Plasticizing is a crucial step in the injection molding process that prepares plastic resin for molding by converting it from a solid to a molten state. In this comprehensive guide, as a professional plastic injection molding manufacturer, we’ll break down exactly what plasticizing entails and why it’s so important for creating high-quality injection molded parts.
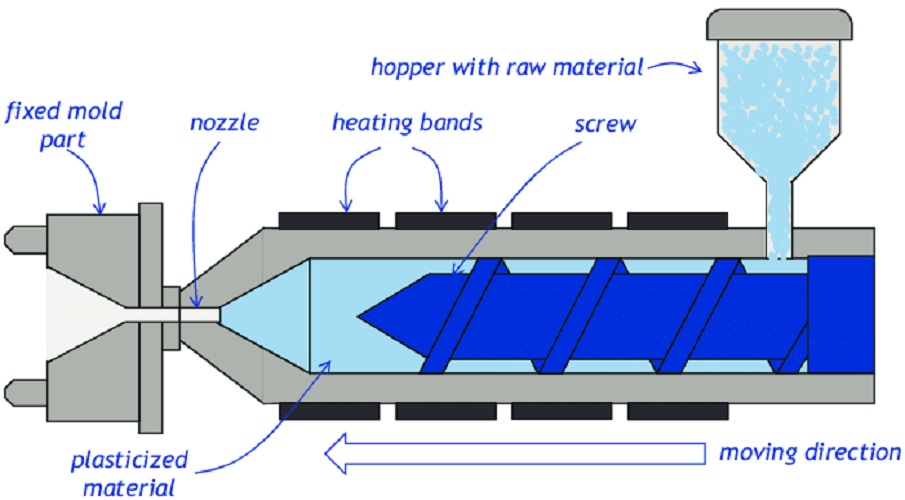
What is Plasticizing in Injection Molding?
Plasticizing refers to the process of melting plastic resin pellets and mixing them until they become a homogeneous molten liquid that can be injected into a mold. It is one of the initial steps of injection molding, taking place before the plastic enters the mold cavity.
Proper plasticizing is essential for producing strong, consistent parts with good surface finishes. If the plastic isn’t thoroughly melted and mixed, it can lead to visual defects, structural weaknesses, and inconsistencies between parts.
During plasticizing, plastic pellets are fed into a heated barrel and rotated by a screw. The mechanical friction and external heat melt the plastic, while the screw mixing ensures uniform temperatures and viscosity. Once plasticized, the molten plastic can be injected at a controlled rate and pressure to fill the mold cavity.
Why is Plasticizing Important?
Plastic that isn’t thoroughly plasticized will fail to fill the intricate details of an injection mold, reducing part quality. Here are some of the main reasons plasticizing is a critical step:
- Ensures proper melting and mixing of polymer chains
- Achieves uniform temperature and viscosity
- Allows complete mold filling without obstructions
- Enables strength and flexibility required for part function
- Provides smooth surface finish free of visual defects
In a nutshell, comprehensive plasticizing eliminates issues that would otherwise undermine the cosmetic appearance and mechanical performance of injection molded components.
How Does the Plasticizing Process Work?
Plasticizing occurs inside the injection molding machine’s heated barrel through the combined effects of:
- Frictional Heat: Generated by the rotating screw’s shearing forces.
- External Heat: Added through barrel temperature controls.
- Mixing: Provided by the screw geometry.
As plastic pellets enter the barrel from the hopper, they encounter three distinct zones that each facilitate melting, mixing, and melt accumulation:
1. Feed Zone
Pellets are fed into the barrel and conveyed forward by the rotating screw. Minimal melting occurs here, largely from conducted heat through the barrel walls.
2. Compression Zone
The space between screw flights narrows, increasing pressure and shearing forces/heat. This starts melting the outer layers of the pellets.
3. Metering Zone
Extreme shear from smaller screw channels and highest temps melt pellets completely into a liquid matrix. Thorough mixing results in a homogeneous melt ready for injection.
Tuning the barrel temperatures, screw RPM, and back pressure allows processors to dial in settings that deliver a uniform plastic melt to the mold. The plasticizing process culminates as the screw injects the molten resin through the nozzle, sprue bushing, and runner system into the awaiting mold cavity.
Plasticizing Issues and How to Fix Them
To achieve flawless, consistent parts through injection molding, plasticizing must prepare material to precisely meet viscosity, temperature, and flow characteristics. Here are some common plasticizing problems and troubleshooting tips:
Overheated Material
- Causes: Excessive barrel heat, screw RPM too high
- Solutions: Lower barrel temperatures, reduce screw RPM
Undermelted Material
- Causes: Low barrel heat, low screw RPM
- Solutions: Increase heat and screw RPM to improve melt factor
Non-uniform melt
- Causes: Inadequate mixing and residency time
- Solutions: Slow down injection, increase back pressure
Material Degradation
- Causes: Too much shear heat history
- Solutions: Increase feed rates, lower screw RPM
Black Specks in Parts
- Cause: Material overheated and degraded
- Solution: Lower barrel temps and screw RPM
Careful adjustment of plasticizing parameters allows molders to hone in on the optimal material preparation that permits complete mold filling without degrading the resin.
Takeaways on Plasticizing in Injection Molding
- Plasticizing converts plastic pellets into a molten state prior to injection through frictional an external heating combined with mixing.
- It is a critical step enabling proper mold filling and quality component production through injection molding.
- During plasticizing, plastic resin passes through specialized screw zones allowing melting, pressure buildup, and mixing.
- Precise heat, pressure, screw speed, and residency time adjustments are needed to achieve ideal viscosity, temps, and flow properties without material degradation.
Understanding plasticizing helps molders control this sensitive process to achieve high yields of defect-free, robust injection molded components. With thorough plastic preparation, intricate molds can be filled repeatably to fully realize part design performance potential.