Injection molding is one of the most common ways to manufacture plastic parts at scale. But did you know that injection molding can also be used for short production runs?
Low volume injection molding allows manufacturers to produce small batches of high-quality plastic components without the high costs associated with high-volume production.
If you’re wondering exactly what low volume injection molding is, how it works, and when you should use it, you’re in the right place. As a professional plastic injection molding manufacturer, I am writing this complete guide to teach you everything you need to know.
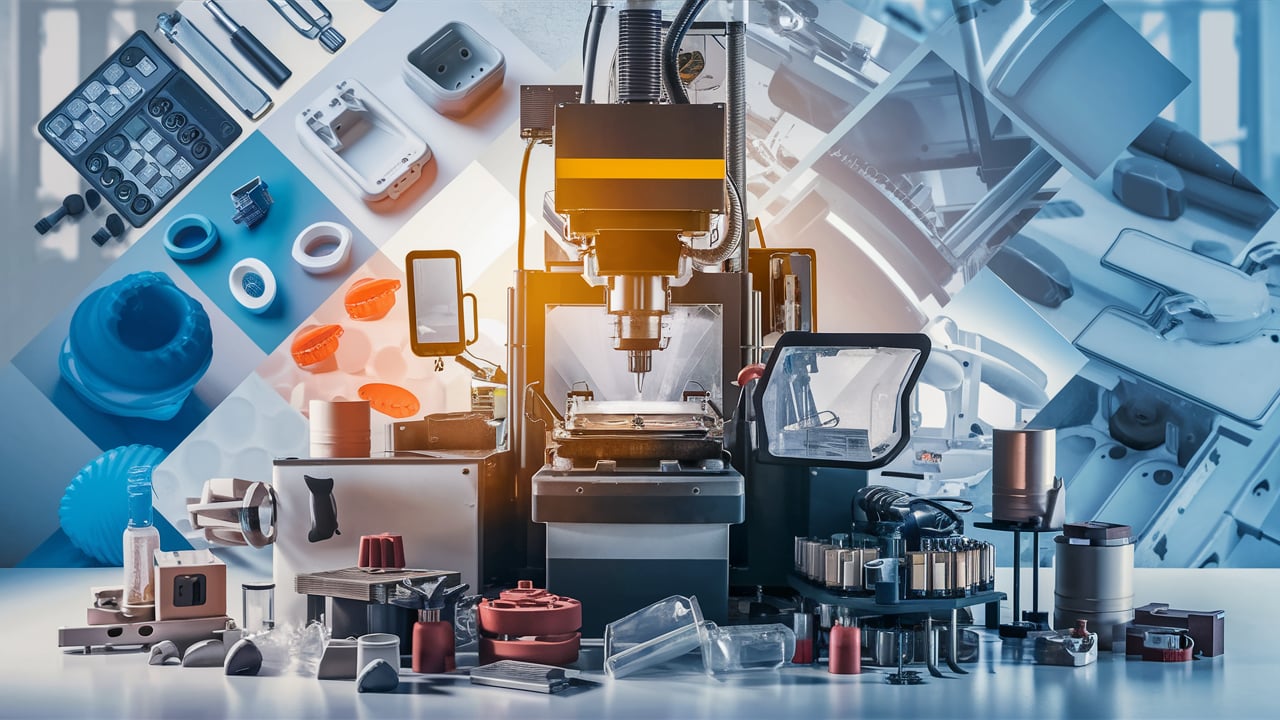
What is Low Volume Injection Molding?
Low volume injection molding refers to the production of small batches of plastic parts, typically less than 10,000 pieces per year. It leverages the same injection molding process used in high-volume manufacturing, but on a smaller scale.
Rather than producing hundreds of thousands or millions of identical plastic components, low volume injection molding creates smaller quantities in the range of 10 to 10,000 parts annually.
Low volume injection molding enables low-cost, high-quality plastic part production in small quantities. This makes it an ideal solution for companies that need small production runs for product testing, short-run manufacturing, or bridge production while scaling to higher volumes.
How Does Low Volume Injection Molding Work?
While high-volume injection molding relies on large machines and hardened steel tooling, low volume injection molding can use smaller equipment and softer aluminum molds to reduce costs. But otherwise, the overall process is the same.
Here are the main steps:
- Tool Design: An injection mold is designed, often with fewer cavities since only a small number of parts will be produced. Simple molds reduce tooling costs.
- Tool Production: Instead of steel, softer metals like aluminum are machined or manufactured using 3D printing to create the mold. This saves on material and machining costs.
- Mold Setting: The mold is set into the plastic injection molding machine and secured. Critical process parameters are set based on the material used.
