Selecting the right end mill is critical for precision plastic injection mold manufacturing. The choice directly impacts the mold’s surface finish, durability, and production efficiency.
As a professional plastic injection molding manufacturer, I am writing this definitive guide to walk you through everything you need to know about choosing end mills for plastic molds.
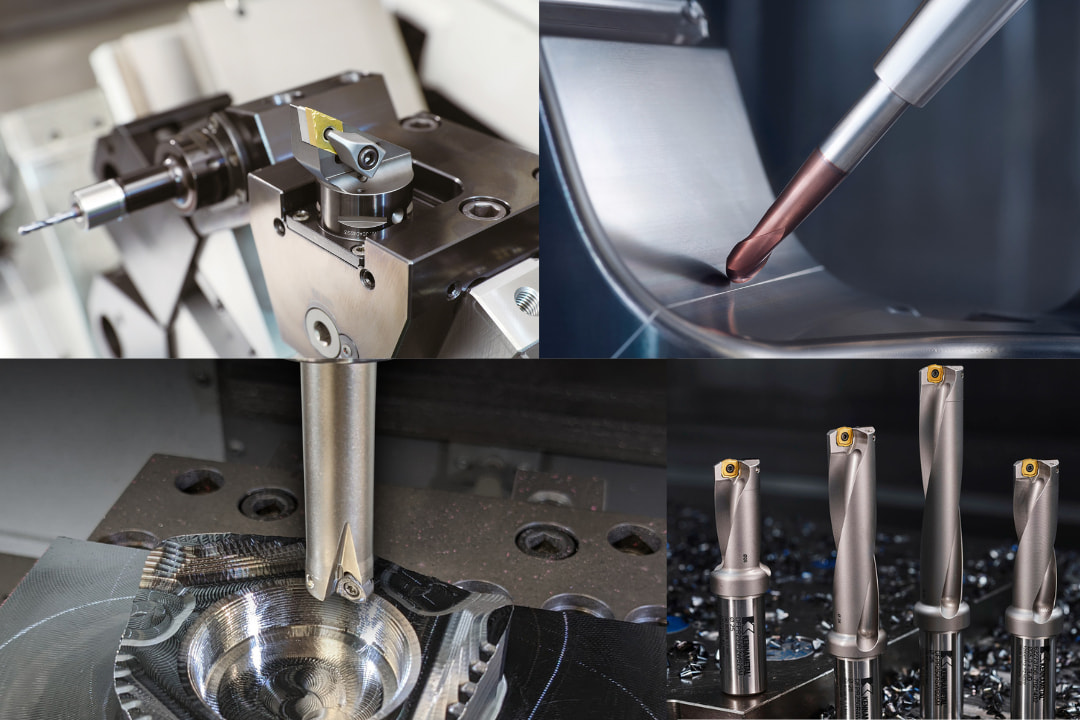
Why the End Mill Matters
The end mill does the heavy lifting during the CNC machining process that creates injection molds. It’s the cutting tool that physically removes material to form the mold’s cavities and cores.
Choosing the optimal end mill depends on factors like:
- Mold material
- Level of part detail and complexity
- Surface finish requirements
- Tool life expectancy
- Material removal rate
Balancing these parameters allows moldmakers to achieve the best possible outcome. The quest is finding end mills capable of maintaining precision while working efficiently.
So what should someone creating plastic injection molds look for in end mills?
Key End Mill Selection Considerations
Moldmakers have several dynamics to weigh when selecting end mills best suited for machining plastic injection molds. Being cognizant of these dynamics from the job outset primes the process for success.
Mold and Electrode Material
Hardened tool steel is a common moldmaking material because it withstands high injection pressures and resists wear over time. Pre-hardened tool steel eliminates heat treating but is difficult to machine.
Therefore, the end mill requires exceptional wear resistance and hardness to repeatedly impact this challenging material without losing form or function. Carbide end mills are ideal for meeting these demands.
Carbide provides:
- Hardness to maintain integrity machining hardened steels up to ~48 HRC
- Strength and toughness at elevated temperatures
- Compressive strength for interruptions
Meanwhile, graphite and copper electrodes enable spark erosion finishing. The end mill must expertly machine these softer, gummier materials requiring maximum shearing action.
