Injection molding is one of the most common manufacturing processes for making plastic parts. It involves injecting molten plastic material at high pressure into a mold cavity to give the desired shape. Injection pressure is a crucial parameter that determines the quality of injection molded parts. As a professional plastic injection molding manufacturer, I will share every thing about it.
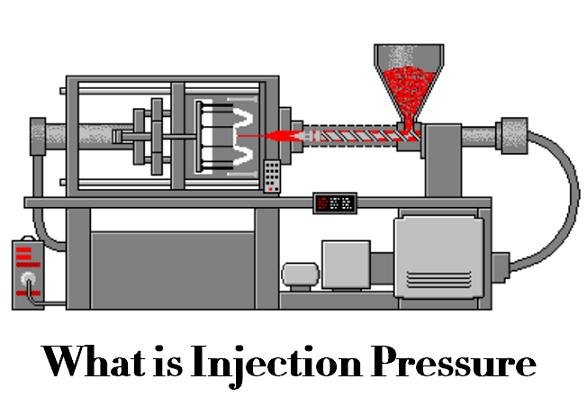
What is Injection Pressure?
Injection pressure refers to the amount of force applied by the injection molding machine through the screw or plunger to fill the mold with the molten plastic resin with a certain velocity and packing pressure. It is measured in units of Megapascals (MPa) or pounds per square inch (psi).
The magnitude of injection pressure depends on factors like:
- Type of plastic material – Higher viscosity materials require higher injection pressures
- Part design – Thicker and more complex parts need higher injection pressures
- Injection speed – Faster filling calls for higher injection pressure
- Mold temperature – Cooler molds require higher pressure
- Gate size – Smaller gates need higher injection pressures to overcome flow resistance
Typical injection pressures range from 35 MPa to 200 MPa depending on the application. Careful selection of injection pressure is key for high quality and consistent injection molded components.
Why is Controlling Injection Pressure Important?
Injection pressure must be adequately high to completely fill the mold cavity before the gate freezes off. If pressure is too low, it can lead to defects like short shots.
Excessively high injection pressure can also cause defects like flashing, jetting, excessive internal stresses, and even damage the mold. It can also degrade the plastic material due to overheating from excessive shearing.
By controlling injection pressure precisely, defects can be minimized while achieving complete cavity filling resulting in good replication of even the finest mold details on the injection molded part.
Properly set injection pressure enables production of good quality components consistently within specified cycle time and clamp tonnage limits of the injection molding machine.
Types of Pressures in Injection Molding Process
There are primarily three important pressure parameters encountered during the injection molding process:
1. Injection Pressure
This is the primary pressure exerted by the screw or plunger to fill the mold cavity during the filling phase. It fills the cavity up to 95-98% by volume.
Injection pressure depends on factors like plastic material viscosity, melt and mold temperatures, flow length, thickness, gate size etc. Typical range is 35-200 MPa.
2. Holding Pressure
Also called packing pressure, holding pressure is applied after the mold cavity is 97-98% filled during the packing phase. Holding pressure packs and compacts the material in the mold compensating for material shrinkage as it cools.
Typical holding pressure is 50-80% of injection pressure. Insufficient holding pressure can lead to sink marks and warpage in the molded part.
3. Back Pressure
This is the pressure maintained on the screw during plastication as the screw retracts. Creating some back pressure enhances mixing and homogenization of melt. However, excessive back pressure can degrade material.
Back pressure is typically below 20 MPa for commonly used injection molding materials.
How to Calculate Injection Pressure?
Injection pressure can be calculated using this formula:
P = k * Q / A
Where:
P – Injection pressure (MPa or psi)
k – Material dependent injection pressure coefficient
Q – Volumetric melt flow rate (cm3/s or in3/s)
A – Projected part surface area (cm2 or in2)
Let’s say we need to determine the injection pressure to mold a 4 x 4 x 0.1 inch part with flowing melt rate of 10 in3/s.
For Polypropylene k = 25000 psi
Projected part area A = 4 x 4 = 16 in2
Putting the values in the equation:
P = 25000 x 10 / 16
P = 15625 psi
So 15,625 psi injection pressure needs to be set on the injection molding machine to mold this particular part.
By adjusting the parameters in this injection pressure equation, you can determine the right pressure for your application.
How to Optimize Injection Pressure Settings?
Here are some tips to optimize injection pressure parameter:
- Start with material supplier’s recommendations and fine tune through scientific molding experiments
- Set higher injection pressures for complex, thicker parts and vice versa
- Use lower pressures for easy flowing materials like PP, PE. Higher values for PVC, Nylon, PC
- Reduce pressures if flashing or jetting type defects are seen
- Increase pressures if short shots, weak weld lines, sink marks are observed
- Use cavity pressure transducers for closed loop pressure control
- Maintain injection pressure profile – gradual increase in fill & pack phases
Continuous monitoring and corresponding adjustments of injection pressures are key for stable injection molding processes and consistent production of good quality components.
Conclusion
Injection pressure is a crucial injection molding process parameter than directly impacts the molded part quality and production efficiency. By properly controlling injection pressure per the application requirements, molding defects can be minimized, while achieving complete mold filling and good replication of mold details on the injection molded component.