Производитель вакуумной формовки пластика
В рамках нашего обязательства по предоставлению комплексных возможностей формования пластмасс мы с гордостью представляем услуги по вакуумной формовке пластмасс. Этот передовой производственный процесс дополняет наш опыт литья под давлением, обеспечивая универсальные и экономически эффективные решения для широкого круга задач.
Что такое вакуумная формовка пластика?
Вакуумная формовка пластика, также известная как термоформовка, - это производственный процесс, при котором лист термопластичного материала нагревается до податливого состояния, а затем формируется над формой с помощью вакуума. Этот процесс особенно хорошо подходит для создания больших, неглубоких деталей со сложной геометрией, предлагая экономически эффективную альтернативу литью под давлением для некоторых областей применения. Он широко используется в различных отраслях промышленности благодаря своей эффективности, гибкости конструкции и способности быстро производить высококачественные детали.

Наши возможности вакуумной формовки пластика
Компания Baiwe Molding использует свой обширный опыт в производстве пластмасс для предоставления исключительных услуг по вакуумной формовке. Наши возможности включают:
Материалы: Мы работаем с разнообразными термопластичными материалами, включая ABS, HIPS, PETG, акрил, HDPE и другие, гарантируя, что сможем удовлетворить ваши конкретные требования к материалам. Эти материалы выбираются с учетом их долговечности, ударопрочности и пригодности для различных применений.
Размеры деталей: От небольших прототипов до крупных серий, мы можем работать с деталями различных размеров и сложности, с размерами от компактных компонентов до негабаритных узлов.
Продвинутые техники: Наше современное оборудование поддерживает передовые технологии вакуумной формовки, такие как вставные формы, формование в виде билау и многодневные пресс-формы, что позволяет повысить детализацию и точность производства деталей.
Отраслевые стандарты: Мы придерживаемся строгих стандартов качества, включая такие сертификаты, как ISO 9001, гарантируя, что каждая деталь отвечает самым высоким требованиям к качеству и производительности.
Процесс вакуумной формовки
Дизайн: Мы сотрудничаем с вами, чтобы разработать оптимальную пресс-форму и спецификации деталей, гарантируя, что конечный продукт будет соответствовать вашим потребностям.
Выбор материала: Исходя из ваших требований, мы подбираем наиболее подходящий листовой термопластичный материал, учитывая такие факторы, как долговечность, ударопрочность и эстетичность.
Отопление: Пластиковый лист нагревается до температуры формования, что делает его мягким и податливым.
Формирование: Нагретый лист растягивается над формой, и под действием вакуума плотно притягивается к поверхности формы, формируя желаемую форму.
Охлаждение и обрезка: Деталь охлаждается для придания ей нужной формы, а затем обрезается для достижения окончательных размеров с использованием передовых технологий, таких как ЧПУ или роботизированная обрезка для обеспечения точности.
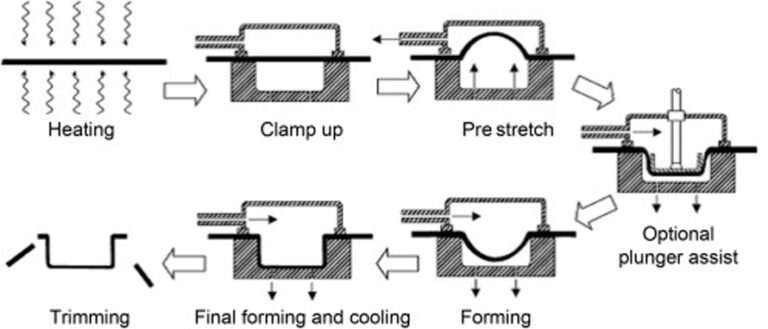
Преимущества вакуумной формовки
Выбор вакуумной формовки для вашего проекта имеет несколько ключевых преимуществ:
Экономическая эффективность
Более низкая стоимость оснастки по сравнению с литьем под давлением делает его идеальным для мало- и среднесерийного производства, сокращая первоначальные инвестиции.
Гибкость конструкции
Процесс позволяет с легкостью создавать большие сложные формы, что делает его идеальным для деталей со сложной геометрией.
Настройка
Мы адаптируем наши услуги к вашим точным спецификациям, гарантируя, что каждая деталь будет соответствовать вашим уникальным требованиям.
Легкий и прочный
Вакуумно-формованные детали легкие и в то же время прочные, что идеально подходит для применения в тех областях, где снижение веса имеет решающее значение без ущерба для прочности.
Быстрый оборот
Быстрые циклы создания прототипов и производства обеспечивают своевременную поставку деталей даже в сжатые сроки.
