Cavity pressure is one of the most important parameters to measure and optimize in injection molding. As an indicator of part quality, understanding and controlling cavity pressure leads to faster cycles, less scrap, and lower costs.
As a professional plastic injection molding manufacturer, I am writing this article to discuss the cavity pressure in injection molding. In this complete guide, you’ll learn:
- What exactly cavity pressure is
- Why cavity pressure is so critical for part quality
- How cavity pressure correlates to your molded parts
- Tips and best practices for optimizing cavity pressure
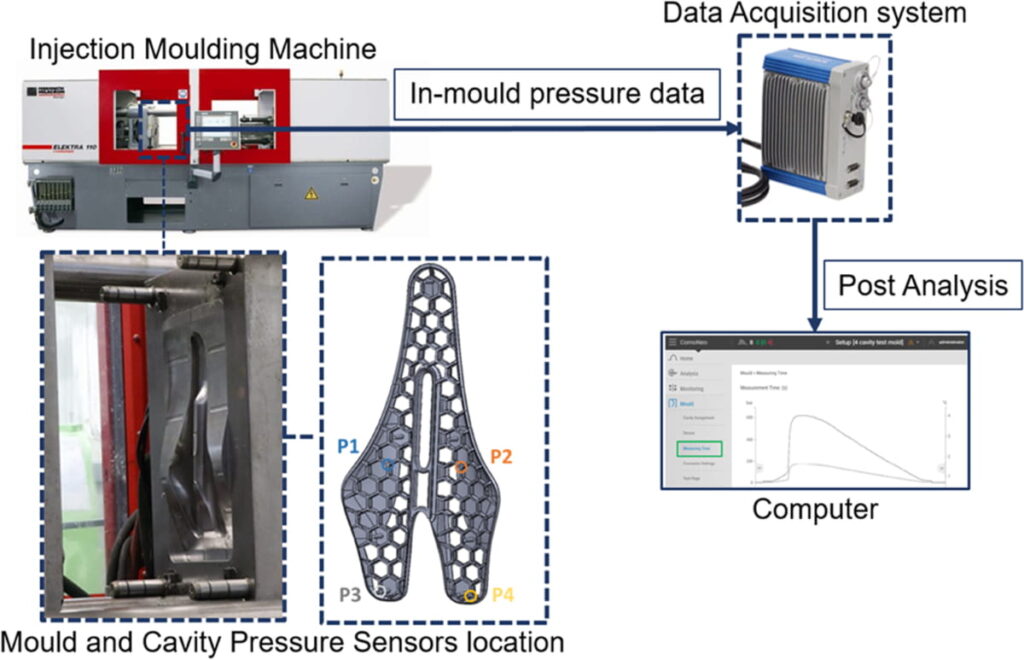
What is Cavity Pressure in Injection Molding?
Inside every injection mold are one or more cavities filled with molten plastic that forms each part. The pressure exerted inside those cavities is simply known as cavity pressure.
Cavity pressure trends dynamically throughout the entire molding cycle, from injection through cooling and ejection. This makes it an incredibly informative parameter about what’s physically happening to the plastic as parts are produced.
Hydraulic, Plastic, and Cavity Pressure
On most injection molding machines, you’ll see hydraulic pressure displayed on the operator control screen since it relates to the pump output. This isn’t the actual pressure inside the barrel or mold though!
Plastic pressure, also called injection pressure or specific pressure, refers to the physical resistance of the melted plastic flowing inside the barrel and nozzle. This pressure gets amplified through the nozzle tip and sprue based on the machine’s intensification ratio.
Finally, cavity pressure represents the real-time pressure inside the mold cavities themselves. It’s lower than plastic pressure due to losses through the runner system.
For true process control and repeatability, cavity pressure is the optimal value injection molders should monitor.
Why is Cavity Pressure So Important?
Measuring and analyzing cavity pressure provides major benefits:
- Direct correlation to part quality
- Improved process stability
- Faster setup and optimization
- Reduced scrap and testing costs
Essentially, tracking precise cavity pressure curves enables you to “see” inside the mold. The visualization it provides is like having x-ray glasses on, making it easy to isolate molding defects and tweak parameters accordingly.
Cavity Pressure is the “Fingerprint” of Quality Parts
As parts fill, pack, and cool inside the mold, changes in cavity pressure correlate directly to the final dimensions, appearance, strength, and performance of that product.
