Injection molding is a common manufacturing process used to produce plastic parts. One critical parameter that impacts part quality is the holding time. But what exactly is holding time and why does it matter? As a professional plastic injection molding manufacturer, I will help you find it out.
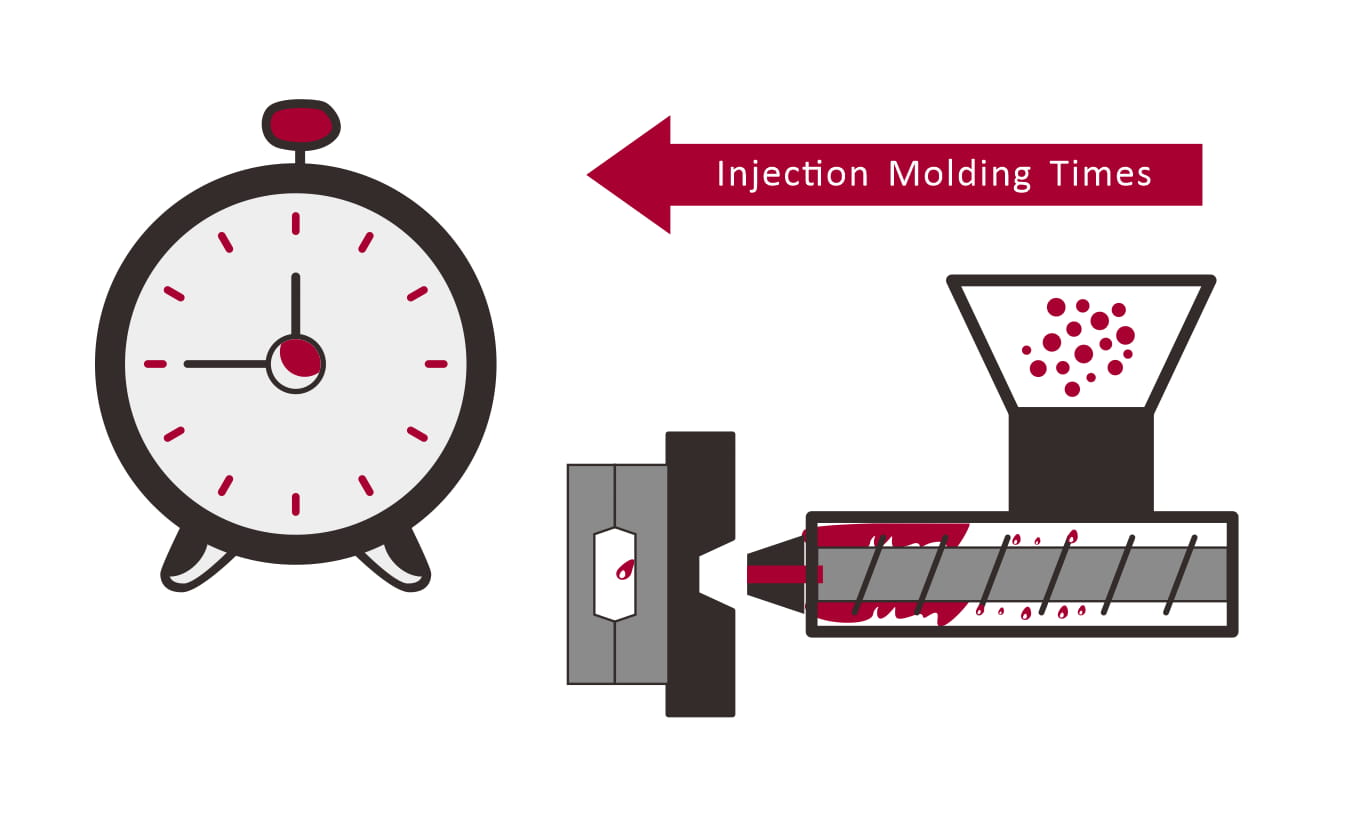
What is Holding Time in Injection Molding
Holding time refers to the duration that pressure is maintained on the plastic part after the mold cavity has been filled during the injection molding process. It is the final stage before the part cools down and solidifies.
