If you’ve ever wondered how plastic packaging, car dashboards, or even dental retainers are made, you’re about to discover the answer.
It’s called vacuum forming. And it’s one of the most versatile manufacturing processes on the planet.
In fact, vacuum forming is responsible for creating thousands of plastic products you use every day. From the blister pack protecting your new headphones to the interior panels in your car.
But here’s the thing:
Most people have no idea what vacuum forming plastic actually is. Or how it works.
That’s why I put together this complete guide.
In this post, as a professional plastic vacuum forming manufacturer, I will talk about:
- Exactly what vacuum forming is (and why it matters)
- How the vacuum forming process works step-by-step
- The key benefits and limitations you need to know
- Real-world applications across different industries
- Materials that work best for vacuum forming
- When to choose vacuum forming over other methods
Let’s dive right in.
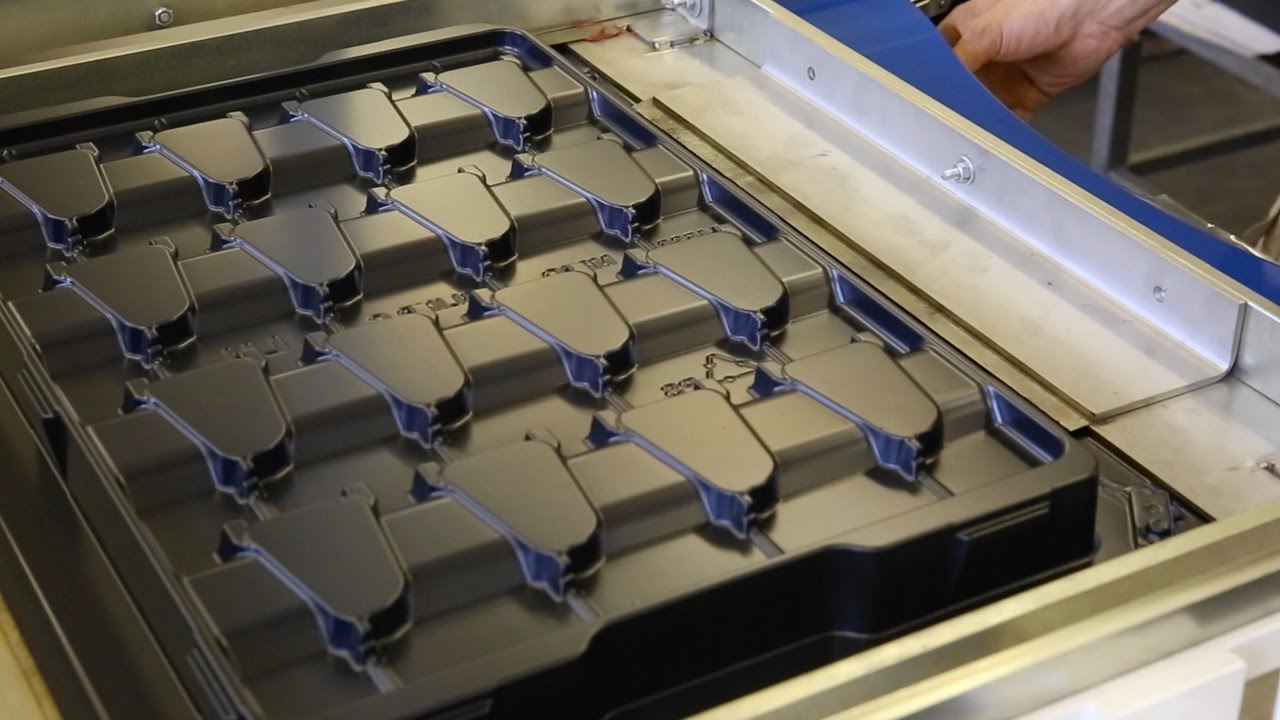
What Exactly Is Vacuum Forming?
Vacuum forming is a manufacturing process where you heat a plastic sheet until it’s soft, then use vacuum pressure to shape it over a mold.
Think of it like this:
You take a flat piece of plastic. Heat it up until it’s flexible. Then drape it over a mold and suck out all the air. The plastic sheet gets pulled tight against the mold surface, copying every detail.
Once it cools down? You’ve got a perfectly formed plastic part.
Simple, right?
Well, yes and no.
The basic concept is straightforward. But modern vacuum forming has evolved into a sophisticated process that can create incredibly detailed parts.
Here’s what makes vacuum forming unique:
It only shapes one side of the plastic. Unlike injection molding that creates fully enclosed parts, vacuum forming only creates detail on the side touching the mold.
