In injection molding, tonnage refers to the clamping force of the injection molding machine. It determines how much pressure can be applied to keep the mold closed during the injection of molten plastic.
Understanding tonnage is key for producing high-quality plastic parts efficiently. In this complete guide, as a professional plastic injection molding manufacturer, I’ll cover everything you need to know about tonnage in injection molding.
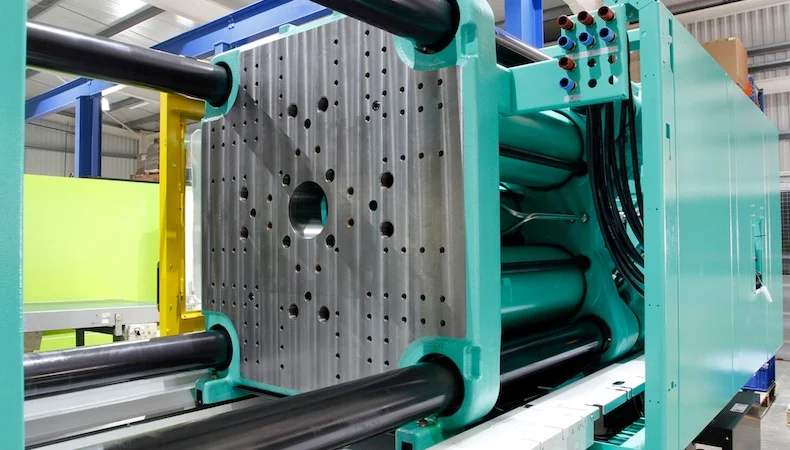
What is Tonnage in Injection Molding?
Tonnage is the measure of force, measured in tons, that an injection molding machine can exert to hold the mold closed during the injection process. The tonnage indicates the size of the machine – higher tonnage equates to a larger machine. For example, a 3000 ton machine can apply 3000 tons of clamping force.
Without enough clamping force, the pressure of the injected molten plastic would cause the mold to open, resulting in defects like flash, short shots, and inconsistent part dimensions.
Why is Tonnage Important in Injection Molding?
There are several reasons why calculating the right tonnage is critically important:
Preventing Part Defects
With inadequate tonnage, the mold will open slightly during injection, leading to defects like flash, short shots, and uneven part walls.
Excess tonnage can also cause defects like burns, discoloration, and ejection marks.
Optimizing Production Capacity
Selecting a machine with insufficient tonnage limits the number and size of parts that can be produced.
Conversely, oversized machines are expensive and inefficient. Accurately determining tonnage ensures optimized production capacity.
Matching Specific Applications
The tonnage must align with the size and complexity of each project. Using improper tonnage can result in wasted material, time, and money.
Extending Machine and Mold Lifespan
Too little tonnage over taxes both the machine and mold by straining them. Too much unnecessarily accelerates wear. Proper tonnage prevents premature breakdowns.
How to Calculate Tonnage Needed for Injection Molding
While there are advanced computer simulations that can determine tonnage, here is the basic manual formula:
Tonnage = Clamping Factor × Projected Area
Step 1: Calculate Projected Area
The projected area is the total surface area of the parts and runners that the plastic pressure pushes against when trying to open the mold.
To simplify, it can be thought of as the top-down area visible when the mold is closed.
Projected area is calculated by length x width for each cavity, then summed with the runner areas.
Step 2: Determine Clamping Factor
The clamping factor represents the pressure required to keep the mold closed during injection and packing. It varies by plastic type from 2 tons/sq. in for easy flowing materials like nylon to 8 tons/sq. in for challenging resins like glass filled compounds.
Material manufacturers recommend appropriate clamping factors. When uncertain, use 4 tons/sq. in.
Step 3. Calculate Tonnage
With the clamping factor and total projected area determined, simply multiply them together:
Tonnage = Clamping factor (tons/sq. in) x Total projected area (sq. in)
Then add 10-15% as a safety buffer.
Now you have the minimum tonnage required to prevent flash and other defects caused by inadequate clamping force.
Real-World Tonnage Calculation Example
Let’s go through an example tonnage calculation for an injection molded part to see how this works:
- 4 cavities
- Each cavity 5 in x 5 in = 25 sq. in
- Total area of cavities = 4 x 25 sq. in = 100 sq. in
- Runner system area = 12 sq. in
- Projected area = 100 + 12 = 112 sq. in
- Material: Polypropylene, clamp factor = 3 tons/sq. in
- Tonnage = 3 tons/sq. in x 112 sq. in = 336 tons
- With 15% safety buffer, total tonnage = 336 x 1.15 = 386 tons
Therefore, the minimum sized injection molding machine required is one with 386 tons of clamp force. Going with the next machine size up is recommended, so a 400 ton machine would be well suited for this mold.
Accurately determining injection molding machine tonnage sets your manufacturing process up for success. I hope this guide provides insight into this critical but often overlooked factor. Let me know if you have any other questions!