Voids are a common defect in injection molding that occur when air pockets or empty spaces form within a molded part. As I explained in my complete guide to injection molding, they can be caused by a number of factors. In this post, as a professional injection molding manufacturer, I’ll outline the main causes of voids and how to prevent them.
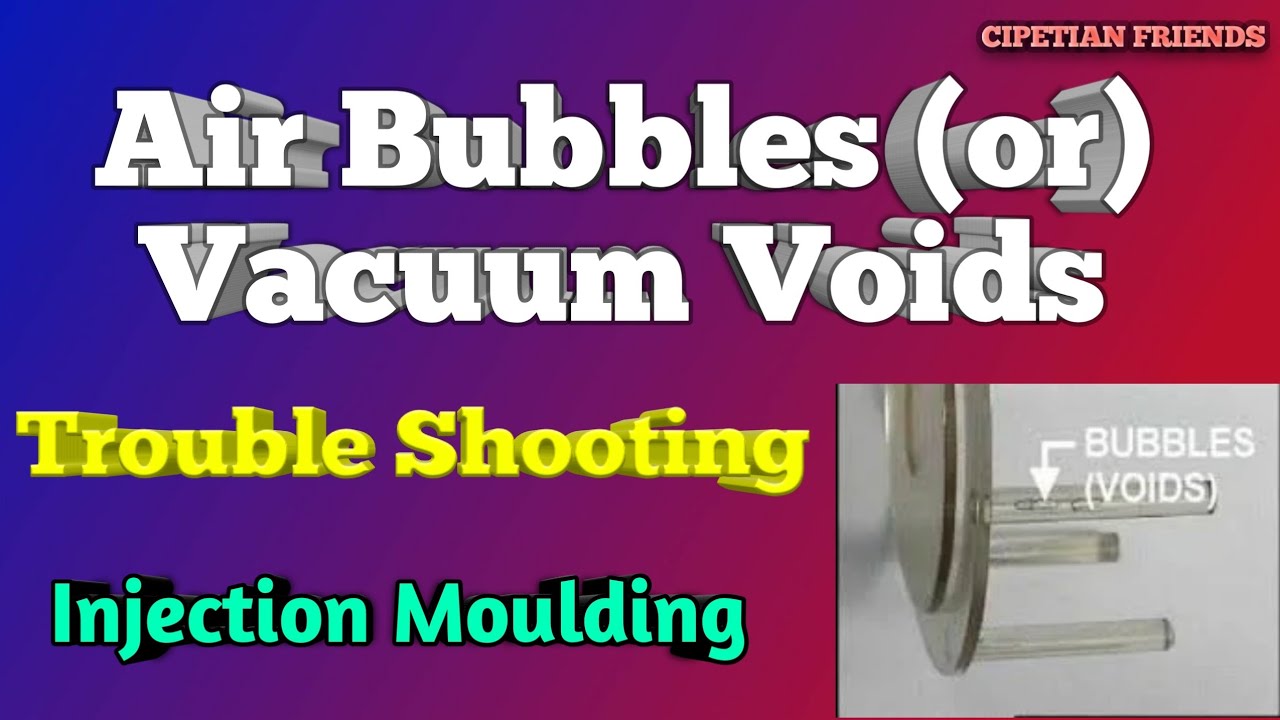
What Are Voids in Injection Molding?
Let’s start with a quick definition of what voids actually are.
Voids are small gaps or holes that form inside an injection molded plastic part. While not always visible, they can weaken the part structurally.
In transparent materials, you can often see voids with the naked eye. But in opaque plastics, specialized scans or cross-sections are needed to detect them.
Voids most commonly arise in thick sections of a part or where material flows converge, creating weak spots. Understanding what causes voids will help you avoid them through better mold design and processing adjustments.
What Causes Voids in Injection Molding?
Insufficient Plastic
If there isn’t enough molten plastic injected into the mold, the plastic that cools will leave empty spaces behind. This is often caused by a short shot, which is when the process step doesn’t introduce enough plastic.
Short shots basically “starve” sections of the mold, preventing complete filling. The result is internal gaps or voids after the plastic solidifies.
Boosting shot size, injection pressure, and other parameters can help ensure the mold cavity fills fully during injection.
Uneven Wall Thickness
Voids are more likely to form in thicker sections of the molded part. This can be caused by low holding pressure, which prevents the material from compensating for shrinkage.
As the outer layers cool faster than the core, they can create voids where the hotter material pulls inward. Maintaining even wall thickness is an important injection molding design rule.
Short Cooling Time
If the cooling time is too short, the surface layer solidifies before the inner layer, causing the inner layer to pull apart and form voids.
Slower, controlled cooling gives the material time to shrink evenly, avoiding these defects. Adjusting mold and melt temperatures can improve cooling performance.
Clogged Mold Water Channels
If the water channels inside the mold are clogged, it can lead to insufficient cooling in some parts of the mold, which can cause increased shrinkage and voids.
Proper mold maintenance and cleaning prevents channel obstructions and uneven cooling issues.
Air Entrapment
Air can become trapped during the injection process if venting is inadequate. As this air is displaced by the incoming material, it can leave behind voids.
Improving venting and using slower injection speeds prevents air bubbles from becoming encapsulated.
How to Prevent Voids in Injection Molding
To minimize or eliminate voids, you can try:
- Increasing the shot size
- Increasing injection pressure
- Increasing hold pressure
- Increasing the gate size
- Reducing melt temperature
- Thinning down the nominal wall
- Changing the gate location
- Raising the mold temperature
Careful analysis of voids found in samples can help identify the root cause so parameters can be tuned appropriately. But following injection molding design best practices is key to preventing defects from the start.
Voids formation requires a combination of process and design factors to arise. Addressing these weak points through changes on either front can create reliable, void-free molded components.
Hopefully this gives you a better understanding of what causes voids in injection molding. Be sure to read my injection molding process guide for more tips on defect prevention.