Plastic Injection Molding Manufacturer
Baiwe is a top Chinese plastic injection molding manufacturer. We can make a wide range of custom plastic parts for your needs.
Types of Our Plastic Injection Molding Service
Reliable Plastic Injection Molding Manufacture in China
Injection molding is a process where plastic is heated and injected into a mold to create products. The products are removed from the mold after cooling. Injection molding machines make many products. China’s plastic molding industry has developed over the years and is now the world’s largest. Baiwe is now one of China’s top injection molding companies.
Plastic Injection Molding Definition
Plastic injection molding is a manufacturing process that converts plastic pellets into fully formed parts. Specialized machines melt plastic resin and inject it at high pressure into custom steel molds. After the plastic cools and hardens, the mold opens to reveal newly created products.
This high-volume process makes plastic injection molding ideal for mass production. In fact, manufacturers use it to produce billions of identical plastic components each year. Common injection molded parts include bottle caps, fishing lures, and even medical devices. The automotive industry also utilizes this technique to craft intricate dashboard pieces.
Our Plastic Injection Molding Capacity
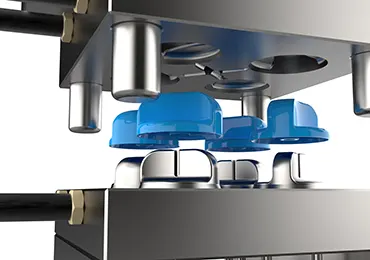
In-house Tooling Workshop
We are fully equipped with mold-making equipment, such as CNC, EDM, wire cutting, drilling machines, and tapping machines.
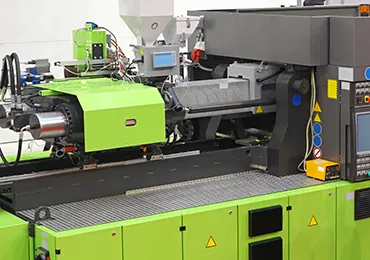
Advanced Plastic Injection Molding Machine
We have over 50 plastic injection molding machines, each weighing different tons and capable of making various kinds of plastic parts.
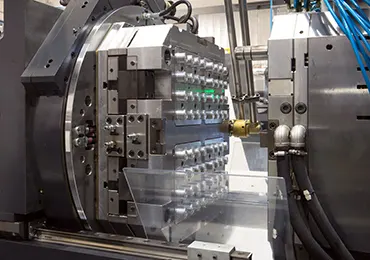
Large Part Injection Molding
We have big plastic injection molding machines for making large plastic parts for our clients. The machines can weigh up to 3000 tons, can make over 35 kg parts, and can be up to 250cm long.
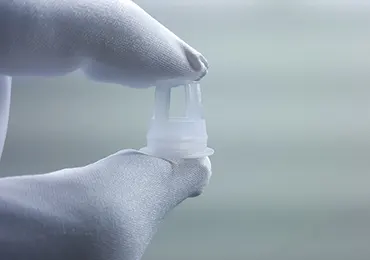
China Plastic Pnjection Molding Medical Parts
We have a 100k-grade clean workshop for manufacturing plastic medical parts.
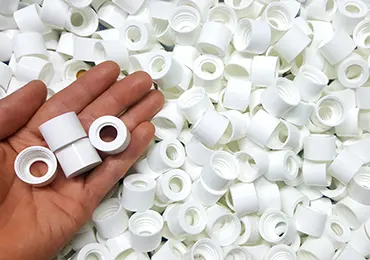
China ABS Injection Molded Plastic Parts
We have made over 100 plastic materials products for our clients.
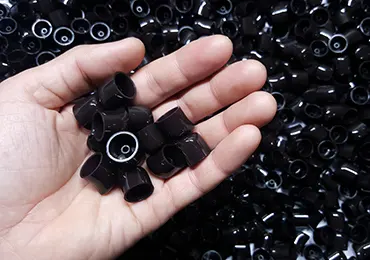
China Precision Plastic Injection Molding
Baiwe provides turnkey plastic injection-molded products for you. We can make high-precision plastic parts with tolerances up to ±0.001mm.
About Baiwe
Best Plastic Injecttion Molding Manufacturer in China
Baiwe is a professional Chinese plastic mold manufacturer with experience in plastic injection, OEM, molding, and manufacturing.
3D Mold Design: We can design molds for physical plastic parts.
Mold DFM Analysis: Baiwe will evaluate whether a plastic product is suitable for injection molding.
DFM analysis: helps you understand the risks of injection molding. Knowing these risks helps reduce waste costs.
Injection Molding Plastic Prototypes: We have the equipment, including 3D printers, to make your low-volume plastic molding project a success.
