Splay is a common cosmetic defect that can occur during the injection molding process. As a professional injection molding manufacturer, I am writing this guide to cover everything you need to know about what causes splay on injection molded parts and how to prevent it.
What is Splay in Injection Molding?
Splay refers to the silvery or white streaks that can appear on the surface of injection molded plastic parts. It typically occurs when tiny gas bubbles form in the plastic material and get dragged across the surface of the part as the mold cavity fills.
The end result is a part with thin, scratch-like marks across the surface. While splay mainly affects appearance, it can also negatively impact the strength of injection molded components if severe enough.
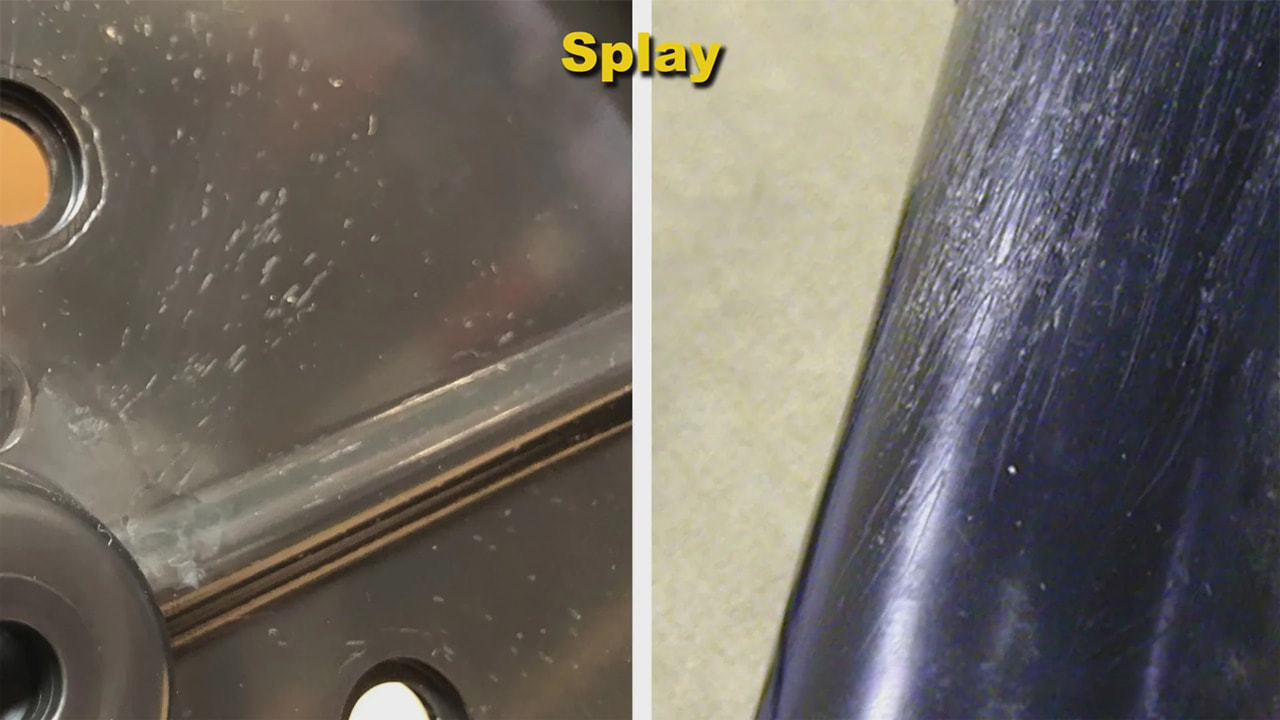
Splay is often confused with similar part defects like flow lines, surface scratches, contamination-induced delamination, and flaking. However, upon close inspection, true splay defects have some distinguishing characteristics:
- Splay marks typically follow the direction of melt flow through the mold.
- The streaks often appear silver or white in color.
- Marks are usually thin and look like scratches on the surface.
- Can occur randomly or appear consistently in the same area.
What Causes Splay in Injection Molding?
The main cause of splay defects is moisture trapped in the plastic resin during molding. But sheer heat and shear forces can also contribute to splay.
