Polyvinyl chloride (PVC) is one of the most versatile and widely used thermoplastics for injection molding applications. Getting the PVC injection molding temperature right is critical for producing high-quality parts efficiently.
In this complete guide, as a professional plastic injection molding manufacturer, I will talk about:
- What is PVC and why temperature control matters
- PVC melting points and optimal injection molding temperatures
- How heating zones, mold temperature and cycle time impact part quality
- Advanced temperature control methods
- Tips for setting process parameters
Properly controlling PVC injection molding temperatures leads to faster cycles, less scrap, and lower production costs. Keep reading to boost your PVC molding expertise!
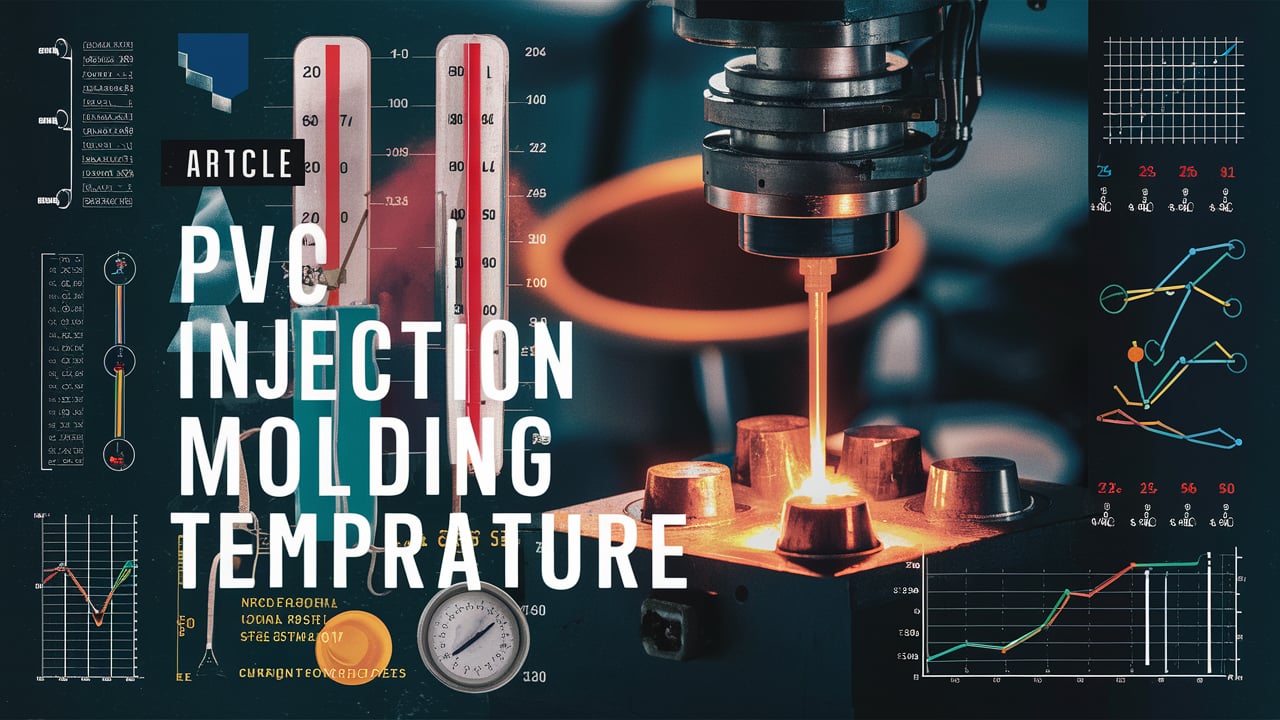
What is PVC?
Polyvinyl chloride or PVC is a thermoplastic polymer frequently injection molded to create pipes, medical devices, and construction materials. The PVC molecule contains chlorine which makes the material naturally white. But colorants are often added to produce parts in any hue.
PVC comes in rigid and flexible grades. Flexible PVC contains plasticizers that give it added bend and stretch. Rigid PVC offers high stiffness and strength along with thermal and chemical resistance. Advanced injection molding processes like gas-assisted molding produce hollow parts that are both rigid and lightweight.
The trouble with PVC is – it releases corrosive hydrochloric acid when overheated! That’s why tight PVC injection molding temperature control is mandatory. Keep reading to learn how to tame this temperamental plastic.