Injection Molding: Baiwe has 15 plastic injection machines.
Injection Molding and Assembly of Plastic Products: We can create injection-molded plastic parts and assemblies for your project.
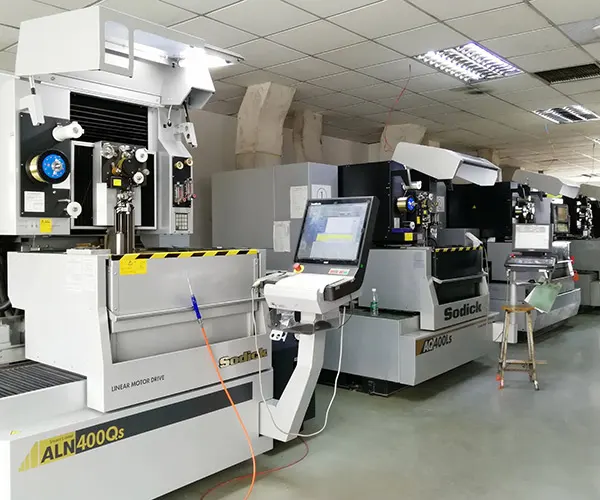
What We Can Make
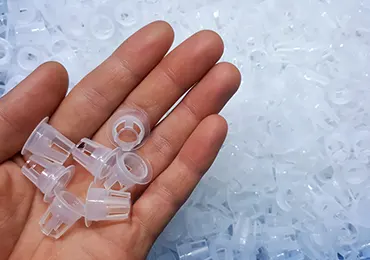
Custom Plastic Molded Fliter
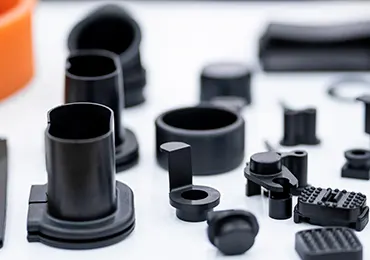
Black Plastic Molded Parts
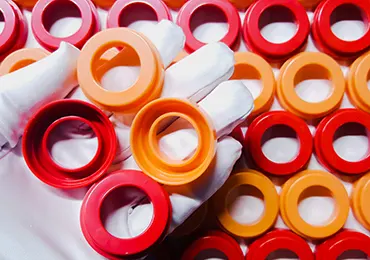
Plastic Injection Molding Lids
Advantages of Plastic Injection Molding
High Volume Production
Once the injection molding machine is set up, it can produce thousands of identical plastic parts in a single day. Automation allows mass production around the clock. Part costs are low.
Fine Tolerances
Injection molding can hold tighter tolerances than competing processes like CNC machining or casting. Parts have a high degree of precision with little variation among parts.
Material Versatility
Thermoplastic polymers offer tremendous variation in mechanical properties, aesthetics, chemical resistance, performance etc. Parts can be colored, filled or altered for special qualities. Recycled plastics lower costs.
Complex Geometries
Multi-cavity molds using side-action, unscrewing and collapsible core techniques can produce highly complex parts with no secondary machining required.
Assembly Consolidation
Insert molding allows placing pre-assembled components inside a plastic part during production. Multi-shot techniques use sequential shots of different plastics. This simplifies product assembly.
Fast Production
Once mold and machine are set up, injection molding production rates are vastly faster than alternatives like CNC machining or 3D printing. Shots take seconds or minutes. 24/7 automation maximizes production scheduling.
Lower Labor
Automating injection molding systems cuts labor costs substantially. Robots even handle finished parts. One operator can manage multiple machines/molds and oversee part handling systems.
Applications of Plastic Injection Molding
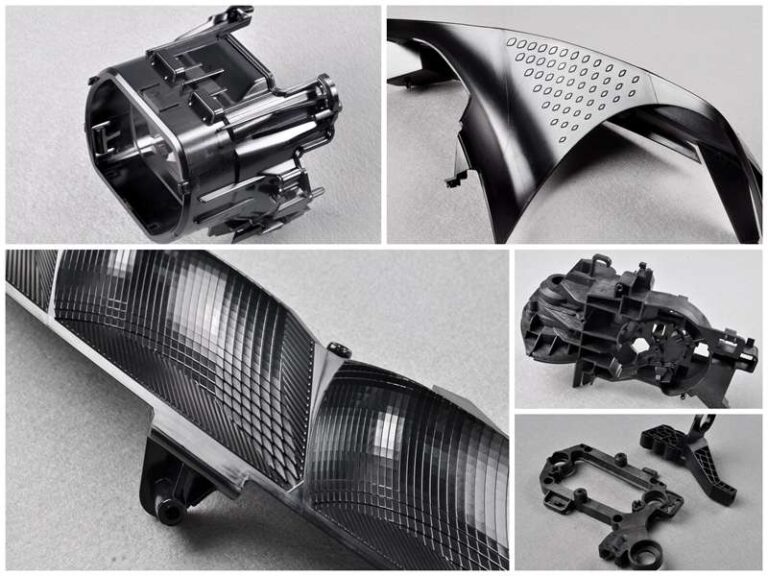
Automotive
Panels, bumpers, lighting components, fluid reservoirs, dashboard instrument housings and heat ventilation parts utilize injection molding extensively. Newer techniques mold hybrid plastic-metal composites and injection overmolded parts.
