Acrylic injection molding is a popular manufacturing process to produce clear plastic parts. But what temperature is best for acrylic injection molding?
In this complete guide, as a professional acrylic injection molding manufacturer, I will share the optimal barrel, melt, mold and other temperatures for successfully injection molding acrylic resin. I’ll also cover how temperature affects acrylic injection molding quality and cycle times.
By the end, you’ll know exactly what temperature settings to use when injection molding acrylic to maximize quality and efficiency.
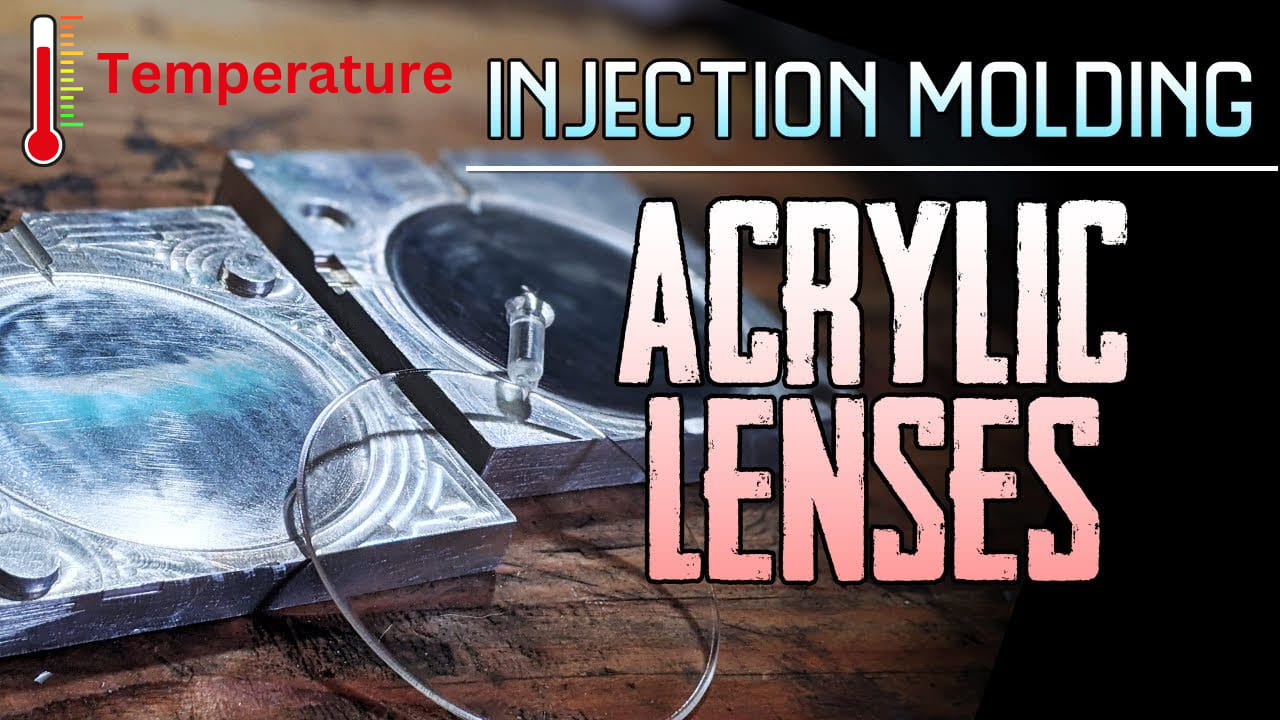
What is Acrylic Injection Molding?
First, a quick overview of the acrylic injection molding process.
Acrylic injection molding involves injecting hot, molten PMMA resin into a mold cavity. After it cools and hardens, you open the mold and eject the finished acrylic part.
The acrylic injection molding process enables high volume production of acrylic components with tight tolerances and detailed features.
Common acrylic injection molded parts include lenses, light covers, signage letters and transparent item packaging. The automotive and medical device industries also use lots of injection molded acrylic.
Now that you know what acrylic injection molding is, let’s look at why managing temperature is critical.
