A short shot is one of the most common defects in injection molding. It occurs when the molten plastic fails to completely fill the mold cavity during the injection process. This results in an incomplete part with flaws like voids, sink marks, or thin areas.
Understanding what causes short shots and how to prevent them is critical for anyone involved in injection molding, whether you operate the machines or design the molds. Keep reading, as a professional plastic injection molding manufacturer, I break down this common issue facing the injection molding industry.
What Exactly is a Short Shot?
Let’s start by properly defining what a short shot is in injection molding:
A short shot refers to when the molten plastic material does not fill the mold cavity fully, leaving parts of the molded part incomplete, often at the farthest end from the gate.
This gives the plastic part unintended voids or holes and creates cosmetic and functional flaws making it unusable.
As you can see in the image below, the incomplete flow of plastic material has left a large section on the part unfinished, clearly characterizing it as a short shot:
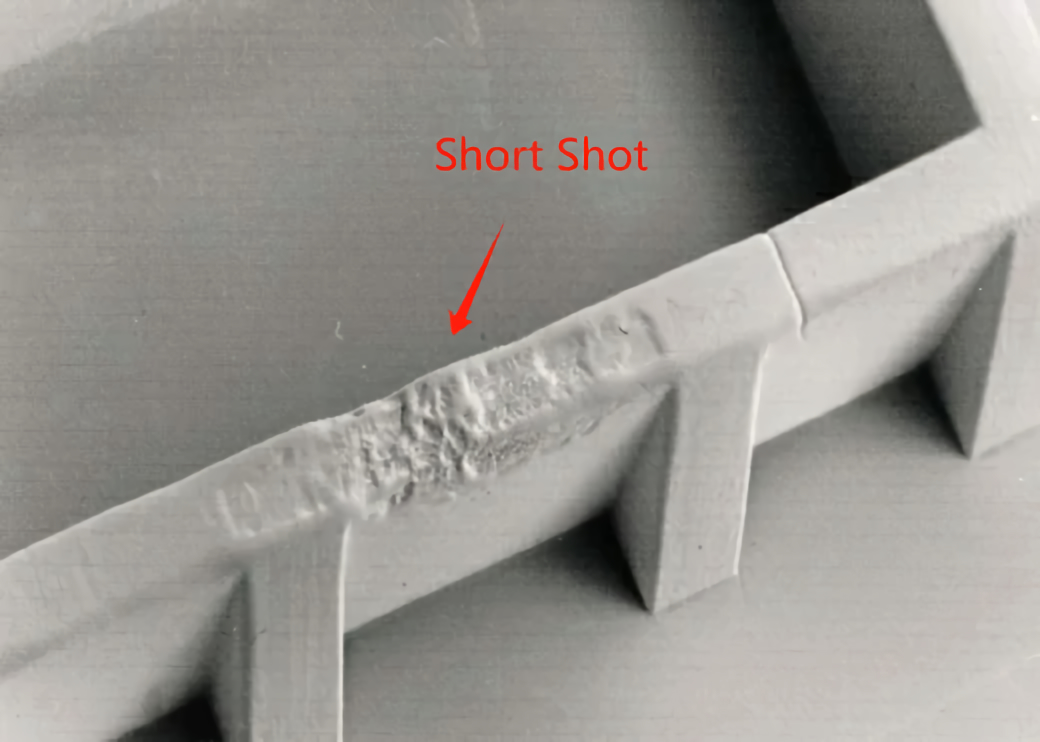
The main indicator of a short shot is the unfilled section. Still, other signs can also help identify the issue, like:
- Visible sink marks, warpage, or cracks
- Non-uniform wall thickness
- Flaws in overtime performance or intended functionality
What Causes Short Shots in Injection Molding?
Now that you know how to recognize a short shot, let’s look into what causes this common injection molding defect:
Inadequate Injection Pressure
One of the most frequent causes of short shots is the injection pressure failing to fill the mold. Reasons include:
- Machine capacity too low
- Pressure loss due to long runner lengths
- Smaller nozzle orifice restricting flow
To fix this, first ensure the injection molding machine has enough clamping capacity for the given mold. Using a larger nozzle orifice size also helps overcome restrictive pressure losses.
Premature Freezing
As the molten plastic flows into the mold, the plastic near the mold walls starts solidifying. This frozen layer keeps increasing in thickness as more material fills, eventually blocking the flow if it gets too thick.
Insufficient temperatures and improper cooling lead to premature solidification.
Uneven Wall Thickness
If the part design consists of both thick and thin sections, the thin areas often solidify before the thick ones fully fill. This imbalance hinders the flow of plastic causing short shots.
Proper mold cooling and using thermally conductive materials like aluminum or copper in those areas can prevent premature solidification.
Improper Venting
Trapped air causes resistance to the advancing plastic melt. No place for this air to vent out can lead to short shots.
Vents must be positioned at the end of fill locations to allow escaping air.
Gate Location and Size Issues
An off-centered gate makes filling the farthest end of the mold difficult. Small gates also restrict material flow, increasing chances of short shots.
Properly placed and sized gates ensure smooth filling without premature solidification.
Material Flow Properties
Plastic resins with higher viscosity flow slowly and can solidify before completely filling. Similarly, variations in moisture content and composition also affect flow.
Choosing low viscosity materials suitable for intricate molds prevents short shots. Proper handling and drying of plastic resins also improve fluidity.
How to Prevent Short Shots
Now that you know the common causes behind short shot defects, here are some ways to prevent them in your injection molding production:
Increase Injection Pressure
Boosting injection pressure gives the extra oomph for the material to fill intricate and complex cavities. But take care not to exceed the mold or machine capacity.
Optimize Process Temperatures
Higher barrel and mold temperatures keep the plastic molten for longer, reducing solidification issues. But don’t exceed material limits.
Improve Ventilation
Adds vents at problem locations for trapped air to escape smoothly without resisting plastic flow.
Account for Material Flow Properties
Consider resin viscosity, drying, and storage requirements during material selection to prevent flow inconsistencies.
Design for Manufacturability
Simplify geometries. Balance wall thicknesses. Mind gate locations and sizing. Simulation software helps virtually analyze problem areas.
How to Troubleshoot Short Shots
Despite the best attempts at prevention, short shots still occur due to the inherently stochastic nature of injection molding processes. But some methods can quickly troubleshoot short shot issues:
Short Shot Testing
Intentionally create short shots by disabling packing pressures. Analyze samples to identify problem locations and likely causes.
Process Monitoring
Track fill time, injection velocity/pressure, and temperature profiles in real-time. Data trends indicate deviations from optimal process.
Simulation Software
Virtually simulate filling patterns under different processing conditions. Optimize process based on predictions.
Catching and resolving short shot defects require understanding their causes, prevention methods, and troubleshooting techniques. Mastering these concepts is key to producing high quality, fully formed plastic injection molded components efficiently.
And that wraps up this guide on what short shots in injection molding entail, what causes them, and how to address them through apt prevention and troubleshooting measures. Let me know in the comments if you have any other tips for tackling short shots in your injection molding plant!