Screw speed is one of the most critical yet often overlooked parameters in the injection molding process. As a professional plastic injection molding manufacturer, I will explain what screw speed is, why it’s important, how to set and control it properly, and the consequences of incorrect screw speed settings in this comprehensive guide.
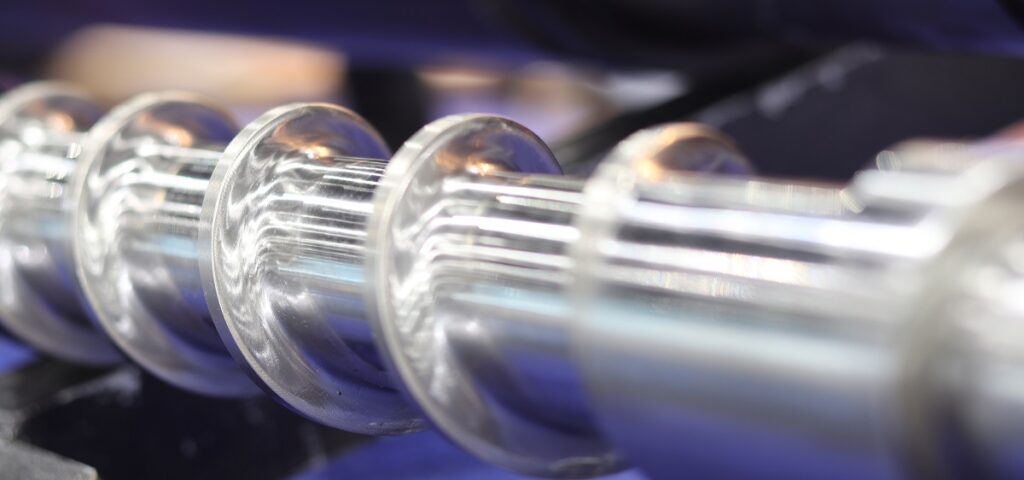
What Exactly is Screw Speed in Injection Molding?
Simply put, screw speed refers to the rotational speed of the screw inside the injection molding machine’s barrel during the plasticizing phase. This is typically measured in revolutions per minute (RPM).
The screw rotates and reciprocates to convey solid plastic pellets forward, melt them into a uniform fluid state, and then inject the molten plastic into the mold cavity under pressure. So the rate of rotation directly impacts the quality and consistency of the melted plastic that gets injected.
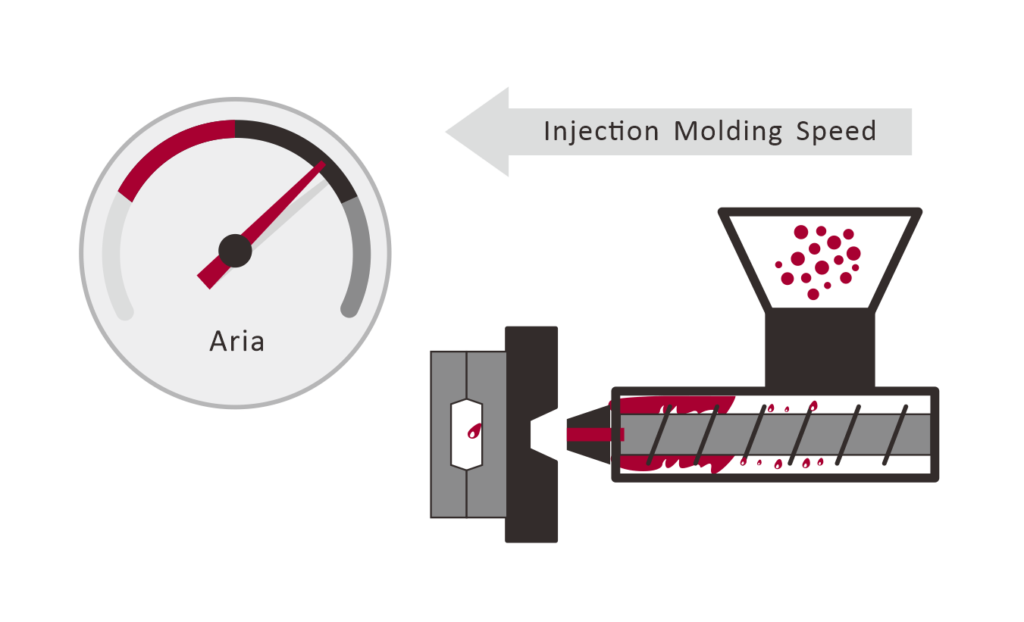
Why Is Controlling Screw Speed So Important?
