Skurcz. Zmora każdego wtryskarza.
Projektujesz część o idealnych wymiarach. Odpowiednio zaprogramuj maszynę do formowania. Wykonujesz kilka próbek. A potem bum! Części wychodzą niewymiarowe.
To nie koniec świata. Ale nikt nie lubi niespodzianek... zwłaszcza gdy w grę wchodzą precyzyjne części.
Dobra wiadomość? Skurcz nie musi zrujnować ci dnia. Przy odrobinie planowania i finezji można je okiełznać.
Jako profesjonalista formowanie wtryskowe tworzyw sztucznych Podzielę się z Tobą sposobami kontrolowania skurczu, abyś mógł formować części zgodnie z dokładnymi specyfikacjami.
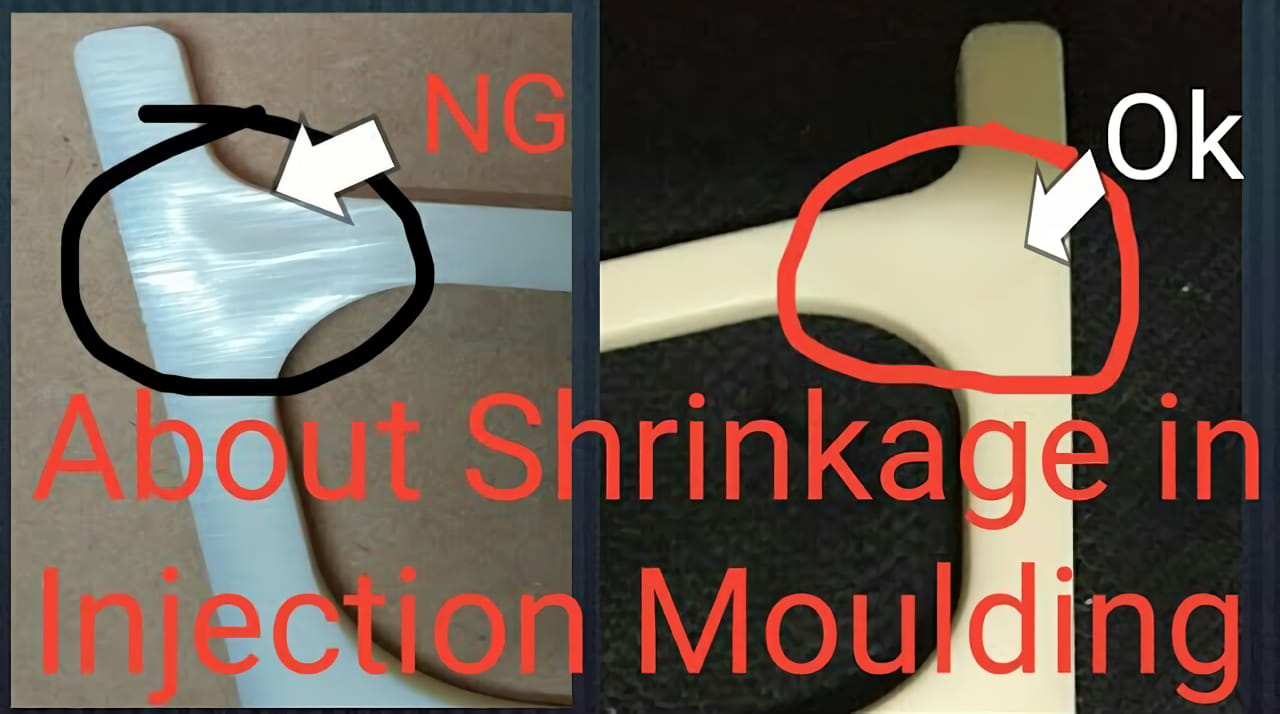
Co powoduje skurcz w formowaniu wtryskowym?
Zanim zajmiemy się rozwiązaniami, musimy przede wszystkim zrozumieć, co jest przyczyną problemu.
