W formowaniu wtryskowym prowadnica jest kluczowym elementem, który prowadzi stopione tworzywo sztuczne z dyszy wtryskowej do gniazd formy. Jako profesjonalista Producent form wtryskowych z tworzyw sztucznychDlatego piszę ten kompleksowy przewodnik, aby omówić wszystko, co musisz wiedzieć o prowadnicach, w tym ich rodzaje, kwestie projektowe, ich wpływ na jakość części i nie tylko.
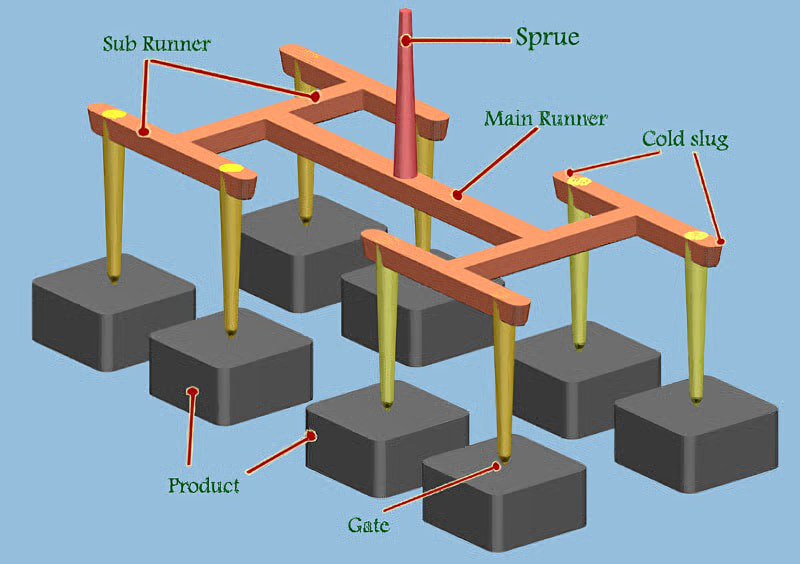
Co to jest Runner w formowaniu wtryskowym?
Prowadnica to kanał wycięty w formie, który przenosi stopione tworzywo sztuczne z dyszy wtryskowej do wnęk podczas procesu formowania wtryskowego. Służy jako przejście, które umożliwia równomierny przepływ tworzywa sztucznego do wnęk.
Dobrze zaprojektowane prowadnice są niezbędne do produkcji wysokiej jakości, spójnych części. Rozmiar, kształt i położenie prowadnic ma bezpośredni wpływ na szybkość wypełniania wnęk, straty materiału, jakość części i czas cyklu.
Komponenty systemu Runner
Kompletny system runner składa się z kilku kluczowych komponentów:
Wlew - W pierwszym segmencie stopione tworzywo sztuczne wchodzi przez dyszę wtryskową. Wlew podaje materiał do prowadnic.
Biegacze - Kanały o różnych długościach i średnicach, które rozprowadzają materiał do bram formy.
Bramki - Końcowe zwężone punkty przejścia z prowadnic do wnęk części. Zasuwy regulują przepływ do wnęk.
Elementy te współpracują ze sobą, aby zapewnić równomierny przepływ tworzywa sztucznego do wszystkich wnęk jednocześnie. Celem końcowym jest wyprodukowanie w pełni wypełnionych części wolnych od wad w najkrótszym możliwym czasie cyklu.
Systemy Cold Runner vs Hot Runner
Istnieją dwa główne typy systemów prowadnic do formowania wtryskowego - zimne i gorące:
Cold Runners
Prowadnice zestalają się wewnątrz formy wraz z formowanymi częściami. Wlew, prowadnice i części pozostają połączone jako jeden solidny element po wyrzuceniu. Wypełnione materiałem zimne kanały stanowią odpad, który należy usunąć i ponownie przetworzyć lub wyrzucić.
Zimne kanały pozwalają na prostsze formy, niższe koszty oprzyrządowania, elastyczność projektowania i dostosowanie do różnych żywic. Generują one jednak więcej odpadów i mają dłuższy czas cyklu w porównaniu do gorących kanałów.
Hot Runners
Gorące kanały wykorzystują podgrzewane kolektory i dysze do utrzymywania tworzywa sztucznego w stanie stopionym, gdy przepływa ono do wnęk. Po wyrzuceniu zestalone części są wyrzucane bez dołączonych wlewków lub prowadnic. Zmniejsza to ilość odpadów i przyspiesza czas cyklu.
