Flow marks are a common defect in injection molded plastic parts, showing up as wavy lines or patterns on the surface. While usually not detrimental to the part’s structural integrity, they negatively impact the aesthetics and can render parts unusable for applications where appearance is critical.
Reducing flow marks requires adjustments to process parameters and often some trial and error. However, with persistence and attention to detail, their occurrence can be decreased significantly or even eliminated. As a professional plastic injection molding manufacturer, I will cover the root causes of flow marks and proven methods for reducing them in this guide.
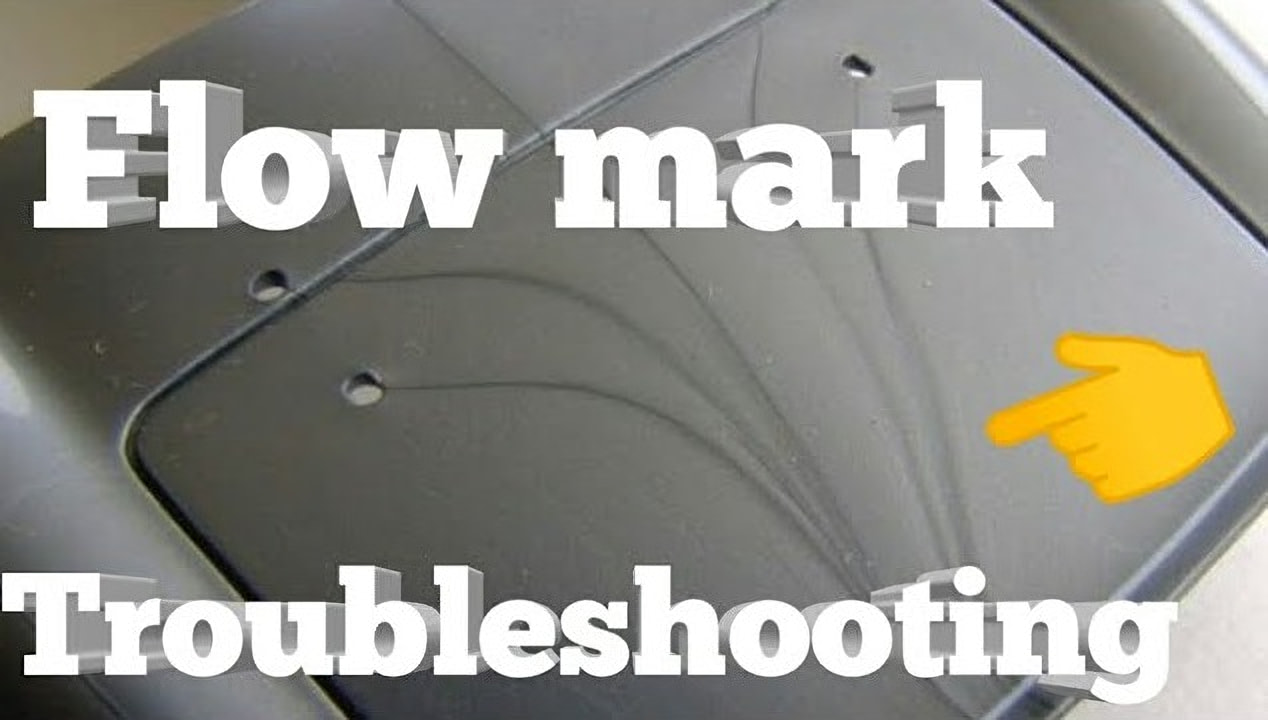
What Causes Flow Marks in Injection Molded Parts
Flow marks occur when the molten plastic solidifies at uneven rates as it flows into the mold cavity. The main culprit is non-uniform cooling caused by:
Insufficient Injection Pressure or Speed
If the injection pressure or speed is too low, sections of the melt may prematurely cool as the material flows slowly into the mold. Hotter, faster-moving material then flows over these partially solidified areas, resulting in visible flow lines.
Improper Gate, Runner or Nozzle Sizing
If the gate, runners or nozzle have openings that are too narrow, restriction in material flow can allow portions of the melt to cool early while other areas are still filling the mold.
Thickness Variations in the Part Geometry
Areas with thicker cross-sections take longer to fill and solidify than thinner sections. The prolonged cooling in thick areas combined with faster cooling in thin spots leads to flow marks at the transition.
Low Mold Temperature
A mold that is too cold can cause the hot plastic to cool and harden almost immediately upon injection. The frozen layer prevents smooth flow, allowing subsequent shots of material to leave flow lines on the surface.
Material Related Factors
Thermoplastics with higher melt flow indexes, which indicate ease of flow in the molten state, are less prone to flow marks. However, all materials have optimal molding process windows. Conditions straying outside those parameters tend to cause flow issues.