Design Detail
Micro-milled plastic parts showcase the most intricate contoured, etched, or textured surfaces. But miniature components challenge end mills to perform similar to their full-sized counterparts.
Tighter tolerances mandate precision toolpaths. Accuracy becomes paramount with smaller dimensional part details, especially pockets, radii, ribs, etc. High-performance end mills reliably meet spec machining miniature core/cavity features.
Shorter end mills with high flute counts and variable spacing provide additional stability when pushing small-diameter tools for detail work. Reduced runout further enhances precision milling accuracy.
Surface Finish
Glossy plastic parts start with polished mold surfaces. Most injection mold surfaces target an Ra <0.025μm, which is possible based on factors like workpiece material, tool selection, and machining parameters.
Maintaining tool sharpness is vital for achieving mirror surface finishes required in production molds. Coatings reduce friction and associated heat for keeping cutting edges sharp longer.
Carbide end mills should exhibit exceptional edge retention. At the same time, coatings like titanium aluminum nitride (TiAlN) or titanium carbon nitride (TiCN) boost performance. A smooth end mill finish passes directly to the mold.
During testing, electropolishing further enhances surface finish. It also helps inspect tool marks indicating deficient end mill performance.
Tool Life
Within certain parameters, opting for larger-diameter end mills improves material removal rates for efficiency. But tool life expectancy is another calculation that aids appropriate end mill selection.
Given extended machining time for mold components, end mills demonstrating longevity keep costs down. Tool changes result in downtime along with insert indexing for replaceable head tools.
Tool manufacturers conduct cutting tests representing real-world parameters to determine insert life. For example:
Feed Rate: 8 in/min
Cutting Speed: 400 SFM
Axial Depth per Pass: 0.25″
Radial Depth: 100% diameter
Cold Work Tool Steel ~52 HRC
Such input helps estimate life per cutting edge (~15 minutes). This translates to production outcomes based on aspects like work schedules, complexity, tool accessibility, etc.
Carbide end mills often feature parabolic flutes for added strength and life expectancy when running full slotting operations. Meanwhile, replaceable-head designs allow fresh cutting edges introducing upon insert indexes.
Material Removal Rate (MRR)
MRR refers to volumetric metal removal over time. Essentially, it defines machining efficiency for improved cost management, scheduling, capacity, etc.
Larger-diameter tools inherently remove material faster for roughing mold cavities and cores. Then finishing progresses from larger to smaller end mills for detail work per optimal chip load and surface finish requirements.
So mold shops balancing plastic part quality against cost and delivery needs factor MRR into end mill selections.
Injection Mold Process – Material Removal Steps
- Roughing with large roughers/hoggers
- Semi-finishing with roughers/hoggers or smaller tools
- Finishing with ball nose end mills
- Polishing with ball nose end mills
The goal becomes determining the fewest end mills for completing the job satisfactorily within standards.
Recommended End Mills for Plastic Injection Molds
Moldmaking demands led cutting tool engineers to designs end mills purpose-built for machining molds. Several factors make certain end mills well suited for milling plastic injection molds.
Solid Carbide End Mills
Carbide is integral for tooling that machines abrasive materials hour after hour. For mold work, micrograin carbide provides hardness nearing ceramic with higher fracture resistance.
Major end mill delineations include:
- Material/substrate
- Number of flutes
- Diameter
2-flute, square end mills cover roughing needs typically with larger diameters for slotting efficiency.
Carbide allows reasonably high surface speeds and feed rates. So while removing substantial material, cutting forces and heat generation remain manageable. Proper chip evacuation is key!
Ball nose end mills excel in semi-finishing to finishing requiring low stepovers. Their rounded cutting edges self-center in contours preventing gouging at edges. High feed rates blend well with light stepovers maintaining tight geometric tolerances.
Ensuring appropriate corner radii relative to details prevents over engagement. Variable helix and core flute geometry facilitate chip egress.
But for intricate components with thin walls, even specialty carbide end mills may lack necessary integrity.