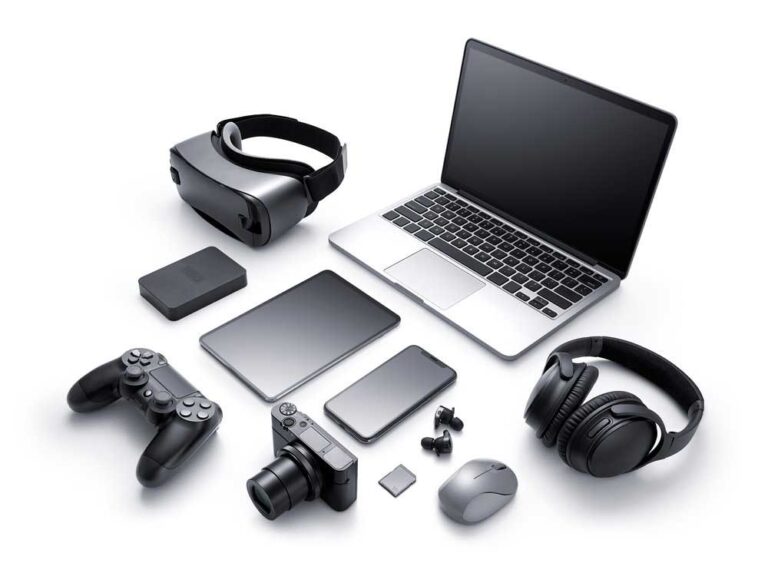
Electronics
Mobile device housings, computer keyboards, TV remote exteriors and other consumer electronics rely on precision plastic parts from injection molding. The process also molds tiny electrical connectors and precision enclosures.
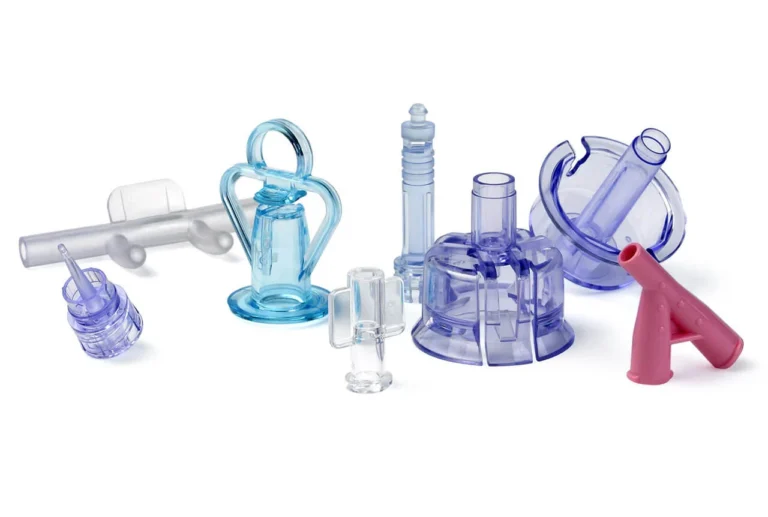
Medical Industry
Disposable syringes, vials, valves, IV tubes, surgical instruments like forceps, and diagnostic devices molded from plastic engineered for medical devices. Newer lightweight prosthetics also use injection molded plastics.
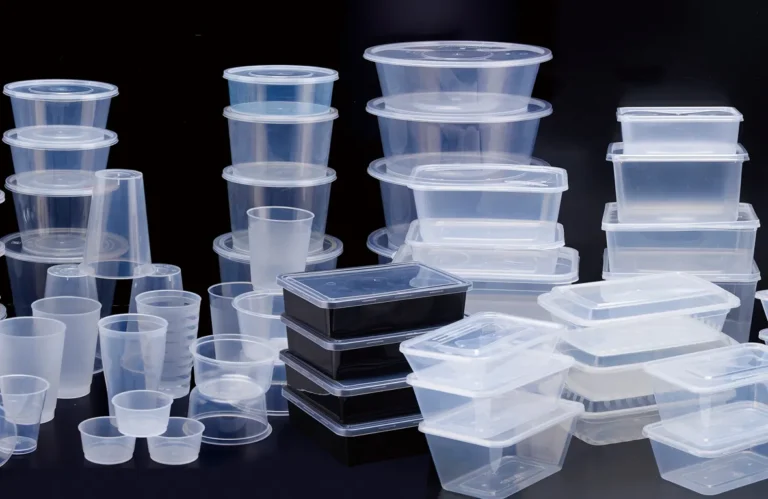
Packaging Industry
Injection molding produces plastic bottles, containers, caps and closures, cases, trays and bags for consumer goods. Food packaging molds antibacterial plastics. Cosmetics packaging focuses heavily on aesthetic plastic parts.

