Injection molding is one of the most versatile and widely-used manufacturing processes in the world. This production method is commonly utilized to mass produce plastic parts and products in a variety of shapes, sizes and complexities.
But what exactly is injection molding used for? What types of applications and products use this manufacturing technique?
In this complete guide, as a professional plastic injection molding manufacturer, I’ll cover everything you need to know about what injection molding is used for across various industries.
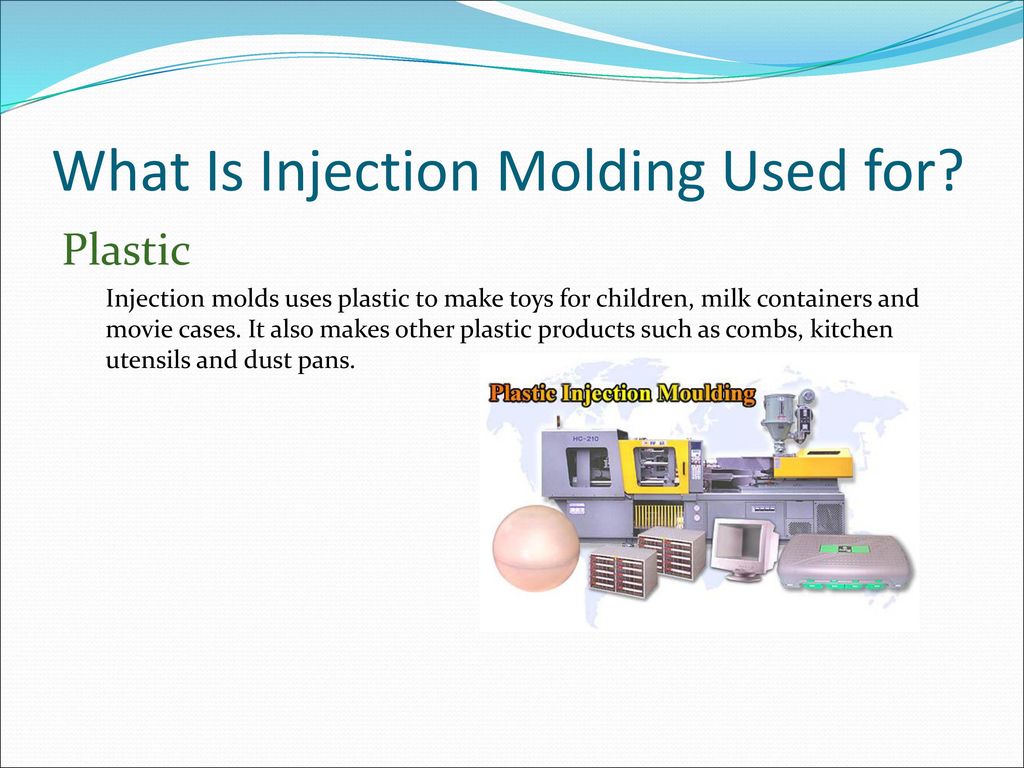
An Overview of Injection Molding Processes and Capabilities
In essence, injection molding works by injecting molten plastic materials into a mold under high pressure. The plastic then cools and solidifies into the shape of the mold’s interior cavities.
This makes injection molding suitable for producing intricate, detailed and complex shapes at scale. The process is also extremely repeatable, enabling manufacturers to produce thousands or even millions of identical plastic parts.
As a result, injection molding is very cost-effective for mass producing plastic products and components. The more parts are produced, the lower the cost per part becomes compared to other manufacturing methods.
This combination of shape complexity, repeatability and economical production volumes is why injection molding is one of the most extensively used manufacturing technologies across many industries.
Let’s take a closer look at some of injection molding’s most common applications and the types of products that leverage this versatile process.
What is Injection Molding Used For?
Automotive Industry
The automotive industry utilizes injection molding heavily to manufacture the countless plastic components found in modern vehicles. Interior and exterior vehicle parts such as:
- Door panels
- Steering wheels
- Dashboards
- Bumpers
- Lights
- Grilles
Are all frequently produced through injection molding due to its ability to combine complex geometries, precision, strength and economical production runs.
As automakers continue incorporating more lightweight plastic parts to reduce vehicle weight and increase fuel efficiency, injection molding will continue growing as an indispensable process for auto manufacturing.
Consumer Goods and Products
Many day-to-day consumer goods leverage injection molding during production, including:
- Mobile phone cases
- Computer peripherals (mice, keyboards etc.)
- Household appliances
- Furniture
- Toys
- Storage containers
- Kitchenware
Essentially, if a product contains plastic parts, there’s a very high chance it was manufactured using injection molding at some stage of production.
The process excels at allowing manufacturers to produce plastic goods in virtually any shape, texture or color while keeping costs low. This flexibility and scalability makes injection molding the consumer goods industry’s material processing method of choice.
Medical Devices
Medical device manufacturers frequently utilize injection molding for the vast array of equipment, disposables and accessories used in healthcare. These encompass both high and low volume components such as:
- IV connectors and bags
- Syringes
- Multi-well plates
- Pipette tips
- Enclosure housings
Stringent quality control is often required to ensure precision dimensions and avoid defects. Fortunately, injection molding delivers exceptional repeatability when process parameters are tightly controlled.
The medical industry also benefits from the versatility of injection molding, which can cost-effectively shape plastics to demanding product specifications.
A Recap
As one of the most versatile and accessible manufacturing methods available, injection molding serves industries spanning medical, automotive, consumer goods, industrial machinery and many more.
Essentially, if a product or component requires:
- Detailed plastic shapes/geometries
- Consistent, high dimensional precision
- Large production quantities per mold
- Economical per-part cost at production volumes
Then it’s highly likely injection molding is or can be used during its manufacturing process.
The process empowers manufacturers to produce endless configurations of plastic parts, at scale, to almost any specification required. For this reason it has grown into one of the most prolific, influential and widely adopted manufacturing technologies in the world.