Why Temperature Matters in PVC Injection Molding
PVC begins decomposing into hydrochloric acid (HCl) above 300°F-350°F. The acidic vapor corrodes mold steel and can appear as black specks on freshly molded parts. HCl also promotes further degradation.
To prevent this vicious cycle, PVC injection molding machinery must maintain precise heating zone control and rapid cycle times. The injection mold temperature should also be kept low to minimize HCl outgassing as parts solidify.
Finding the Sweet Spot – Optimal PVC Melting Points
Unlike metals, plastics soften over a temperature range instead of at a defined melting point. The peak of this range – where the material flows best – depends on the specific PVC formulation.
PVC injection molding temperatures typically fall between 350°F-450°F. But specialized medical-grade and chemical-resistant PVC compounds may require much hotter plasticating temperatures exceeding 500°F.
Consult manufacturer datasheets to pin down optimal melting points and viscosities. These represent the “sweet spot” where PVC melts completely without degrading.
Balancing Heating Zones
On an injection molding machine, a reciprocating screw turns inside the heating barrel to melt granulated PVC resin. The barrel contains separate temperature control zones that should follow a “profile” suited to the material.
Due to its poor thermal stability, PVC processing benefits from gradual heat input. Set the initial feed zone to attract and preheat material as it enters the barrel.
Next, rapidly bring PVC up to melting temperature in the transition zone. Avoid overshooting the optimal melting point here.
Finally, the front end holds the hottest temperatures to reduce viscosity before injection. Dropping just 10°F-20°F at the nozzle can prevent degraded material leaking out.
PVC injection molding temperature profiling requires an experienced molding technician to get right! Modern electric machines with auto tuning capability make the job much easier.
Why Mold Temperature Matters Too
Once PVC fills the injection mold cavity, it starts losing heat to the surrounding tool steel. Set the mold surface temperature low – between 50°F-150°F to promote rapid cooling.
Chilled molds also discourage gas bubbles from forming as material solidifies. Testing indicates that dimensional stability and replication of mold details significantly improve with lower mold temperatures.
However, dropping below 50°F risks permanent thermal shock distortion of PVC parts. Certain engineering resins like PEEK thermoplastic require molds heated to over 300°F!
Shorter Cycle Times = Better Quality
To minimize PVC degradation during processing, use the shortest injection cycle time possible while completely filling parts.
With fast cycles, freshly melted material enters the cavity before the previous shot has completely hardened. This “cushions” the hot resin, protecting delicate features from damage.
Automotive lens manufacturer Magna International combines thin-wall PVC molding with 15-20 second cycle times. Their process optimization focuses on preventing stress cracking and visual defects.
For commodity items like PVC pipes produced 24/7, injection molding machinery may cycle every few seconds! Photosynth technology ensures mold cavities fill uniformly regardless of position.
Advanced Temperature Control Methods
Basic strategies like profiled barrel heating and rapid cycles take you 90% of the way towards optimized PVC injection molding temperature management. But modern techniques like these take you even further:
1. Hot Runner Molds
Hot runner tooling contains heated manifold channels that keep PVC fluid right up to the gate area. This technology is perfect for molding small, detailed parts not suitable for cold runners.
By preventing material freeze off, hot runners enable very fast cycle times under 15 seconds. Cleaner gate vestiges also minimize secondary finishing operations.
2. Rapid Heat/Cool Molding
Rapid Heat Cycle (RHC) injection alternates thermally aggressive and gentle phases to obtain complete fills without overpacking. The mold temperature itself rapidly cycles between hot and cold settings.
Combining variotherm molding with thinner cavities permits 30% faster cycles. And rather than waiting during cooling, another shot preps to enter the mold immediately after part ejection!
3. Scientific Molding Methods
Through systematic measurement of temperatures, pressures and plastic behavior, Scientific Molding procedures optimize processing windows. This minimizes trial and error when working with difficult resins like PVC.
Scientific molding relies on instrumentation like cavity pressure transducers. But simpler thermocouples that monitor melt temp during fill can still provide useful data to perfect process settings.
Conclusion – Take Charge of PVC Injection Molding Temps!
This guide toured key PVC injection molding temperature considerations starting from fundamental material properties through advanced process control methods. Applying even a few of the tips above will directly enhance part quality.
The unpredictability of PVC makes maintaining discipline around temperature and cycle settings imperative. But the extra effort invested pays back over years of low-scrap production of flawless injection molded components!