Injection molding is one of the most common manufacturing processes for creating plastic parts. However, warpage is a common defect that occurs during injection molding, causing parts to bend, twist, or deform after they’ve been ejected from the mold.
So what exactly causes warpage? And what can you do to prevent it? In this complete guide, as a professional plastic injection molding manufacturer, I’ll explain everything you need to know about warpage in injection molding.
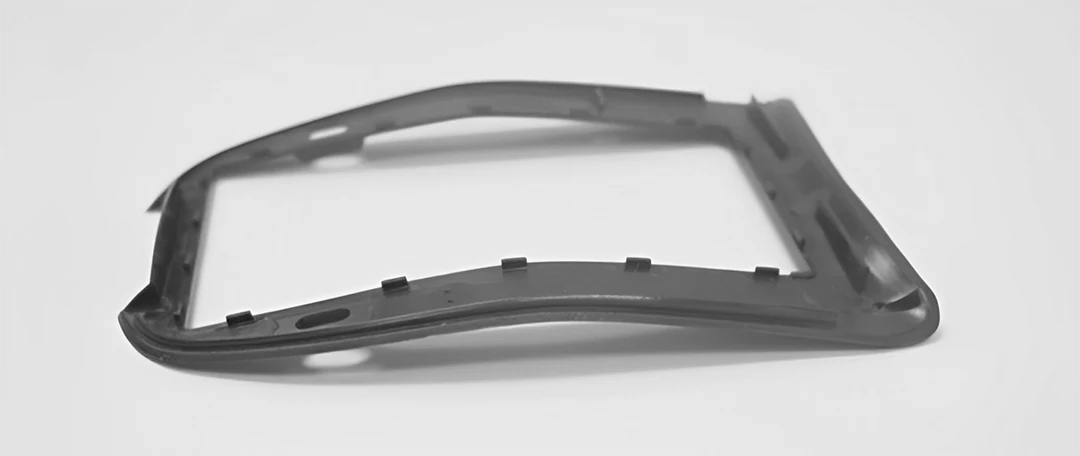
What is Warpage in Injection Molding?
Warpage refers to the distortion or deformation of a plastic part after it’s been ejected from the injection mold. Instead of maintaining the exact shape of the mold cavity, the part “warps” due to uneven cooling or molecular alignment issues.
There are a few common types of warpage that can occur:
- Twisting – The part twists out of shape along its length
- Bending – The part develops a curve or bow shape
- Cupping – The edges of the part curve up or down
Typically even small amounts of warpage can prevent parts from properly assembling or fitting together. And in severe cases, warpage can make parts completely unusable.
So what causes this frustrating defect? Let’s take a closer look.
What Causes Warpage in Injection Molding?
There are three main triggers that cause warpage during injection molding:
1. Uneven Cooling Rates
As plastic parts cool down in the mold, if some areas cool significantly faster than others it can cause the molecules to shrink unevenly. These areas essentially “pull” on the still warm plastic, causing stresses that lead to warpage.
Common triggers for uneven cooling include:
- Variations in wall thickness
- Poor cooling channel design
- Temperature variations in the mold
2. Molecular Alignment Issues
The high heat and pressure during injection molding causes polymer chains to align along the direction of flow. If these molecules don’t have time to properly relax, it can “lock in” stresses that lead to warped parts after ejection.
3. Ejection and Residual Stresses
Finally, uneven stresses during ejection can cause warpage issues. If some areas of the part stick to the mold longer than others, it twists the part out of shape. Residual stresses “frozen” into the plastic during packing can also be released when the part is ejected, causing deformation.
Next I’ll outline some ways to prevent warpage by addressing these common causes.
How to Prevent Warpage in Injection Molding
The best way to avoid warpage is to optimize your injection molding process, part design, material selection, and mold cooling early on during prototyping. But you can also take some corrective actions if warpage occurs in production.
Here are my top tips:
Carefully Evaluate Part Design
Pay close attention to uniform wall thickness, draft angles, rib placement, and avoidance of abrupt transitions in geometry. This allows for even cooling and molecular alignment.
Choose a Suitable Material
Amorphous plastics like ABS tend to warp less than semi-crystalline plastics like nylon. Also consider fillers, reinforcements, and shrinkage rates.
Optimize Process Settings
Lower injection pressures and speeds can minimize molecular alignment stresses. Sufficient packing time and pressure minimizes voids. And adequate cooling times are critical.
Improve Mold Cooling Efficiency
Use materials with higher thermal conductivity, and ensure cooling channels are evenly distributed. Monitoring mold temperature variances also helps identify issues areas.
Try Secondary Operations
Annealing or stabilizing the parts after molding can relieve internal stresses and reduce warpage. Just keep in mind that additional handling introduces variability.
Conclusion
While warpage will likely never be 100% avoidable in injection molding, paying attention to part design, material selection, process settings, and mold cooling early on can go a long way towards minimizing issues.
And if defects do occur after production is underway, there are secondary operations such as annealing that can help improve part quality as well.
What is warpage in injection molding? Warpage refers to the bending, twisting or deformation of plastic parts after they’ve cooled in the injection mold. It’s usually caused by uneven cooling rates, poor molecular alignment, and stresses during ejection. Careful part design, suitable material selection, optimized process settings, and efficient mold cooling are key to avoiding warpage issues.
I hope this guide gives you everything you need to understand, detect, and prevent the common yet frustrating issue of warpage in injection molding! Let me know in the comments if you have any other questions.