Decompression, also known as suckback, is an important setting in injection molding that helps relieve pressure at the end of the injection process. As a professional plastic injection molding manufacturer, I am sharing this detailed look at what decompression is, why it’s important, and how it impacts the injection molding process.
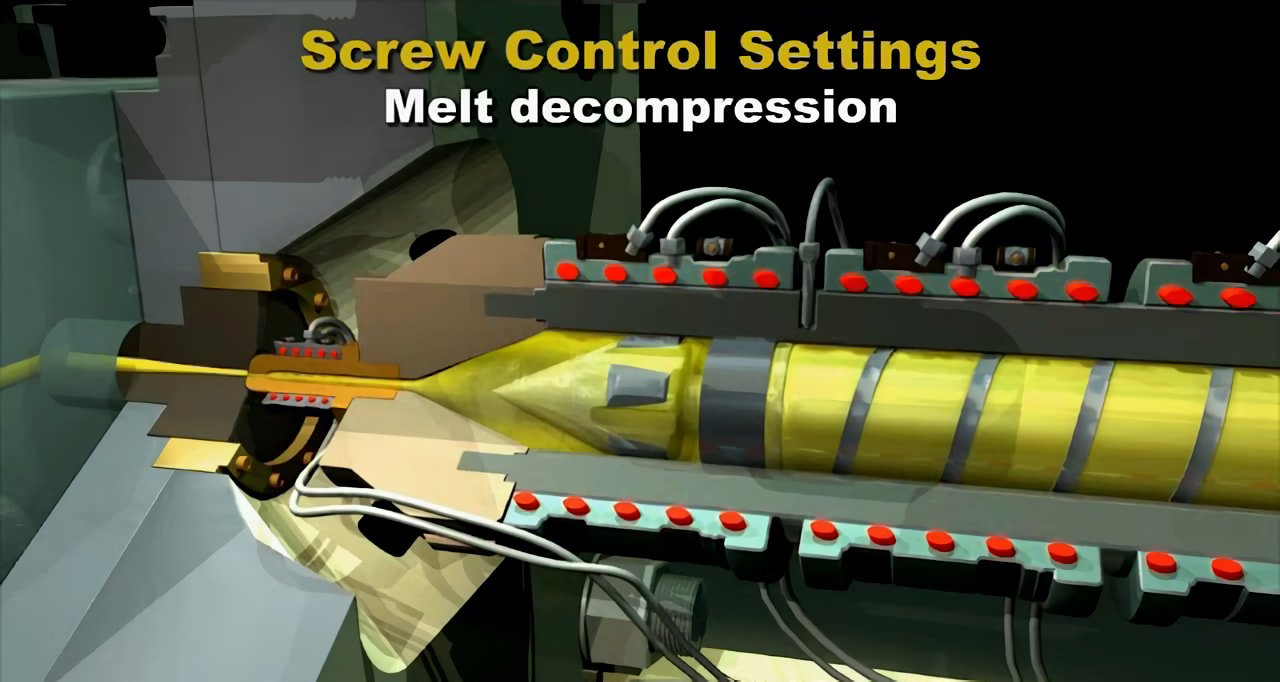
What is Decompression in Injection Molding?
Decompression, or suckback, refers to retracting the screw slightly at the end of the injection process to relieve pressure in front of the screw tip. This is done by pulling the screw back linearly a small distance, usually around 0.1 inches or a couple millimeters.
Decompression is critical for reliving the built-up pressure in the barrel right before the packing and holding phases. It creates a small gap between the screw tip and the cushion in front of it. As the screw rotates to dose material for the next shot, this gap gets filled first before pressure can build up again to start forcing the screw back.
What Happens During Decompression
Decompression is a controlled movement where the screw partially retracts, or gets “sucked back” into the barrel. This happens after the screw has finished injecting plastic into the mold cavity.
The screw may retract just a few millimeters. But this small movement has a big purpose – it relieves pressure that has built up in front of the screw tip.
Without decompression, high pressure would remain trapped.
Relieving this pressure serves several functions:
- It allows machines with open nozzles to prevent drool or material leakage
- It improves consistency of shot size and plasticization
- It may help the check valve close completely
- It can reduce wear and tear on components like the check ring
Later in this guide we’ll explore the specifics of how decompression impacts injection molding processes. First, let’s look at why managing pressure is so crucial in injection molding.