Here are the most common causes:
Moisture
Moisture is the number one cause of splay. When plastic resin contains trace amounts of water, it vaporizes into steam when exposed to the intense heat inside the injection barrel.
As the plastic melt fills the mold cavity, these steam bubbles migrate to the surface, solidifying into scratches and marks.
Hygroscopic resins like nylon and polycarbonate readily absorb atmospheric humidity and require proper drying prior to molding. But even non-hygroscopic materials only need small amounts of moisture to cause issues.
Water can inadvertently enter resin during transportation, storage, preprocessing, and even from equipment leaks.
Heat
Excessive heat exposure can also create splay-like defects on injection molded parts. Overheating the plastic can cause material degradation which gives off gases that get dragged on the surface upon ejection.
Potential heat-related causes include:
- Barrel or nozzle temperatures set too high
- Excessive back pressure shearing and overheating the resin
- Poor temperature control causing fluctuations
- Too long residence time in the barrel
Shear
High shear regions in the injection molding machine and mold can mechanically drag gases to the surface of parts. These shear-induced splay defects often appear consistently in the same location.
Typical shear-related causes:
- High screw rpm during plasticization
- Improperly sized gate causing shear
- Obstructions or restrictions in runner system
How to Prevent Splay Defects
Here are 7 tips to help avoid splay on your injection molded parts:
1. Use Splay-Resistant Materials
Some resins like acrylic, ABS, polypropylene and polyethylene are less prone to splay versus hygroscopic options like nylon or polycarbonate.
2. Dry Materials Thoroughly
Use a proper industrial dehumidifying dryer to remove moisture from resin prior to molding. Carefully follow manufacturer specs for optimal temperature and dwell times.
3. Lower Barrel Temperatures
Reduce barrel, nozzle and mold temperatures to recommended settings to prevent material degradation. Start conservative and slowly work up.
4. Limit Residence Time
Size the injection barrel and shot size for the mold to limit the duration resin spends inside the hot barrel. This reduces the chance of overheating.
5. Optimize Injection Speeds
Tweak fill speed profiles – slowing certain segments – to minimize shear from overly fast flow. Gradual transitions help too.
6. Ensure Proper Venting
Confirm the venting system in the mold has adequate cross-sectional area to allow gases to escape efficiently without obstructing flow.
7. Increase Back Pressure
Boosting back pressure can improve plasticization and dispersion of gases, reducing splay in some cases. But take care not to overheat.
Fixing Existing Splay Issues
If splay defects are already occurring, here is a systematic approach to identify root causes and correct the problem:
1. Thoroughly Dry Materials
Regardless of the type of plastic, confirm resin moisture levels are within specifications using a moisture analyzer. Increase dry time or temperature if too high.
2. Lower Mold & Melt Temps
Try dropping mold and nozzle temperatures in small increments. Give 20+ minutes for changes to take effect before inspecting parts.
3. Tweak Injection Profile
Alter fill speed, transition speeds, pressures and timing to minimize shear. Slow segments causing issue, improve gradual velocity changes.
4. Adjust Gate Size
If splay consistently appears around the gate, modify size and design to reduce shear. May require mold modification.
5. Check for Obstructions
Inspect nozzle tips, runners and vents for signs of plugs or restrictions contributing to splay from shear or poor venting.
6. Reduce Screw RPM
Lowering screw rpm can help diagnose if shear inside the barrel is causing splay. Marks should diminish if this is the case.
7. Lower Back Pressure
Like temperature, reduce back pressure incrementally if heat-related splay is suspected. Give time for changes to take effect.
Methodically evaluating and ruling out each variable influencing splay formation is key to both resolving current issues and preventing future occurrence through optimal injection molding process control.
In Summary
plastic injection molding process, preventing splay in injection molding, moisture induced splay defects, shear-related splay causes, heat and splay in injection molding process, fixing existing splay defects systematic approach
Splay defects from poorly controlled process parameters or material conditions can significantly reduce injection molded part quality and performance. But with vigilance and a systematic approach, these unpleasant silver streaks can be remedied or avoided altogether.