This leads moldmakers to solid ceramic mills, chemically stronger than carbide. Zirconium oxide boosts wear resistance and heat tolerances for pushing small tools harder without losing precision.
Of course, solid tools lack replaceable inserts found with carbide counterparts. So detecting and replacing ceramic end mill wear is vital for quality and safety. Frequent resharpening restores a sharp cutting edge but allows limited regrinds.
Still, ceramic end mills serve a purpose roughing and finishing temperature resistant or abrasive plastics that quickly dull steel alternatives. They provide mold shops means for tackling specialty materials and applications.
Coated End Mills
Coatings create a slippery barrier minimizing heat and cutting forces. This enhances end mill tool life, performance, and consistency for improved capacity and profitability.
Consider coatings like:
Aluminum Titanium Nitride (AlTiN) – Multipurpose for working stainless steels with high speeds/feeds. Provides temperature resistance and wear protection well suited for semi-finishing and finishing cast iron molds.
Titanium Aluminum Nitride (TiAlN) – Maintains tool integrity for precise finishing at high surface footage machining hardened materials ≥ 48 RC. TiAlN allows pushing carbide end mills harder with less wear.
Titanium Carbonitride (TiCN) – Ideal for high production machining needs working steels from 1144 stressproof up to P-20 mold steel. Provides strength and lubricity for secure, accurate toolpaths.
So for shops milling various mold components, optimized coatings enhance appropriate tools for associated needs. This allows standardizing broadly capable end mills capable of satisfying diverse machining objectives.
Micro End Mills
Miniature end mills provide means for adding fine details making molds for micromolded components. Certain production applications require high accuracies with wall thicknesses and feature sizes below 150 μm.
With their minute diameters, micro end mills feature precision cutting mechanics. Very short flutes prevent deflection while optimizing chip evacuation. This maintains dimensional precision and reliability during lights out production runs.
Micro end mill geometries include square end, ballnose, and varieties with highly polished flutes. Rigid precision collets and machine setups ensure stability and accuracy when pushing micro tools aggressively within safe parameters.
Moldmakers gain means for bypassing laser technology needs with high velocity techniques using micro carbide end mills. Component costs come down through fast accurate CNC processes. And replacing hand polishing reduces lead times.
Variable Helix and Variable Pitch End Mills
Variable helix end mills feature flutes ground at differing helix angles. This design innovation disrupts harmonics for preventing chatter and vibration even within deep pockets. Stable low-noise cuts result from uneven timing of teeth contacting the material.
The varying helix angles also enhance chip evacuation. So combining this ability with precisely ground variable pitch flutes further promotes efficient chip removal for clean accurate cuts. Open channels help reduce heat buildup to maintain sharp cutting edges and tight dimensional tolerances.
End Mill Selection Process Example
To summarize appropriate end mill selections for high quality, economical plastic injection molds, let’s explore a theoretical sample part.
Injection Molded Sample Part
- Thin-wall electronic enclosure
- ABS plastic material
- Tight dimensional tolerances
- Textured exterior finish
- Draft angles for extraction
- P-20 hardened steel mold
Machining Objectives
- Secure tight geometries and wall thickness from cores and cavities
- Mirror surface finish on mold components
- Reduce polishing procedures through precision milling
End Mill Selection Rationale
Roughing – Larger square end carbide mills
Semi-finishing – Carbide ball nose mills with TiAlN coating
Finishing – Smaller TiCN coated carbide ball nose mills
Result – Textured surface finish achieved physically machining the mold instead of spark eroding electrodes. This saves costs and lead time.
Key Takeaways
- Carbide end mills deliver strength and longevity for reliable production molds
- Purpose-built geometries enhance toolpaths through challenging materials
- Coatings like AlTiN, TiAlN and TiCN boost tool performance and surface finishes
- Micromills provide accurate intricate capability potential
- Custom designs help moldmakers push boundaries controlling quality, cost and delivery
Determining appropriate characteristics and custom specifications primes tools for tackling diverse plastic moldmaking challenges. So rather than settling with marginal solutions, leverage the expanding technological potential granting means for achieving moldmaking objectives smarter.
The optimal tool exists! Finding the best path for getting there poses the fun.