Injection molding is a ubiquitous manufacturing process used to produce plastic parts and products at scale. As one of the most common methods of plastic part production globally, understanding injection molding – including key concepts like cold slug wells – is important for anyone involved in manufacturing or product design roles.
In this complete guide, as a professional plastic injection molding manufacturer, we’ll break down exactly what a cold slug well is, why it matters in injection molding, and how to properly design cold slug wells for optimized mold performance. Let’s get started!
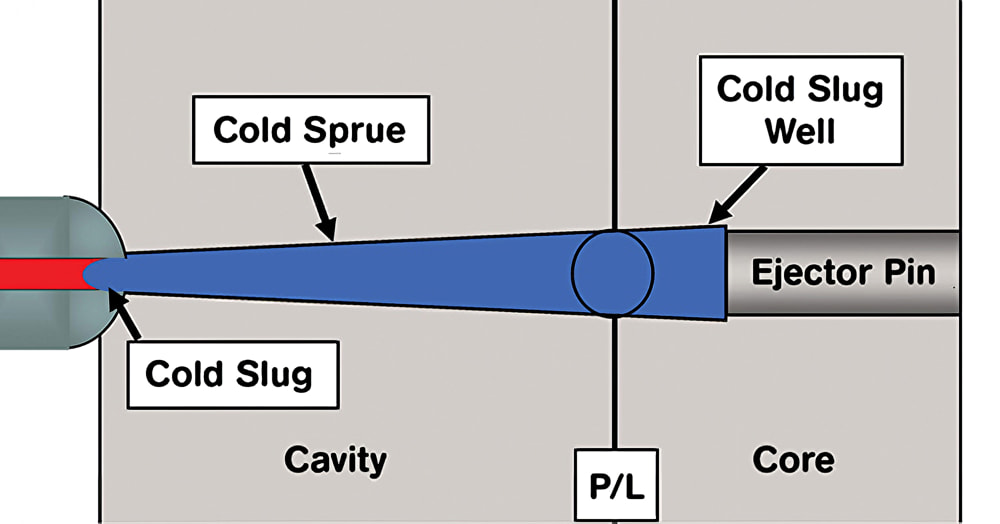
What Is a Cold Slug Well?
A cold slug well is a small reservoir or cavity that is deliberately designed into the runner system or gate area of an injection mold.
The primary purpose of the cold slug well is to capture and contain the cold slug – a small volume of cooled, solid plastic that often forms at the tip of the injection nozzle during molding processes.
What is Cold Slug Well in Injection Molding?
It is a small reservoir built into the mold that captures solid plastic pieces that can form at the nozzle tip, preventing them from causing defects like surface imperfections or knit lines. Strategic cold slug well placement and design helps safeguard part quality consistency.
Why Do Cold Slugs Form?
Cold slugs form intermittently at the nozzle tip for a couple of key reasons:
- Heat Loss – The nozzle tip loses heat to the surrounding air and cold mold steel during idle periods. This can cause the residual plastic to cool down and solidify.
- Temperature Differentials – There is a significant temperature discrepancy between the heated barrel/nozzle (200-300°C) and the cooled mold cavities (<100°C). This amplifies material solidification issues at the gate.
So in essence, cold slugs start to take shape when the nozzle tip or gate area interfaces with cooler mold components, causing the hot plastic melt to rapidly lose heat and solidify.
Problems Caused By Cold Slugs
If these cold slugs enter the mold cavity, they can cause all sorts of issues, including:
- Surface defects (e.g. sinks, voids, blisters)
- Visible weld/knit lines from material flow obstruction
- Reduced mechanical properties
- Inconsistent fill leading to short shots
Fortunately, this is where cold slug wells shine…
The Role of The Cold Slug Well
As the name implies, cold slug wells provide a place to contain, capture and isolate cold slugs during the injection molding sequence.
By sequestering the cold slugs before they reach the mold cavity, cold slug wells prevent defects and maintain part quality consistency.