Toys
From model assembly parts to dolls to board game pieces, injection molding offers the versatility and precision needed for mass-produced toys. Toys can replicate intricate product designs impossible with most other manufacturing techniques.
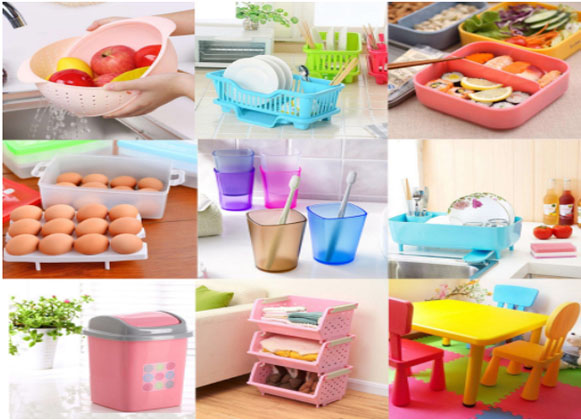
Household Items
Everyday plastic products use injection molding including storage containers, kitchenware, fans, vacuum components, organizers, home appliances and laundry accessories.
The Plastic Injection Molding Process
There are mainly 5 processes of plastic injection molding.
Step 1- Clamping Process: The pressure oil in the clamping cylinder pushes the clamping mechanism, and the moving template moves to close the mold.
Step 2 – Injection Molding: After the mold is locked with the clamping force during the injection molding process, the injection device enters the working condition to make the nozzle and the mold fit.
Step 3-Pressure Holding: during the process of filling the mold cavity, the screw is required to maintain a certain pressure on the thermoplastic material to prevent it in the mold from flowing back.
Step 4—Cooling: Once the gate is sealed, the pressure-holding process is canceled, and the plastic-molded product is naturally cooled in the mold to shape.
Step 5—Mold Opening and Plastic Product Demolding: To prevent the nozzle from forming cold material due to long-term contact with the cold mold, it is usually necessary to remove the nozzle. Then, evacuate the mold, and the molded plastic parts are demolded.
Types of Injection Molding That Baiwe Can Do
Gas assisted injection moulding
The gas-assisted injection molding system injects inert gas (usually nitrogen) into the plastic in the mold cavity. This makes the plastic expand and form a hollow part while keeping the surface intact.
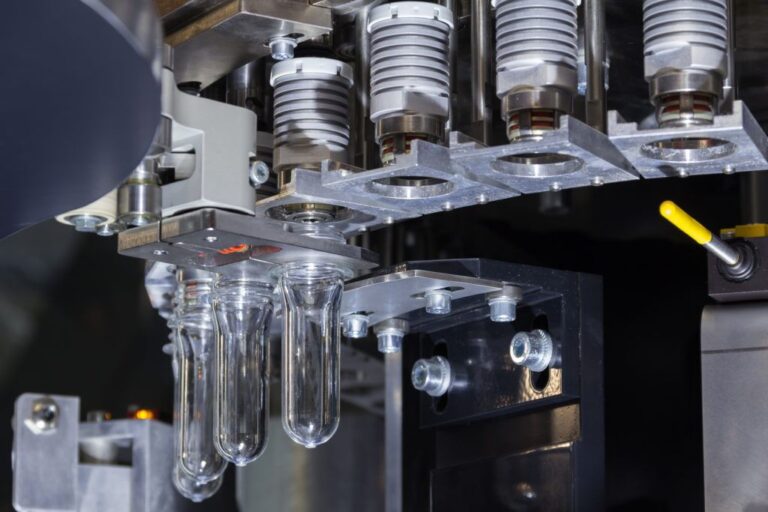
Liquid silicone rubber injection molding
Baiwe can make silicone rubber parts using LSR injection molding. These include industrial products like O-rings and buttons and consumer products like pacifiers.