It uses existing plastic sheets. You’re not melting plastic pellets and injecting them. You’re taking pre-made sheets and reshaping them.
It relies on atmospheric pressure. The “vacuum” part removes air between the plastic and mold. Then normal air pressure does the heavy lifting to push the plastic into place.
The process has been around since the 1940s. But it’s still one of the most cost-effective ways to create plastic parts today.
The Step-by-Step Vacuum Forming Process
So how does vacuum forming actually work?
Let me break it down into six simple steps:
Step 1: Clamp the Plastic Sheet
First, you load a plastic sheet into the machine’s clamping frame. This frame holds the edges of the sheet securely during the entire process.
The clamping pressure needs to be just right. Too loose and the plastic will slip. Too tight and you might damage the material.
Step 2: Heat the Plastic
Next, heating elements warm the plastic sheet from above (and sometimes below for thicker materials).
The temperature varies based on the plastic type. But we’re typically talking about 300-400°F for most thermoplastics.
Here’s the critical part:
The plastic needs to reach its “forming temperature” – hot enough to be flexible but not so hot that it starts to degrade.
Step 3: Position the Mold
Once the plastic reaches the right temperature, the mold moves into position beneath the heated sheet.
There are two types of molds:
- Male molds (convex) – The plastic drapes over the outside
- Female molds (concave) – The plastic gets pulled into the cavity
Step 4: Apply the Vacuum
This is where the magic happens.
A vacuum pump removes the air between the heated plastic and the mold surface. The pressure difference causes the plastic to get sucked tightly against every contour of the mold.
We’re talking about 27 inches of mercury – that’s serious suction power.
Step 5: Cool and Set
With the plastic formed to the mold, cooling begins. Some machines use fans or water mist to speed this up.
The plastic needs to cool below its heat deflection temperature before removal. Otherwise, it’ll warp or lose its shape.
Step 6: Release and Trim
Finally, the formed part gets released from the mold. Any excess material around the edges gets trimmed away.
Depending on the application, you might need additional finishing like drilling holes or adding texture.
The entire cycle can take anywhere from a few minutes to half an hour, depending on material thickness and part complexity.
Materials That Work With Vacuum Forming
Not all plastics are created equal when it comes to vacuum forming.
You need thermoplastics – materials that soften when heated and harden when cooled. And they need to maintain their properties through multiple heat cycles.
Here are the most popular vacuum forming materials:
ABS (Acrylonitrile Butadiene Styrene)
The workhorse of vacuum forming. ABS offers excellent impact resistance, good detail reproduction, and moderate cost. Perfect for automotive parts and electronic housings.
PETG (Polyethylene Terephthalate Glycol)
Crystal clear with great chemical resistance. PETG is your go-to for retail packaging and medical applications where visibility matters.
HIPS (High Impact Polystyrene)
Affordable and easy to form. HIPS works great for prototypes, signage, and light-duty applications.
Polycarbonate (PC)
When you need serious durability. PC offers outstanding impact strength and heat resistance. Think safety equipment and outdoor applications.
Acrylic (PMMA)
For when appearance is everything. Acrylic provides optical clarity and weather resistance. Common in displays and lighting fixtures.
PVC (Polyvinyl Chloride)
Chemical resistant and flame retardant. PVC suits industrial applications and outdoor signage.
The thickness typically ranges from 0.5mm to 10mm. Anything thicker becomes challenging to heat uniformly.
Key Benefits of Vacuum Forming
Why do manufacturers choose vacuum forming over other plastic forming methods?
The benefits are pretty compelling:
Lower Tooling Costs
Here’s the big one: vacuum forming molds cost a fraction of injection molding tools.
We’re talking $5,000 for a vacuum forming mold versus $50,000+ for an injection mold. That’s a game-changer for smaller production runs.
Faster Turnaround
Need parts quickly? Vacuum forming delivers.
You can go from design to finished parts in days, not months. The simpler tooling means faster manufacturing and quicker design iterations.
Design Flexibility
Making changes? No problem.
Vacuum forming molds can be modified relatively easily. Compare that to injection molding where changes mean expensive retooling.
Large Part Capability
Vacuum forming excels at big parts. We’re talking bathtubs, car doors, and refrigerator liners.
Try making those with injection molding. The tooling costs would be astronomical.
Material Variety
From crystal-clear PETG to tough polycarbonate, vacuum forming works with dozens of thermoplastics. Each offers different properties to match your application.
Limitations You Need to Know
But vacuum forming isn’t perfect for everything.