Additionally, cold slug wells help stabilize molding processes by promoting steady melt flow. This minimizes cycle variations and fluctuations at startup after the barrel has been idle.
Now that we understand why cold slug wells matter, let’s explore some best practices for cold slug well design…
Cold Slug Well Design Guidelines
Properly implementing cold slug wells is crucial for optimized injection mold performance. Follow these design guidelines when planning your cold slug wells:
1. Strategic Positioning
It’s important to tactically locate your cold slug wells based on flow dynamics and where cold slugs are likely to accumulate.
Ideally, position the cold slug well at the end of primary runners or wherever major melt flow convergences occur before gates. This ensures cold slug interception right before cavity injection.
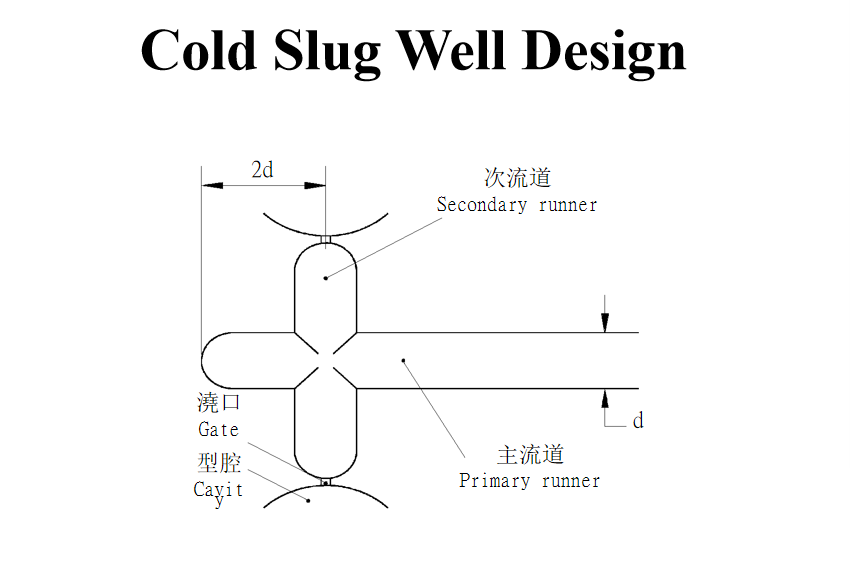
Figure 1. Example of a strategically positioned cold slug well before a mold gate.
Gate geometry and processing parameters will also influence positioning. Consult with your mold designer to identify optimum locations.
2. Adequate Sizing
When sizing a cold slug well, ensure adequate volume to contain expected cold slug formation – but avoid excess space.
Oversized wells can allow too much material to pool, starving parts and extending cycles.
Conversely, undersized wells may lead to overflow into the cavities. Both scenarios defeat the purpose of the cold slug well.
As a rule of thumb, size the cold slug well about 20-30% larger than the primary runner width. This adds margin without introducing pooling risks.
3. Flow Merge Considerations
When implementing wells in multi-gate molds with converging melt flow, carefully consider dynamics at flow merges.
In these cases, provide enough cold slug well space to contain slugs from ALL leading runners. Failure to account for aggregate flow could negate the effectiveness of the well.
4. Robust Construction
While cold slug wells don’t withstand injection pressures, they still endure significant thermal-mechanical forces.
Construct wells from robust, durable mold materials – typically prehardened stainless tool steels (P20, PX5). Durable materials prevent erosion or deformation issues over time.
Summarizing Cold Slug Wells
In injection molding, cold slug wells are vital insurance policies against molded defects and inconsistencies.
By intercepting solidified nozzle drool before it reaches mold cavities, cold slug wells safeguard part quality.
Careful placement relative to gates/runners ensures comprehensive cold slug capture. Additionally, proper design sizing avoids problems like short shots or pooling.
With attention to positioning, dimensions and molding dynamics, cold slug wells banish flow obstructions – helping realize optimized, repeatable molding processes.
Now that you understand cold slug wells more clearly, you’re well-equipped to implement them into your future injection molds!