Plastic leaking from the parting line is one of the most common issues in injection molding. This plastic flashing can seriously impact part quality and functionality. Fortunately, there are several effective strategies to prevent leaks along the parting line. In this comprehensive guide, as a professional plastic injection molding manufacturer, you’ll discover 8 proven ways to stop plastic from escaping your molds.
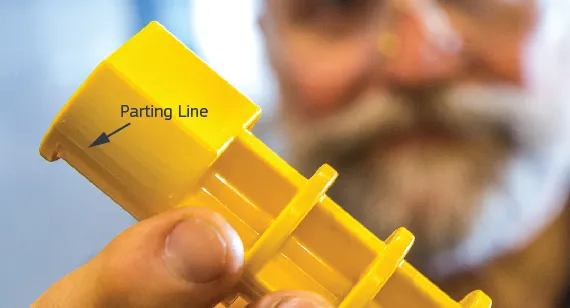
Why Plastic Leaks from Parting Lines
Before we get into solutions, it’s helpful to understand what causes plastic to leak along parting lines during injection molding.
The parting line is where the two halves of an injection mold meet and seal shut. When the mold closes, tons of clamping force pushes the halves together to prevent material from escaping.
However, sometimes molten plastic still squeaks through small gaps along the seam:
Contamination
Dust, oil, plastic shavings or other debris stuck in the parting line prevents the two mold surfaces from properly mating when closed. This tiny gap then allows flashing to occur.
Mold Wear
Over thousands of cycles, the contact area along parting line faces gradually wear. These micro imperfections eventually allow material to escape, resulting in flash.
Improper Venting
Trapped gases have no way to escape the cavity when vents or vents channels are clogged. The excessive internal pressure then forces plastic out through the parting line.
Excessive Injection Pressure
If injection pressure exceeds the available clamp force, the mold halves can be forced apart. Plastic then fills these newly opened gaps, causing flash.
And that’s just the tip of the iceberg. Warpage, deflection or core shifts can also create leak paths along parting lines.
But the good news? There are several proven ways to combat plastic leakage, as we’ll explore in the next sections.
How to Prevent Plastic Leaking From Parting Line Injection Molding
Clean & Maintain Parting Line Surfaces
Keep things neat and tidy. That’s Molding 101.
After all, tiny particles in the parting line region prevent the mold halves from fully closing. And even microscopic gaps can cause leaks, material shearing and other issues.
That’s why regular parting line cleaning is a must:
- Use compressed air to blow out loose contaminants
- Carefully scrape plastic shavings and buildup
- Apply mold cleaner and gently wipe down faces
While you’re in there cleaning, closely inspect for any signs of wear. Even minor imperfections that seem harmless can degrade sealing performance over time.
Keep things extra pristine around vent ports and ejector pin holes where debris easily collects unnoticed.
Pro tip: Schedule cleanings based on cycles, not hours or days. Certain materials generate more buildup than others.
Perform Regular Maintenance & Inspections
Dirty molds aren’t the only culprit behind plastic flashing. Improperly aligned cores, worn components and ill-fitting mold inserts can also introduce leak paths.
That’s why comprehensive mold inspections should complement routine cleanings.
Here’s a general checklist to guide your maintenance protocol:
- Verify dimensions of mold components haven’t drifted from original specifications
- Inspect overall parting line contact using pressure indicating films
- Closely examine vent ports, ejector pins and slides for signs of wear
- Ensure uniform contact between guide pillars and bushing surfaces
- Check for uneven grease or oil distribution in cooling lines
If everything checks out, you know for certain that any new flashing issues result from factors beyond basic tooling health.
Establish a structured calendar for inspections based on cycles or operating hours. Increase frequencies for molds seeing the most action.
Apply High-Quality Mold Finishes
When two perfectly flat surfaces meet under pressure, just a few particles in between can reduce contact significantly.
Now imagine if those meeting faces weren’t so smooth and planar. Uneven rough peaks unable to fill microscopic valleys result in leak-inducing micro gaps.
That’s why the finish quality on parting line regions plays a major role. Smoother surfaces increase contact area when mated. And tighter contact equals better sealing.
Most injection molders specify surface finishes of at least Rz5 microns. While a good baseline, going down to Rz1-3 microns provides a noticeable seal-ability boost for only a moderate upcharge.
Keep super fine finishes isolated just to parting line zones to minimize cost. This focused approach reduces surface prep work while maximizing capability where needed most.
Design for Proper Venting
Escaping gases generate tremendous pressure inside mold cavities. And this trapped air really wants to vent.
Without a clear exit path, pressurized gases end up creating new ones: by forcing the mold open at the parting line.
Ensuring adequate venting helps avoid leaks in two ways:
- Lowers cavity pressure during filling
- Reduces clamp requirements
Careful vent placement and sufficient cross-section do the trick. Position vents at the end of fill patterns in slower packing regions.
Adequate size also prevents clogs from minor flashing. As a general rule, opt for vent depths approximately 70% of wall thickness. And for widths, stick to around 5 times wall thickness.
Vent channels seamlessly integrate with water flow loops without disrupting cooling. Strategically placed vents balance performance with mold complexity.