Why Acrylic Injection Molding Temperature Matters
With acrylic injection molding, maintaining proper temperatures is crucial for:
- Achieving complete fills
- Good surface finish
- Quick cycle times
- Dimensional accuracy
- Optimal mechanical properties
Set your barrel, hot runner and mold temperatures too cold? You’ll get short shots, long cycles and ugly parts.
Conversely, excessively high temperatures lead to degraded material, dimensionally unstable parts and bubbles/burn marks.
Furthermore, acrylic’s high melt viscosity sensitivity to temperature means stability is essential. Fluctuating heat causes radical viscosity shifts and screw movement inaccuracies.
Clearly, keeping temperatures within specified ranges is vital for successful PMMA injection molding.
Recommended Temperatures for Acrylic Injection Molding
So what are the ideal temperature windows? Here are typical settings:
Barrel: Front 205-230°C, Center 195-205°C, Rear 175-195°C
Melt: 205-230°C (must pyrometer measure)
Hot Runner: 205-230°C
Mold: 60-95°C (run on higher end for best finish)
Let’s examine these acrylic injection molding temperature guidelines further:
Barrel Temperatures
- Front barrel around 220°C gives lowest melt viscosity. But limit residence time over 230°C to avoid material degradation.
- Center barrel cooler to ease back flow and minimize thermal degradation.
- Rear barrel significantly lower prevents premature melting and accommodation for high back pressure.
Generally, use a reverse temperature profile with the highest heat up front. However, stable temps of ±2°C are most critical.
Melt Temperature
Closely controlling PMMA’s melt temperature between 205-230°C is also essential.
Excessive heat causes material breakdown. And inadequate melting won’t properly lower the viscosity for filling intricate part details.
I highly recommend installing a pyrometer for direct nozzle melt readings. Don’t rely on barrel setpoints alone.
Hot Runner Temperatures
For hot runner systems, follow the same 205-230°C suggested temperature guideline.
Tuning between cycles, verify tips stabilize at setpoints before starting full-speed production.
Mold Temperature
Mold temperature significantly impacts PMMA’s surface finish and dimensional stability after cooling.
Higher acrylic mold temps from 80-95°C best balance achieving glossy appearances with acceptable cycle lengths.
Furthermore, consistent mold temperature maintains uniform cooling and minimizes residual stress cracking.
How Temperature Affects Acrylic Injection Molding
Now that you know typical temperature recommendations for PMMA injection molding machines, let’s examine how heat variations influence:
- Part quality
- Cycle times
- Viscosity stability
Understanding these thermal cause-and-effect relationships will help guide your temperature tuning.
Impact on Quality
Maintaining a stable 205-230°C melt temperature is imperative for flawless acrylic parts.
Overheating above 250°C discolors material and creates weakness-inducing internal stresses.
While undermelting due to low/ fluctuating heat offers insufficient impregnation of micro-details.
Both extremes breed cosmetic and performance failures.
Effect on Cycle Times
Within limits, pumping up the barrel, melt and mold heat speeds up injection cycles. And dropping temperatures extends cycles.
Too hot though and you’ll exceed acrylic’s safe viscosity processing window and decompose the polymer.
But when fine-tuned, running PMMA molding machines on the hotter end of suggested temp ranges offer 25-50% faster cycles. There’s just less cooling needed before safe part ejection.
Importance for Viscosity Stability
Stable temps also prevent radical PMMA viscosity shifts mid-run.
Acrylic’s high sensitivity to temperature requires consistency for proper metering and plasticization.
Otherwise, pressure fluctuations cause short shot parts, unsightly cracks or surface defects.
Double-check barrel controller PID modes and thermocouple functionality to ensure minimal variance.
Conclusion
You should now understand acrylic injection molding temperature considerations much better.
To recap, key things to remember are:
- Closely follow recommended barrel, hot runner and mold temperature guidelines
- The stability of settings outweighs meeting exact numbers
- Measure real-time melt temps with a pyrometer
- Higher (within limits) temps quicken cycles but risk burning
- Keep variations minimal to avoid drastic viscosity changes
Integrating these thermal management best practices will ensure your acrylic injection molding delivers superior quality and efficiency.
Now focus on holding those tight ±2°C tolerances and let me know how it works out for your PMMA molding applications!