Formowanie wtryskowe to powszechny proces produkcyjny wykorzystywany do wytwarzania części z tworzyw sztucznych na dużą skalę. Właściwe zaprojektowanie części do formowania wtryskowego ma kluczowe znaczenie dla uniknięcia wad, kontroli kosztów oraz osiągnięcia pożądanego wyglądu i wydajności. Ten kompleksowy przewodnik projektowy przedstawia kluczowe kwestie dotyczące geometrii części, wyboru materiału, oprzyrządowania i operacji wtórnych w celu optymalizacji komponentów formowanych wtryskowo.
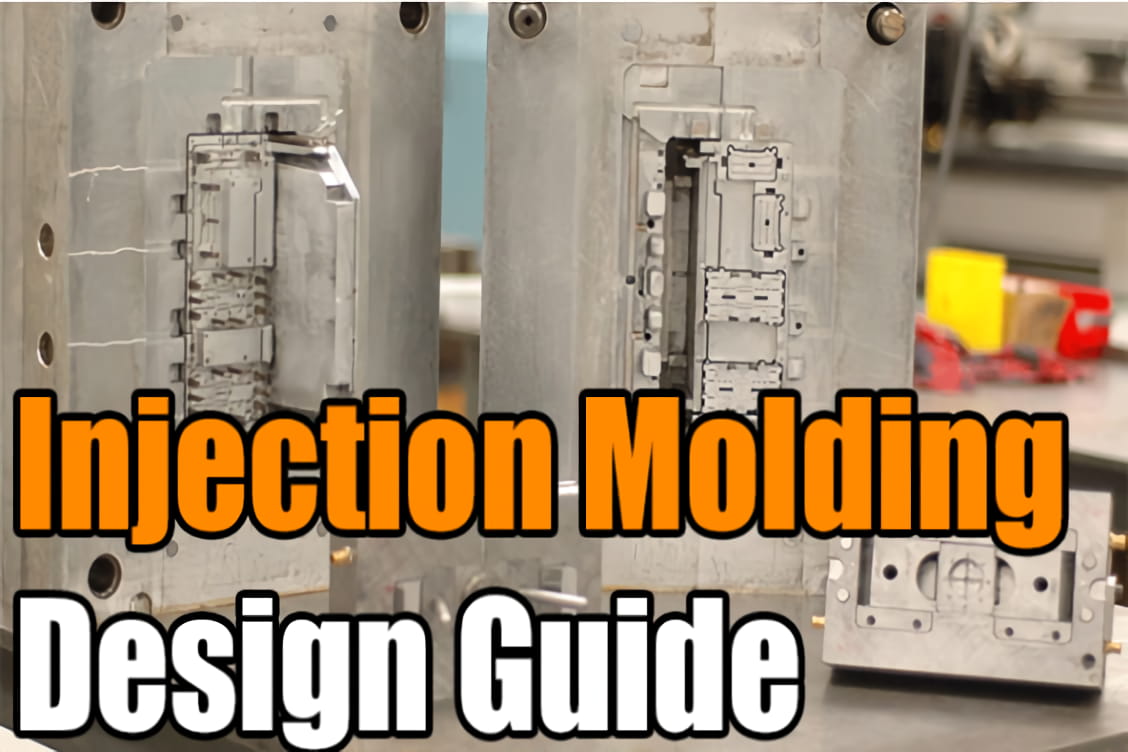
Przewodnik projektowania form wtryskowych
Krytyczne elementy projektu
Istnieje kilka krytycznych elementów, które należy wziąć pod uwagę podczas projektowania części do formowania wtryskowego:
Linie rozstania
Linia podziału to miejsce, w którym dwie połówki formy wtryskowej spotykają się w celu wyrzucenia schłodzonej, zestalonej części. Linie podziału zawsze będą widoczne na gotowych częściach w pewnym stopniu w zależności od lokalizacji, dozwolonych kątów pochylenia i wykończenia powierzchni. Strategiczne umieszczenie linii podziału może pomóc zminimalizować widoczność.
Podcięcia
Podcięcia odnoszą się do geometrii części, które wystają lub powodują zakłócenia, przez co część nie może zostać czysto wyrzucona z prostej dwuczęściowej formy wtryskowej. Typowe przykłady obejmują otwory krzyżowe, gwinty i haki zatrzaskowe. Podcięcia zwiększają złożoność i koszty oprzyrządowania. Tam, gdzie to możliwe, części powinny być projektowane tak, aby uniknąć podcięć przy użyciu technik takich jak kąty pochylenia lub elementy przekształcające. Nieuniknione podcięcia można uwzględnić poprzez zastosowanie rdzeni bocznych i innych wkładek.
Kąty zanurzenia
Kąty zanurzenia są niezbędne na wszystkich pionowych powierzchniach części, aby zmniejszyć tarcie i umożliwić czyste wyrzucenie z formy. Minimalny kąt zanurzenia wynoszący 1-2 stopnie jest zalecany dla większości elementów, a większy jest wymagany w przypadku wyższych geometrii lub teksturowanych wykończeń powierzchni.
Grubość ścianki
Jednolita grubość ścianki w całej części jest optymalna, aby ułatwić przepływ materiału, zmniejszyć ryzyko wypaczenia, zminimalizować czas cyklu i obniżyć koszty. Typowe specyfikacje grubości ścianek wahają się od 0,060 do 0,180 cala w zależności od użytego materiału. Stopniowe przejścia powinny łączyć wszystkie sekcje o różnych grubościach ścianek.