Certain values can indicate whether pressure is too high or low, viscosity isn’t optimal, or if other defects like short shots, flash, sinks, and warpage are present.
By monitoring these trends, cavity pressure becomes the “fingerprint” of a good quality part. As long as the curve stays within defined process limits, you can confirm parts meet specifications.
Faster Setup and Process Optimization
Setting up a stable injection molding process typically requires extensive production trials testing combinations of temperatures, pressures, speeds, and timing.
Monitoring real-time cavity pressure accelerates validation by immediately showing the impacts of adjustments. It also makes balancing hot runner systems easier since you can pinpoint pressure uniformity.
Over the long run, optimizing around cavity pressure minimizes variation part-to-part and lot-to-lot. This reduces the need for revalidation and expensive dimensional inspections.
Step-by-Step How to Measure and Analyze Cavity Pressure
Now that you understand why cavity pressure is so valuable, let’s explore how to actually measure it and use the data.
Here is an overview of best practices to implement cavity pressure sensors and monitoring systems:
Step 1: Install Sensors at Optimal Locations
Piezo or strain gauge-based sensors are mounted directly inside the mold cavity to capture pressure data.
Where to place sensors depends on the part geometry, number of cavities, and injection locations. Via simulation software, determine positions that provide an accurate overall representation of cavity pressure.
Pay attention to:
- Gates and end-of-fill locations
- Areas with thick and thin cross-sections
- Areas prone to defects like short shots or sink marks
Proper sensor integration requires screw holes or notches inside the cavity steel along with slots/grooves for routing cables out of the mold.
Step 2: Connect to Data Acquisition Device
Wired or wireless transmitters connect sensors inside the mold to a central data acquisition device. This captures pressure and temperature measurements dynamically over the entire molding cycle.
Choose hardware with the capabilities to handle required:
- Number of sensor channels
- Sampling speed and data volume
- Integration with other sensors like melt or mold temp
- Software compatibility for analyzing results
Step 3: Interpret the Cavity Pressure Curve
With real-time quantitative data, operators can identify the specific molding phase where issues arise based on changes in the pressure curve shape:
Injection Phase: Pressure spike indicates initial mold filling. Premature drop can predict short shots.
Transition Phase: Pressure peaks reaching predetermined optimal value correlates with 100% mold fill. Lower values indicate incomplete filling.
Packing/Holding Phase: Pressure must remain high enough through solidification to generate required part strength and appearance. Premature drop indicates material or machine deficiencies.
Ideally, plot data from multiple cycles on top of each other to visualize stability. Try to achieve a tight process window where cavity pressure stays repeatable cycle-to-cycle.
Tips and Best Practices for Optimizing Cavity Pressure
Consistently meeting cavity pressure targets leads to less scrapped parts and faster cycle times. Here are tips improve control:
1. Determine optimal targets
Every mold and material combination has unique optimal pressure targets. As a starting point, consider manufacturer’s recommendations but fine-tune based on correlation to first article inspection results.
2. Improve sensor integration
If pressure values fluctuate erratically cycle-over-cycle, sensors may be installed suboptimally. Double check placement locations and cable routing issues.
3. Tweak injection velocity
Faster injection exponentially increases cavity pressure, while slower injection provides a wider process window. Adjust velocity profiles to stabilize pressure.
4. Modify mold temperature
Cooler molds allow easier cavity packing while hotter molds reduce viscosity and pressure losses. Optimize mold temp to meet targets.
5. Switch gate location
Long flow lengths cause more pressure losses than direct gates. Consider relocating gates closer to problem areas in the mold.
6. Upgrade machine size
On small machines, maximum injection pressure might not reach levels needed for complete fills. Switch to larger clamp tonnage.
Conclusion – Why Cavity Pressure Matters for Part Quality
Understanding what’s happening inside the mold is critical for companies seeking to optimize their injection molding processes and slash manufacturing costs.
As the most direct indicator showing the conditions in which each part gets created, real-time cavity pressure measurement provides unparalleled value.
With proper sensor selection and placement paired analytics software, cavity pressure curves inform smarter decision-making:
- Identify stability issues causing defects
- Accelerate DOEs and process optimization
- Document process validation for ISO or medical regulations
- Sort good vs. bad parts automatically
By leveraging this easily accessible data, your team gains valuable insight into the plastic’s physical state and unlocks production efficiencies across all injection molded products.
What aspects of cavity pressure were most surprising or new to learn? Let me know in the comments what you found valuable in this guide or have any additional questions!