Why Control Pressure With Decompression?
Pressure control is challenging yet critical in injection molding. Too much pressure causes issues like flashing, short shots, and part defects. Too little pressure leads to incomplete filling.
Decompression gives processors better control over pressure at a key point – when injection ends and packing/holding begins.
With decompression, you avoid applying packing pressure to an over-pressurized situation. This prevents problems like:
- Flashing from excessive pressure
- Premature gate freeze off blocking flow
- Damage to components from pressure spikes
- Inconsistent shot sizes from check valve leaks
Well-tuned decompression also ensures adequate pressure remains to completely pack out parts.
Dialing in the optimal decompression is all about finding the right balance between relieving excess pressure and maintaining enough pressure for packing.
Decompression Vs. Other Types of Pressure Control
In addition to decompression, injection molding machines have other ways to manage pressure like:
- Packing pressure – Lower pressure applied after filling to pack out the mold cavity
- Two-stage injection – Switching from high injection pressure to lower pressure at a set point
- Nozzle shut-offs – Valves to block the nozzle and contain pressure
Decompression works hand-in-hand with these other pressure controls. For example, well-timed decompression allows a smooth transition from injection pressure to packing pressure.
And removing residual pressure may eliminate the need for nozzle shut-offs on many molding processes.
How Much Decompression Is Needed?
There’s no universal rule for how much decompression (retraction distance) to apply. Requirements depend on factors like:
- Machine nozzle – Open vs. shut-off
- Material viscosity and freezing characteristics
- Actual injection pressure used
- Desired packing pressure
- Check ring design and condition
As a starting point, many processors use a decompression distance equal to 1.5 times the check ring travel. But don’t rely solely on rules of thumb.
Tuning decompression settings is key for optimizing pressure control. We’ll explore tuning procedures in more detail shortly.
Decompression Terminology
Like most manufacturing processes, injection molding has its own unique language. Here are a few key terms related to decompression:
- Suckback – Another term for decompression based on the screw getting “sucked back” into the barrel
- Drool control – Preventing material leakage from open nozzle tips during decompression
- Cushion – The small amount of plastic left in front of the screw after decompression
The cushion acts like a spring to transmit pressure into the pack and hold phases. Size and consistency of cushion are critical for uniform production.
Why Use Decompression? Benefits and Drawbacks
Now let’s explore some of the key benefits decompression brings to injection molding:
Prevent Material Leakage
On machines with open nozzle tips, decompression prevents material from drooling out or stringing during the transition between injection and packing.
This function replaces mechanical shut-off nozzles. Avoiding shut-offs eliminates their maintenance and potential for leaks or freeze-off.
Improve Shot Consistency
Well-tuned decompression optimizes the size and shape of the cushion. This enhances shot-to-shot consistency.
In contrast, inadequate decompression allows material to flow back irregularly toward the screw. This erodes the cushion and causes shot size variation.
Reduce Wear and Tear
Decompression alleviates pressure trying to force the check valve open during injection. This reduces grinding and wear.
Lower pressure during valve closure also decreases loads on components like the screw tip, check ring, and spray nozzle.
Over long production runs, decreased wear saves money on maintenance, repairs, and downtime.
Enhance Process Control
Getting decompression right is key for total pressure management. Mastering this parameter gives processors better command of filling, packing, and part quality.
However, incorrect decompression can undermine consistency and part quality:
- Excessive decompression allows air ingestion leading to defects
- Too little decompression causes check valve leaks and cushion variation
This unpredictability will sabotage even the best attempts at scientific molding process control.
How And When To Decompress
Now that we’ve covered the critical importance of decompression, let’s look at how and when it happens in the injection molding cycle.
There are two options for initiating decompression:
Time-Based
The early, purely time-based approach starts decompression after injection time reaches a setpoint.
A typical sequence is:
- Injection phase fills mold cavity
- Injection ends when cavity pressure or screw position reaches threshold
- Timered delay allows gate freeze
- Decompression retracts screw to reduce pressure
Basing decompression solely on time lacks precision. It risks retracting too soon before the gate seals or too late allowing backflow.
Position-Based with Screw Recovery
Modern controllers tie decompression directly to screw position. This approach decompresses during screw recovery after detecting the screw reaches a target.