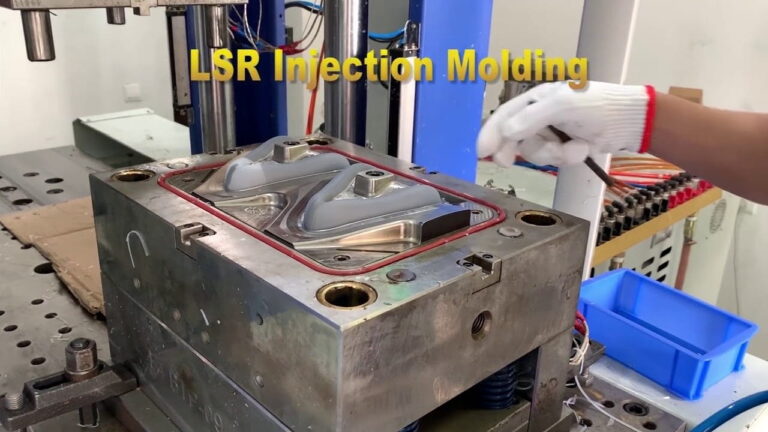
Overmolding
Overmolding is two-component 2K injection molding. It’s done on a two-color injection molding machine. One material is injected into the other part, and then the mold jumps to the mold cavity corresponding to another injection plastic cylinder. Injection molding is another material to make a finished product. Silicone can be over-molded on plastic or metal.
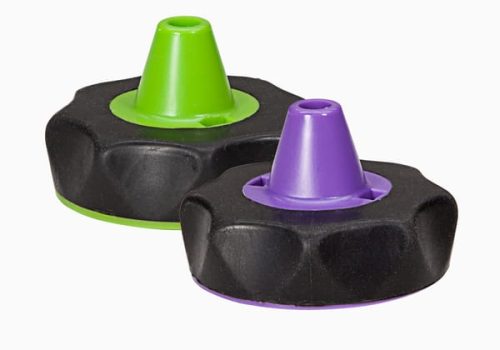
Thin wall injection molding
Smaller, lighter parts require custom injection molding. Thin-wall injection molding is plastic parts with a wall thickness of less than 1mm. Thinner walls mean different machining requirements, including higher pressures, faster cooling, and better mold designs. Baiwe can make thin-wall injection molds.
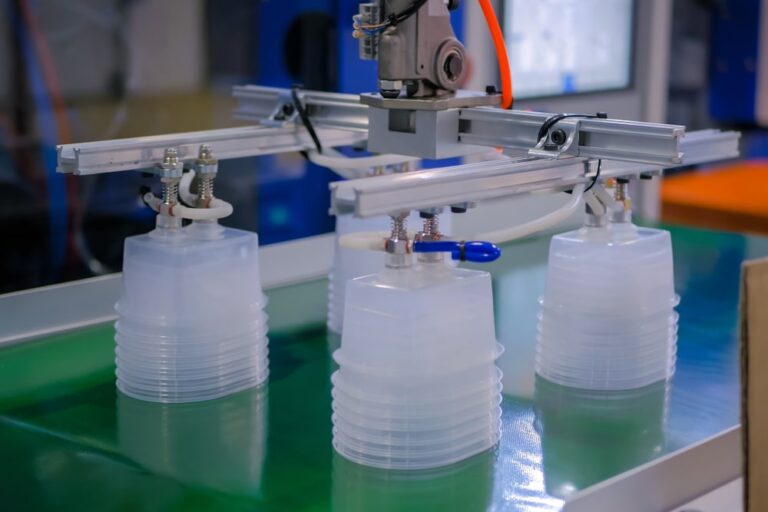
What Plastic is Used for Injection Moulding?
ABS-Acrylonitrile Butadiene Styrene
ABS is a plastic used for structures. It is a polymer made from acrylonitrile and butadiene. It is also called ABS. ABS is used in many products because it is heat—and impact-resistant and can be processed easily. Baiwe can make ABS parts using injection molding.
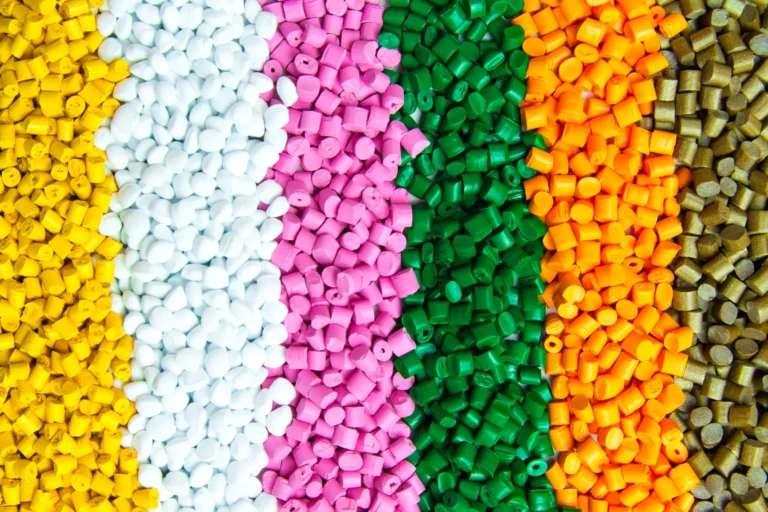
PE – Polyethylene
Polyethylene is odorless, non-toxic, and resistant to most acids and alkalis. It doesn’t dissolve in common solvents at room temperature. It absorbs little water and insulates well. Baiwe is a good choice for PE injection molding.