Formy gorącokanałowe są bardziej złożone i kosztowne w produkcji niż formy zimnokanałowe. Redukcja odpadów, choć długoterminowa, może zapewnić znaczne oszczędności kosztów w scenariuszach produkcji wielkoseryjnej.
Dlaczego właściwa konstrukcja runnera jest kluczowa
Wydajność każdej formy wtryskowej w dużym stopniu zależy od konstrukcji układu kanałów. Oto dlaczego optymalizacja układu kanałów jest tak ważna:
Czas napełniania i ciśnienie
Odpowiednio dobrane prowadnice szybciej wypełniają puste przestrzenie, umożliwiając przepływ przy mniejszych stratach ciśnienia. Cienkie, długie prowadnice mogą przedwcześnie zamarzać, powodując krótkie strzały.
Jakość części
Zrównoważona konstrukcja kanału zapewnia równomierny przepływ stopionego materiału do wszystkich wnęk. Ta spójność zapewnia jednolite właściwości i wygląd każdej części. Niezrównoważone systemy prowadzą do różnic między wnękami, powodując problemy z jakością.
Wydajność cyklu
Nadmierna liczba kanałów oznacza wydłużenie czasu krzepnięcia i chłodzenia, co spowalnia cykle. Zoptymalizowany układ minimalizuje objętość kanałów w celu szybkiego chłodzenia i wyrzucania części.
Oszczędność materiałów
Krótsze prowadnice o mniejszej średnicy zmniejszają ilość zmarnowanego wlewu i tworzywa sztucznego. Prowadzi to do znacznych oszczędności kosztów, zwłaszcza w zastosowaniach zimnokanałowych.
Wytyczne projektowe dla kluczowych biegaczy
Oto kluczowe wskazówki dotyczące projektowania efektywnego układu systemu runner:
Rozmiar
1. Średnice - Powinien być odpowiednio dobrany w oparciu o czynniki takie jak grubość ścianki części, długość przepływu, właściwości stopu oraz prędkość/ciśnienie wtrysku. Typowe średnice wynoszą od 2 mm do 10 mm.
2. Długości - Zminimalizuj wszystkie segmenty prowadnic - utrzymuj ciągi od wlewu do bramek tak krótkie, jak to możliwe. Długie odcinki przepływu obniżają ciśnienie i sprzyjają przedwczesnemu zamarzaniu.
Równoważenie
3. Równe ścieżki przepływu - Upewnij się, że trasy do każdej wnęki mają taką samą długość, aby zapewnić zrównoważone warunki. Wykorzystanie symulacji przepływu do sprawdzenia wydajności.
4. Bramki strategiczne - Zwiększenie liczby bramek/lokalizacji w celu zapewnienia bardziej bezpośredniego dostępu do wnęki i zminimalizowania objętości runnerów.
Konfiguracja
5. Prostota - Używaj najmniej złożonego systemu, który spełnia cele wydajnościowe. Prostsze jest lepsze. Ocenić potrzebę stosowania dodatkowych prowadnic lub podbramek.
6. Usprawniony układ - Delikatnie zakrzywione prowadnice podążają za konturami, zamiast ostro skręcać pod kątem. Eliminacja martwych stref, w których materiał może się zatrzymywać.
Prawidłowe uwzględnienie tych elementów konstrukcyjnych zapewnia niezawodny sukces każdego systemu biegowego, maksymalizując jakość i wydajność.
Jak prowadnice wpływają na jakość części formowanych wtryskowo
Wady w układzie prowadnic często objawiają się jako widoczne wady części lub problemy z wydajnością. Oto jak to zrobić:
Niezrównoważone wypełnienie - Gdy ścieżki przepływu zawierają drastyczne różnice w stratach ciśnienia, wnęki wypełniają się w różnym tempie. Wolniejsze wypełnianie pozwala na nierównomierne chłodzenie materiału w formie, tworząc widoczne linie spoin, ślady zapadnięć, puste przestrzenie lub wypaczenia.
Przedwczesne zamrażanie - Nieodpowiedni rozmiar kanału w stosunku do długości przepływu ogranicza ciśnienie, pozwalając stopionemu materiałowi zamarznąć przed całkowitym wypełnieniem. Skutkuje to krótkimi częściami z niekompletnymi detalami.