Properly setting and controlling screw speed is pivotal because it affects several crucial aspects:
- Melt Quality: Faster screw rotation provides more shear heating and mixing action, ensuring thorough homogenization. Slower speeds can leave unmelted particles.
- Temperature Control: Screw speed significantly influences the shear heat generated during plasticization. This affects maintaining optimal melt temperatures.
- Cycle Time: Optimizing screw rotational rates can help reduce cycle times by balancing plasticizing duration with other stages.
- Material Properties: Appropriate screw speeds preserve the base resin’s key characteristics like strength, flexibility, shrinkage rate, etc. Excess speeds can degrade polymers.
So in a nutshell, screw speed settings directly impact the quality, efficiency, and economics of the entire injection molding process. Even minor variations can be hugely detrimental.
What Factors Influence Optimal Screw Speeds?
There is no universally ideal screw speed setting. The optimal value depends on several factors:
Type of Material
- Every plastic material has distinct rheological behaviors, melting points, viscosities, flow properties, etc. So each one needs customized screw speeds.
Screw Design
- Diameter, length, channel depth, and overall screw geometry impact how plastic is conveyed and sheared during melting. So the rotational speed must align with the screw design.
Part Design and Specifications
- Dimensional precision needs, wall thickness variations, flow length, venting requirements, etc. necessitate specific melt quality. So the screw speed has to be set accordingly.
Injection Molding Machine Capabilities
- The machine’s maximum shot size, plasticization rate, torque, clamping force, etc. constrain the workable speed ranges.
Step-by-Step Guide to Setting and Controlling Screw Speed
Follow this methodical approach to dial in the optimal screw speeds:
Baseline and Trials
- Start with the material supplier’s recommendation as an initial baseline for screw RPM.
- Conduct short experimental runs across a range of speed settings in small increments or reductions from the baseline.
- Keenly observe corresponding changes in cycle times, melt temperature stability, part surface finish, occurrence of defects, etc. with each iteration.
- Plot the data to determine the preliminary optimal setting based on your product requirements.
Optimization and Refinement
- Carry out further fine-tuning centered around the newly identified optimal value.
- Continue monitoring critical process parameters and product quality attributes.
- Use feedback data for any necessary adjustments to achieve a “sweet spot”.
- Periodically validate to ensure consistency.![Screw speed injection molding graph][]
Real-time Monitoring and Control
- Employ computerized monitoring and control systems.
- They measure screw RPMs, melt temperatures, pressures, etc. in real-time.
- Critical for instant, automated adjustments to maintain optimal process stability.
Rechecking and Documentation
- Revalidate optimal screw speeds whenever changing materials or molds.
- Properly document all finalized parameter settings for future troubleshooting, efficiency, training purposes, etc.
In essence, determining screw speeds requires an iterative approach grounded in scientific principles and data-backed decision making.
What Happens If Screw Speeds Are Too High or Too Low?
Deviating from the optimal range in either direction can detrimentally impact quality, productivity, costs, and profitability.
Consequences of Excessive Screw Speeds
- Thermal degradation due to overheating, discoloration
- Higher-molecular-weight polymer breakdown
- Excessive shear rates causing loss of mechanical properties
- Air entrapment increasing chances of blowholes
- Higher energy consumption and operating costs
Consequences of Insufficient Screw Speeds
- Inadequate plasticization giving unmelted solid particles
- Non-uniform melt distribution and composition
- Longer cycle times reducing productivity efficiency
- Improper fusion causing structural weaknesses
- Gate freeze-off blocking flow triggering short shots
Therefore, injection molding facilities must emphasize the meticulous monitoring and control of screw rotational speeds. Minor inconsistencies can quickly spiral out of control into bigger part defects or process instabilities.
Staying within the optimal range is crucial for reaping maximum productivity at minimal costs.
Expert Tips for Injection Molding Success
Here are some pro tips when dealing with screw speeds:
- Invest in upgraded machines with advanced computerized control systems for automation, data analytics, and precision.
- Ensure proper specific screw designs for different materials instead of one-size-fits-all approaches.
- Train operators extensively and consistently on screw speed optimization techniques.
- Schedule preventative maintenance checks on screw and barrel wear to sustain melt consistency.
- Implement stringent quality control protocols for part dimensional conformance tracking.
- Frequently review process data to identify any deviations from optimal settings.
The Bottom Line
At its core, screw speed represents the pivotal rhythm of the injection molding process. Much like a symphony, every section has to flawlessly play their role at the right tempo.
Master injection molders precisely calibrate screw rotational velocity to keep this rhythm going. It takes experience, control, and a passion for perfection. But the rewards of enhanced quality, efficiency, and profitability are worth the effort.
So whether starting up or tuning an existing process, never forget this mantra – “It’s all about the speed and feed.”