- Injection Molding: Molten plastic is injected into the mold cavities under heat and pressure. It cools and solidifies into the finished parts.
- Part Ejection: The mold opens and ejector pins push the finished plastic parts out of the mold. Parts are then trimmed and undergo any secondary finishing.
So as you can see, low volume injection molding works much the same as traditional injection molding, just on a smaller scale. The main differences are the cheaper tooling and smaller equipment used.
What Materials Can Be Used?
Low volume injection molding can work with most standard thermoplastics, including:
- Polypropylene (PP)
- Acrylonitrile butadiene styrene (ABS)
- Polycarbonate (PC)
- Nylon (PA)
Specialty plastics are also options but the minimum order quantities (MOQ) are higher since less material is used overall in lower volume production.
The choice depends largely on part performance requirements and production volume. Lower volume jobs lend themselves better to cheaper resins like PP.
Benefits of Low Volume Injection Molding
There are several key benefits that make low volume injection molding an attractive choice over other manufacturing methods:
1. Lower Startup and Production Costs
Because low volume injection molding uses simpler, cheaper molds and smaller equipment, the startup and production costs per part are substantially lower. This makes short production runs much more economical.
2. High Production Quality
Despite lower costs, low volume injection molding maintains the same high levels of repeatability, precision, and quality as high-volume production. Parts perform identically to their high-volume counterparts.
3. Faster Lead Times
With simpler molds and tools, low volume injection molding providers can deliver parts much faster than high-volume production. Lead times are shorter since there is less tooling work required.
4. Design Flexibility
The lower tooling investment also affords greater flexibility when iterating part designs. Design changes can be made without expensive steel mold reworks, saving time and money.
5. Scalable for Higher Volumes
Low volume injection molding production can be used as initial bridge manufacturing while scaling up to full mass production volumes. Companies save money prior to committing to high-volume injection molding.
When Should You Use Low Volume Injection Molding?
There are several situations where low volume injection molding shines compared to conventional mass-scale injection molding:
1. Short-Run Production
For short manufacturing runs where hundreds to a few thousand plastic parts are required, often as a bridge to higher volumes, low volume injection molding reduces the high cost of small batch production. The lower tooling investment pays off with runs under ~10,000 parts.
2. Design Verification & Testing
Producing parts identical to the final design using the actual production process enables comprehensive testing and verification before investing in high-volume tooling. Companies confirm part design and performance prior to mass production.
3. Custom/On-Demand Manufacturing
For bespoke or custom plastic part orders where buyers want specialized small-batch components, low volume manufacturing is ideal. It allows cost-effective production identical to high-volume processes and materials.
4. Rapid Prototyping
While 3D printing excels for early stage prototyping, low volume injection molding enables more refined pre-production plastic prototypes identical to the final mass manufactured components. Critical performance attributes can be tested.
So in summary, low volume injection molding excels at small batch production where high precision and repeatability is still needed without the high costs of conventional mass production injection molding tools and equipment.
Finding the Right Low Volume Injection Molding Partner
Choosing the right low volume injection molding partner is key to ensuring high quality parts delivered reliably within your project’s timeframe and budget. Here are some tips:
1. Make Sure They Specialize in Low Volume Molding
Not all injection molders work in lower volumes. Seek out an expert who specializes in low volume and has optimized their process around smaller batch jobs. They’ll better understand the unique requirements.
2. Look for Quick Turnaround Capabilities
Since speed is one of the advantages of low volume injection molding, find a shop that can deliver parts rapidly. Ask about their typical lead times for both new tooling and production.
3. Review Their Past Project Case Studies
Vet potential partners by looking at case studies of past small batch injection molding jobs they have completed. Make sure they have expertise across different applications with different materials, part geometries, and volumes.
4. Make Sure They Offer Design & Engineering Support
To ensure manufacturable part designs optimized for their process, select a shop that provides upfront DFM analysis and engineering collaboration to preempt production issues.
Conclusion
I hope this guide gave you a comprehensive overview explaining what exactly low volume injection molding manufacturing is all about.
The key takeaways are:
- It enables small production runs of 10-10,000 high quality plastic parts per year
- Leverages injection molding but with smaller/cheaper molds and equipment
- Substantially lowers costs for short runs vs. high-volume production
- Maintains identical precision, repeatability and performance
- Ideal for design testing, short-run production, custom orders
To recap, low volume injection molding bridges the gap between prototyping and mass production. It makes short batch plastic part production affordable without sacrificing quality.
What is low volume injection molding? It’s an indispensable manufacturing solution for companies that require low-cost plastic component production at volumes under 10k parts per year.