Injection molding can be an extremely cost-effective way to manufacture large quantities of plastic parts, but the high tooling costs often associated with large part injection molding can make it prohibitively expensive. As a professional large part injection molding manufacturer, I wanted to share some insider tips on how manufacturers can reduce the costs of large part injection molding without sacrificing quality or production capacity.
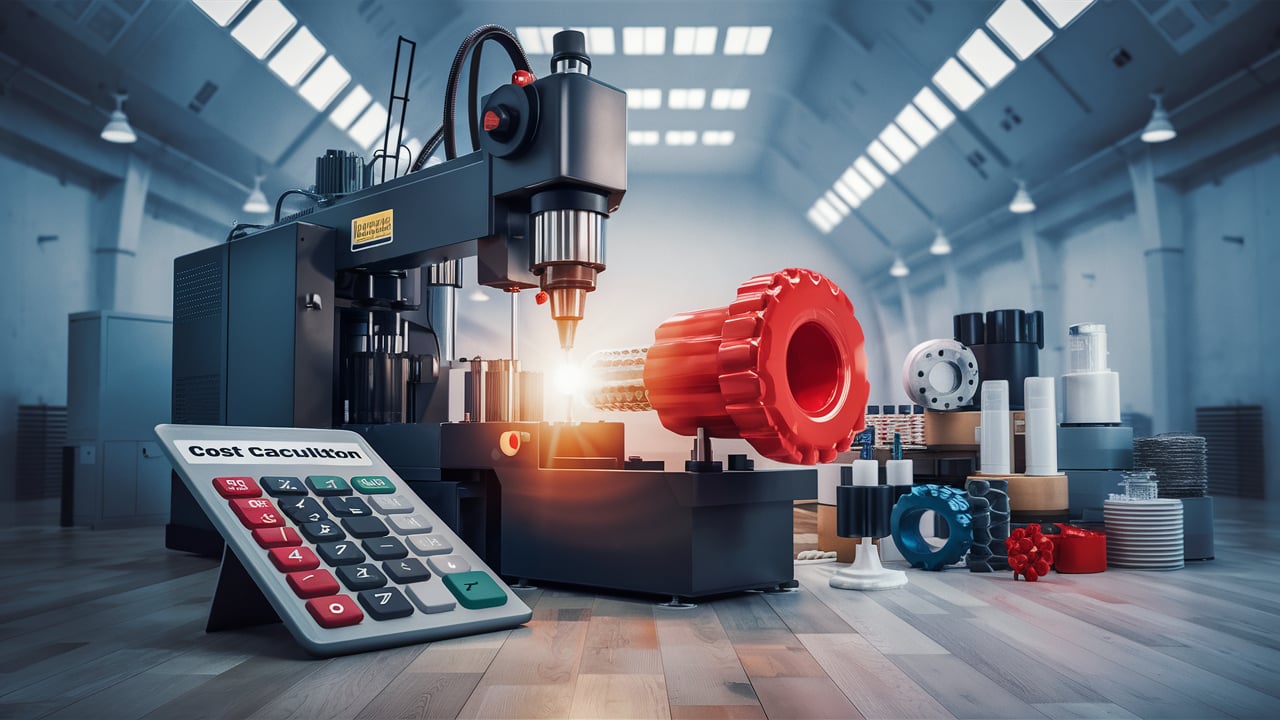
Why Large Part Injection Molding Tends to Cost More
There are a few key reasons why large part injection molding often incurs higher costs compared to small part production:
- Larger machines: Large parts need bigger injection molding machines to accommodate their size and weight. These industrial-scale machines have higher capital, operating, and maintenance costs.
- Increased cycle times: It takes longer for the molten plastic to fill larger, deeper molds, lengthening cooling times. Longer cycle times mean higher operating costs and lower hourly production.
- Heavy-duty tooling: Large injection molds require heavy-duty tooling constructed from hardened steel to withstand the prolonged production runs and avoid premature wear. The machining and material costs are consequently higher.
- More plastic resin: Larger cavities obviously demand more raw plastic to fill them up. The sheer material quantity leads to higher per part plastic costs.
So how exactly can a manufacturer negate these big-part penalties? Here are my tips.
How to Reduce the Cost of Large Part Injection Molding
Carefully Evaluate Part Design
As with most manufacturing methods, the part design hugely impacts the molding costs. Simple, streamlined shapes use less material and minimize cycle times. Consolidate multiple small components into single large parts whenever feasible.