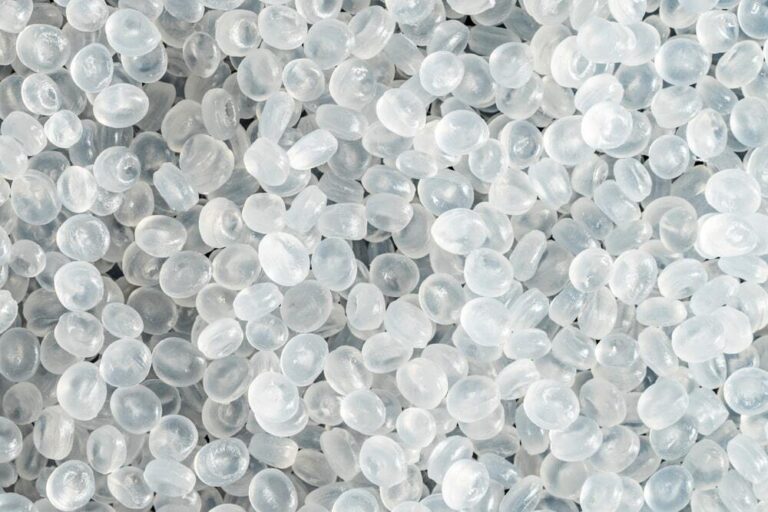
PC – Polycarbonate
PC is strong, flexible, and can be used in a wide range of temperatures. It is transparent, can be dyed, and has good stability. PC injection molding is used in many industries.
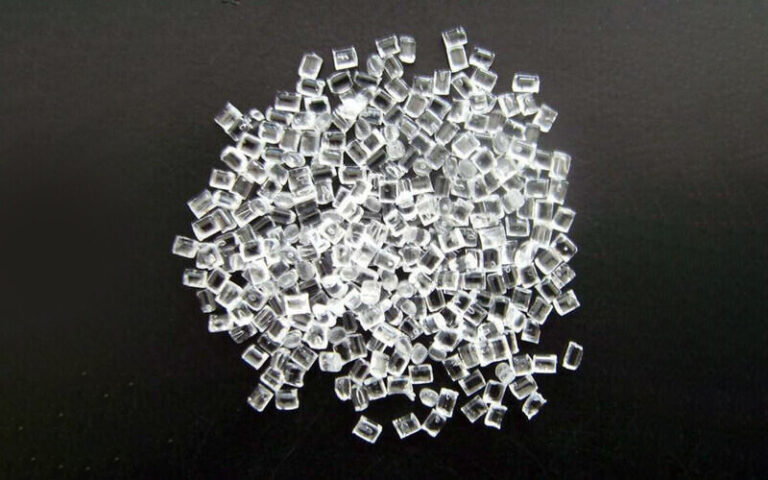
PVC – PolyVinyl Chloride
PVC is strong and tough, so it doesn’t tear or break easily. The new material is stronger than HDPE, but thinner and cheaper to make. Baiwe has provided PVC injection molding for over 10 years.
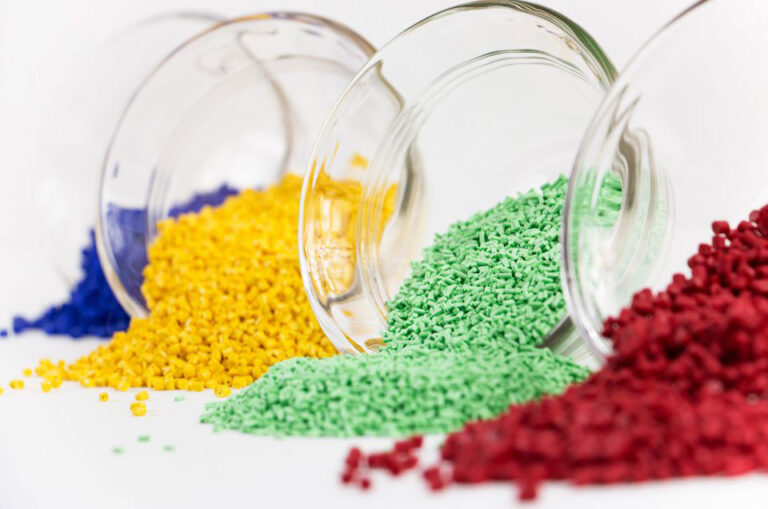
PP – Polypropylene
PP is strong and has a regular structure. It has poor impact strength at room temperature and low temperature because its molecules are so regular. PP is resistant to bending. China is the top exporter of PP injection molding.