Promienie i narożniki
Ostre narożniki koncentrują naprężenia i powodują wcześniejsze uszkodzenia części. W miarę możliwości należy stosować duże zaokrąglenia i promienie na wszystkich wewnętrznych i zewnętrznych narożnikach, aby zachować wytrzymałość.
Zaawansowane kwestie projektowe
Oprócz podstawowych wymagań dotyczących geometrii i szkicu, następujące funkcje zapewniają dodatkową funkcjonalność części i wymagają dodatkowej staranności podczas projektowania:
Szefowie
Pustaki służą jako punkty mocowania dla wkładek lub wkrętów samogwintujących. Cienkie żebra lub kliny powinny łączyć piasty z głównymi ścianami, gdy tylko jest to możliwe, aby poprawić stabilność i uniknąć zapadnięć spowodowanych kurczeniem się materiału.
Żebra
Żebra wzmacniają części bez zwiększania grubości ścianki. Żebra powinny być zaprojektowane zgodnie z limitami grubości ścianek i zawierać zaokrąglenia u podstawy, aby uniknąć koncentracji naprężeń.
Snap Fits
Pasowania zatrzaskowe umożliwiają montaż części formowanych wtryskowo bez użycia elementów złącznych. Podobnie jak w przypadku innych występów z nominalnej geometrii ściany, przeciąg jest niezbędny na pionowych ścianach pasowania zatrzaskowego, aby umożliwić rozformowanie. Grubość w stosunku do ściany nominalnej i umiejscowienie wymagają dodatkowej analizy podczas projektowania haków lub wsporników.
Żywe zawiasy
Żywe zawiasy działają jak cienkie, elastyczne połączenia między sztywnymi segmentami z tworzywa sztucznego. Wybór materiału jest krytyczny, a polipropylen i polietylen są powszechnie stosowane w produktach konsumenckich. Grubość zawiasu, ograniczenia długości i włączenie ramion wpływają na trwałość w oczekiwanych cyklach życia.
Uwagi dotyczące materiałów
Wybór materiału wpływa na wygląd części, wymagania dotyczące wydajności, opcje oprzyrządowania i wymagane procesy produkcyjne. Niektóre kluczowe alternatywy tworzyw sztucznych obejmują:
- Polipropylen (PP) - Tania żywica o dobrej odporności chemicznej, często stosowana w produktach konsumenckich i rurociągach.
- Akrylonitryl-butadien-styren (ABS) - Powszechny wybór, gdy wymagana jest wyższa wytrzymałość i plastyczność w stosunku do PP. Stosowany w obudowach samochodowych i elektronicznych
- Poliwęglan - Optycznie przezroczysta opcja o wysokiej wytrzymałości, gdy odporność na uderzenia i stabilność wymiarowa mają kluczowe znaczenie
- Poliamid (nylon) - Preferowany do części mechanicznych wymagających większej wytrzymałości, zmęczenia i odporności na zużycie
Wykończenie powierzchni
W zależności od wstępnej obróbki formy i przenoszonych tekstur, na powierzchniach części formowanych wtryskowo można uzyskać różne efekty estetyczne. Typowe alternatywy według standardów SPI obejmują:
- SPI-A2 - Błyszczące, lustrzane wykończenie uzyskane dzięki polerowaniu diamentowemu.
- SPI-B1 - Satynowe, matowe wykończenie dzięki zastosowaniu papieru ściernego o ziarnistości 600 na formie
- Teksturowanie formy - Niestandardowe wykończenia przypominające ziarno nakładane za pomocą form do piaskowania
Operacje dodatkowe
Etapy po formowaniu, takie jak montaż, etykietowanie, drukowanie, spawanie lub obróbka skrawaniem, mogą w razie potrzeby rozszerzyć funkcjonalność części:
- Tampodruk - Metoda dodawania kolorowych logo, etykiet i grafik na zakrzywionych powierzchniach formowanych wtryskowo
- Spawanie ultradźwiękowe - Łączy oddzielnie formowane komponenty, wywołując wibracje o wysokiej częstotliwości.
- Obróbka CNC - Umożliwia tworzenie bardziej precyzyjnych elementów, które są trudne do bezpośredniego zintegrowania z formowanymi konstrukcjami.
Szybka lista kontrolna projektu
Podczas finalizowania projektów części formowanych wtryskowo, poniższa lista kontrolna obejmuje kluczowe elementy do przeglądu:
- Jednolita grubość ścianki od 0,060 do 0,180 cala
- Minimalny kąt zanurzenia wynoszący 1 stopień zastosowany do wszystkich powierzchni pionowych
- Promienie na wszystkich narożnikach wewnętrznych i zewnętrznych
- Dodano żebra wspierające do odizolowanych bossów
- Kratownice łączące wystające żebra z powrotem do ścian nominalnych
- Skontrolowano bramę, trzpień wyrzutnika i lokalizacje otworów wentylacyjnych
- Podcięcia wyeliminowane tam, gdzie to możliwe
- Określone standardowe wykończenie powierzchni SPI
Prawidłowe uwzględnienie tych krytycznych kwestii projektowych zapewni dokładne wymiarowo części o niższych wadach produkcyjnych i kosztach. Skontaktuj się z nami, jeśli masz pytania dotyczące optymalizacji kolejnego elementu lub zespołu formowanego wtryskowo.