Injection speed is one of the most important process parameters in injection molding. It refers to the speed at which the molten plastic material is injected into the mold cavity during the molding cycle. Proper control of injection speed is crucial for producing good quality parts efficiently. In this comprehensive guide, as a professional plastic injection molding manufacturer, I’ll be covering everything you need to know about injection speed in injection molding.
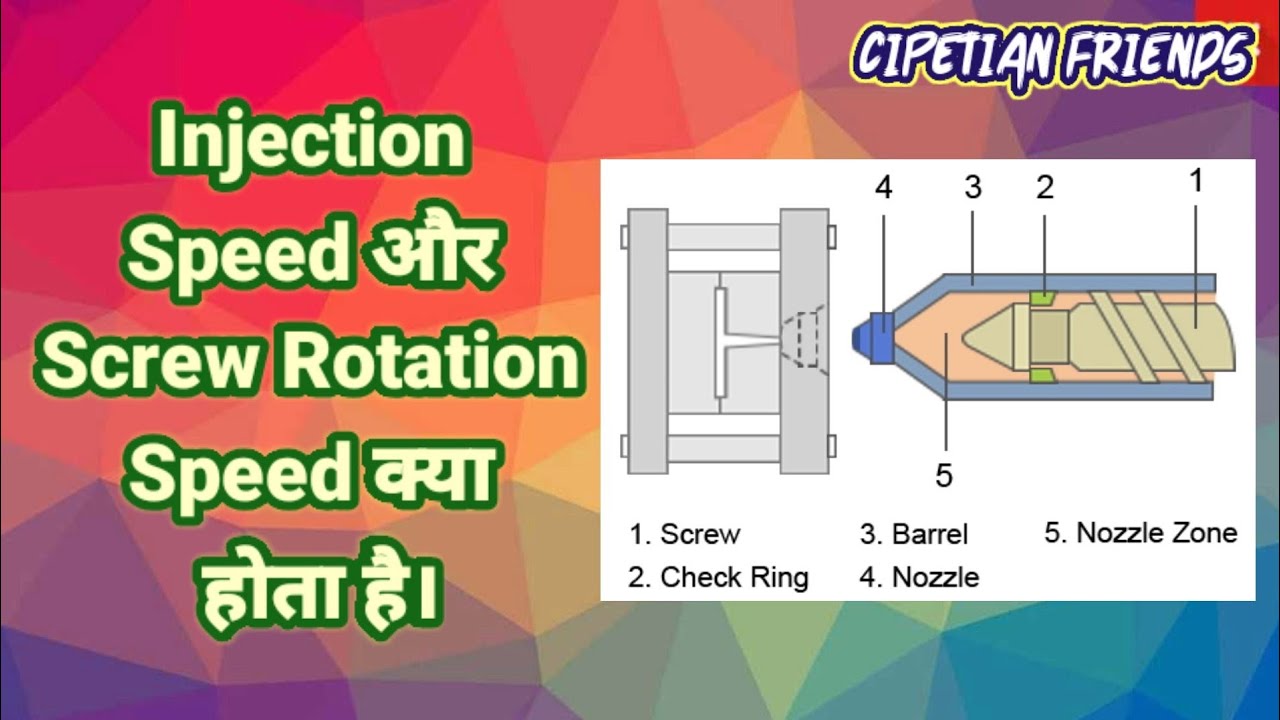
An Overview of Injection Speed
As mentioned, injection speed refers to the rate or velocity at which the molten plastic is introduced into the mold cavity. It is measured either as a linear speed (such as mm/s) which refers to the speed of the screw or plunger movement, or as a volume flow rate (cm3/s) which indicates the volume of material injected per unit time.
Typically, injection speed is categorized as slow (50-100mm/s), medium (100-250 mm/s) and fast or high speed (over 250mm/s). Most average-sized machines allow for injection speeds in the range of 50-500 mm/s. However, specialized machines for applications like micro-molding can use much faster speeds exceeding 1000mm/s.
Injection speed is a pivotal process parameter because it directly impacts the manner and effectiveness with which the mold cavity gets filled during the injection phase. An optimal injection speed ensures complete mold filling while a less-than-ideal speed causes defects.
As such, setting the right injection speed forms a balancing act based on factors like material type, melt and mold temperatures, part thickness, and flow length. Getting this parameter wrong can compromise the quality as well as the cost economics of the entire injection molding process.
Why Is Controlling Injection Speed Important?