Strzyżenie - Nadmierne przejścia kątowe lub zwężenia degradują polimery poprzez nadmierne ogrzewanie i chłodzenie. Prowadzi do miejscowych zmian właściwości materiału.
Każdy z tych typowych defektów wskazuje na podstawowe niedociągnięcia w projekcie runnera.
Optymalizacja i analiza projektu runnera
Stworzenie optymalnego systemu runner jest złożonym przedsięwzięciem wymagającym doświadczenia i specjalistycznych narzędzi symulacyjnych. Oto ogólny przegląd nowoczesnego podejścia do projektowania:
1. Układ koncepcyjny - Początkowa konfiguracja prowadnicy jest z grubsza naszkicowana w oparciu o geometrię części, wybór materiału, właściwości przetwarzania i doświadczenie.
2. Analiza przepływu formy - Szczegółowe badania symulacyjne oceniają proponowane układy w rzeczywistych warunkach. Umożliwia dokładne przewidywanie wydajności. Umożliwia szybką analizę wielu pomysłów typu "co by było gdyby" w celu udoskonalenia strategii.
3. Ostateczna walidacja - Optymalne projekty pochodzące z analizy są ostatecznie potwierdzane empirycznie przez rzeczywiste próbkowanie form. Daje to możliwość dostosowania ustawień przed rozpoczęciem produkcji form na pełną skalę.
Wykorzystanie metod analizy do informowania o projektach zapobiega kosztownym korektom w przyszłości, jeśli nieoptymalne wybory trafią do stali. Początkowa inwestycja czasowa zwraca się znacznie w całym okresie eksploatacji formy.
Najczęściej zadawane pytania dotyczące formowania wtryskowego
Poniżej znajdują się odpowiedzi na najczęściej zadawane pytania dotyczące prowadnic do formowania wtryskowego:
Jaka jest najlepsza średnica prowadnicy?
Typowe średnice wynoszą od 2 mm do 10 mm, w zależności od czynników takich jak długość przepływu, lepkość materiału i prędkość wtrysku. Szersze prowadnice umożliwiają szybsze napełnianie, ale wolniej się zestalają, co wydłuża czas cyklu.
Gdzie powinny znajdować się bramki do wnęk?
Bramki powinny wchodzić w grubsze ścianki części w minimalnie widocznych miejscach na zewnątrz. Umożliwia to najszybsze napełnianie i najłatwiejsze odgazowywanie przy jednoczesnym zminimalizowaniu widocznych skaz.
W jaki sposób biegacze powinni rozgałęziać się do wielu wnęk?
Główny kanał powinien dzielić się na równomiernie rozmieszczone odgałęzienia prowadzące bezpośrednio do każdej bramy wnęki na tych samych długościach. Zapewnia to jednoczesne zrównoważone warunki napełniania we wszystkich zagłębieniach.
Jaka jest korzyść z hot runnera w porównaniu do cold runnera?
Gorące kanały eliminują odpady, umożliwiając jednocześnie szybsze cykle. Jednak zimne kanały kosztują początkowo mniej i współpracują z większą liczbą materiałów. Określ kompromisy w oparciu o priorytety lub ograniczenia specyficzne dla danego zastosowania.
Jak długa powinna być prowadnica do formowania wtryskowego?
Jak najkrótsze. Zasadniczo, jeśli pozwala na to zastosowanie, długość przewodów nie powinna przekraczać 2 stóp. Dłuższe mogą powodować nadmierne straty chłodzenia i ciśnienia, pogarszając jakość części końcowych.
Jak stworzyć najbardziej opłacalny system dla biegaczy?
Skupienie się na minimalizacji wymiarów w celu wykorzystania jak najmniejszej ilości materiału przy jednoczesnym wystarczającym wypełnieniu części. Strategiczne rozmieszczenie bramek również minimalizuje nakład pracy. Unikaj zbyt złożonych geometrii, gdy prostsza trasa daje takie same wyniki. Użyj narzędzi analitycznych, aby znaleźć optymalne kompromisy.
Wnioski
Optymalizacja prowadnic ma kluczowe znaczenie dla osiągnięcia sukcesu produkcyjnego w formowaniu wtryskowym w każdej branży. Chociaż niewidoczne dla użytkowników końcowych, te "zakulisowe" komponenty naprawdę tworzą wszystko, co jest potrzebne do niezawodnej i wydajnej produkcji wysokiej jakości części z tworzyw sztucznych z każdej formy.