Apply Sufficient Clamping Force
In a battle between injection pressure and clamp force, plastic flows seeking the path of least resistance.
And when clamping force loses, those flow paths end up going right through the mold’s parting line. Excess material then solidifies, leaving tell-tale flashing behind.
Ensuring adequate clamp force requires calculating totals pressures. Then specifying sufficient clamp tonnage to resist escape.
For example, pressures from injection filling, packing, material decomposition and other sources often exceed 5,000 psi. Total forces trying to open the mold quickly add up.
A good rule of thumb is to allow for at least 1.5 times the projected cavity pressure. And no less than 3 tons per square inch along the parting line.
Clamp capability limits part size more than anything else. Getting creative with fundamentals like minimizing projected area reduces high costs associated with advanced hydraulics.
Lower Peak Injection Pressures
Specifying enough clamp force provides plenty of resistance against escaping plastic flow.
But excessively high injection pressures overloaded even the most robust clamps. Creating leaks. Short shots. Flashing. And other defects.
Careful process tuning helps avoid pressure spikes while ensuring complete cavity filling.
Start by choosing resins with melt flow indexes best matching your application. Thermoplastic viscosities directly impact resulting injection pressures.
Helical flow channels then encourage gradual filling absent problematic fountain flow impingement sites.
Switching from cold to insulated or heated manifolds practically eliminates sluggish melt delivery causing short shot part defects.
And optimizing slow injection speeds followed by high pack and hold stages promote cavity packing at the lowest pressures.
It all comes down precise control. Monitoring sensors providing PID feedback automatically implement tuning tweaks maximizing quality.
Invest In Flash-Free Tooling
Ask any molder what the surefire route is to absolutely preventing flash and they’ll all say the same thing:
Go flash-free.
While ultra-high precision tooling costs substantially more upfront, some applications justify the serious capital investment long-term via radically improved performance.
We’re talking tolerances under 0.005” maintained across mold bases. Sub-micron finishes on parting line zones. Guided components eliminating shifts entirely.
Flash-free molds even incorporate multi-stage venting handling high degassing loads while preventing leaks both large and microscopic.
For mission-critical molding applications where perfection is the only option, flash-free tooling delivers as promised when configured properly. Just be prepared to pay premium dollar in exchange for unparalleled capability.
Carefully Control Processing Conditions
Dialing in process set points falls squarely on the molding technician’s shoulders. But small overcorrections attempting to compensate for suspected fluctuations cause more harm than good.
Pressure. Temperature. Speed. They all demand judicious fine-tuning balancing competing needs. Knowing which knobs to turn and when is crucial.
As covered earlier, lowering viscosities reduces pressures. But take things too far and material easily flashes small gaps. Or burns, degrading mechanical performance.
Likewise, minor leaks seemingly justify boosting pack and hold times. But extended durations unnecessarily introduce orientation stresses down the road.
Rely on data, not gut intuition directing next steps. Sensors indicating thresholds automatically trigger set point tweaks through machine interfaces. Quick testing then verifies effects on objective quality metrics.
Staying firmly rooted in fundamentals keeps processes operating smoothly regardless of job function. Stepping back assesses wider ecosystems connecting decisions to results. Cohesive understanding aligns efforts optimizing outcomes across departments.
How To Remove Existing Flash
Despite best efforts, sometimes plastic flashing still makes an appearance. Fortunately, several efficient methods exist for removing flash after parts eject.
Hand trimming with blades or files works great for prototypes and short runs. It’s slow, yet ensures minimum material removal from critical dimensions. Unique fixture designs aid positioning for tricky locations.
Abrasive media like sand injected into vibratory bowls makes fast work of high volume flash removal. Parts screen media ensuring appropriate particle sizes target just flash without compromising component integrity through unintended general thinning. Though inexpensive systems scale easily, safety shields are definitely a must for operators.
For tricky materials like PEEK and silicone, cryogenic deflashing has really taken off recently. Parts are dunked in liquid nitrogen, selectively embrittling just the thin flashing portions. Vibration easily detaches the now brittle bits absent damaging the still-ductile plastic underneath. It’s surprisingly inexpensive given the exotic process while generating zero secondary waste requiring disposal.
Conclusion
Leaking plastic may be common, but it’s certainly not unavoidable. Applying the guidelines outlined here goes a long way toward preventing parting line flashing in even the most demanding applications.
The first step inspects root causes behind leaks to begin with. Addressing contamination or wear at this early stage significantly extends overall mold service life.
Proactive maintenance paired with minor tooling adjustments then ensures leaking issues don’t return after fixing things initially. Precision machining focused on sealing surfaces combined with sufficient venting lowers chances for plastic to escape cavities under pressure.
And for the toughest jobs where zero flashing is the only option, high end flash-free tooling delivers as promised. Though expensive, unparalleled performance results may justify upfront capital investment for certain programs.
In the end, sticking to fundamentals generally wins the battle against flashing most of the time. But when all else fails, several efficient flash removal techniques quickly restore parts back up to spec.
Now you’re equipped with a complete game plan tackling plastic leaks at the source. Leveraging these guidelines significantly reduces pesky flashing’s impact on manufacturing operations. The improved quality and throughput benefits dramatic bottom line results.