Injection molding is one of the most popular manufacturing processes for plastic parts, from tiny Legos to car bumpers and dashboard components. But despite how commonplace the technology is, many people don’t understand what happens after molten plastic is injected into a mold.
One of the inherent behaviors of plastic is that it shrinks significantly as it cools. This shrinkage isn’t just a change in dimensions but it can also cause internal stresses that lead to warpage, a distortion of the geometry or dimensions of a part.
Managing and reducing shrinkage is an essential aspect of designing and manufacturing intricate plastic parts that maintain tight tolerances over the life of a product. In this guide, as a professional plastic injection molding manufacturer, I will share what causes injection molding shrinkage, how it can be predicted and controlled, and strategies for reducing defects in your parts.
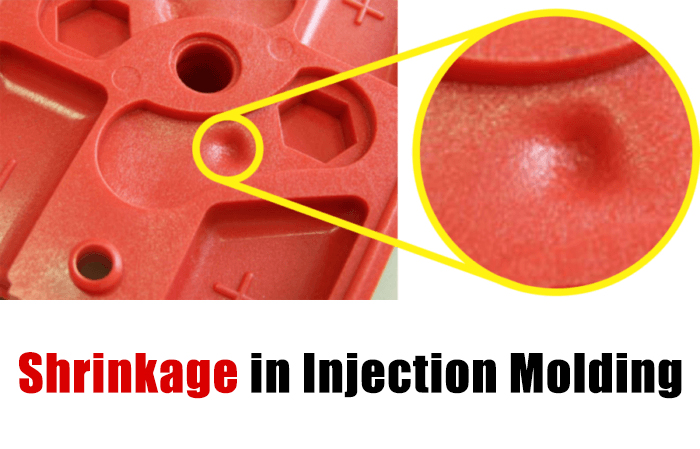
What Is Shrinkage in Injection Molding?
Shrinkage refers to the contraction of a plastic molded component as it cools after injection in an injection molding machine. Generally, plastic polymers will shrink between 2-4% although this can range from 0.5% up to 10% depending on the plastic, reinforcement additives like glass fibers, and details like wall thickness. It’s impossible to completely eliminate shrinkage so it must be accounted for during the design of plastic parts.
In the most extreme cases, uneven shrinkage called warpage can distort parts to point that they won’t fit within specified tolerances. But warpage can appear in very subtle ways as slight bends or twists invisible to the human eye—so managing shrinkage through design and processing choices is fundamental.
The dynamics of shrinkage and its impact depend on a combination of:
- Polymer composition: How the molecules react to changes in temperature and pressure which influences directional shrinkage tendencies. Amorphous polymers like ABS have more uniform while semi-crystalline plastics like PE and PP anisotropic behaviors.
- Melt temperatures: Higher melt temperatures generally increase shrinkage due to expansion of polymer chains.
- Mold temperatures: Faster cooling increases internal stresses. Hotter molds allow more relaxation of molecules before freezing in place.
- Molecular weight distribution: Higher weight polymers tend to shrink more.
- Presence of fillers/reinforcement: Fibers restrict shrinkage along their orientation. Mineral fillers lower shrinkage overall.
- Geometry factors: Like wall thickness, ribs, etc. Thicker areas shrink more than thinner areas potentially causing distortions.
Why Does Plastic Shrink?
To understand what drives shrinkage, it’s important to first look what happens to polymers at the molecular level as they transition through the injection molding process.
Molecular Behavior in Plastics
Plastics contain long molecular chains of repeated units bonded together known as polymers. The behavior of these chains—how orderly they pack together—determines if a material is amorphous or semi-crystalline.
Amorphous polymers have a randomly coiled structure without any repeating organization between chains. When heated amorphous polymers form a free-flowing liquid as molecules spread apart. Cooling allows the tangled chains to move closer, shrink down, and solidify in place but never arrange into ordered structures.
Common amorphous plastics:
- Acrylonitrile butadiene styrene (ABS)
- Polycarbonate (PC)
- Polystyrene (PS)
Semi-crystalline plastics contain areas where molecular chains pack together forming ordered crystalline regions while other areas remain amorphous.
When heated, the crystalline areas melt into the amorphous regions but molecules still mostly point in the same directions. As cooling takes place ordered crystalline structures reforms pulling molecules into a smaller volume—that’s where shrinkage comes from.
Common semi-crystalline plastics:
- Polyethylene (PE)
- Polypropylene (PP)
- Nylon (PA)
The high degree molecular alignment of semi-crystalline materials causes shrinkage perpendicular to flow while amorphous polymers shrink along flow directions.
How Molding Process Causes Shrinkage
Now relating back to injection molding—how do machine and mold conditions lead to shrinkage?