Ribs and gussets provide strength and rigidity while enabling thinner walls and less plastic usage. Flow and cooling simulations will reveal any design flaws upfront. Don’t underestimate the cost benefits of design-for-manufacturing (DFM) analysis.
Use Aluminum Mold Bases
Aluminum makes excellent large mold bases given its strength-to-weight ratio. The material costs and machining is cheaper for aluminum versus steel. Repairs and modifications are simpler too. Aluminum’s lower melting point shortens cooling times as an additional cost saving.
I’d recommend aluminum molds for shorter production runs up to about 10,000 cycles. For higher quantities, steel molds offer longer working lifespans and use specialized coatings to accelerate cooling. Discuss options with your chosen injection molder to determine the optimal mold material for your application.
Employ Faster Plastic Resins
Faster molding resin chemistries have been developed that drastically cut cooling times. For example, the Catamold motion series from BASF contain special catalysts enabling up to 35% faster cycles. Eastman produces similar fast-cycle polymers like Tritan OM430.
Investigate the newest rapid-molding plastic formulations when selecting your materials. The extra cost per pound is easily justified by the greater hourly output and lower energy consumption stemming from shorter cycle times. Be sure to validate the mechanical performance too.
Leverage Multi-Cavity and Family Molds
While initially more expensive, multi-cavity molds producing four, six or eight parts simultaneously provide tremendous cost advantages at higher volumes. You amortize the tooling expense over greater output per cycle while streamlining automation.
A modular family mold system with interchangeable inserts allows molding sequential components from the same base. Changeover is faster and cheaper than entirely separate dedicated tools. Larger parts with shared attributes or dimensions are prime family mold candidates. Standardizing your mold parameters facilitates this approach.
Adopt New Multi-Material Molding
Innovative multi-material molding combines hard and soft plastics in a single step, eliminating assembly. The enhanced functionalities can downgrade costs overall through part integration. Overmolding onto metal inserts is another rising option.
Multi-material molding does require specialized machinery and expertise. Seek out custom injection molders and OEMs with demonstrated capabilities. Be ready to pay licensing fees for certain proprietary technologies still under patent. The long-range savings should warrant the expenses nonetheless.
Outsource to Asia for Higher Volumes
Presently no region can match China and Southeast Asia in sheer injection molding capacity and low-cost labor. Once you’ve vetted the quality and IP protections, offshoring high-volume contracts makes economic sense despite additional shipping and duties.
Domestically, utilizing an injection molder close to resin suppliers slashes your materials logistics costs. Maintaining competitive quotes from multiple vendors ensures you’re getting fair market pricing as well. Consider contract manufacturing for peak capacity needs or specialty applications too.
Take Advantage of Tax Incentives
State and local governments are providing tax holidays, credits, property exemptions and employee training grants to attract and retain manufacturers. Mexico touts logistics access and free-trade incentives. Puerto Rico offers similar perks like a 4% corporate tax rate.
Prioritize Energy Management
Injection molding plants are notoriously power-hungry. DOE statistics indicate electricity comprises over 25% of production costs for injection molders. Strategically managing your energy consumption through peak load shifting, smart metering, waste heat recycling and utility rebates directly raises profits.
Take a Total Cost Perspective
Always employ a total cost perspective when weighing injection molding investments versus part price savings. Will design changes enhance manufacturability? Do multi-cavity molds justify the riskier initial outlays? Does local production nullify offshore savings? Model different scenarios to uncover your optimum landed price point.
These money-saving pointers just skim the surface for keeping large part injection costs under control. For me, regularly monitoring every expense denominator—materials, machining, labor, logistics and yes, even utilities—is paramount to maximizing earnings in this margin-compressed industry. Comprehensive cost transparency lets you nimbly adjust operations accordingly.
What steps have you discovered to be effective for economizing large part injection molding? I welcome hearing about any additional cost-lowering tactics in the comments below!
Key Takeaways to Reduce Injection Molding Costs:
- Simplify part geometries whenever feasible
- Substitute aluminum components for steel in the mold tooling
- Use newer plastic formulations to slash cooling times
- Adopt multi-cavity and family mold configurations
- Consider multi-material molding or overmolding solutions
- Seek overseas manufacturing partners for volume production
- Leverage state and federal business incentives
- Monitor and conserve energy consumption
The Bottom Line
As we’ve examined here, companies can pare down the typically higher costs of large part injection molding via smart design decisions, materials selections, advanced production strategies and process refinements. What other methods have I missed? I’m eager to learn new ideas from readers for economizing large part molding. Please share your own plastic manufacturing experiences below!