Wszystkie tworzywa sztuczne kurczą się, gdy stygną ze stopionej masy do stałych części. Im gorętsze tworzywo sztuczne, tym bardziej rozciągnięte są łańcuchy polimerowe. Gdy wszystko się ochładza, następuje skurcz termiczny. (Wiesz, to całe "gorące powietrze unosi się" z podstawówki).
Wielkość skurczu zależy od kilku czynników:
- Materiał: Żywice amorficzne, takie jak ABS, mają tendencję do kurczenia się bardziej niż żywice krystaliczne, takie jak nylon. Dlaczego? Łańcuchy polimerowe w materiałach amorficznych nie są tak ściśle upakowane, więc mają więcej miejsca na kurczenie się podczas chłodzenia.
- Konstrukcja formy: Grubsze części lub części o nierównej grubości ścianek są podatne na nierównomierne kurczenie się. Grubsze obszary stygną - a tym samym kurczą się - wolniej niż cieńsze sekcje.
- Warunki przetwarzania: Duża prędkość wtrysku w połączeniu z niskim ciśnieniem docisku pozwala na luźne upakowanie materiału w gnieździe formy. Pozwala to na większy skurcz po ostygnięciu.
Teraz, gdy wiemy już, dlaczego dochodzi do kurczenia się, porozmawiajmy o tym, jak temu zaradzić.
Jak zmniejszyć skurcz w formowaniu wtryskowym?
Kontrolowanie skurczu obejmuje trzy główne podejścia:
- Optymalizacja projektu formy
- Wybór odpowiedniego materiału
- Dostosuj parametry procesu
Rozbijmy to na czynniki pierwsze.
1. Optymalizacja projektu formy
Gdyby maszyna do formowania miała swój sposób, każda część chłodziłaby się dokładnie w tym samym tempie we wszystkich sekcjach. Brak nierównomiernego chłodzenia = brak nierównomiernego skurczu lub wypaczenia.
Nie żyjemy jednak w idealnym świecie. A osiągnięcie całkowicie jednolitego chłodzenia w złożonych geometriach 3D jest łatwiejsze do powiedzenia niż do wykonania.
Mimo to, możemy skorzystać z kilku strategii projektowych, aby zbliżyć się do nich tak bardzo, jak to tylko możliwe:
- Eliminacja nagłych zmian grubości ścianki: Staraj się stopniowo przechodzić między cienkimi i grubymi sekcjami (filety są tutaj twoimi przyjaciółmi). Pomaga to zapobiegać powstawaniu "gorących punktów" i minimalizuje nierównomierne kurczenie się.
- Uważaj na narożniki: Ostre narożniki działają jak koncentratory naprężeń, które podkreślają kurczenie się materiału. Zaokrąglone narożniki rozkładają naprężenia bardziej równomiernie.
- Strategiczne rozmieszczenie żeber: Żebra i kliny wzmacniają części bez znaczącej zmiany grubości ścianki. Należy jednak uważać, aby nie tworzyć nowych gorących punktów.
- Wybierz bramę: Umieszczenie bramy określa sposób, w jaki materiał wpływa do formy. Upewnij się, że wszystko wypełnia się równomiernie. Brak słabych punktów, w których materiał nie może się w pełni zapakować.
Wskazówka: Oprogramowanie symulacyjne umożliwia podgląd rozkładu temperatury i skurczu przed cięciem stali. Pozwala to zoptymalizować projekt formy cyfrowo, a nie poprzez kosztowne próby i błędy na hali produkcyjnej.
2. Wybór odpowiedniego materiału
Jeśli wymagana jest ekstremalna precyzja wymiarowa, należy zacząć od odpowiedniego surowca.
Oto kilka rzeczy, które należy wziąć pod uwagę w odniesieniu do kurczenia się:
- Żywice amorficzne i krystaliczne: Jak wspomniano wcześniej, materiały amorficzne, takie jak ABS lub poliwęglan (PC) mają tendencję do kurczenia się bardziej niż żywice krystaliczne. Acetal i nylon są lepszymi opcjami, jeśli skurcz musi być ograniczony.
