Injection molding is a manufacturing process used to produce plastic parts in high volume. It works by melting plastic pellets and injecting the molten plastic into a mold cavity, where it cools and solidifies into the final part shape.
One of the key components of an injection mold is the runner system, which delivers the molten plastic from the injection molding machine nozzle to the cavities in the mold. The runner can be heated or left unheated.
A hot runner is a heated delivery system that keeps the plastic molten as it flows into the mold cavities. Hot runners allow parts to be produced faster, with less waste compared to traditional cold runner molds. As a professional plastic injection molding manufacturer, I will share everything about hot runner in injection molding in this post.
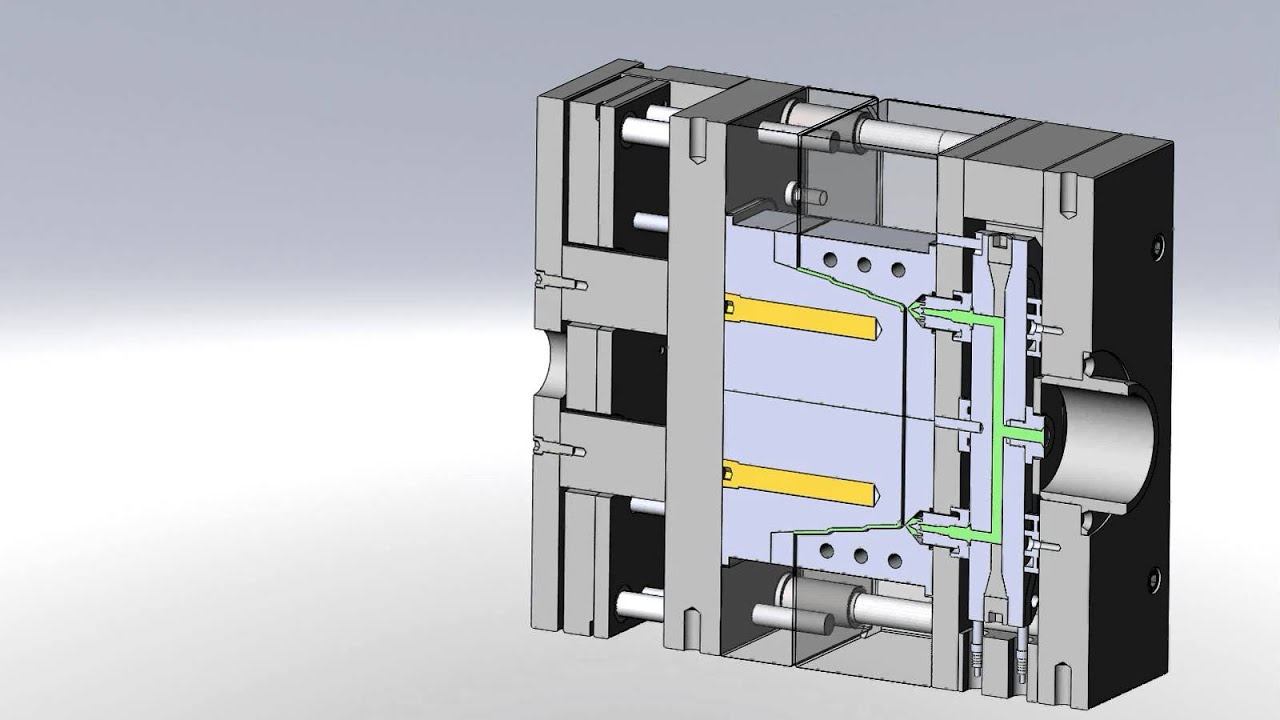
What Exactly is a Hot Runner?
A hot runner consists of a heated manifold and a series of heated nozzles. The main tasks are:
- Distribute the molten plastic entering the mold to multiple nozzle tips
- Meter the plastic precisely into each cavity through injection points at the nozzle tips
The hot runner manifold and nozzles remain heated, which keeps the plastic molten as it travels into the mold cavities.
Once the cavities are filled, the part is cooled and ejected just like with a cold runner system. The difference is no solid plastic remains inside the hot runner after each cycle.
Hot runner systems totally eliminate scrap plastic waste. They also speed up cycle times since there’s no need to cool a big slug of plastic inside a cold runner.
Hot Runner System Components
A basic hot runner system consists of:
- Manifold – Distributes melt to the nozzles
- Nozzles – Precision gate the plastic into each cavity
- Heaters – Heat elements that maintain temperature
- Controllers – Monitor and control manifold/nozzle heaters
More complex systems also contain extra components like nozzle tips, valve gates, filters, etc.
Hot Runner vs Cold Runner
Cold runners use unheated channels to deliver plastic into the mold cavities. After each cycle, the cold slug of plastic in the runners must be ejected along with the parts.
The pros of cold runners:
- Lower upfront cost
- Accommodate more material types
- Easier to change runner layouts
The downsides are longer cycle times, plastic waste, and lower part quality.
Hot runners provide complete melt control, faster cycles, and no scrap plastic. The tradeoffs are higher initial cost and maintenance requirements.
Over the long run, hot runner systems often pay for themselves through:
- Faster production rates
- Reduced energy and material costs
- Higher quality parts
Types of Hot Runner Systems
There are two main hot runner configurations:
1. Internally Heated
Internal heaters are embedded into the hot runner components. This offers precise thermal profiles and great process control.
Most common for engineering grade resins like ABS, PC, nylon when tight tolerances are needed.
2. Externally Heated
External heaters clamp onto the outside of hot runner components. More suitable for thermally sensitive materials like PVC and PET.
Also allow faster color changes compared to internal designs.
Hot Runner Gate Types
The gate is the restriction point where plastic enters the mold cavity. Hot runners use either a hot tip gate or valve gate.
Hot Tip Gates
A heated nozzle tip injects plastic through an open gate into the cavity. After injection the plastic freezes off naturally inside the gate.
Pros: Simple, low cost, small gate vestige
Cons: Less process control, potential for stringing
Valve Gates
A valve pin rapidly opens and shuts the gate to start and stop the flow. This creates a clean gate with no vestige or strings.
Valve gates offer the best performance for challenging resins and strict quality requirements.
Benefits of Hot Runners
Hot runner systems provide complete melt control from machine nozzle to mold cavity. This enables:
- Faster molding cycles
- Higher production output
- Reduced scrap plastic waste
- Improved part quality and consistency
- Greater design freedom
Hot tip and valve gate designs meter plastic through precision gates into the mold cavities. Smart gate placement eliminates cosmetic blemishes on finished plastic parts.
When Are Hot Runners Used?
Any application running over 1 million cycles per year is a good hot runner candidate. The benefits multiply for molds with higher cavitation counts.
Typical hot runner applications:
- High volume plastic components – closures, cups, caps, lids
- Medical consumables – pipette tips, syringe parts
- Electrical connectors and encapsulations
- Precision technical parts
Larger hot runner systems with 128+ drops are used to produce billions of bottle caps, closures, and other high volume plastic parts.
Conclusion
A hot runner keeps molten plastic hot as it flows directly into mold cavities without cooling inside a runner. This eliminates scrap plastic waste while accelerating cycle times.
Hot runner injection molding improves part quality, reduces production costs, and increases manufacturing efficiency. When designed and processed properly, hot runners generate significant long term savings over the cold runner approach.