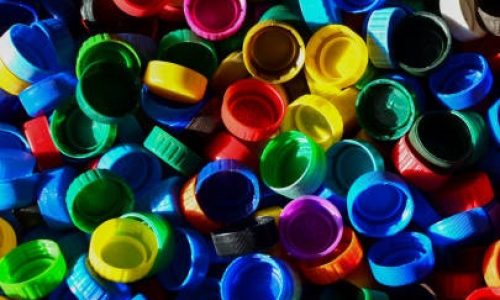
PEEK Material
Peek is a special engineering plastic with excellent properties. It can be manufactured and processed into various mechanical parts. Not all injection molders can make PEEK in China. Baiwe has done many PEEK projects.
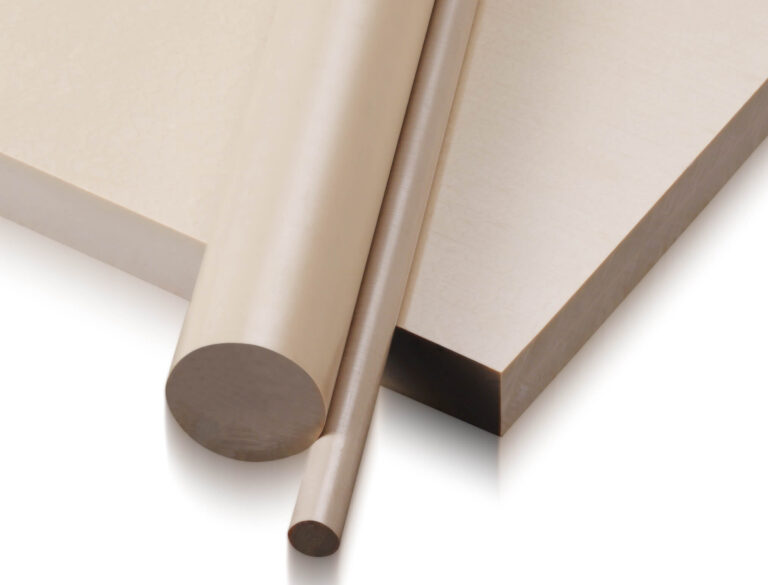
TPU – Thermoplastic Polyurethanes
TPU is hard, strong, and resistant to cold. It is easy to process. TPU also has disadvantages, such as poor formability and hydrolysis resistance. This article helps you learn more about TPU injection molding.
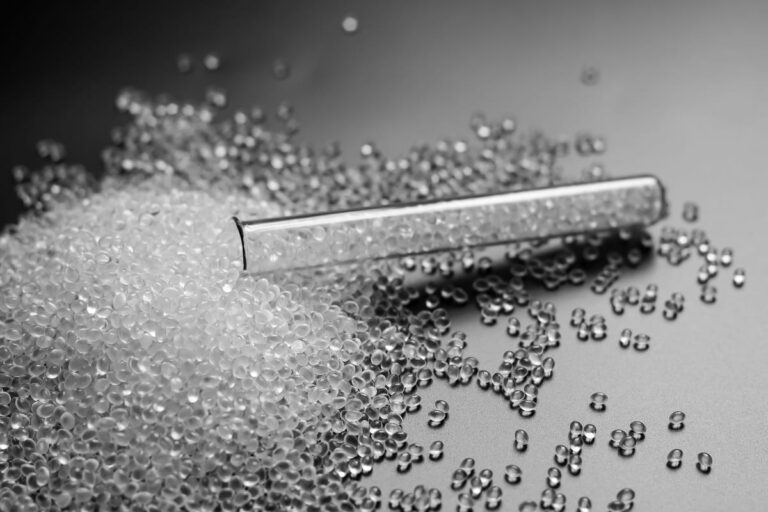
Why Choose Us as Injection Moulding Supplier
Exceptional Quality Control
We implement strict quality checks at every stage of production to ensure that each product meets the highest standards.
Advanced Manufacturing Technology
Our facilities are equipped with cutting-edge machinery and technology, enabling us to handle complex and high-precision injection molding projects.