There are several reasons why maintaining the proper injection speed holds significance:
- Influences mold filling patterns: The rate at which the molten plastic is introduced into the mold determines how the material spreads and fills up the cavity. An appropriate speed results in uniform flow while inadequate speeds cause uneven filling.
- Affects part quality and consistency: Injection speed has implications on crucial product properties like surface finish, strength, warpage control, and dimensional stability. The right speed enhances quality.
- Impacts molecular orientation: Faster filling induces greater molecular alignment along the flow direction. While moderate orientation improves strength, excessive speeds can cause warpage or shrinkage.
- Determines cycle efficiency: The filling time, which depends on injection speed, constitutes a primary component of the molding cycle. Optimized speeds shorten cycle times for improved productivity.
As such, accurately setting and controlling the injection speed forms a vital step in attaining defect-free, high-quality, and cost-effective production of injection molded components.
How Does Injection Speed Affect Part Quality?
Positive Effects of High Injection Speeds
Using an appropriately high injection speed provides certain benefits:
- Improves surface finish: Fast filling creates a glossier surface by rapidly transferring heat to the mold walls.
- Enhances visual quality: Rapid cavity filling minimizes flow marks, weld lines, and other appearance defects.
- Increase dimensional precision: Faster speeds improve the replication of mold details reducing post-molding shrinkage.
- Boosts strength: The rapid cooling achieved restricts molded-in stresses delivering higher mechanical properties.
Potential Drawbacks of Excessive Speeds
However, exceeding optimal speeds can also induce certain defects:
- Jetting issues: Too high velocities can produce a jetting effect causing surface defects like burn marks.
- Residual stresses: Rapid cooling and pressure buildup may create residual stresses in the molded parts.
- Air traps: Fast filling provides inadequate time for proper venting which can trap air bubbles.
- Warpage: The uncontrolled shrinkage and cooling with very high speeds often leads to warpage.
Therefore, while a reasonably high injection speed offers advantages, excessive velocities can be detrimental. Determining the sweet spot forms a vital aspect.
Process Optimization Using Scientific Injection Speed Selection
Optimally leveraging injection speed’s benefits while restricting its downsides involves adopting a scientific approach backed by factors like:
- Part design details: The section thickness, flow length ratio, layout of gates, and inserts guide appropriate speed selection.
- Material considerations: Depending on thermal sensitivity and viscosity, materials require distinct filling rate specifications.
- Machine capabilities: Parameters like maximum injection pressure and screw recovery influence feasible speeds.
- Precision monitoring: Real-time tracking of cavity pressure is indispensable for scientific speed control.
- Simulation modeling: Flow simulations help predict filling patterns directing optimal settings proactively.
By holistically analyzing these elements using advanced engineering tools paired with precision sensor-based monitoring, modern injection molding leverages injection speed judiciously for quality and efficiency.
The Concept of Multi-Stage Injection Speed
Pioneered for enhancing part quality by balancing high and low injection rates, multi-stage injection molding entails modulating the filling velocity over the entire molding sequence.
It divides the filling process into discrete stages defined by the instantaneous percent of cavity volume filled, with each segment utilizing a pre-set injection speed:
As observed, the speed trajectory progresses from slow, to fast, to medium or slow – aligning with the cavity geometry and material flow characteristics at specific fill percentages.
These optimized settings for each stage derive from the analysis of rheological principles and production trials. The segmented control enhances part quality while the high speeds in the middle accelerate cycle times.
By enabling fine-tuned modulation as per mold designs, multi-stage injection achieves optimal quality and efficiency – signifying a vital milestone in scientific advancement.
Key Takeaways About Injection Speed in Injection Molding
To summarize, regulating injection speed forms a pivotal processing condition for quality and consistency in injection molding:
- It indicates the rate of cavity filling central to product quality and efficiency.
- Optimized speeds ensure complete mold filling while inadequate velocities cause defects.
- Multifaceted analysis considering design, material, equipment, and process data is vital for selections.
- Precision monitoring and simulations enable proactive and scientific parameter adjustments.
- Multi-stage capabilities delivering fine modulation of velocities are indispensable for optimization.
Properly grasping these injection speed intricacies and harnessing advanced engineering techniques paves the path for molded product excellence.
In Summary
What is injection speed in injection molding? In a nutshell, it constitutes a vital processing parameter where both very high and very low velocities can be problematic – thus necessitating precision modulation enabled by multi-stage molding. A keen understanding of its implications paired with adopting engineering best practices holds the key to mastery.