The purpose of the holding time is to allow extra molten plastic to flow into the mold cavity to make up for material shrinkage as the part cools. This helps minimize defects like sink marks, warpage, and short shots. An optimal holding time will result in uniform shrinkage and a good surface finish.
So in summary:
- Holding time starts after the mold cavity has been filled
- Holding pressure is maintained during this time
- It allows the mold to “pack” more material to account for shrinkage
- A properly set holding time improves part quality
Understanding how holding time impacts your injection molded components is key to producing consistent, high-quality parts.
Why is Holding Time Important?
Maintaining the proper holding time ensures that the mold cavity remains completely filled as the plastic solidifies. This achieves several objectives:
Compensating for Shrinkage
As we know, plastics shrink as they cool. Holding time gives additional molten resin time to flow into the mold cavity. This replaces the material that’s shrinking, minimizing defects.
Insufficient holding time leads to short shots, sinks, voids, and other flaws. Parts can also be inconsistent from shot to shot.
Eliminating Backflow
The other purpose of holding time is to apply pressure until the gate or Gates freeze. If pressure drops too soon, material can flow back out of the cavity.
Backflow causes similar defects as inadequate holding time. It also prevents full packing out of details in the mold.
Allowing Gate Sealing
In order for gates to completely seal, pressure must be maintained on the resin for a sufficient duration. Prematurely ending holding time risks leaving gates partially open.
The gate seal time ensures no more material can enter the cavity. If gates don’t properly seal, backflow occurs.
How Long Should Holding Time Be?
Unfortunately there’s no universal holding time that works across the board. The required duration depends on several factors:
Part Thickness
Thicker parts need longer holding times. More material shrinkage occurs in thicker cross-sections as they cool. This takes longer to replace with additional flowing resin.
As a rule of thumb, allow 1 second of holding time per 1 mm of part thickness. Complex geometries may need more time.
Material Being Molded
The type of plastic used affects holding time requirements. For example, nylon and acetal tend to shrink more than materials like ABS due to their semi-crystalline nature. These resins need longer holding times.
Materials that flow easily like polyethylene can usually get by with shorter durations. The viscosity impacts how quickly gates will seal.
Mold Design Considerations
Certain mold aspects influence needed holding times as well. Molds with unbalanced flow or larger gates require longer holding. More time is needed to fully pack out and freeze these gates.
Hot runner molds also frequently need extended holding. Their gates don’t completely seal until after injection is done.
How to Determine Optimal Holding Time
While rules of thumb like 1 second per mm of thickness provide a starting point, the best way to determine holding time is through experimentation. Here are some methods:
Weight Method
This procedure involves changing only the holding time while keeping other parameters constant:
- Weigh a sample part molded with no holding time
- Increase holding time incrementally (say by 0.5 seconds)
- Weigh samples from each step, recording part weights
- Repeat until weight levels off and stabilizes
The time just before weight stabilizes is considered the minimum holding time. Add 10-20% to this number as a safety factor.
Dimensional Method
Similar to the weight procedure, dimensions are checked while incrementally increasing holding. The time where overall dimensions stop changing significantly indicates when the gate seals. As with the weight method, add an extra margin beyond this point.
Mold Protection Methods
For unbalanced molds or those with inserts, various techniques can help prevent overpacking while still sealing gates:
- Adjustable pins that shut off flow to packed areas
- Valve gates
- Multi-stage holding profiles
Regardless of method used to determine holding time, it’s critical to understand its role in producing quality injection molded components. Track part weight or dimensions, or utilize advanced mold technologies. But don’t neglect this important parameter.
Properly setting and controlling holding time eliminates defects, ensures consistency, and maximizes efficiency. It’s an essential consideration for any injection molder.
Key Takeaways on Holding Time
- Holding time allows the mold to pack out after filling, replacing shrinking material
- It prevents backflow by keeping pressure until gates seal
- Thicker parts, certain materials, and complex molds need longer times
- Use weight or dimensional analysis to find optimum duration
- Add a 10-20% safety margin beyond minimum required
- Consistent holding = consistent, high-quality injection molded parts
Knowing these holding time fundamentals will help you achieve defect-free, repeatable results across all your injection molded component product lines.