As plastic enters a heated barrel, shear forces breaks up crystalline regions while heating allows molecular chains to spread out increasing free volume.
Next, the molten polymer gets forced at high pressure and velocity into a relatively cooler mold cavity that restricts movement perpendicular to the flow direction. Molecules align along the direction of flow like spaghetti through a nozzle.
With semi-crystalline plastics as temperature drops ordered structures begins forming again. The realigning molecules have less free volume leading them to pull tighter—shrinking the plastic.
Additionally residual stresses develop between the hotter core and cooler surface regions restrained by rigid mold walls. Parts will try relieving these stresses as they continue cooling once ejected from the mold potentially causing warpage.
Where Does Shrinkage Occur?
The majority of shrinkage transpires while cooling inside the mold although a smaller amount can occur after ejection as temperature fully stabilizes.
Post-mold shrinkage depends on a few factors:
- Processing conditions like injection speed, pressure, and temperature
- How fast surface layers solidify restricting molecular movement
- Level of residual stresses
For example with amorphous plastics like PC and ABS more shrinkage takes place outside the mold as interior sections remain molten longer allowing relaxation of polymer chains. Or very thin parts solidify faster build less internal stresses.
Predicting and Measuring Shrinkage Rates
Each plastic material will shrink differently under various conditions. So the first step understanding how a part might distort is accurately determining shrinkage rates.
Shrinkage is measured as a percentage change between dimensions of the injection molded part compared to the tool steel mold: Shrinkage (%) = (Mold dimension - Part dimension) / Mold dimension x 100
Most plastic resin manufacturers provide shrinkage data in material datasheets although testing under your exact production parameters is ideal. Typical shrinkage values range between:
- Amorphous polymers: 0.3-0.7%
- Semi-crystalline plastics: Around 2%
Keep in mind processing details influence shrinkage for a given plastic. Changes to injection speed, temperature, pressure and more can all impact the shrinkage rate.
How Simulation Software Predicts Shrinkage Rates
Specialized simulation software can model the injection molding process for a specific plastic part design to predict behaviors like shrinkage. They work by digitally mimicking factors like:
- Rheological properties of the plastic
- Molding machine performance
- Temperatures, speeds, pressures
- Geometry of the part
As a result engineers can visualize shrinkage tendencies and warpage risks of their design. This enables making tweaks before committing to expensive mold tooling.
Simulation also aids determining the best compromise between properties needed for functionality against distortional defects from shrinkage. Changes might involve modifying geometry, gate locations, or even secondary operations.
How to Control Injection Molding Shrinkage
Eliminating shrinkage completely is nearly impossible with plastics. However, through intentional design and process decisions it can be minimized enough to manufacture dimensionally robust, functional parts.
Strategies to Reduce Plastic Shrinkage
Here are some best practice strategies used to reduce shrinkage defects:
1. Getting fill, pack, and cooling balance right
Fill too fast – Encourages molecule alignment risking anisotropic shrinkage.
Pack inadequately – Leads to part’s inner sections collapsing unpredictably once ejected.
Cool too quickly – Causes varying shrinkage across thick and thin areas leading to warpage.
2. Increasing mold temperature
Allows relaxation of polymer chains before complete solidification reducing internal stresses. Often 30-50°C below melt temperature is ideal.
3. Using hot runner systems
Hot runners keeps the sprues and runners molten eliminating cold slugs reducing flow length requirement allowing optimization for part sections.
4. Adding glass fibers
At around 30% cutoff by weight fibers hinder shrinkage providing reinforcement. Although reduces impact strength.
5. Include proper mold venting
Venting prevents air becoming trapped in the cavity during fill encouraging complete packing for uniform shrinkage.
6. Using gas-assisted injection molding
Compressed gas is injected into the cavity pushing material against walls improving replication and dimensional accuracy. The pressure drives shrinkage into small intended hollow channels.
7. Overpacking high shrink zones
Typically areas against flow direction see higher shrinkage as molecules relax. This can be compensated with intentionally higher packing.
Design Rules to Minimize Uneven Shrinkage
Engineering proper part geometries contribute enormously towards stability as plastic contracts when cooling. Some design guidelines helping reduce uneven shrinkage include:
- Setting overall wall thickness optimally thin as possible for adequate strength. Thick zones see greater shrinkage compared to thin areas.
- Restricting variance in wall thickness across single parts keeping sections uniform. Sudden changes cause preferential shrinking distorting thinner areas.
- Including proper draft angles on vertical walls allowing even contraction when ejecting preventing sticking.
- Positioning weld and meld lines away from high appearance or tolerance zones. These areas intrinsically prone to inconsistent shrinkage.
- Using ribs or supports structures with thin profile details only where needed managing bulk. Ribs help limit differential contractions across larger walls but add extra mass if not required.