What Is Switchover Position in Injection Molding?
The switchover position, also known as the V/P switchover point, is a crucial transition point in the injection molding process. This position indicates when the injection molding machine switches from a velocity-driven filling stage to a pressure-driven packing stage.
Understanding what the switchover position is and how to optimize it is key for producing consistent, high-quality molded parts. In this comprehensive guide, as a professional plastic injection molding manufacturer, I’ll explain everything you need to know about determining and controlling the switchover position for precision injection molding.
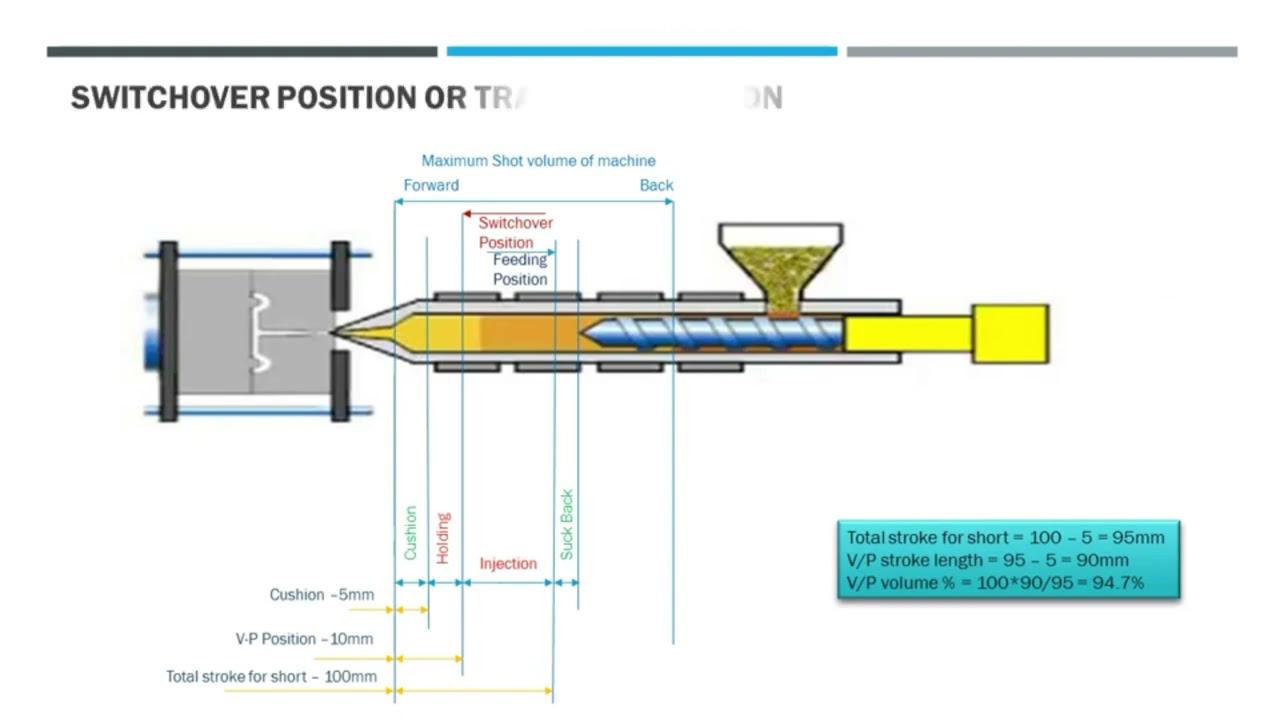
When Does Switchover Occur?
During the injection molding cycle, there are two distinct stages that fill the mold cavities with molten plastic:
- The filling or injection stage
- The packing or holding stage
The switchover position marks the transition between these two stages:
- Filling stage: The screw shoots forward, injecting molten plastic into the mold at a controlled velocity. The goal here is to quickly fill around 95-98% of the mold.
- Switchover: At the switchover position, the machine changes from velocity control to pressure control. This usually occurs when the cavity is 95-98% filled.
- Packing stage: The screw applies consistent pressure to pack out the mold and compensate for material shrinkage as it cools.
So in summary:
- The switchover position is the transition from velocity control to pressure control
- It typically occurs when the mold cavity is 95-98% full
- Determining the optimal switchover point is crucial for consistency
Now let’s look at how to determine when switchover should occur.
How is Switchover Position Determined?
There are a few common ways that injection molding machines can detect when to switch from filling to packing:
1. By Screw Position
This is the most popular method. The machine monitors the screw’s linear movement during injection. When the screw reaches a preset position, usually 95-98% of its maximum forward position, switchover is triggered.
Screw position is a proxy for cavity fill. The logic is that if the screw has moved to a certain position, the mold cavity should now be mostly filled with plastic.
However, this method can be inconsistent:
- Differences in material density or viscosity shot-to-shot alter how much the screw position correlates with cavity fill percentage.
- Wear on the screw and barrel can change the position values over time.
Still, screw position is simple and sufficient for many applications.