How to Reduce Flow Marks in Injection Molded Parts
Eliminating flow marks requires attention to material selection, machine process settings, and mold design factors. Strategically adjusting these injection molding variables can prevent uneven filling and cooling in the cavity.
Choosing the Right Material
- Select a thermoplastic grade with higher melt flow index within acceptable property ranges
- Use manufacturer’s recommendations for optimal molding process conditions
- Avoid highly filled or reinforced grades as they flow poorly compared to neat resin
Dialing in Process Settings
- Increase injection speed and pressure for faster mold cavity filling
- Ensure nozzle, barrel and mold temperatures are within material guidelines
- Allow adequate cooling time for part thickness to prevent early ejection
Improving Mold Design Elements
- Widen gate, runner and nozzle diameters to prevent flow restrictions
- Round sharp corners in part geometry to enable smoother flow fronts
- Eliminate drastic changes in wall thickness whenever possible
- Optimize vent placement to allow trapped gases to escape
It often requires testing, inspection and adjustment to mold design and process parameters to minimize flow marks. But the effort pays dividends in higher quality, less scrap and the ability to mold intricate geometries.
Careful mold and machine qualification combined with a watchful eye can significantly reduce flow defects. And further process control via sensor feedback allows adjustments before flaws even develop.
Implementing scientific molding principles provides the understanding needed to not just treat the symptoms of flow marks, but address root causes for complete prevention. This reduces troubleshooting time, lowers manufacturing costs and delivers more robust, capable injection molding processes.
Step-by-Step Guide to Eliminating Flow Marks
Preventing flow marks in injection molding requires a strategic approach focused on materials, process settings and tooling factors. Follow these steps to methodically address what causes uneven filling and cooling:
Step 1: Review Part Design
Critically evaluate part geometry before mold fabrication:
- Are there drastic changes in wall thickness? Can these transitions be smoothed out?
- Do ribs, bosses and attachments enable smooth flow paths?
- Can shape complexity be reduced while retaining function?
Simpler, more uniform part layouts prevent many downstream defects.
Step 2: Select Proper Material
Choose a thermoplastic that fits application requirements yet optimizes moldability:
- Favor higher melt flow index grades with suitable strength, temperature resistance, etc.
- Start with neat rather than filled/reinforced resins
- Adhere to manufacturer recommendations for molding process conditions
Step 3: Adjust Injection Machine Settings
Methodically change temperature, pressure and speed parameters while inspecting for improvements:
- Raise temperatures within material guidelines to improve melt flow
- Increase injection speed and pressure for faster cavity filling
- Ensure adequate cooling time based on part thickness
Document the parameter adjustments that reduce flow defects.
Step 4: Refine Mold Design
Alter tooling features to fix persistent filling and cooling issues:
- Widen runner diameters to prevent restrictions impeding flow
- Relocate/add vents so trapped gases freely escape
- Round sharp corners that alter flow front direction
- Adjust cooling circuits to prevent early freezing in problematic areas
Step 5: Implement Advanced Flow Monitoring
Sensor-driven process adjustments prevent flaws before they occur:
- Cavity pressure sensors detect flow restrictions
- Thermal imaging pinpoints uneven cooling
- closed-loop controllers self-correct deviations automatically
Taking these proactive steps isolates what factors contribute to flow marks in a given molding setup. Addressing each one builds quality into the process instead of chasing sporadic defects. And advanced flow monitoring takes precautions further by self-optimizing parameters before flaws arise.
While rarely straightforward, flow mark prevention delivers outsized benefits compared to remedies further downstream. And the knowledge gained troubleshooting these defects leads to robust processes capable of flaw-free production of intricate plastic components.
Frequently Asked Questions
Can flow marks be completely eliminated in injection molding?
With sufficient attention to material selection, machine settings and mold design factors, flow marks can be reduced significantly or even prevented entirely in most cases. However, most processes still encounter occasional flow defects. Advanced flow monitoring and closed loop control provides the best protection against intermittent issues cropping up.
How do flow marks affect performance of injection molded plastic parts?
In most instances, flow marks are a purely cosmetic issue impacting only aesthetics and do not alter mechanical performance. However, in rare cases involving optical clarity requirements or precision dimensions, the surface rippling may render parts unusable if severity exceeds specifications. Generally flow marks should not be accepted as normal, but preventative measures can usually bring their occurrence well within acceptable tolerances.
How can mold flow analysis software help reduce flow marks?
Flow simulation programs can accurately predict locations in mold geometries prone to uneven filling, premature freezing and related defects. Detailed mold filling and cooling visualizations allow designers to spot and address problem areas in the plastic part tooling before ever cutting steel. Virtual insights drive design revisions and process changes preventing flaws like flow marks.
In Summary
Eliminating flow marks in injection molding improves quality, reduces scrap and prevents customer returns. And the effort invested pays dividends in developing robust processes capable of producing flaw-free, high precision plastic components able to meet strict modern demands.