Custom Solutions Tailored to Your Needs
We specialize in customized plastic injection solutions, creating unique products that align with your specific requirements and design.
Competitive Pricing and Timely Delivery
We offer competitive rates without compromising on quality, and our efficient processes ensure that projects are completed on time, every time.
China Plastic Injection Molding Cost
The core and cavity die steel is important. Steel prices vary by region. The more cavities, the more expensive. The price of the runner design also affects the cost.
A simple single-cavity injection mold can cost a few thousand dollars. A large, complex, high-production, multi-cavity mold can cost $10,000–$100,000+.
We can make low-cost plastic injection molds if you have a tight budget.
Other Plastic Injection Molding Companies Recommend
Many companies worldwide make plastic injection molds. It’s hard to choose. These companies are mainly in China and the US. If you need to compare USA and Chinese injection molding manufacturers, click this article to help you make a better decision.
Baiwe is one of China’s best plastic injection molding suppliers. We offer fast, short-run molding with professional service.
If you need to find other cheap plastic molders in China, we list the top 10 plastic injection molding manufacturers in China. I hope it helps.
FAQs About Injection Moulding
Plastic injection molding is a manufacturing process that involves melting plastic material, injecting it into a metal mold, and then allowing it to cool and solidify into a specific shape. This technique is widely used for producing a large volume of identical plastic parts and components due to its efficiency and cost-effectiveness.
Injection molding is a widely used manufacturing process for producing a large volume of plastic parts and products. It involves several key steps:
Melting the Plastic: Plastic resin, typically in the form of pellets, is fed into a hopper and then into a heated barrel where it is melted through friction and external heating.
Injection: The molten plastic is then forced under high pressure by a plunger or screw-type mechanism into a cooled metal mold. This mold is designed to have the negative shape of the final part, meaning that when the plastic cools and solidifies, it takes on the mold’s shape.
Cooling and Solidification: Inside the mold, the plastic cools and hardens to the configuration of the mold cavity. The cooling time depends on the size and complexity of the part, as well as the type of plastic used.
Ejection: Once the plastic has cooled and solidified, the mold opens, and the part is ejected using mechanical or air ejection systems. The cycle then repeats for the next part.
This process is highly versatile and can produce parts with intricate designs and from a wide range of thermoplastic materials. Polypropylene (PP) is a commonly used plastic in injection molding, representing a significant portion of global plastic production.
Plastic injection molding is a sophisticated manufacturing process that combines technical expertise with precise machinery to produce high-quality plastic parts. While it is not inherently simple, its complexity depends on various factors such as design intricacy, material selection, and process control.
Injection molding is a versatile manufacturing process that employs a range of plastic materials, each with unique properties suited for different applications. Here are some common plastics used in injection molding:
Acrylonitrile Butadiene Styrene (ABS): Known for its toughness, dimensional stability, and ability to be easily molded, ABS is widely used in products like electronics casings, toys, and automotive parts.
Polyethylene (PE): With its low cost, lightweight, and chemical resistance, PE is suitable for various applications, including packaging, containers, and simple household items.
Polypropylene (PP): Durable and heat resistant, PP is used in products requiring flexibility, such as bottle caps, straws, and automotive components.
Polycarbonate (PC): Known for its high impact resistance and transparency, PC is ideal for lenses, safety glasses, and electronic housings.
Polyethylene Terephthalate (PET): Often used for single-use beverage bottles due to its clarity and recyclability.
Polyvinyl Chloride (PVC): PVC is used where rigidity and chemical resistance are needed, such as pipes, window frames, and some packaging.
Nylon (Polyamide, PA): Strong and abrasion-resistant, nylon is used in mechanical parts, textiles, and sports equipment.
Thermoplastic Elastomers (TPEs): Offering rubber-like flexibility combined with plastic processing, TPEs are used in handles, grips, and soft-touch parts.
Acetal (Polyoxymethylene, POM): Known for its high strength, low friction, and wear resistance, it’s used in precision parts like gears and bearings.
Polystyrene (PS): A common choice for its clarity and low cost, used in disposable cutlery, CD cases, and packaging.
These materials are chosen based on factors such as durability, cost, temperature resistance, and the specific requirements of the final product. The selection process also considers the molding process itself, including the ability of the plastic to flow into the mold cavities and its behavior during cooling.
Injection molding costs can be between $100 and $100,000+. A small, simple plastic injection mold costs between $1,000 and $5,000. Large or complex molds may cost up to $80,000.
Selecting the “best” plastic for injection molding depends on the specific application and requirements of the product. However, Polypropylene (PP) is often considered a top choice due to its versatility and widespread use.
Contact Us for a Quote
Let us help you achieve your manufacturing goals efficiently and effectively.