2. By Pressure
Some machines can switch from velocity to pressure control when the measured injection pressure reaches a setpoint.
As the mold fills with plastic, pressure gradually builds. When pressure hits the preset level, typically indicating 95%+ fill, the transition occurs.
This removes inconsistencies caused by screw wear and changes in material consistency. Pressure correlates directly to cavity fill, regardless of equipment condition or resin batch differences.
However, this method can still be thrown off if factors like injection velocity or mold temperature shift significantly.
3. By Time
Another option is to switchover based on injection time. The machine simply uses a timer to transition at a consistent moment in each cycle.
For instance, data analysis may show that 1.4 seconds of injection at a certain velocity reliably fills 95% of the mold. So the machine would switch from velocity to pressure control at 1.4 seconds every time.
This approach is rarely feasible, though. In order to set and maintain an accurate time value, parameters like part size, material viscosity, injection rate, and mold design need to be extremely consistent from run to run. In most real-world scenarios, there are too many uncontrollable variables to rely on a fixed timer.
4. By Cavity Pressure
Finally, cavity pressure sensors provide the most advanced and precise way to pinpoint switchover position.
Discrete sensors placed in the mold measure the real-time pressure inside the cavities during injection. When the sensors indicate that pressure hits a target, corresponding to 95% fill, switchover is triggered.
This approach accounts for inevitable inconsistencies between shots like changing material viscosity, temperature fluctuations, screw wear, etc. It also eliminates mold deflection variables found in machine-mounted sensors.
However, integrating these sensors adds cost and complexity. Each mold must be equipped with wired or wireless sensors and the necessary data transmission hardware to communicate with the central controller.
Why Getting Switchover Right Matters
The switchover position ties the injection stage and packing stage together. It ensures the cavity fills properly right as the machine transitions to apply packing pressure.
Getting this transition right is crucial for molding high-quality parts:
- Premature switchover can cause short shots. If pressure decreases before the cavity completely fills, the material will stop flowing, leaving unfilled sections.
- Switching to packing after the cavity fills can result in flashing at the parting line or ejector pins. Excess material may have nowhere to go but to leak out.
- The optimal switchover point balances fast cavity filling while ensuring ample pressure to pack out the mold. This results in dimensional stability shot-to-shot.
Takeaway: Consistent switchover timing, triggered at around 95% fill, leads to uniform cavity fill cycle-to-cycle. That means stable part weights and dimensions, less scrap loss, and higher quality components.
How to Optimize Switchover Position
Start by reviewing historical process data to set an initial target switchover value. Past successes or failures molding the same tool with the same material provide a reasonable baseline.
Collect datasets mapping recorded switchover values and part quality metrics cycle-by-cycle. Datalogging screw position, pressure, cavity pressure, fill time, etc. allows assessing correlations between switchover and key dimensions over numerous cycles:
- Does switchover happen consistently at one position or are there shot-to-shot variations?
- Do early or late transitions correlate with out-of-spec parts?
- What switchover value tends to produce the most dimensional stability?
Analyzing these data relationships helps narrow the optimal position. Additional validation testing fine-tunes machine settings like injection speed, mold temperature, etc. to help pattern and maintain desired conditions across multiple cycles.
Typical starting points for switchover position based on the transition method:
- Screw position: 95-98% of full screw travel
- Injection pressure: ~95% of maximum fill pressure
- Cavity pressure sensors: 90-98% of required fill pressure
Today’s precise electric machines and smarter process controls allow dialing-in highly repeatable switchover positioning to yield incredibly consistent molded components.
Developing a robust process with optimized V-P switchover control delivers tremendous quality advantages. But without diligent data collection and validation early on combined with disciplined, ongoing monitoring, even tiny variations can undermine the entire effort. Rigorous process verification ensures sustained precision output over long production runs.
Conclusion
The switchover position marks the vital transition during injection molding when the machine changes from filling the cavity at a controlled velocity (injection) to applying consistent pressure (packing). This changeover typically occurs at 95-98% cavity fill.
Selecting the most appropriate switchover detection method – screw position, injection pressure, precise time, or direct cavity sensors allows determining when the mold has reached the target partial fill percentage. This triggers the calculated filling-to-packing change command cycle after cycle.
Closely correlating monitored switchover data points to measurable output characteristics aids identifying optimum transitional values. Maintaining these idealized process parameters then helps ensure maximizing productivity and minimizing deviations. Carefully validating that only properly formed parts meeting all specifications are produced builds essential quality assurance.
With hundreds of interconnected device settings and material properties influencing overall precision, verifying performance through comprehensive data assessment confirms that statistically measured quality limits sustainably meet expectations through extended manufacturing campaigns.
Now you have a robust understanding of what exactly the switchover position is and how to leverage it for meticulous process control. Consistently triggering the transition at the ideal point in the filling-packing sequence promotes tremendous part consistency and minimizes variations that undermine efficiency and quality.
What questions do you still have about determining and optimizing the switchover position for your precision injection molding applications? Let me know in the comments!