Here are the key limitations:
Single-Sided Detail
Remember: vacuum forming only creates detail on one side. The back side remains relatively featureless.
Need detail on both sides? You’ll need to look at other processes.
Wall Thickness Variation
As the plastic stretches over the mold, it gets thinner in some areas. Deep draws can result in significantly thinned sections.
This affects both strength and appearance.
Limited Undercuts
Vacuum forming struggles with undercuts and complex geometries. The part needs to release from the mold, which limits design options.
Lower Precision
Compared to injection molding, vacuum forming offers less dimensional precision. Tolerances are typically ±0.020″ for the first inch.
Higher Per-Part Cost (High Volume)
For massive production runs (think millions of parts), injection molding becomes more cost-effective per unit.
Real-World Vacuum Forming Applications
So where do you actually see vacuum formed parts?
They’re literally everywhere:
Packaging Industry
- Blister packs for retail products
- Food containers and trays
- Clamshell packaging
- Medical device packaging
Automotive Sector
- Dashboard components
- Door panels
- Truck bed liners
- Engine covers
- Wheel well liners
Medical Field
- Equipment housings
- Dental retainers and aligners
- Surgical trays
- Prosthetic components
Consumer Products
- Refrigerator door liners
- Bathtubs and shower bases
- Luggage shells
- Toy components
- Swimming pools
Industrial Applications
- Machine guards
- Equipment enclosures
- Protective covers
- Material handling trays
The versatility is incredible. From a $2 food container to a $20,000 medical device housing, vacuum forming handles it all.
Vacuum Forming vs Other Plastic Manufacturing Methods
How does vacuum forming stack up against other plastic forming processes?
Let’s compare:
Vacuum Forming vs Injection Molding
Injection molding wins for:
- High-volume production (millions of parts)
- Complex geometries with undercuts
- Tight tolerances
- Parts with details on all sides
Vacuum forming wins for:
- Lower tooling costs
- Larger parts
- Faster prototyping
- Shorter production runs
Vacuum Forming vs Pressure Forming
These are actually cousins. Pressure forming adds positive air pressure to push the plastic more tightly against the mold.
Pressure forming offers:
- Better detail reproduction
- Sharper corners
- More consistent wall thickness
- Ability to form textured surfaces
But it costs more than standard vacuum forming.
Vacuum Forming vs Rotational Molding
Rotational molding creates hollow parts by rotating a mold filled with plastic powder.
It’s better for:
- Large hollow parts
- Consistent wall thickness
- Stress-free parts
But vacuum forming is faster and more cost-effective for most applications.
When Should You Choose Vacuum Forming?
Here’s my advice on when vacuum forming makes sense:
Choose Vacuum Forming When:
You need 100-50,000 parts per year. This is the sweet spot where vacuum forming economics work best.
Your parts are relatively large. Anything over 12 inches starts favoring vacuum forming.
You need quick turnaround. From design to parts in days, not months.
Your budget is limited. Lower tooling costs mean lower upfront investment.
You’re still prototyping. Easy mold modifications support design iterations.
Detail is only needed on one side. Perfect for covers, housings, and panels.
Look Elsewhere When:
You need millions of identical parts. Injection molding becomes more economical.
Your design has complex undercuts. These can make vacuum forming impossible.
You require tight tolerances. Vacuum forming can’t match injection molding precision.
Wall thickness must be uniform. The stretching process creates variations.
Getting Started With Vacuum Forming
Ready to explore vacuum forming for your project?
Here’s how to get started:
- Define your requirements – Part size, quantity, material needs, and critical features
- Create your design – Remember the design limitations we discussed
- Choose your material – Match plastic properties to your application
- Find a vacuum forming partner – Look for experience with similar parts
- Prototype first – Test your design before committing to production tooling
- Plan for finishing – Factor in trimming, drilling, and any assembly needs
The key is starting simple. Your first vacuum formed part doesn’t need to push the boundaries. Get comfortable with the process, then expand from there.
The Bottom Line
Vacuum forming plastic remains one of the most versatile and cost-effective manufacturing methods available today.
It’s not the right choice for every application. But when you need affordable tooling, quick turnaround, and design flexibility, vacuum forming delivers.
From the packaging protecting your latest purchase to the dashboard in your car, vacuum formed parts are everywhere. And now you know exactly how they’re made.
The process might be 80 years old. But it’s still solving modern manufacturing challenges every single day.
Understanding what vacuum forming plastic is – and when to use it – gives you another powerful tool in your manufacturing toolkit.
And in today’s competitive market, having options like that can make all the difference.