Области применения вакуумной формовки пластмасс
Наши услуги по вакуумной формовке предназначены для различных отраслей промышленности, включая:
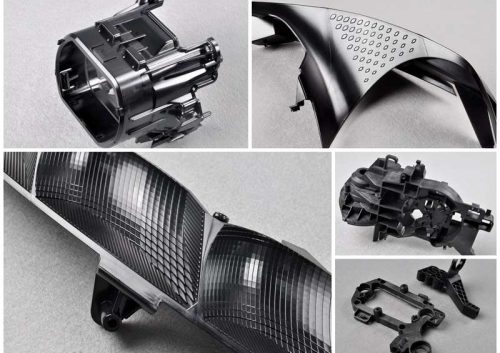
Автомобили
Внутренняя отделка, приборные панели, защитные крышки, лотки для аккумуляторов и подкрылки
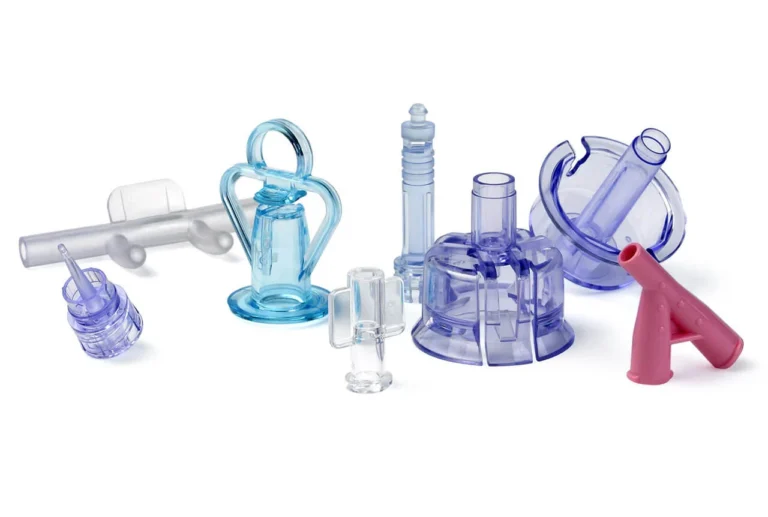
Медицина
Корпуса для устройств, лотки и упаковочные решения
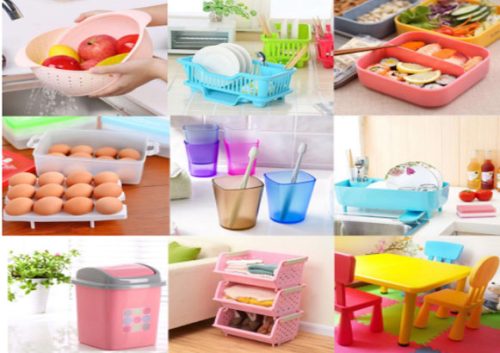
Потребительские товары
Детали для бытовой техники, корпуса для электроники и предметы домашнего обихода
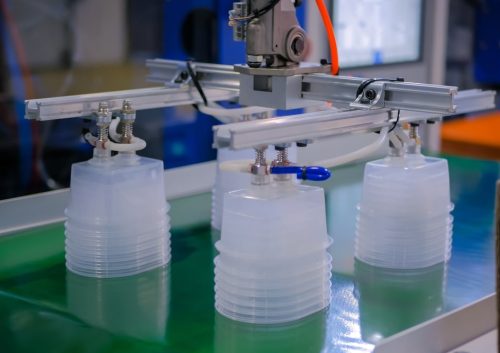
Упаковка
Нестандартные лотки, блистерные упаковки и контейнеры
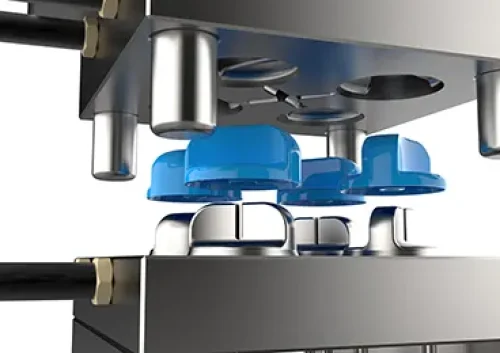
Прототипирование
Быстрое создание прототипов для разработки и тестирования продукции
Вакуумная формовка в сравнении с литьем под давлением
В компании Baiwe Molding мы понимаем, что разные проекты требуют разных производственных подходов. В то время как наши услуги по литью под давлением идеально подходят для крупносерийного производства сложных, детализированных деталей, вакуумная формовка предлагает явные преимущества для крупных деталей и коротких производственных партий. Предлагая обе услуги, мы предоставляем вам полный спектр решений по формованию пластмасс, обеспечивая возможность выбора наилучшего метода для конкретных потребностей вашего проекта. Такой комплексный подход позволяет нам обеспечивать беспрецедентную ценность и гибкость для наших клиентов B2B.
Характеристика | Вакуумная формовка | Литье под давлением |
---|---|---|
Стоимость оснастки | Низкая, идеально подходит для коротких пробегов | Более высокая, подходит для крупносерийного производства |
Объем производства | Малые и средние объемы | Большие объемы |
Сложность деталей | Лучше всего подходит для крупных, неглубоких деталей | Идеально подходит для сложных, детально проработанных деталей |
Время выполнения | Более короткое и быстрое создание прототипов | Дольше из-за сложности формы |
Использование материалов | Пластиковые листы (например, ABS, HIPS, PETG) | Термопластичные гранулы |
Почему стоит выбрать нас в качестве производителя вакуумной формовки пластика?
Экспертиза
Имея большой опыт работы в области литья пластмасс под давлением, мы привносим наш опыт и точность в вакуумную формовку, обеспечивая неизменное качество и надежность.
Обеспечение качества
Мы придерживаемся строгих стандартов качества, включая такие сертификаты, как ISO 9001, чтобы гарантировать, что каждая деталь соответствует самым высоким стандартам.
Клиентоориентированный подход
От первоначального проектирования до конечного производства мы тесно сотрудничаем с вами, чтобы обеспечить реализацию вашего видения и удовлетворение ваших потребностей.
Комплексные услуги
Будучи поставщиком полного цикла, мы предлагаем бесперебойную работу: от разработки концепции до создания прототипов и производства.
Дополнительный опыт
Литье под давлением идеально подходит для крупносерийного производства сложных деталей, а вакуумная формовка - для более коротких серий. Предлагая обе услуги, мы предлагаем вам лучшее решение для вашего проекта.
Свяжитесь с нами
Готовы узнать, как наши услуги по вакуумной формовке пластика могут принести пользу вашему бизнесу? Свяжитесь с нами сегодня, чтобы получить бесплатное предложение или обсудить требования к вашему проекту. Наша команда экспертов готова предоставить вам индивидуальные решения и исключительное обслуживание клиентов.