- Wzmocnione tworzywa sztuczne: Dodanie włókna szklanego, włókna węglowego lub talku do mieszanki materiałów zwiększa stabilność wymiarową. Kompromis polega na tym, że te wypełniacze lub wzmocnienia mogą sprawić, że tworzywo sztuczne będzie bardziej lepkie - potencjalnie powodując problemy z formowaniem.
- Poznaj swoje dane PVT: Każdy dostawca materiałów zapewnia szczegółowe informacje na temat charakterystyki skurczu żywicy w różnych zakresach temperatur i ciśnień (dane PVT). Zapoznaj się z tymi informacjami, aby wybrać najlepszą opcję.
Konkluzja: Współpracuj z dostawcą materiałów, aby wybrać żywicę, która spełnia zarówno potrzeby aplikacji, jak i zapewnia minimalny skurcz.
3. Dopracowanie parametrów procesu
Ostatnim, ale nie mniej ważnym aspektem jest wykorzystanie elastyczności wtryskarek do udoskonalenia samego procesu formowania.
Celem jest upakowanie jak największej ilości materiału w formie PRZED rozpoczęciem krzepnięcia. Pozostawia to mniej miejsca na naturalne kurczenie się, które występuje podczas chłodzenia.
Oto kilka usprawnień procesu, które warto wypróbować:
- Zwiększ ciśnienie: Zwiększenie ciśnienia wtrysku powoduje zbliżenie łańcuchów polimerowych do siebie. Zwiększenie ciśnienia pakowania i utrzymywania przeciwdziała kurczeniu się po początkowym wtrysku poprzez jeszcze większe zagęszczenie cząsteczek.
- Powolne napełnianie: Szybkie tempo napełniania może pozostawić słabe punkty w profilu materiału. Zmniejszenie prędkości wtrysku pozwala na ściślejsze upakowanie materiału.
- Wydłużenie czasu chłodzenia: Wiem, wiem... dłuższy czas cyklu wpływa na produktywność. Jednak umożliwienie pełnego schłodzenia części przed ich wyrzuceniem pozwala uniknąć usuwania ich w stanie "zestalonym, ale wciąż kurczącym się".
Porada: Nie podnoś ciśnienia do niebotycznych wartości od razu. Zacznij ostrożnie i stopniowo zwiększaj ciśnienie, oceniając jakość części. Nadmierne ciśnienie może również powodować problemy, takie jak ślady zapadania się, puste przestrzenie lub rozbłyski.
Ile "nadwymiarować" w przypadku skurczu?
Teraz nadszedł moment prawdy.
Zastosowanie tej wiedzy w praktyce wymaga jeszcze jednego kroku - kompensacji skurczu poprzez celowe przewymiarowanie gniazda formy.
Ale o ile?
Jak zawsze, nie ma sztywnych i szybkich reguł. Skurcz zależy od wszystkich czynników opisanych powyżej. Najlepszą odpowiedzią jest wyprodukowanie próbek, które jak najdokładniej naśladują formę/proces produkcyjny.
Poniżej przedstawiamy jednak kilka docelowych rozmiarów w oparciu o żywicę, z którą pracujesz:
- Polietylen (PE): 2-5%
- Polipropylen (PP): 1.5-3%
- Akrylonitryl-butadien-styren (ABS): 2-4%
- Nylon: 2-4%
Te wartości procentowe należy zweryfikować poprzez próbkowanie, ale stanowią one rozsądne punkty wyjścia do wstępnego doboru rozmiaru formy.
Kluczem jest dostosowanie wymiarów na podstawie rzeczywistych danych pomiarowych z formowanych części. Wymaga to kilku iteracyjnych poprawek, ale wyzerowanie dokładnego nadwymiaru potrzebnego do wyprodukowania dokładnie zwymiarowanych, stabilnych wymiarowo części jest warte wysiłku.
Nikt nie powiedział, że formowanie wtryskowe jest łatwe! Jednak odrobina wiedzy w połączeniu ze strategicznym dostosowaniem procesu pozwala zminimalizować skurcz.
A kiedy wszystko jest już powiedziane i zrobione, ta ładna część wyskakująca z formy sprawia, że wszystko jest tego warte!