Here is a typical sequence:
- Fill phase injects material until screw reaches programmable position
- Pressure switchover to cavity sensor
- Screw recovers to catch up with position setpoint
- Decompression activates at recovery limit switch
- Screw rotates to rebuild cushion
This technique prevents backflow while ensuring adequate pressure remains to pack the mold.
Position-based screw recovery for decompression is accurate and responsive to each shot’s variations. This keeps the process optimized and under control.
Tuning Decompression Settings
Like most injection molding parameters, properly setting decompression requires testing and analysis:
Step 1: Baseline Without Decompression
First, turn off decompression and establish baseline conditions. Take note of key indicators:
- Shot weight consistency
- Part quality variation
- Flashing or marks from pressure spikes
- Nozzle drool
Step 2: Start Low And Slow
Turn decompression back on starting with conservative settings. For example:
- Distance: 1 mm
- Time delay: 50 ms
Step 3: Gather Data
Take measurements over a sample run length (ex. hourly checks over 8-hour stretch):
- Shot size average and range
- Cavity and nozzle pressure readings
- Production log showing defects
Step 4: Adjust And Retest
Increase decompression settings incrementally while assessing impacts:
- Try higher retraction distance
- Adjust time delay forward or back
- Enter values directly or by percentage
After each tweak, repeat data sampling and analysis before making the next change.
Step 5: Find The Sweet Spot
Plot trends until defect rates hit an acceptable threshold while other critical measures like shot weight show minimum variation.
Be methodical while evaluating the risk/reward trade-offs from increased decompression distance or time.
Zeroing in on optimal settings aligns decompression perfectly to relieve excess pressure while sustaining packing phase requirements shot after shot.
Getting Help With Decompression
Because so many variables impact optimizing decompression, getting help can accelerate setup. Options include:
- Material Suppliers – Manufacturers provide detailed processing guides for their resins including decompression recommendations.
- Machine Manuals – Most press manuals give baseline decompression distances to start tuning from.
- Moldmakers – Companies engineering and building your mold have expertise for setting decompression with their tooling design and your selected plastic.
- Simulation Software – Advanced programs now model impacts of parameter changes like decompression timing and distance. Their predictions generate an excellent initial baseline.
- Scientific Molding Experts – Injection molding specialists and advanced control system integrators bring extensive hands-on knowledge for rapidly mastering decompression methods to apply for your application. Take advantage of their expertise rather than starting from scratch alone.
While tuning decompression relies on precision indicators and systematic adjustment methods, also use your senses while testing. Listen for changes in machine sound with more or less decompression. Feel for subtle shifts in vibration. Input from all your faculties helps guide your analysis.
Mastering decompression – and pressure control in general – is challenging yet worthwhile. Injection molding is as much art as science. Develop experience-based intuition to take your scientific process control to the next level.
Applications Suited For Decompression
Adding decompression enhances injection molding processes in many ways. But several situations gain particular advantages:
1. Eliminating Nozzle Drool
Open nozzle molding machines risk material leakage without decompression. Well-calibrated suckback containing melt in place of nozzle shut-offs prevents mid-cycle drool.
2. Hot Runner Molds
Decompression releases residual pressure preemptively. This protects delicate hot runner components from exposure to excessive spike loads when valve gates close.
3. Precision Molding
Micromolding and other processes requiring shot-to-shot consistency depend on stable cushion formation. Decompression tunes cushion just right for repeatability.
4. Scientific Molding
Advanced analysis and control methods demand total pressure management. Decompression is the missing link for true mastery over fill, pack, and hold stages.
5. Validating Controls
Dialing in decompression puts sophisticated sensor suites and adaptive-on-the fly algorithms to an extreme test. If process models can nail this parameter, confidence is supreme in their recommendations.
For any application chasing utmost consistency and capability, learning to leverage decompression is a must. Start reaping the benefits today with the guidance above. Keep pressing onward to ever-tightening precision and perfection!
In Summary
To summarize, decompression (or suckback) retracts the screw to relieve trapped pressure after injection fills the mold cavity. Managing this pressure transition prevents defects while enabling complete part packing.
Tuning decompression distance and timing is nuanced yet vital for boosted consistency. Mastering this technique unlocks new levels of scientific control and advanced precision molding.