi ścianami.
Dobrze zaprojektowane żebra wzmacniające i otwory sprzętowe to cechy charakterystyczne funkcjonalnych, trwałych elementów formowanych wtryskowo.
Szybkość kurczenia się materiału
Każde tworzywo sztuczne kurczy się w unikalny sposób podczas chłodzenia w formach wtryskowych. Jednak większość kurczy się w zakresie 2-4%, co należy uwzględnić w projektach.
Zaniedbanie skurczu skutkuje niewymiarowymi częściami, które nie mogą być prawidłowo zmontowane z komponentami współpracującymi w gotowym produkcie. Sztuczka polega na kompensacji poprzez celowe projektowanie części nieco ponadwymiarowych.
Powszechne techniki stosowane przez doświadczonych twórców form obejmują:
- Zwiększenie całkowitej grubości ścianki.
- Dodawanie pasowań interferencyjnych, takich jak żebra zgniatane na wkładkach.
- Projektowanie dużych słupków wciskanych zamiast otworów.
Przegląd danych dotyczących kurczliwości formy producenta podczas wyboru materiału. Prototypuj również nowe oprzyrządowanie, aby potwierdzić właściwe strategie kompensacji skurczu.
Uzyskanie właściwego skurczu w fazie projektowania zapobiega bólom głowy związanym z wtórnymi operacjami po formowaniu.
Linie rozstania
Wcześniej omówiliśmy podstawy wieloczęściowych form wtryskowych i sposób, w jaki tworzą one komponenty, w których połówki spotykają się wzdłuż linii podziału.
Jako wytyczna projektowa, lokalizacja linii podziału wymaga osiągnięcia równowagi między estetyką a funkcjonalnością oraz uznania ich wpływu na możliwości produkcyjne.
Ze względu na wygląd często ukrywamy linie podziału wzdłuż ostrych, niekosmetycznych krawędzi lub umieszczamy je z tyłu komponentów. Działania boczne i inne złożone mechanizmy zwiększają koszty oprzyrządowania podczas uszczelniania na zakrzywionych powierzchniach.
Doskonałe umiejscowienie linii podziału poprawia również wytrzymałość i cykl życia formy. Należy tylko uważać na punkty wypełnienia, podcięcia i wypychanie, aby zapobiec wypłukiwaniu.
Lokalizacja/typ bramy
Konstrukcja bramy jest bezpośrednio związana z sukcesem formowania, ponieważ wprowadzają one stopiony plastik do wnęk. Umiejscowienie bramy ma duży wpływ na czas cyklu, wymagane ciśnienie wtrysku i estetykę komponentów.
Typowe typy bramek obejmują:
- Bramki krawędziowe: Najpopularniejsze podejście z prostokątnym profilem wzdłuż linii podziału.
- Bramki z gorącymi wskazówkami: Okrągła brama wtryskiwana przez dach wnęki najlepiej zapewnia koncentryczność.
- Bramki bezpośrednie: Duże bramy do szybkiego napełniania formy, ale wymagają dodatkowego demontażu bramy.
Poza typem, należy przestrzegać tych podstawowych zasad lokalizacji bramek:
- Ustaw bramy tak, aby najpierw wypełnić najgłębsze sekcje formy.
- Trzymać z dala od powierzchni kosmetycznych lub miejsc narażonych na duże obciążenia.
- Używanie wielu bramek ułatwia wypełnianie złożonych geometrii.
Bramki działają zasadniczo jako "wlewki" kierujące przepływem tworzywa sztucznego do gniazd formy, podobnie jak w przypadku odlewania. Dbałość o ilość, kształt, rozmieszczenie i rozmiar wlewów ma kluczowe znaczenie dla bezusterkowego formowania wtryskowego o wysokiej wydajności.
Podsumowanie
Mamy nadzieję, że niniejszy przewodnik zawiera pomocne wytyczne dotyczące projektowania form wtryskowych. Teraz, gdy rozumiesz najważniejsze wytyczne i masz dostęp do dodatkowych zasobów, jesteś gotowy do projektowania niesamowitych części z tworzyw sztucznych zoptymalizowanych pod kątem precyzyjnego formowania wtryskowego.
Wdrożenie tych koncepcji usprawni produkcję wstępną, zapobiegnie defektom i doprowadzi do stworzenia solidnych linii produkcyjnych wypompowujących bezbłędne produkty.
Jakie pytania projektowe pojawiają się podczas realizacji kolejnego projektu elementu formowanego wtryskowo? Zachęcam do kontaktu, jeśli chcesz porozmawiać na ten temat. Zawsze chętnie pomagam kolegom w zwiększaniu możliwości technicznych i dzieleniu się najlepszymi praktykami.